Accumulator Facts & Tips
July 27, 2022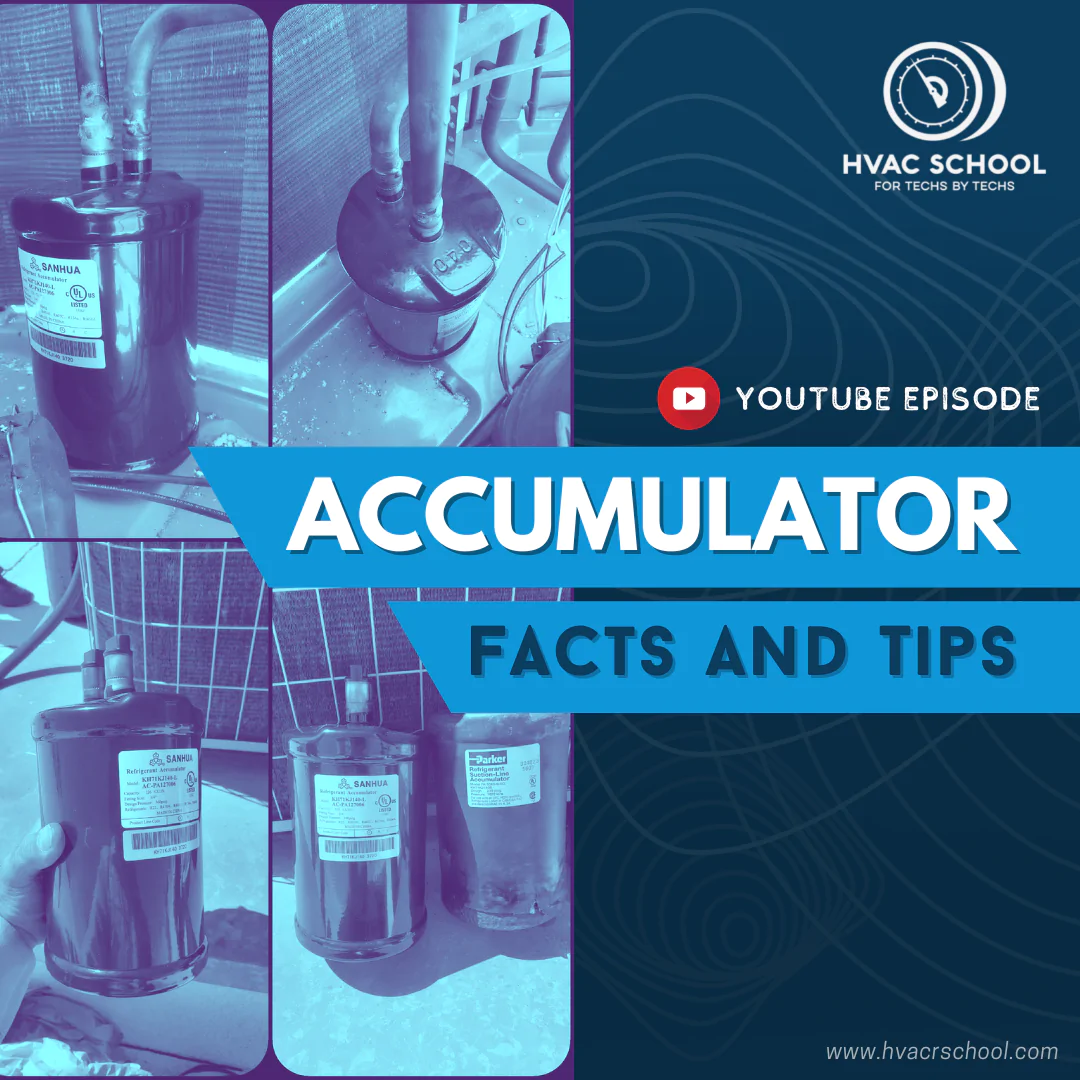
Accumulators are designed to accumulate liquid refrigerant before that liquid can reach the compressor. Liquid should never get inside the compressor. When liquid floods the compressor, it washes out the oil. Many compressors are also refrigerant-cooled, and that refrigerant has to be a cool vapor, not a liquid.
Accumulators are more common in Carrier heat pumps because those systems have fixed-orifice pistons that don’t control the superheat. Therefore, the accumulator is an additional safety measure when there is no control over the superheat in a wide operating envelope; it interrupts the liquid before it can affect the compressor. Although the accumulator can become liquid-locked and feed back, it’s unlikely. Accumulators also prevent slugging. However, modern compressors are unlikely to slug due to their refrigerant-cooled nature. Slugging happens when liquid gets into the compression chamber.
Overall, getting liquid into the compressor in any capacity is undesirable because it starts foaming the oil and ejecting it from the compressor. The oil lubricates the compressor bearings, which keeps the compressor working for its entire lifespan; premature failure may happen if there is too much mechanical wear without the oil. When oil is ejected from the compressor, it also goes to the rest of the system and can get stuck in the evaporator coil when it gets more viscous.
The accumulator has a U-shaped tube with a small pickup hole at the bottom, which picks up oil. (Oil is heavier than liquid refrigerant and will sink to the bottom of an accumulator.) If that bottom port gets blocked, oil won’t be able to get through and will get stuck in the accumulator, so it can’t lubricate the compressor. Copper shavings, dirt, and carbon flakes may block that port. There is also a port near the top that stops the accumulator from becoming liquid-locked.
In some cases, oil also may not return to the compressor due to long line sets. Long lines require the HVAC/R technician to add more refrigerant, and special considerations need to be taken to make sure that liquid refrigerant doesn’t migrate (or vapor refrigerant doesn’t condense to a liquid in the compressor). These strategies include liquid line solenoid valves, hard shutoff TXVs, and crankcase heaters.
When we replace a compressor, we want to pay attention to the accumulator. Replacing the accumulator is perhaps the best practice, especially in a burnout situation, but the old accumulator can be reused if it’s flushed and completely cleaned out. It’s a good idea to dump out the accumulator and analyze the oil; a lot of contaminated oil indicates a lot of oil loss and could be a burnout. The accumulator is a good place to test the oil, too.
Charging a system with an accumulator is different from charging a system without an accumulator. Liquid charging could result in refrigerant going into the accumulator and getting cold, which makes it hold liquid refrigerant and indicate undercharge because the subcooling won’t go up (even though the system could be overcharged). So, using a charging scale and giving the system plenty of time to equalize will help prevent that from happening. With labor, refrigerant, and callbacks being as expensive as they are, the small details matter.
It’s also worth noting that motors and electrical parts often fail due to mechanical conditions, not electrical ones. So, burnout isn’t always caused by lightning strikes, start capacitors that aren’t taken out of the circuit, or over-voltage conditions.
Comments
To leave a comment, you need to log in.
Log In