Evacuation, Recovery, and Dehydration Facts Podcast
In this episode, Bryan covers evacuation, recovery, and dehydration.
Evacuation refers to putting a vacuum pump on the system and pulling it down. We use a few different measures of vacuum, including inches of mercury (“Hg) or microns (millionths of a meter of mercury). We use such small units to measure a vacuum that effectively boils off moisture in the system. You must pull the vacuum very close to a perfect vacuum. So, a measurement of 500 microns indicates that the vacuum is 500 microns of mercury above a perfect vacuum.
Dehydration is a mere component (or result) of evacuation. If there is excess moisture in the system, it can freeze inside the system and cause blockages. It can also interact with oil and refrigerant inside the system to create an acid that ruins your unit.
To get a proper vacuum, you have to pull down to 500 microns. You can go lower than that, if possible, but 500 microns is the industry standard. Remember that Schrader cores restrict your vacuum. Remove them with a proper core remover tool for a more effective evacuation. Larger hoses and better equipment won't make a difference if you leave those Schrader cores in. If you don't have Schraders, you probably have a service valve.
Recovery removes refrigerant from a system under vacuum and puts it in a tank. We do recovery because we CANNOT vent refrigerant.
As a best practice, when you connect your vacuum rig to the port, you can use a little bit of Nylog thread sealant to keep moisture and other contaminants out.
Bryan also covers:
- Push/pull method
- Microns
- Vacuum pump oil
- Moisture contamination
- Vacuum restrictions
- Triple evacuation and sweeping nitrogen
- King valves/service valves
- De minimis
As always, if you have an iPhone, subscribe HERE, and if you have an Android phone, subscribe HERE.
Author:
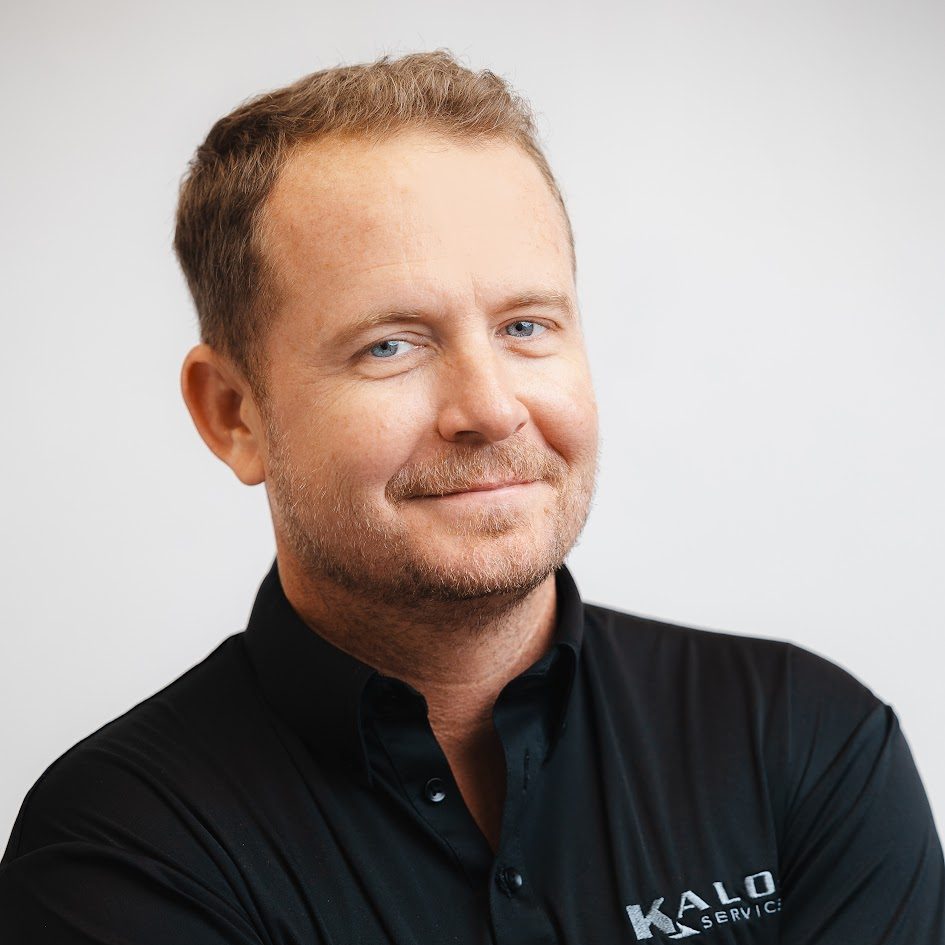
Comments
Great Job Bryan. You have a way of putting things so that people can understand. I always try to learn by other people’s mistakes.
I was fortunate to have worked with many different people over the years. By applying a little common sense only eliminates equipment failure. Laziness and not keeping our tools in proper working order are what I have experienced to be the most common
Reason for bad installs. Most of the time pressure from office or home has a key role in that also. One of the most important things I have learned is speed kills.
ROCK ON!
Great Job Bryan. You have a way of putting things so that people can understand. I always try to learn by other people’s mistakes.
I was fortunate to have worked with many different people over the years. By applying a little common sense only eliminates equipment failure. Laziness and not keeping our tools in proper working order are what I have experienced to be the most common
Reason for bad installs. Most of the time pressure from office or home has a key role in that also. One of the most important things I have learned is speed kills.
ROCK ON!
Tadalafil achat en ligne: Tadalafil 20 mg prix en pharmacie – Tadalafil 20 mg prix sans ordonnance tadalmed.shop
Tadalafil achat en ligne: Tadalafil 20 mg prix en pharmacie – Tadalafil 20 mg prix sans ordonnance tadalmed.shop
acheter kamagra site fiable: kamagra oral jelly – kamagra oral jelly
acheter kamagra site fiable: kamagra oral jelly – kamagra oral jelly
https://pharmafst.com/# pharmacie en ligne france livraison internationale
https://pharmafst.com/# pharmacie en ligne france livraison internationale
kamagra en ligne Achetez vos kamagra medicaments or kamagra en ligne
https://maps.google.gr/url?sa=t&url=https://kamagraprix.shop Kamagra pharmacie en ligne
[url=https://www.google.cg/url?q=https://kamagraprix.shop]acheter kamagra site fiable[/url] acheter kamagra site fiable and [url=https://bbs.hy2001.com/home.php?mod=space&uid=70188]kamagra oral jelly[/url] Achetez vos kamagra medicaments
kamagra en ligne Achetez vos kamagra medicaments or kamagra en ligne
https://maps.google.gr/url?sa=t&url=https://kamagraprix.shop Kamagra pharmacie en ligne
[url=https://www.google.cg/url?q=https://kamagraprix.shop]acheter kamagra site fiable[/url] acheter kamagra site fiable and [url=https://bbs.hy2001.com/home.php?mod=space&uid=70188]kamagra oral jelly[/url] Achetez vos kamagra medicaments
pharmacie en ligne pas cher [url=http://pharmafst.com/#]Medicaments en ligne livres en 24h[/url] pharmacie en ligne france livraison internationale pharmafst.shop
pharmacie en ligne pas cher [url=http://pharmafst.com/#]Medicaments en ligne livres en 24h[/url] pharmacie en ligne france livraison internationale pharmafst.shop
pharmacie en ligne france pas cher: Medicaments en ligne livres en 24h – pharmacie en ligne france livraison internationale pharmafst.com
pharmacie en ligne france pas cher: Medicaments en ligne livres en 24h – pharmacie en ligne france livraison internationale pharmafst.com
Pharmacie sans ordonnance: pharmacie en ligne pas cher – pharmacie en ligne pharmafst.com
Pharmacie sans ordonnance: pharmacie en ligne pas cher – pharmacie en ligne pharmafst.com
https://tadalmed.com/# Tadalafil 20 mg prix en pharmacie
https://tadalmed.com/# Tadalafil 20 mg prix en pharmacie
olympe casino avis: casino olympe – olympe casino avis
olympe casino avis: casino olympe – olympe casino avis
To leave a comment, you need to log in.
Log In