Get Tech Tips
Subscribe to free tech tips.
Ramping Your Team Up for CO2
This tech tip is based on a podcast with Andre Patenaude from Copeland. You can listen to that podcast episode HERE, and we encourage you to check out some of the resources at the end of this tech tip—whether you’re all in on ramping your team up for CO2 or just CO2-curious.
Carbon dioxide (CO2) is something we deal with every day, whether we realize it or not. We’re giving off CO2 every time we exhale, and our cells produce it when they work, too. However, it’s going to be involved in refrigeration techs’ lives a lot more in the coming decades.
CO2 has many advantages as a refrigerant (R-744), including its safety (insert obligatory “any refrigerant can be dangerous when it displaces oxygen” disclaimer here). It also has a low GWP—just 1. However, it is unique and has operational considerations that we’d never even think about when working with other refrigerants. If the word “supercritical” makes you nervous (and not because of overbearing parents or senior techs), I guarantee you’re not alone.
As with anything in this industry, training is the best way to get people comfortable with CO2. More and more commercial facilities are adopting the technology, even in climates where we couldn’t use it efficiently before, and with good reason. So, let’s take a look at why CO2 is gaining popularity and how HVACR teams can work on these systems with confidence.
Why CO2?
CO2 has many qualities that make it a good refrigerant for large commercial systems. It’s an A1 refrigerant, meaning it’s non-toxic and non-flammable, so the safety factor alone makes it an attractive choice (compared to flammable options like R-290 propane and the high toxicity of R-717 ammonia).
CO2 also has a GWP of 1. (Compare that to R-410A’s GWP of 2088 or even A2L R-32’s GWP of 675.) The entire United States is shifting to lower-GWP refrigerants, with some states like California implementing even stricter policies. With CO2’s GWP of 1, we don’t have to worry about it potentially being above future GWP thresholds. On top of that, we don’t need to recover CO2.
Where CO2 Came From
CO2 is one of the “natural” refrigerants, and it has been in use for a long time, as far back as the late 1800s. Its main draw was its safety advantages over ammonia, another common refrigerant at the time. However, with CO2’s pressure management challenges and the rise of CFC refrigerants (like R-12) in the early 20th century, CO2 fell out of favor, and new systems were rarely ever installed. (ASHRAE has a really neat article from 1999 that goes into greater detail about the history of CO2 as a refrigerant.)
About 20 years ago, CO2 saw a renewed interest in Europe’s refrigeration sector as regulations started targeting refrigerants with GWPs over 2500, including R-404A. Refrigeration systems typically contain a high volume of refrigerant; leaks can wreak havoc on the environment when you have refrigerants with a near-4000 GWP. Low-GWP gasses, like CO2, are a sensible solution to that problem with the technology to manipulate its pressures.
CO2 started popping up in North American commercial facilities in the early 2010s, starting with Canada and colder climates. CO2 is more efficient in markets with lower ambient temperatures, but we’ve recently seen CO2 make its way south and be used effectively even in states like Florida and Arizona where high-ambient mitigation strategies are employed.
Where CO2 is Going
CO2 equipment started off with a centralized model; a single CO2 system would feed all evaporators. However, we’re starting to see smaller racks with greater distribution; we can match suction pressures more evenly, improving efficiency.
We’re also starting to see hybrid models with HFC or HFO-based refrigerants. There are many cases when facility managers want to expand their infrastructure and add loads but can’t use the same refrigerant in the existing system due to regulatory changes. By installing CO2 equipment, facilities can add loads to existing infrastructure and stay in compliance with GWP regulations. One such example of a hybrid system is the cascade system, shown below. Come 2027 the high side side of cascade systems will need to use <300 GWP refrigerant to meeting EPA guidelines.
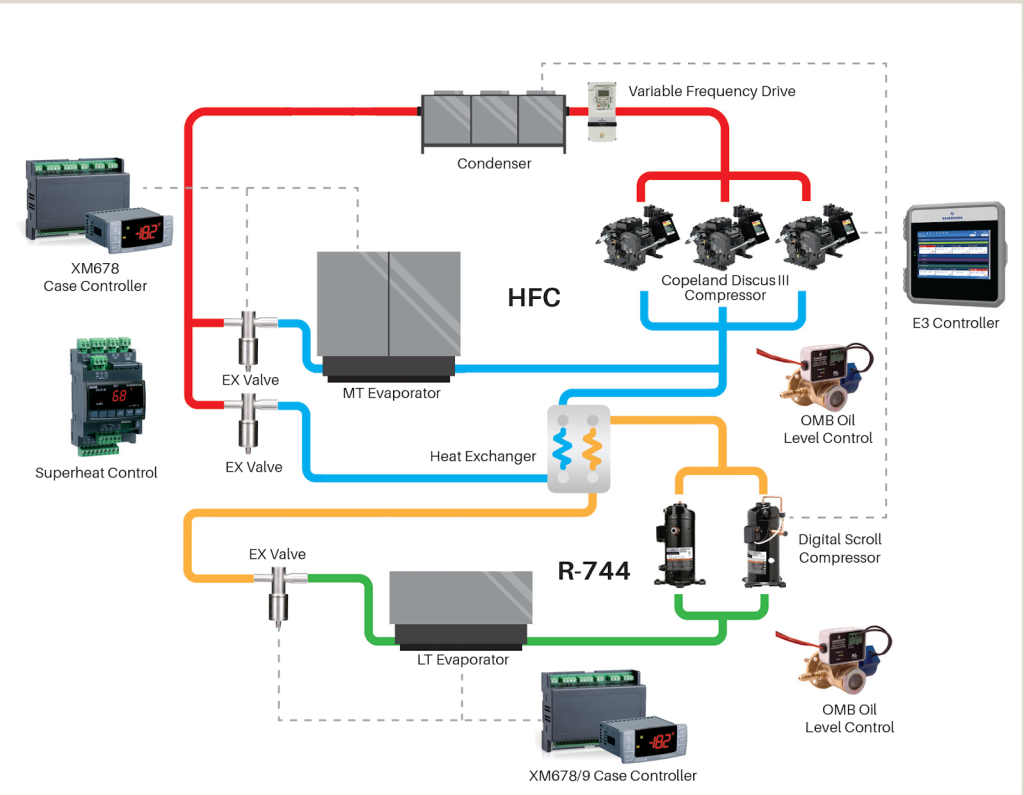
Credit: Copeland
CO2 chillers are also becoming more common. Chillers are typically smaller than traditional CO2 equipment and rely on a secondary fluid to provide refrigeration to the loads. This type of refrigeration isn’t limited to things like refrigerated cases; we could use CO2 chillers to move heat in comfort cooling applications, too.
Some boiler companies are even looking to CO2 as gas and oil fall out of popularity (or face legislative challenges). CO2 has high discharge temperatures, which helps provide a heat source without combustion. There is also an interest in using CO2 for heat pumps.
As promising as CO2 is, we have to be mindful of its unique traits that may catch a lot of techs off guard if they’ve never worked on CO2 systems before.
CO2’s Quirks
Before we get into CO2’s idiosyncrasies, let’s have a quick chemistry vocab lesson.
Terms
Triple point — The pressure and temperature at which a substance may exist as a solid, liquid, or vapor
Critical point — The temperature and pressure at which a substance becomes a supercritical fluid and stops obeying the pressure-temperature relationship
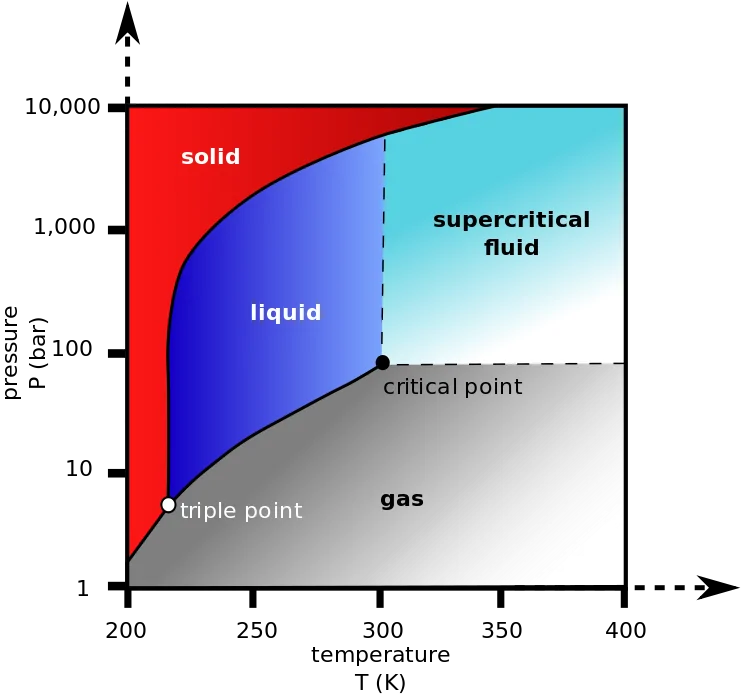
Bar — Unit of pressure equivalent to 100,000 Pascals (Pa) or approximately one atmosphere (one bar: 14.5 PSI; one atmosphere: 14.7 PSI)
Kelvin — An absolute temperature scale that starts at 0 (absolute zero, –273°C, or roughly –460°F) and is based on the same increments as the Celsius scale; commonly used to describe temperature differentials in countries that use the Celsius scale (multiply a Kelvin value by 1.8 to get the differential Fahrenheit equivalent)
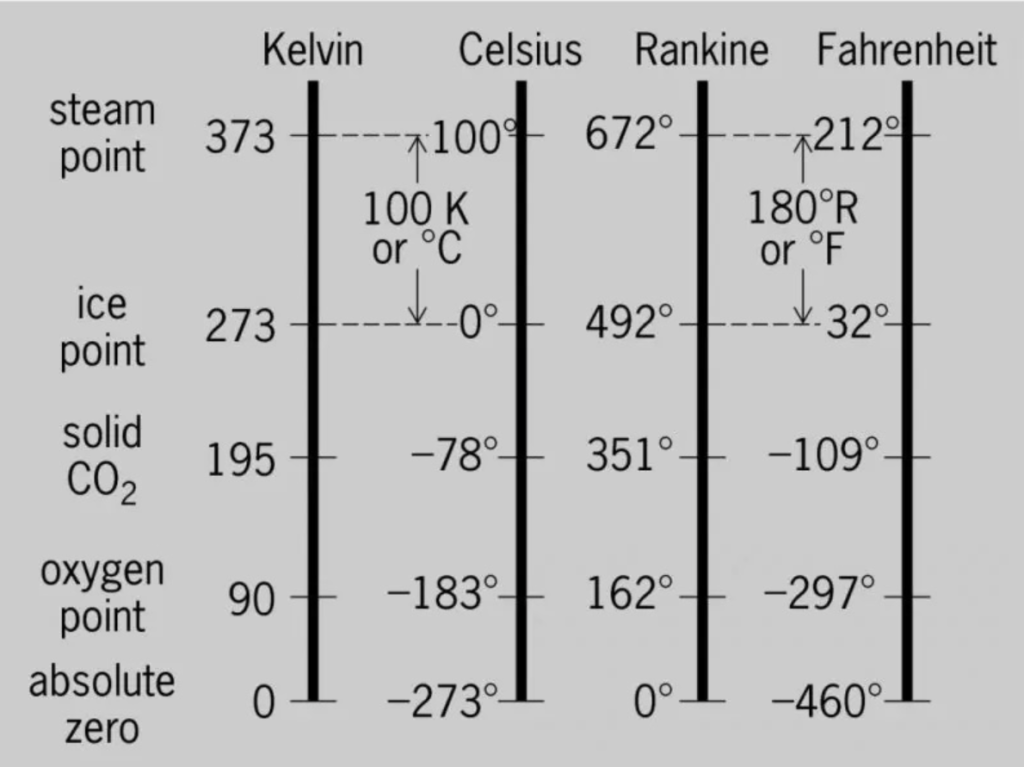
CO2 Properties
CO2 has a high triple point: 60 PSI. Even though the system should keep pressures high enough to prevent solid CO2 (dry ice) from forming during operation, it still could happen. If we have CO2 and open a liquid line valve to relieve some of the pressure onto a section that is below 60 PSIG, it could very well cause dry ice to form. Refrigeration techs have to be very careful when they do things like pull a vacuum on a CO2 system; system pressures need to be well over 60 PSIG to prevent dry ice from forming.
CO2 also has a low critical point: 87.8°F. When we get above that point, the pressure and temperature decouple; they can change without affecting the other, which can cause a dip in efficiency. When the pressure and temperature decouple, the CO2 becomes a “supercritical fluid.” A Florida summer day can easily stay above the critical point all day long, so a CO2 system would have to run in a “transcritical” or “supercritical “ state—where the CO2 is a supercritical fluid for part of the refrigerant circuit.
Pressure Zones and Pressure Relief Valves
In general, CO2 systems operate at higher pressures than other systems. We use the bar scale instead of PSI, and some pressure relief valves are set for 120 bars. That’s over 1700 PSI.
CO2 systems, especially transcritical systems, have different pressure zones. Just as we have the “high side” and “low side” of a system, we have different pressures throughout the CO2 refrigeration circuit. The system relies on pressure relief valves to provide safety mitigation for these zones.
The condenser (also known as a gas cooler in transcritical CO2 systems) can discharge supercritical fluid at a pressure of roughly 1500 PSI, but we need it to get down to about 500 PSI to provide useful work. We rely on two things to make that happen: a high-pressure valve/bypass gas valve (both modulated by the high-pressure controller) and a flash tank. The flash tank is similar to a liquid receiver, and a high-pressure valve before the flash tank reduces the pressure based on the HP controller’s settings.
The higher pressures we see in CO2 systems may alarm some people who aren’t familiar with CO2 infrastructure. Those high pressures are mostly limited to the medium-temp compressors and their discharge piping to the gas cooler/condenser. The tubing here is NOT the run-of-the-mill copper you’d expect in most HVAC applications; you’ll see stronger copper and even stainless steel tubing.
Supercritical vs. Subcritical Operation
All refrigerants have a critical point, but very few of them are as low as CO2. Since the majority of refrigerants stay below their critical point while the system is working, the system is under “subcritical” operation. The opposite—when the refrigerant is above the critical point—is called supercritical operation.
Supercritical operation occurs due to CO2’s low critical point and high ambient air entering the gas cooler. When that happens, the condenser that traditionally rejects heat to turn vapor refrigerant into liquid becomes a gas cooler, which reduces the temperature of the refrigerant but doesn’t liquefy it in the same way that a traditional condenser does.
Transcritical Booster Systems
“Booster” architecture consists of two sets of compressors: one for low-temperature loads and one for medium-temperature loads.
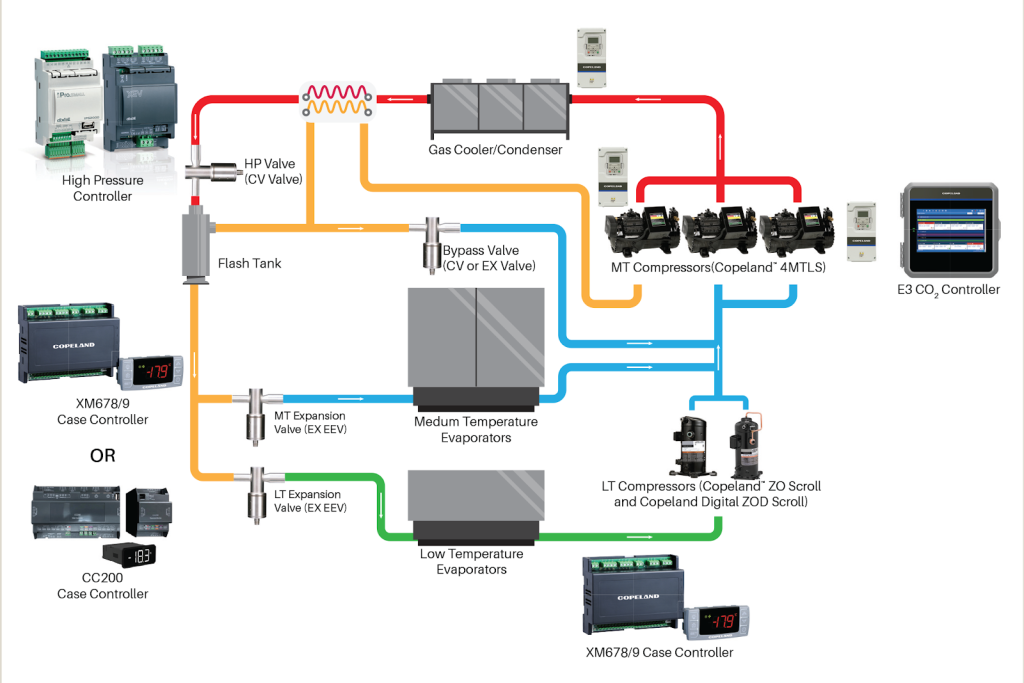
Credit: Copeland
The low-temperature compressors operate at pressures similar to that of R-410A. Their suction pressures are only around 200 PSI, and since the gas cooler/condenser could potentially operate at around 1500 PSI in the heat of the summer, it’s just not realistic to expect a low-temperature compressor to crank up the pressure by over 1300 PSI.
Instead, the LT discharge pressures are only around 400 PSI—similar to R-410A. That discharge gas goes into the suction line of the medium-temp loads, which leads into the medium-temp compressor. Those medium-temp compressors usually have to deal with a total of three sources of mass flow:
- Low-temperature discharge gas
- Medium-temperature suction gas
- Bypass gas from the flash tank
With all three of those combined, the compressors can actually achieve those high operating pressures. It helps to think of the low-temp compressors as being “boosted” to bring the low-temp suction pressure up in multiple steps instead of increasing the pressure sevenfold all at once.
The third item on the list, the bypass gas, comes from the bypass valve. This valve is at one of the flash tank outlets. It brings in another mass flow for the medium-temp compressors, but it also relieves some of the pressure from the flash tank to maintain a set liquid temperature (and its corresponding pressure). On the hottest days of the year, up to 45% of the total system mass flow can come from that bypass valve. This condition is very inefficient, so equipment manufacturers have developed mitigation strategies to decrease that ratio of bypass gas.
CO2 Compressors
As we already established, transcritical CO2 booster systems have two different sets of compressors: medium-temp and low-temp.
Copeland 4MTLS Transcritical CO2 Semi-Hermetic Compressors for Medium-Temperature Applications
Transcritical CO2 compressors have to be able to handle the heavier stress on the mechanical components due to the higher pressures of CO2. Copeland’s 4MTLS medium-temp compressors are of the semi-hermetic reciprocating type. These have heavier bearings than most compressors, and the crankshaft is balanced at both ends to keep operation smoother and quieter.
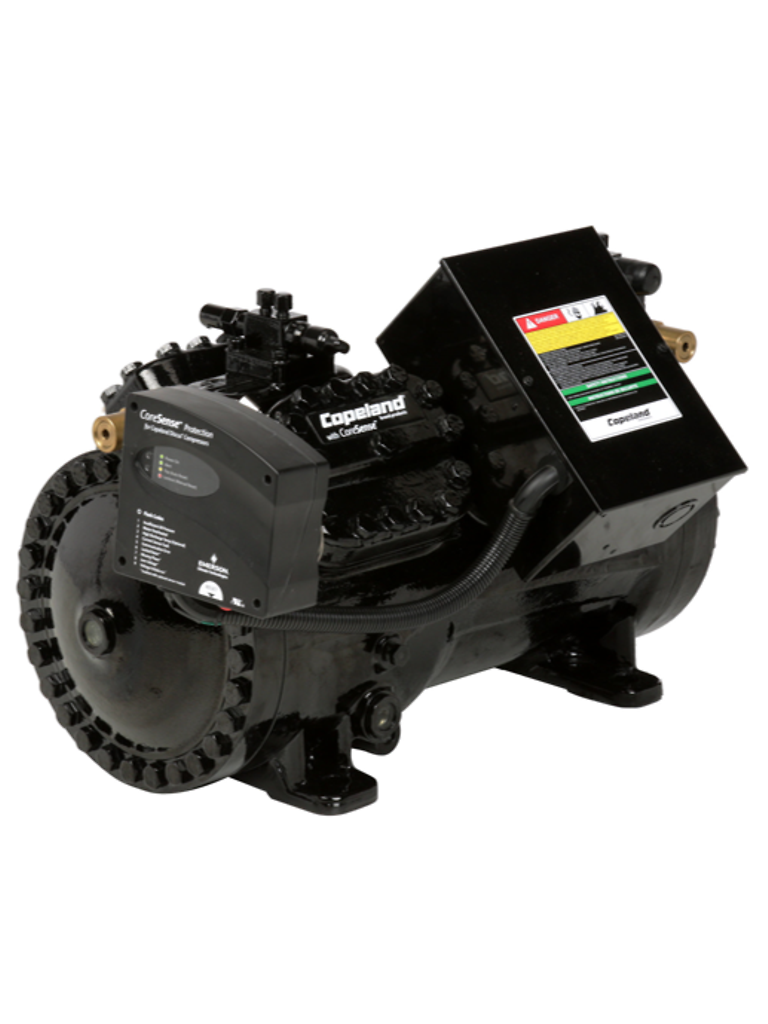
Credit: Copeland
Copeland has also included a diagnostic and communication module with the 4MTLS compressors. (We have a podcast about the module HERE.) This module can tie into the Modbus, allowing for remote monitoring and diagnosis. Copeland variable frequency drives (VFDs) are optimized for use with Copeland 4MTLS compressors and come with a pressure relief valve for safe operation.
Copeland ZO(D) Subcritical CO2 Scroll Compressors for Low-Temperature Applications
The most common Copeland low-temp compressors for CO2 refrigeration are ZO(D) scroll compressors, and they look a lot like typical HVAC scroll compressors but have been designed for the needs and rigor of CO2 refrigeration. There are digital scroll models that can adapt to a range of heat loads, but the discharge is limited to around 40°F. (Remember: The discharge goes right into the medium-temp suction.)
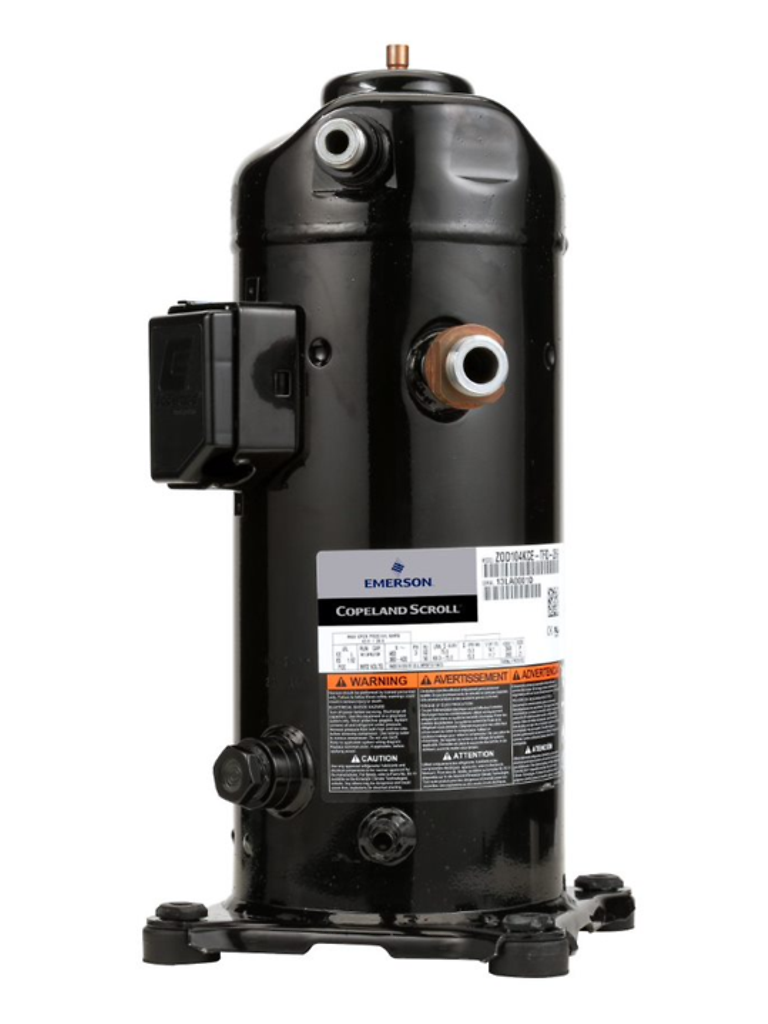
Credit: Copeland
Copeland also offers semi-hermetic low-temp compressors (4MSLS). These compressors have the same design considerations as their medium-temp counterparts. Sometimes, power outages can cause high pressure on the low-temp side of the refrigeration circuit when no work is being done, and compressors may need to overcome high standstill pressures (of around 1305 PSI or 90 bars). Facility managers may want a compressor model that can withstand those high pressures.
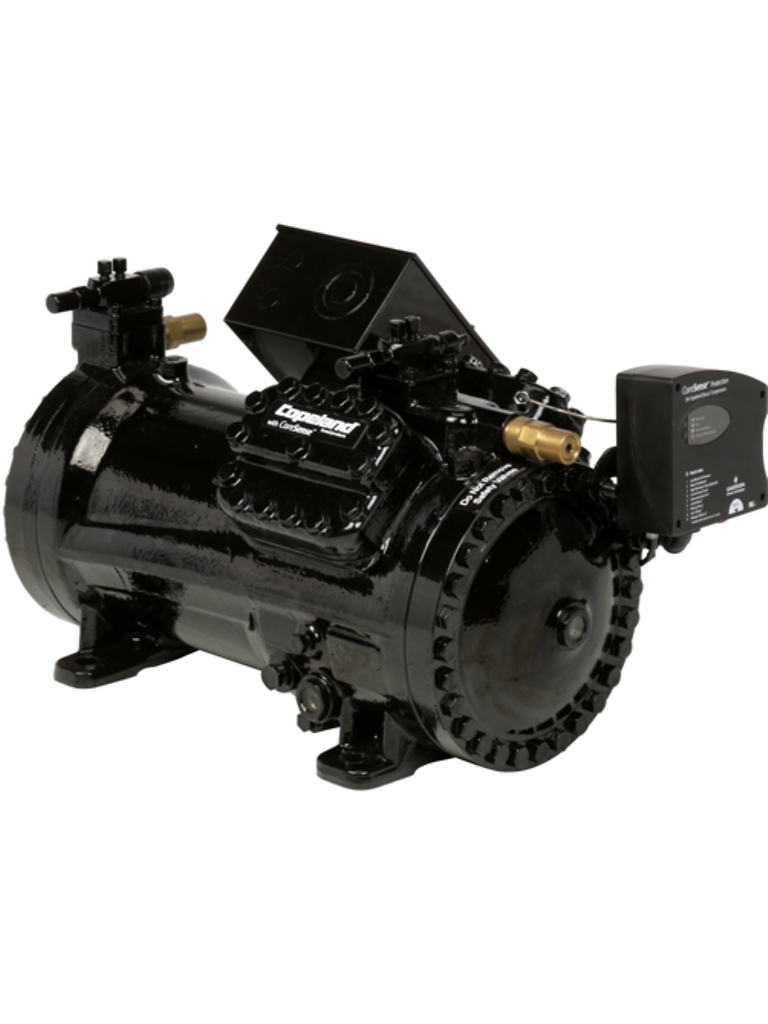
Credit: Copeland
CO2 Educational Resources
CO2 refrigeration is the future, and providing proper education to technicians, facility managers, and HVAC/R companies will be one of the biggest hurdles to overcome. However, there is no shortage of opportunities to receive training on CO2 systems.
Copeland’s E360 Resource Hub is perhaps one of the most invaluable tools you’ll find as you dip your toes into CO2 refrigeration. It has a range of blog posts by experts (including this one by Andre Patenaude), webinars, and outlook articles with industry trends and case studies.
The North American Sustainable Refrigeration Council (NASRC) also has multiple free natural refrigerant training expos for technicians. While there is a time investment (and travel costs), these events bring together hundreds of technicians and teach the most up-to-date technical developments of CO2 and propane (R-290) refrigeration with breakout rooms, training by industry experts and manufacturers, networking opportunities, and hands-on demonstrations. You can read more about future summits and view recordings and slides from past ones at https://nasrc.org/natural-refrigerant-training-summits
The Environmental Protection Agency (EPA) also has several resources about commercial refrigeration with its GreenChill Resources & Reports. While many of the resources are general and regulatory, you will find some on natural refrigerants, including CO2. You can access fact sheets, official industry protocols, webinars, and more through the GreenChill advanced refrigeration resource hub.
Wholesalers and manufacturers also often provide training. You’ll find a lot of great information from Hillphoenix (YouTube channel), Hussmann (training portal), and other manufacturers who make equipment for CO2 refrigeration.
HVAC School’s CO2 Resources
We also can’t pass up the opportunity for some shameless self-promotion. The 6th Annual HVACR Training Symposium is returning to Central Florida from February 6–7, 2025 (right before the 2025 AHR Expo in Orlando!). We’ll post updates about next year’s symposium at https://hvacrschool.com/symposium. You can still access this past year’s symposium presentations (including one about CO2) and purchase a virtual ticket HERE.
In addition to the symposium, we have the following resources already on our website:
Tech Tips
Podcast Episodes
- CO2 Introduction Podcast & Resources
- Intro to CO2 w/ Don Gillis
- Why CO2 Matters w/ Trevor Matthews
- 3 Flavors of CO2 w/ Rusty Walker
Comments
To leave a comment, you need to log in.
Log In