Get Tech Tips
Subscribe to free tech tips.
Callback Prevention: Electronic Leak Detection

Whether you love it or hate it, leak detection is one of those staples of HVAC, and the stakes are pretty high. Leaks that go undetected can also cost the customer quite a bit in refrigerant over time, especially with the rising prices of R-22 and R-410A. Worst of all, we could end up replacing parts (or entire systems) that don’t need to be replaced, all while the original problem remains unsolved. That’s when the callbacks roll in.
We’ve got some great resources in this industry, like INFICON and ESCO Institute’s free new NATE-certified course on the HVACR Learning Network, that cover best practices and technology in depth to help you prevent callbacks. This tech tip won’t go into as much detail as that course, but it’ll cover a few things you can keep in mind to reduce your callback rate on jobs where you use your electronic leak detector.
Be 100% positive that the charge is low
Refrigerant doesn’t just disappear into thin air once it’s inside a system; the only way it can get out, apart from being removed by humans, is through a leak. If there is a low charge, and no one has recovered refrigerant from the system, then you’ll know there’s a leak.
Weighing the charge is the only way to be completely sure that your system is low (and by how much), but there are a bunch of clues that can also lead you to that conclusion. Here are some of the symptoms of low charge:
- Low suction pressure*
- Low head pressure
- High superheat*
- Low subcooling
- Low compressor amp draw
- Low delta T*
*Fixed-orifice systems; TXVs modulate and may cause the system not to show these signs
We have a video that explains these symptoms in detail, which you can watch HERE. But the main thing to remember is that you’ll need to confirm that you have these readings and then rule out other possible causes, including airflow restrictions from dirty filters and coils.
And don’t forget: when in doubt, weigh it out!
Next-level visual inspections
We’ve said it a million times by now—use your senses! Before we even pull out our electronic leak detectors, we can use our eyes and hands to find things that sound the alarm bells in our heads.
Oil spots
Like refrigerant, oil doesn’t just disappear from the system; it has to get out via a leak. Luckily for us, it’s a lot easier to see possible oil leaks than refrigerant leaks.
Oil spots can show up as duller areas on shiny copper tubing. You can also distinguish oil from water if you attempt to wipe off drops or wet areas with your fingers. Water comes off pretty easily and doesn’t smear, but oil will typically smear and feel slippery.
Evaporator coils pull moisture out of the air, so their surface will naturally get wet. Since oil and water don’t mix, you may notice oil beads on the evaporator coil—these spots are always worth investigating further. (In many cases, the oil drips onto the surface from a leak above the point where you’ve spotted the oil.)

Checking the drain pan is also a good idea. Again, water and oil don’t mix, so you might see spots in the drain pan where the water looks discolored in patches.
On the high-pressure side of the system, you may see oil sprayed against the insides of the outdoor unit.
Corrosion
Rusting out is quite common in evaporator coils, ductless line sets, and accumulators, and those cases are always worth a second look.
There are two types of corrosion you’ll see: galvanic and formicary.
Galvanic corrosion looks like your typical red rust. It happens when the metal in the coil is exposed to moisture and reacts with the oxygen.

Formicary (or formic) corrosion looks a bit like an ant’s nest. This type of corrosion often happens when copper is exposed to moisture and VOCs. (The HVACR Learning Network also has a “Did You Know?” episode about formicary corrosion and pinhole leaks in copper line sets. You can watch it for free HERE.)
Abrasions and tubing deformities
Keep an eye out for brazed joints that look weak or places where the tubing or coil may have rubbed out against something (usually a wire or another tube). Note anything that seems odd, and make sure you go over those spots with your leak detector.
Know your leak detector’s uses and limitations (RTFM)
This section may seem a bit silly, but it’s easy to misdiagnose a leak if you don’t know how to use your electronic leak detector. Infrared detectors work quite differently from the heated diode type, and ultrasonic detectors are a completely different animal.
You’ll need to know your leak detector’s uses and limitations. Heated diode leak detectors, like the trusty Bacharach H-10 series, are great because of their sensitivity, but they may sound the alarm when they pick up a chemical other than refrigerant. (Some of them also need time to warm up before use.)

Corona suppression leak detectors are even more likely to pick up a false positive than heated diode leak detectors. I don’t recommend using them at all.
Infrared (IR) detectors, like the INFICON D-TEK Stratus, are less likely to be set off by other chemicals (though it can happen), but they constantly recalibrate to the area around they’re in. You’ll need to move them consistently to avoid a false alarm. The D-TEK Stratus manual also has a list of common automotive chemicals that may trigger a false alarm.

All of the leak detectors I just mentioned will need sensor and filter changes on occasion; the manual will tell you when and how to do that. Some sensors can also be fouled by oil or refrigerant and will need to be changed immediately when that happens.
Ultrasonic leak detectors, like the AccuTrak VPE, don’t sample gases at all. They pick up the sound of gases leaving a leak, which we can’t hear with the naked ear. They also don’t have sensors that you'll need to change. However, they’re known to have more of a learning curve than some of the other types.
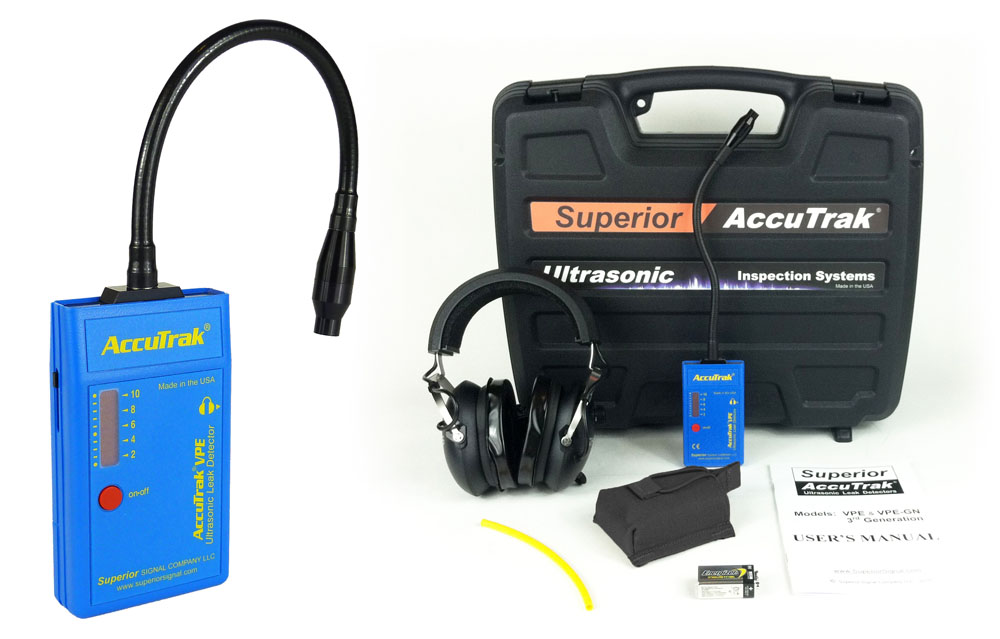
Reading the manual will also let you know how to configure the sensitivity settings of your leak detector; a higher sensitivity isn’t always better. The manual will also tell you how to maintain your leak detector.
Understand what can cause a false positive (or negative!)
Some electronic leak detectors will pick up gases other than refrigerant, and we work with a lot of things that can set off a leak detector even when there isn’t a leak. We also work in conditions (or with materials) that can mask leaks.
Chemicals
Unfortunately, some leak detectors pick up common chemicals that we work with on a daily basis:
- Cleaners
- VOCs (off-gassing from paint or insulation)
- Soap bubbles

If you’re using a heated diode leak detector, make sure your leak detection area is clear of any of these chemicals. (It’s good practice for any leak detector, but those are more likely to pick up false positives.)
On the other hand, soap bubbles can also block leaks and cause them to go undetected by ultrasonic or IR leak detectors.
Refrigerant
Refrigerant can cause a leak detector to go off?! No way! Thanks for that groundbreaking discovery, Captain Obvious!
Refrigerant makes the list for two main reasons: its density and its ability to accumulate in indoor spaces.
Most refrigerants sink because they are heavier than air. If you’re at an evaporator coil and start your leak detection at the bottom of the coil, your leak detector has a good chance of going off below the actual leak. When you pinpoint a leak, you’ll want to check a little bit higher than the spot where the leak detector first started going off
In rack houses where large volumes of refrigerant are being moved, the entire room can fill with leaked refrigerant from the bottom up. Whenever possible, make sure you’re checking for leaks in spaces that have good ventilation. That’ll make your leak detection more precise and make the job a lot safer for you.
Wind
Outdoors, you may have to worry about the wind blowing refrigerant away from the leak. Your leak detector may pick up refrigerant a little bit away from the actual leak, or it may fail to pick up a leak at all, so you’ll just have to be mindful of that when pinpointing leaks outdoors.
Noisy wind can also make it harder to hear your ultrasonic leak detector if you’re still learning how to use the leak detector.
The leak detector isn’t working
Sometimes, the leak detector just doesn’t work. But it’s our responsibility to make sure we’re testing our leak detectors and maintaining them.
Before we do a leak detection with an IR or heated diode leak detector, we must test it against a small amount of refrigerant to make sure the sensor works as it should. Whether we use a reference vial or depress a Schrader core for a sample, we need to make sure our leak detector sounds the alarm when it comes into contact with the refrigerant we’re looking for.
It’s also worth noting that some leak detectors are less sensitive to HFCs (R-410A and R-32) than HCFCs (R-22).
If you find a leak, take the time to find other leaks
It's tempting to find a leak on the evaporator coil and walk away from a job well done, but our job isn't finished when we find one leak. It's up to us to do our due diligence and check for more leaks.
Evaporator coil leaks are common, but that doesn't mean the condenser can't also have a leak. If there's a leak outside, replacing the evaporator only solves half the problem. You'll still get a callback.
You owe it to yourself (and your customer) to do a leak check on the condenser with your leak detector. At the very least, check for common signs of leaks: rusty accumulators, oil, dirt stuck to oil spots, etc.
I’ve done everything right and still can’t find a leak. What now?
There will be some jobs where we just can’t find a leak in the coils or visible areas of the line set. In the Central Florida market, we see a lot of underground line sets and can’t always access those.
When that happens, you may have to give the customer the option to continue with a line isolation test. A line isolation test is a specific type of nitrogen pressure test that focuses on the line set and evaporator coil, and we have a video about it HERE. We’ve also included our 9-panel below.
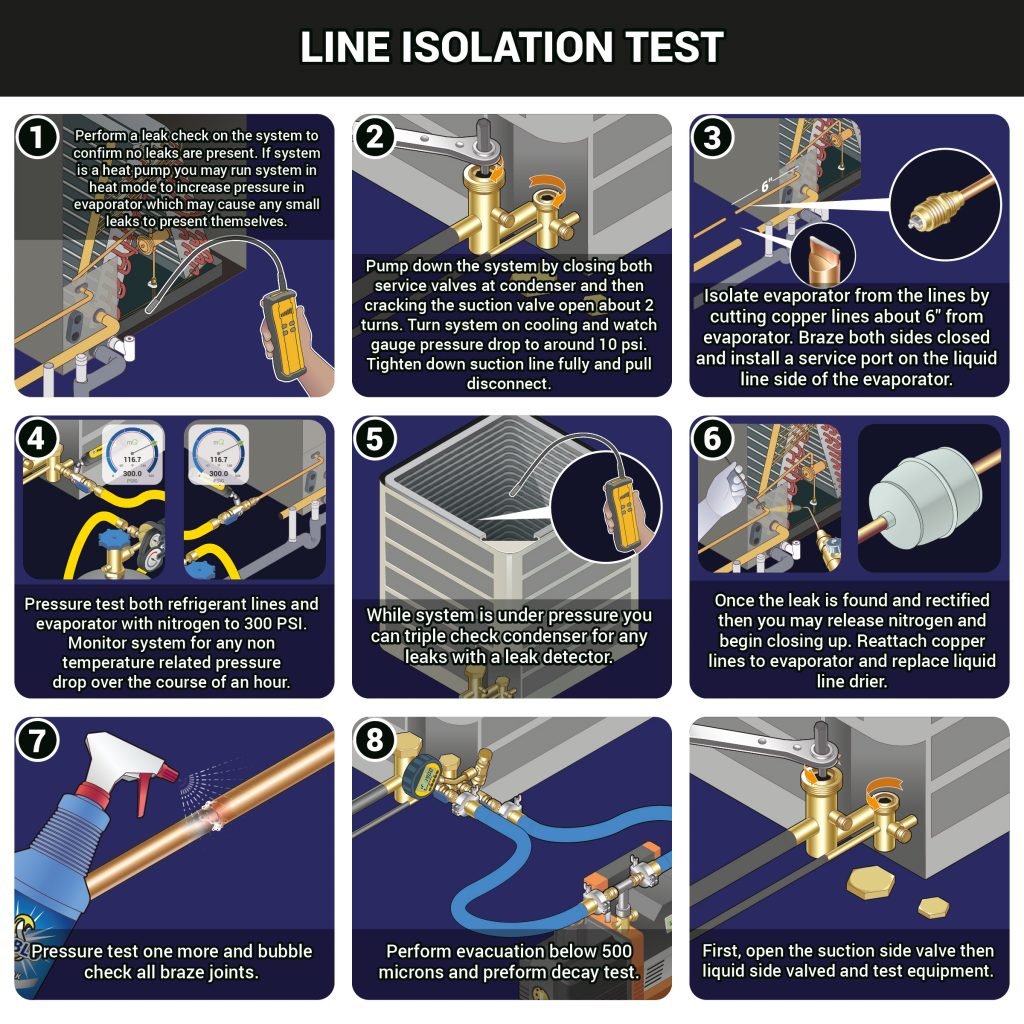
We’ve already won half the battle against callbacks once we know how our leak detectors work and how to handle their limitations. But there’s still a lot more to consider. We wrote a large article about the ins and outs of leak detection a while ago, which you can read HERE.
Again, the HVACR Learning Network has the new INFICON Leak Detection Technology and Best Practices course, which is completely free and qualifies for NATE credits. You can learn more at https://hvacrschool.com/leak-detection. The HVACR Learning Network also has two short, free courses on ultrasonic leak detection and leak detection tips.
P.S. — We also have a video where Bert shares some of his leak search tips, which you can watch HERE.
Special thanks to Matt Bruner for his editing assistance
Comments
To leave a comment, you need to log in.
Log In