Get Tech Tips
Subscribe to free tech tips.
Practical Uses of Combustion Analysis
This tech tip reviews the live stream by the same name aired on November 1st, 2023. You can watch the full live stream HERE. We want to give special thanks to the guests: Jim Bergmann, Jim Davis, Tony Gonzalez, Louise Kellar, Bill Spohn, and Tyler Nelson!
Gas furnaces (or any combustion equipment) create a controlled chemical reaction that releases heat. This chemical reaction consists of fuel (such as natural gas or propane), heat (from an ignition module), and oxygen (from air).
In a perfect scenario, this chemical reaction yields only heat, carbon dioxide (CO2), and water, mostly harmless to us in the amounts produced. However, a lack of oxygen in the combustion process may yield harmful carbon monoxide (CO). Nitrogen in the air or fuel may also introduce oxides of nitrogen (NOX).

Photo Credit: Fieldpiece
Combustion analysis is the only way to understand how well the combustion process is happening. When we do combustion analysis, we analyze the flue gases to help us understand the conditions by measuring the temperature, oxygen, and CO. While it may not sound practical for every job, there are things we can do to test combustion (or at least the dangerous byproducts of it).
Theoretical vs. Real Combustion
Theoretically, we could get 100% of our fuel to transform into energy, but that’s unrealistic. In reality, our combustion won’t be perfect because combustion air is imperfect. Even “ideal” real-world combustion yields a little CO and isn’t perfectly efficient. The two main categories of combustion are “fuel-rich” and “air-rich.”

Photo Credit: UEi Test Instruments
Fuel-rich combustion has heavy fuel levels relative to air, which may lead to reduced efficiency, higher levels of CO, dirty components, and poor fuel efficiency. Air-rich combustion has a much lower CO risk than fuel-rich combustion, but the oxygen levels are higher, and the fuel efficiency is also low in the more extreme cases.
Due to the safety concerns of fuel-rich combustion, we will want to have some excess air to tip the balance in favor of air-rich combustion. For more information about combustion air and excess air, check out this tech tip.
CO Measurements
Every technician should be able to test combustion equipment or, at the very least, wear a personal low-level CO monitor to measure ambient CO. This practice is critical even in the cooling season. We should test for CO anytime anyone has any kind of gas appliance in their home.
Using a personal low-level CO monitor will let you know if your customers have a safe level of CO in their homes. However, testing for CO protects contractors, too. Repeated exposure to CO, even at low levels, can reduce techs’ cognitive function over time.
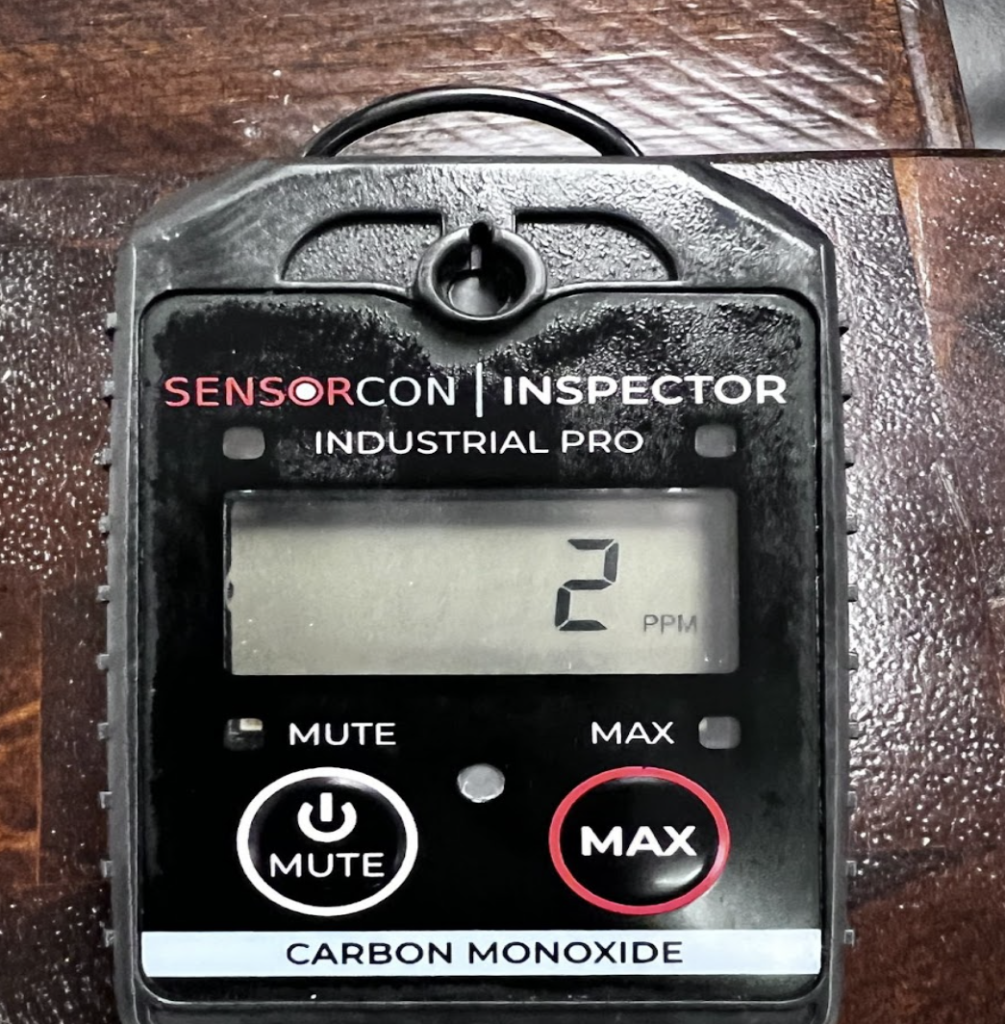
Photo credit: Jim Bergmann
Carbon monoxide is a colorless, odorless, tasteless gas that is only detectable with a monitor. It’s also deadly, as it displaces oxygen in the blood. When the equipment is the source of CO (instead of, say, car exhaust), we typically see higher levels of CO in the flue than in the living space. We usually want to measure no more than 100 PPM in the flue, but keep in mind that the CO limit will vary depending on which industry standard you choose to follow. Less than 100 PPM is a common target threshold well below the industry standard limits.
There are two separate CO readings: CO and CO air-free (COaf). COaf takes dilution by flue gases and excess air out of the equation, whereas a CO reading doesn’t account for other flue gases.
CO Thresholds

Photo credit: AccuTools Combustion Quick Start Guide
AHRI Guideline X sets forth CO thresholds for the airstream and inside the flue. Before measuring CO, ensure that your combustion analyzer has a resolution of 1 PPM. You’ll also want to conduct a thorough visual inspection, making sure you note any odd flame behavior.
Start off by taking an ambient CO reading to use as a reference for your airstream measurements. Once you run the appliance for at least five minutes, collect a return air reading near the system. Then, collect a supply air reading from a location where the air has already been mixed well. The readings will be the same if CO is not leaking into the airstream. In both cases, you will want to measure no more than 9 PPM.
As with the airstream measurements, you will want to ensure that the equipment has been running for at least five minutes before collecting CO readings from the flue pipe. The official threshold for CO in the flue per AHRI Guideline X is 200 PPM. (Other standards may accept readings up to 400 PPM COaf, but lower levels of CO are undoubtedly better.) If the reading exceeds 200 PPM, the next steps will be to verify that the equipment has been installed correctly and then check the heat exchanger for cracks or holes.
If you would like to read AHRI Guideline X, including its step-by-step approach to combustion analysis and CO troubleshooting, you can download it from AHRI’s website HERE.
Regardless of which industry standard you use, the CO target should be <100 PPM in the flue and ZERO PPM inside the structure. Those are the safest thresholds for your customer, and they are both achievable.
CO Risk Factors
White powder and rust around tubing, especially on gas water heaters, indicate flue gas spillage that may contain CO2 or CO. We don’t want spillage at all; CO2 is far less harmful than CO on paper but will still displace oxygen and could become CO if it is drawn into the equipment instead of combustion air. Remember: CO2 is a product of complete combustion, and CO is a product of incomplete combustion.
Keep in mind that a system can look great on the surface but have severe problems. That’s why walking around with a personal low-level CO monitor is crucial. We don’t want to downplay the importance of thorough visual inspections, but we want you to be aware that they may not tell the whole story.
CO Mitigation
By code, most new or renovated structures with gas-fired equipment must have at least a UL-2034 CO monitor. These monitors do not start alarming until they reach a specified PPM concentration within a pre-set time frame (e.g., 30 PPM over 8 hours or 150 PPM over 50 minutes). Low-level monitors alert occupants at far lower concentrations over shorter periods and are a worthy investment to customers.
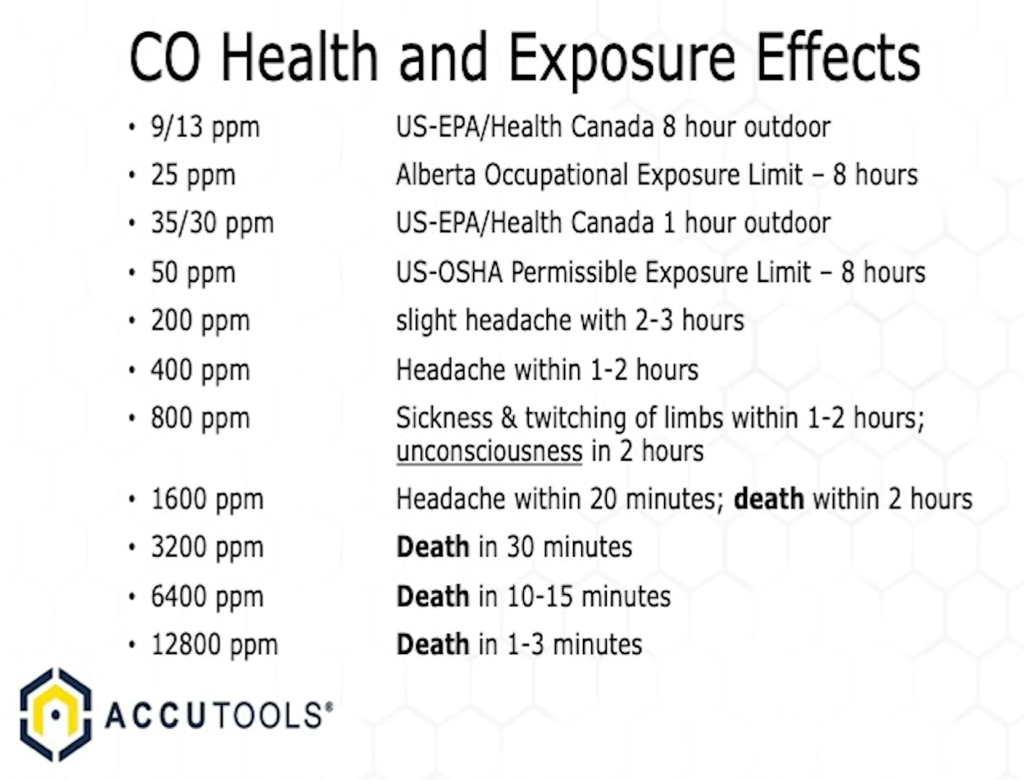
Photo credit: AccuTools, “Advanced Combustion Analysis” presentation by Jim Bergmann
While combustion analysis and CO monitors help us keep our customers safe, they also let us offer a valuable service to customers. In both cases, we’re using tools to generate qualitative and quantitative results that we can deliver (and charge for).
Combustion analyzers and CO monitors will let you quantify health, safety, and efficiency.
Ideal Combustion Analyzer Features
Ideally, we want a combustion analyzer with a NOX filter. NOX is a gas that interferes with CO sensors, and you may read unusually high levels of CO.
You may even read 0 PPM of CO in the flue with a NOX filter. Keep in mind that NOX filters are different from NOX sensors. NOX sensors detect and measure nitrous oxides, whereas filters prevent those nitrous oxides from affecting the CO measurement.

Photo credit: TruTech Tools, LTD
Oxygen and CO2 sensors can also help you determine what’s being produced by the combustion equation. Combustion analyzers also measure stack temperature to provide us with a complete understanding of the combustion equation.
What Should I Do When There’s Ambient CO?
Common CO-related problems include the recirculation of flue products back into the home (or the burner) and contamination in the combustion air zone, such as by car exhaust in a nearby garage.
When you have ambient CO, you’ll need to figure out the source and how that path goes back to the home. Recirculation can happen through vents (including fresh air vents) and even poorly made condensate traps.
Making Penetrations in Type B Vents
Manufacturers don’t include test points in B vents, and inspectors often tell techs that drilling a hole into the vent isn’t allowed.
You’ll want to check what the local codes say about B vent pipe; those codes have more authority than an inspector’s opinion. If there is nothing in the code that forbids you from drilling into B vent for testing, you should be allowed to do it.
HERE is a link to the manufacturers’ letters on testing and Type-B Vent.
Clocking the Gas Meter
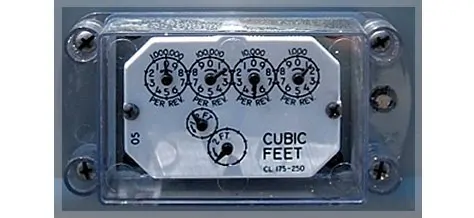
There are some mixed feelings about clocking the gas meter. Some people, like Jim Davis, believe it doesn’t make a major difference in operation (especially in industrial settings).
However, Jim Bergmann thinks it’s vital to clock the meter because clocking the gas meter allows you to manage the average heat content. This argument stems from the need to make sure the appliances get the correct fuel input they’ve been designed for.

Clocking the gas meter will be more critical for high-efficiency appliances, less so for 80% furnaces. High-efficiency furnaces condense water vapor in the flue; we want to manage the heat content to keep the stack temperature cool enough to let the water vapor condense and drain out. In 80% furnaces, we want higher stack temperatures to prevent water vapor from condensing.
If you know what side of the fence you’re on, great! If not, try to do a cost-benefit analysis for the given application you’re working on. And if you’re Team Bergmann-curious, you may want to check out this quick step-by-step guide to clock a gas meter.
Open-Ended Question: Who’s Responsible for Combustion Analysis Training?
The live stream ended with the following question:
“Who is responsible for combustion analysis training? Equipment manufacturers? Independent trainers and training organizations? Tool manufacturers?
While equipment manufacturers would ideally provide training that shows how to install and troubleshoot their appliances, they may not be privy to the less-than-perfect field conditions we see. Independent trainers are more likely to have experience with typical and straight-up bizarre field conditions and bring a different set of strengths to the table.
Who do you think is responsible? Feel free to let us know in the comments!
Comments
To leave a comment, you need to log in.
Log In