Aluminum Repair Tips – Short 132
In this short podcast, Bryan explains the basics of repairing aluminum, such as on coils or tubing.
Repairing aluminum can save lots of time on mission-critical calls and can help stop refrigerant leaks that lead to ozone layer depletion or global warming. Soldering makes almost all of the aluminum repair work we will do. (Brazing is possible, as aluminum has a melting point of 1200 degrees, but that’s still a bit too close to the brazing threshold.)
When working with aluminum, we need to recognize that it melts at a lower temperature than brass, steel, and copper, and it doesn’t change color. Aluminum is also thinner and almost fades away under excess heat.
First, you’ll want to figure out how to get the base temperature to the right temperature, usually with a flux. (Some fluxes require cleaning, some don’t; either way, we recommend cleaning.) The powder flux should go clear, and then you’ll be ready to apply the rod. In many cases, indirect heating can be difficult if not impossible.
After you choose your alloy, you need to choose your torch. We recommend using a swirl-tip air-acetylene torch. (It’s good to use a 3 tip for microchannel.) When working with an air-acetylene torch, you will run lower temperatures than oxyacetylene torches, but you will experience more convective heat. (Heat control is the key!)
When doing a repair, you want products that will make a solid bond to the outside of the joint. Make sure your products are for repairs, not for joining aluminum tubing.
If you do aluminum repairs on an evaporator or condenser coil, cut the fins out of the way. Make sure your work area is exposed and clean.
If you have an iPhone, subscribe to the podcast HERE, and if you have an Android phone, subscribe HERE.
Check out our handy calculators HERE.
Check out information on the 2022 HVACR Training Symposium at https://hvacrschool.com/symposium/.
Author:
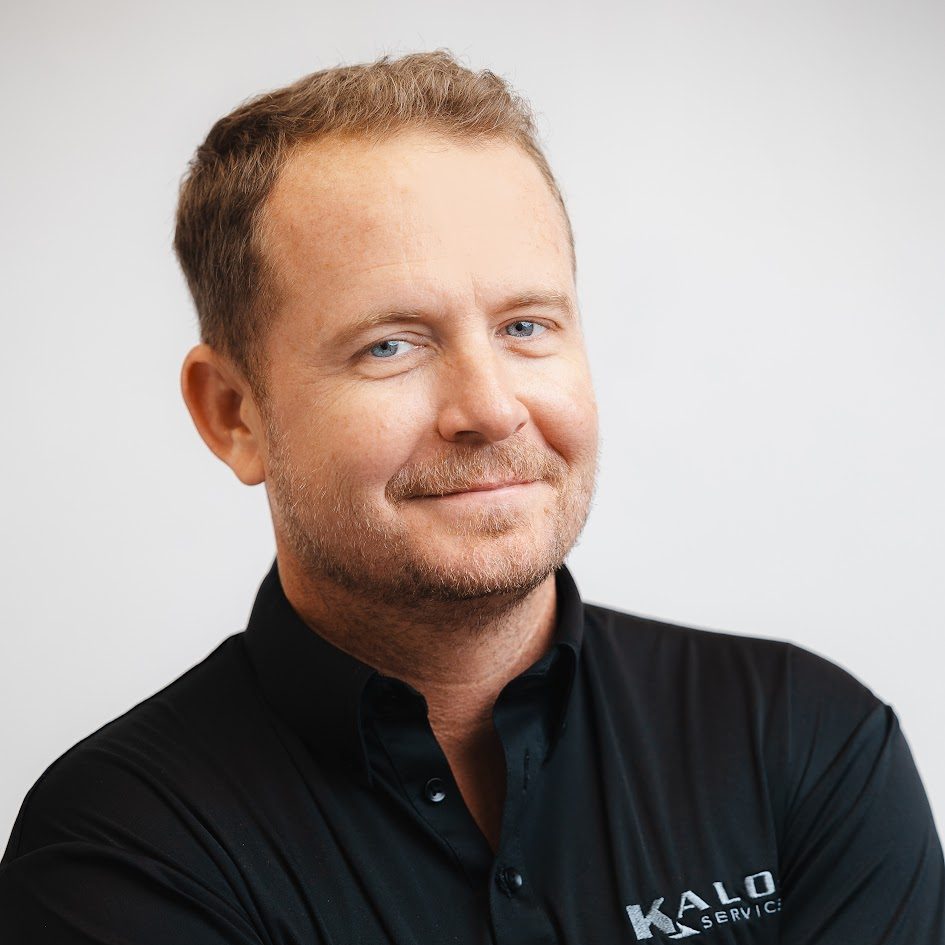
Comments
To leave a comment, you need to log in.
Log In