Get Tech Tips
Subscribe to free tech tips.
Oil Best Practices for HFC and HFO-based Systems
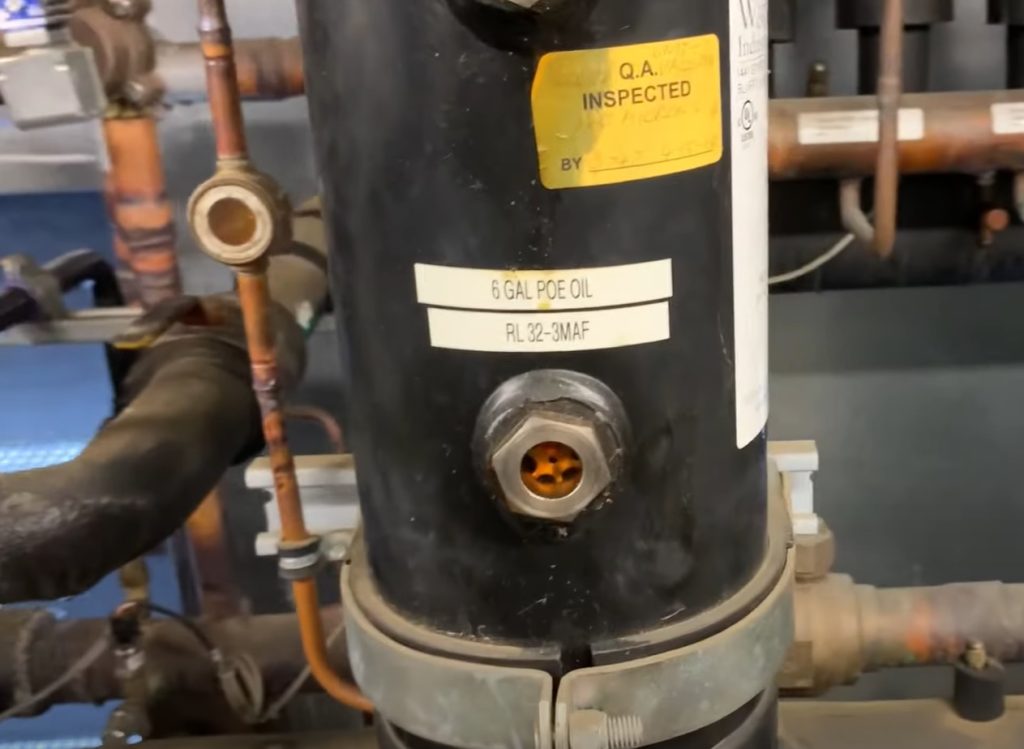
This tech tip was written by Don Gillis with Chemours. Thanks, Don!
The shift to R-410A from R-22 brought some pretty big changes to the industry, including the shift to polyolester (POE) oil. We had been using mineral oil for CFC refrigerants like R-12 and HCFCs like R-22, so we had to update some of our practices to deal with the new oil’s properties; for example, flowing nitrogen while brazing became a lot more important because POE could clean oxides off the tubing and cause them to clog filters and screens.
We’re currently in the middle of another refrigerant transition. Since we need to rethink some of our installation and service practices, I often receive questions about system oil. Will we see a shift to a different oil type, like when R-410A systems became a lot more common?
The good news is that the new A2L refrigerants, especially R-32 and R-454B (Opteon XL41), will continue to use POE oil. The POE oil used in R-32 systems will differ a bit from the oil used in R-454B and R-410A systems, but many of the properties and best practices will be the same.
This tech tip will cover some of those properties and best practices, but it’ll also go over the differences between the POE oil used in R-32 systems and R-454B systems.
Oil Properties
Bryan already has an article explaining the oil properties in detail, so I’ll go over some basic things manufacturers think about and why they matter.
HVAC systems use oil to reduce friction between load-bearing parts in a compressor. In other words, we want the oil to lubricate things like bearings to prevent overheating and mechanical wear. Lubricity is how well an oil minimizes friction between those moving parts.
No matter how good an oil’s lubricity may be, oil is useless if it can’t mix with the refrigerant and return to the compressor. That’s why miscibility, or the ability of an oil to mix and move with refrigerant in a system, is also so important. Mineral oil mixes well with CFCs and HCFCs but doesn’t mix well with HFCs like R-410A, so we started using POE oil.
One of the downsides of using POE oil is its hygroscopicity, which is its ability to absorb moisture. If you open an oil canister, the oil will absorb water vapor from the air. Even worse, POE oil interacts with water to form acid in a process called hydrolysis. This process can cause compressor burnout. Some hygroscopic oils don’t hydrolyze, like PAG and PVE, but those types typically have specific applications.
The final thing manufacturers tend to consider is material compatibility. That’s a fancy way of saying that oil should be able to move through line sets, not get into the motor windings, and overall just work well with the system components. Sometimes, the oil will need to be thicker in systems that have higher discharge temperatures; that thickness is the oil’s viscosity, which I’ll touch on later.
Oil Types and System Compatibility
So far, we’ve already covered two oil types in this tech tip: mineral oil and POE oil. But there are a few more types that we may come across.
Mineral oil is what we use for R-12 and R-22 systems. While it works well for systems that still use R-22 (or dinosaur systems that still use R-12, like some old chillers and classic car A/Cs), it’s not miscible with HFCs—like R-410A and R-32—or HFO blends like R-454B. It also doesn’t lubricate the compressors of HFC and HFO-based systems very well, so it can’t do its job.
Alkylbenzene (AB) is a synthetic oil comparable to mineral oil. You’ll typically find it in CFC or HCFC systems, especially low-temperature R-22 systems. AB is also compatible with mineral oil, and some retrofit HCFCs, like R-402B, require an AB and mineral oil mixture.
Polyalkylene glycol (PAG) is another synthetic oil mostly used in R-134A automotive A/C systems. It’s very hygroscopic, but it doesn’t go through hydrolysis and form acids like POE oil.
Polyvinyl ether (PVE) is a synthetic oil used as an alternative to POE in some systems that use HFC refrigerants. PVE is usually more common in ductless or VRF systems. Like PAG, PVE is hygroscopic but does not go through hydrolysis.
Polyolester (POE) is what we most commonly use nowadays; it’s required of HFC and HFO-based systems and compatible with CFC and HCFC refrigerants except R-12. We will continue to use POE oil as A2L systems emerge in the market.
If you’re working on a system with a Copeland compressor, I highly recommend reading Application Engineering Bulletin 93-11 to see which oil type is best for each compressor. With all that out of the way, let’s focus back on POE and mineral oil.
Key Differences Between POE and Mineral Oil
POE differs from mineral oil in four key ways, and those differences will require us to pay extra attention to how we install and repair systems.
Hygroscopicity
The first key difference is hygroscopicity, which I’ve mentioned a few times already. Mineral oil is not hygroscopic and won’t attract water molecules. Granted, that doesn’t mean we can be careless when opening systems for service, but we usually don’t have to worry about mineral oil pulling moisture in.
Pull a deep vacuum whenever you install or open a system that uses POE oil. Then, that system needs to stay sealed and only be opened for service. Remember: we want clean, dry, and tight systems.
POE oil is also so hygroscopic that it can absorb moisture through plastic, so you should only use POE oil out of sealed tin canisters. Never use POE oil from an opened canister or a container made of a porous material.
Hydrolysis
POE oil doesn’t just attract moisture; water reacts with the POE oil to break it down into its base parts: acids and alcohols. This process is not reversible, and those acids can eat away at the metal lines and components. You can end up with copper plating in the compressor and burnout.
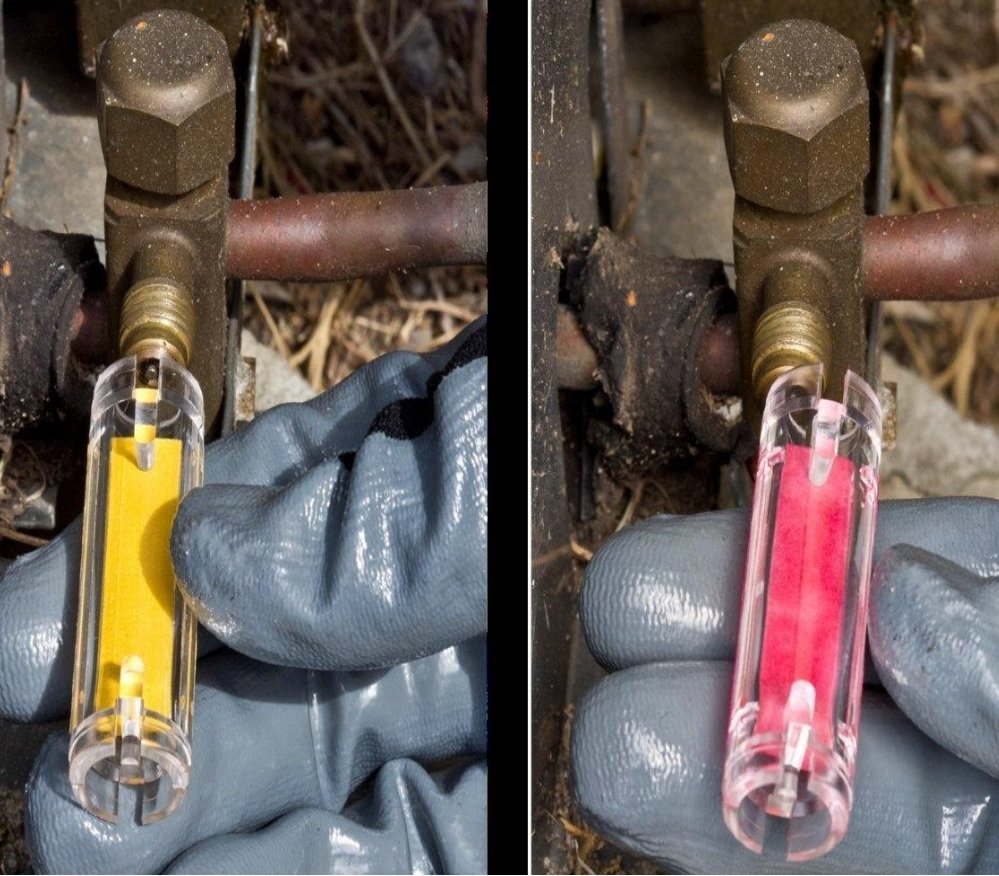
If you suspect the oil has been contaminated, you must do an acid test. A positive test will require you to start treating the system for burnout, including replacing accumulators, strainers on valves, and filter driers. In the photo above, the yellow test indicates a dry system that has tested negative for acid. On the right side, the test with the reddish color indicates that the system has tested positive for acid.
Additives
POE oil contains some additives, including corrosion inhibitors. Even though POE oil looks entirely liquid, those additives are actually solid matter.
When you have additives of any kind, whether they come with the oil or you add them to the system yourself, you’ll want to keep the refrigerant from getting too cold. Cold areas in the system allow the solids to begin clumping together, which can cause screens and driers to clog.
In general, I advise against the use of additives like leak-detection dye. Not only are you adding something that could clump up and cause restrictions, but you’re also changing the chemical makeup of the fluid in the system; pressure-temperature relationships will no longer be 100% accurate.
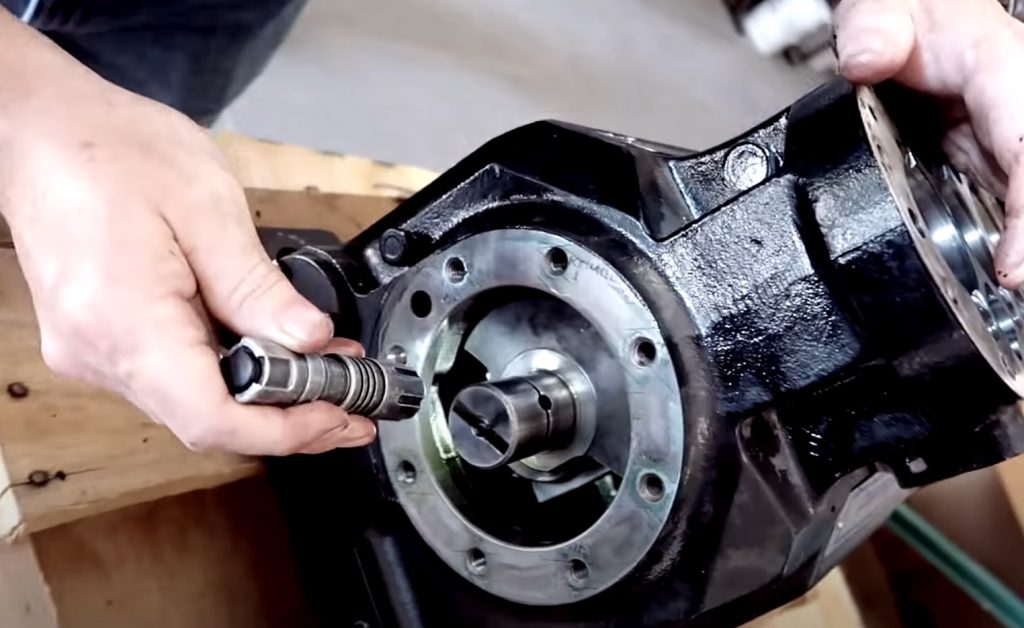
However, if you need to use dyes or other additives, be sure to follow the manufacturer’s guidelines.
Polarity
The molecular structure of POE, PAG, and PVE oils makes them attract water, but water isn’t the only thing these molecules attract.
POE is polar, meaning that its molecules cling to things like scale buildup inside the lines. As that POE oil moves through the line set, it strips cupric oxide from the insides of the piping. That black scale will clog valve screens, filter driers, and gunk up your lines.
Flowing nitrogen was less critical when we used CFCs and HCFCs because mineral oil doesn’t have that polar structure. If you were to install a system without flowing nitrogen while brazing, use mineral oil, leave it in service for 15 years, and cut open the lines, you’d see black scale by the joints.
But if you were to do the same for a system that uses POE oil, your tubing would be pretty clean—even though you’d probably have to replace clogged valve screens and filter driers along the way.
All of that is to say that flowing nitrogen is not overkill. We need to do it nowadays because POE oil is so common, and that extra step will save us a lot of grief (and clogged screens and driers).
POE Oil Viscosity
As A2Ls become more common, we’ll need to differentiate between POE-46 (for R-32) and POE-32 (used in R-410A and R-454B systems), which have different viscosities. Again, viscosity refers to the thickness of the oil; the higher the number, the thicker the oil.
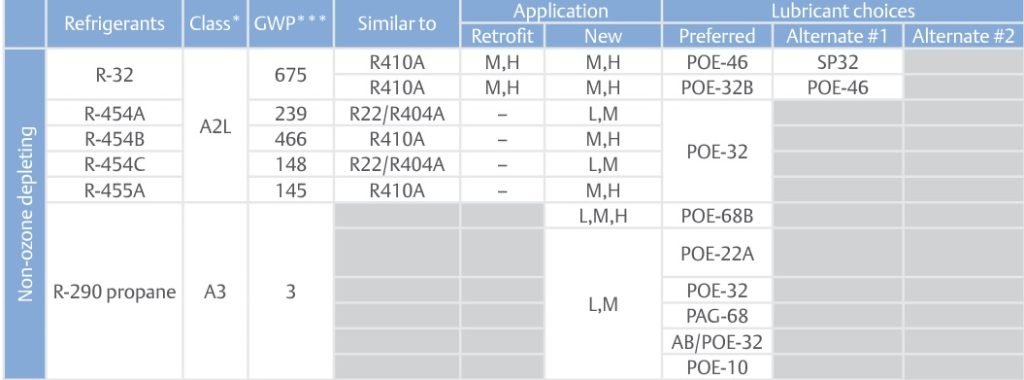
Credit: Copeland AE Bulletin 93-11
R-410A is a mixture of R-32 (a pretty good A2L refrigerant) and R-125 (a flame suppressant that isn’t great as a refrigerant). The flame suppressant quality of R-125 keeps the refrigerant cooler when it exits the compressor; in most cases, R-410A shouldn’t exceed 300°F inside the compressor, which translates to about 225°F six inches out from the compressor on the discharge line.
At 300°F, we start to see oil breakdown, so that’s why we have the “225 stay alive” rule. Without R-125 in the mix to keep the refrigerant cooler, R-32 has a higher discharge temperature. We need to use a thicker oil—an oil with higher viscosity—to prevent that oil breakdown from happening. POE-46 has a higher viscosity than POE-32, so we need to make sure that we’re using the right POE oil for the A2L refrigerant at hand.
Conclusion
All of this is to say that we need to make sure we’re using best practices because POE oil will continue to dominate the market as we transition to A2L refrigerants. Too often, I see compressors that don’t make it to their full lifespan because of burnout. When I come across a compressor that’s seizing and has copper plating inside it, I start wondering about that system’s installation and service history.
In many cases, these compressors aren’t failing earlier because manufacturers “just don’t make them like they used to.” In reality, poor system installation practices have lifetime effects on the system. That’s why it’s so important to flow nitrogen or clean flux off the tubing when brazing systems that use POE oil.
You can email me at don.gillis@chemours.com if you have any questions. If you want more information about Opteon products, visit https://www.opteon.com. Thanks, everyone!
—Don Gillis
Comments
To leave a comment, you need to log in.
Log In