Get Tech Tips
Subscribe to free tech tips.
How Similar Are A2Ls to R-410A?
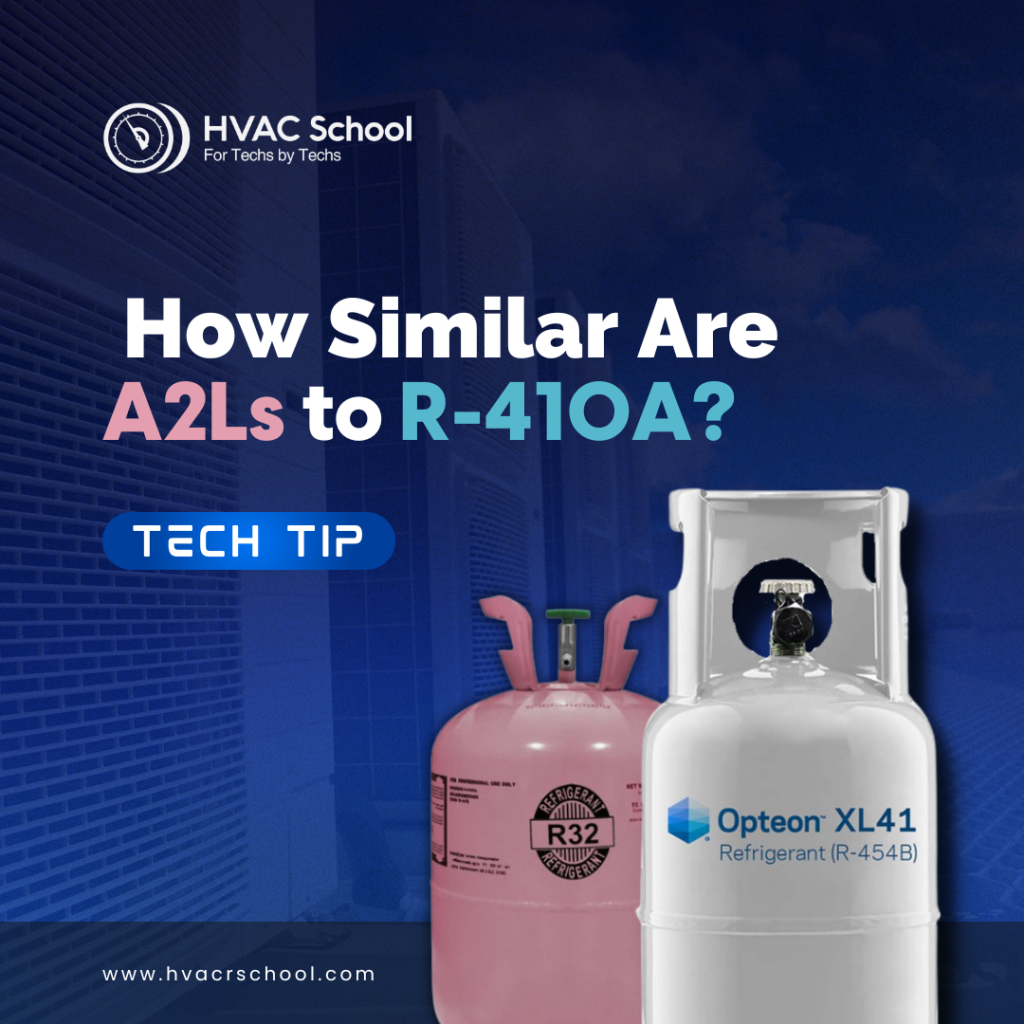
This tech tip was written by Don Gillis with Chemours. Thanks, Don!
You’ve probably heard it way too many times now: A2Ls are coming.
While we’ve heard a lot about what “A2L” really means and the R-410A phasedown timeline, there isn’t a lot of public information about what to expect on the service side. I’ve broken down some changes we’ll see with A2L refrigerants in THIS tech tip, including those related to tanks, tools, and the “best practices” that will soon be required. But that tech tip didn’t really cover what to expect for system pressures, capacity, and components.
I remember the big transition from R-22 to R-410A quite well and understand why there may be concerns about system pressures, oil, and other aspects of HVAC/R service. But in reality, the upcoming A2Ls are very similar to R-410A. Since most manufacturers have opted to use either R-454B or R-32, we now have a better idea of what service and performance will look like for HVAC/R systems that use those refrigerants.
Key Differences
Even though R-454B and R-32 are similar to R-410A in many ways, there are a few key differences between them that I need to bring up early.
The first and most obvious difference is the ASHRAE flammability rating. While all three refrigerants are non-toxic, R-454B and R-32 are mildly flammable A2L refrigerants. R-410A is an A1 non-toxic and non-flammable refrigerant. However, that doesn’t mean A1 refrigerants can’t combust; anything can burn at a high enough temperature.
Chemists have specific testing procedures for these refrigerants. Whenever a flame is propagated between two electrodes in a gas flask, it has to stay within a 90° V-shaped area to be considered a Class 1 refrigerant.
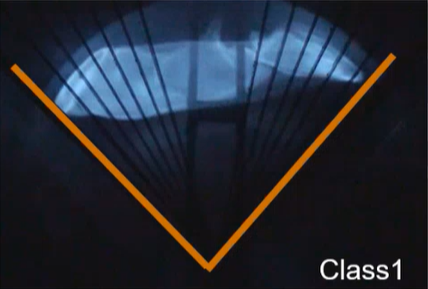
Credit: Chemours
For a refrigerant to be within the Class 2 threshold, the flame must stay within a 180° area (straight across instead of V-shaped). Class 3s propagate flames within a much bigger area—I’ll let you see that for yourself below.
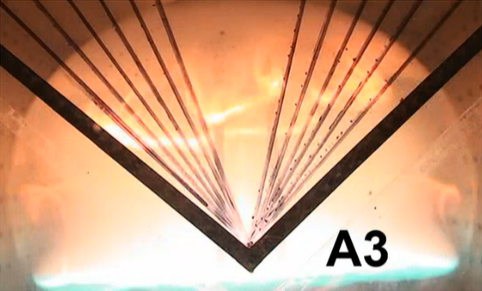
Credit: Chemours
The chemists hadn’t seen anything like the A2Ls, which propagated slow-spreading flames just barely outside the 90° threshold. So, ASHRAE made a new classification, Class 2L, for that reaction. A2Ls are non-toxic (A) and mildly flammable (2L).
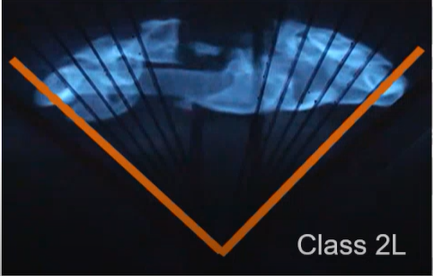
Photo Credit: Chemours
The second big difference between R-454B and R-410A is the GWP or global warming potential. R-410A has a whopping 2,088 GWP.
R-454B has a GWP of 466, which is 78% lower than R-410A. It’s hard to say that something is “future-proof” since no one can say for sure what the next phasedown may look like, but R-454B’s relatively low GWP should make it a refrigerant we can count on for years to come. R-32’s GWP is a bit higher, 676. We’ll come back to the GWP differences later on.
Thermodynamic Properties
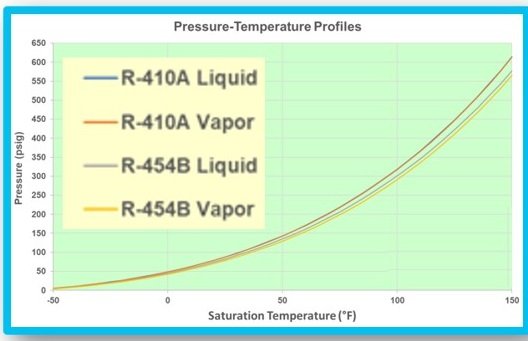
Credit: Chemours
Those of you who were around for the shift from R-22 to R-410A will remember learning how to work with new system pressures. R-410A has much higher system pressures than R-22, but we won’t see nearly as much of a difference between R-410A, R-454B, and R-32.
As you can see in the chart above, R-454B and R-410A have very similar saturation temperatures and pressures. Part of that is because R-410A and R-454B share a common ingredient: R-32, which also behaves similarly to those as a pure refrigerant.
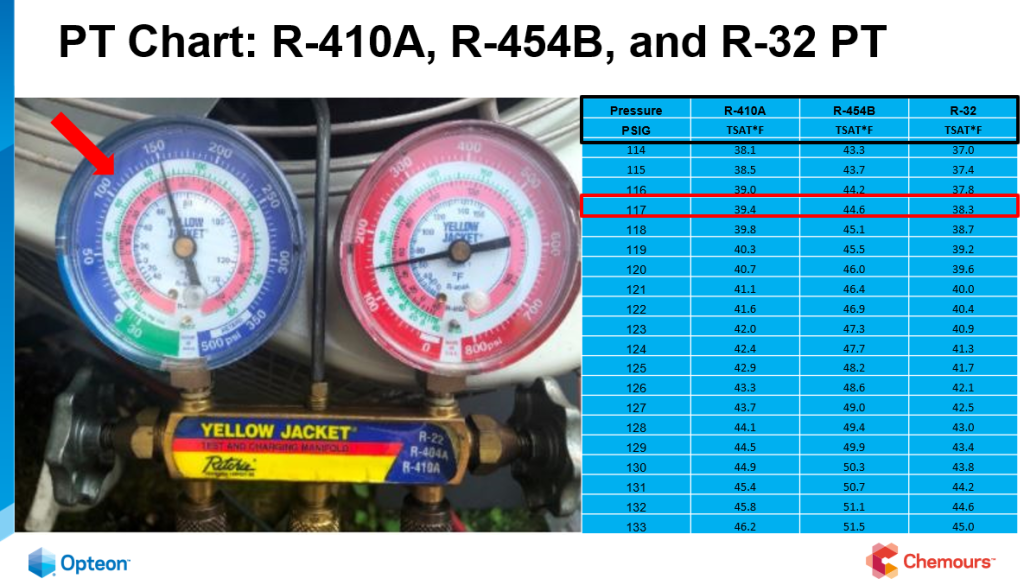
Credit: Chemours
’ve highlighted 117 PSIG in the chart above. It’s a ballpark figure of where the suction pressure could be on an R-454B system. The P-T chart tells us that the suction saturation temperature (SST) for an R-410A system is 39.4°F at that pressure. R-32 is very close behind at 38.3°F. R-454B is a little higher at 44.6°F.
All of those refrigerants have similar temperatures under the same pressure conditions. It’s not like the change from R-22, which has much lower operating pressures than R-410A.
Performance
Cooling capacity won’t differ that much between R-410A, R-454B, and R-32. Each one will deliver between 152 and 171 BTUs per cubic foot, with R-454B on the lower end (152 BTU/ft3) and R-32 on the higher end (171 BTU/ft3).
The coefficient of performance (COP) isn’t going to differ much between the three refrigerants, either. The COP is the ratio of how much useful heating or cooling we get out of the energy we put in. R-454B leads the way with a COP of around 3.68, but that’s still less than 0.1 better than the lowest of the three, R-410A.
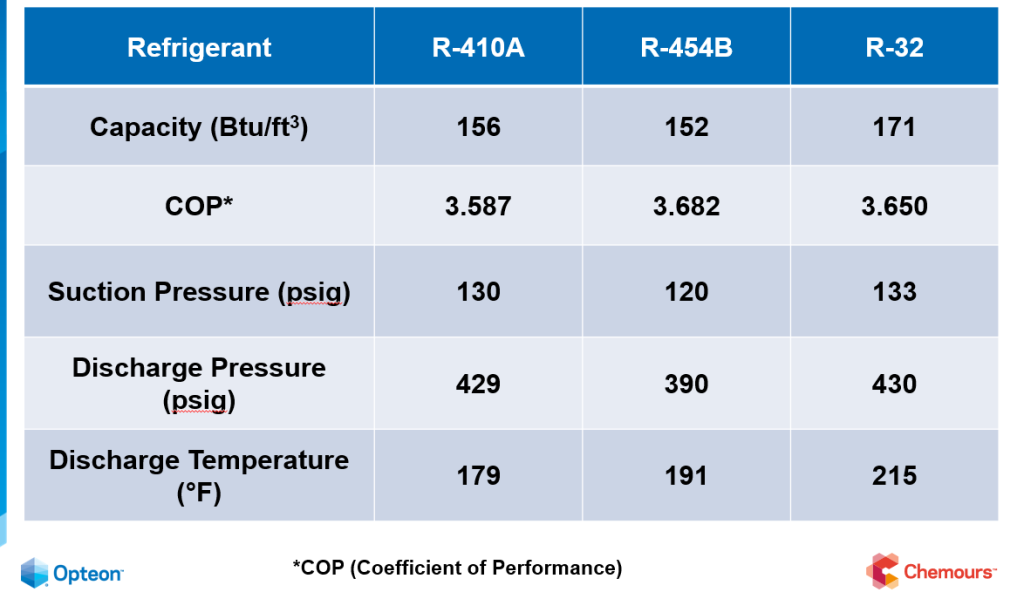
Credit: Chemours
As I said earlier, I was really blown away by the pressure differences when R-410A started replacing R-22—at the time, I didn’t know how safe it would be to keep a tank of R-410A in the back of my van. In this transition, we won’t have to worry about anything quite like that; the A2L suction pressures are within 10 PSIG of R-410A, and the discharge pressures (which already vary quite widely) are within 40 PSIG of R-410A.
The discharge temperatures are a little more critical. While R-454B is only slightly higher than R-410A, R-32 is much higher. There’s a rule I teach: “225 stay alive.” You never want to see a discharge line temperature reading any higher than 225°F six inches out from the compressor.
If we were to use the same oil as R-410A and R-454B on an R-32 system, we would get readings above 225°F and oil breakdown in the compressor. That’s due to a difference in chemical properties between the refrigerants.
Chemical Properties
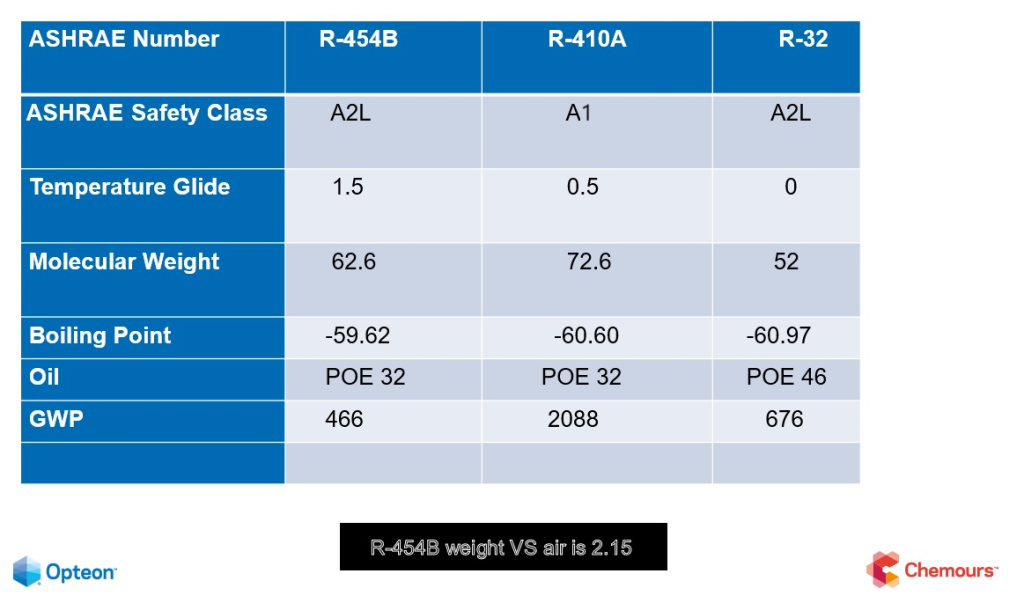
Credit: Chemours
As stated earlier, the main differences between R-410A and the A2Ls are the ASHRAE safety classification and GWP. R-32 has a GWP of 676, which is higher than R-454B.
We’ll want to keep an eye on the GWP in the future. Of course, nothing has been set in stone, but there has been talk of introducing legislation that could reduce the GWP cap to 500. If that comes to be the case, then R-32 won’t meet that new standard at its 676 GWP. R-454B would remain acceptable with its GWP of 466. While that’s not something we need to worry about right now, manufacturers have been keeping it on their radar.
Refrigerant Blends and Glide
Unlike R-410A and R-454B, R-32 is a pure refrigerant with no “glide,” like R-22. However, R-410A has such a small amount of glide that we treat it almost the same as any ordinary pure refrigerant in everyday service (though it’s best to charge it in the liquid phase). The same will be true for R-454B; even though there is a little temperature glide, it’s not enough for us to worry about things like dew point and bubble point.
R-32 is an ingredient in the R-410A and R-454B blends. R-454B is a mix of 68.9% R-32 and 31.1% R-1234yf, which has been used in cars for several years now (and in 9/10 of newly manufactured cars). R-410A is a mix of 50% R-32 (an A2L refrigerant) and 50% R-125 (used in fire extinguishers). The R-125 in R-410A reduces the flammability rating and keeps the refrigerant cooler, which is especially important when we think about discharge temperatures.
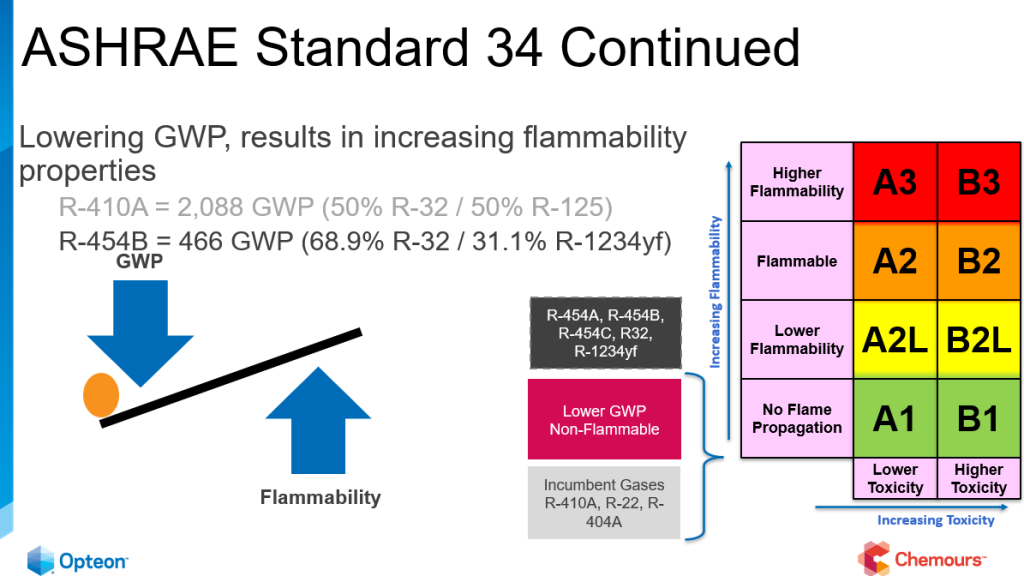
Credit: Chemours
Oil
R-454B and R-410A systems will use the exact same type of oil, but R-32 has higher discharge temperatures and will need an oil with a higher viscosity to withstand those temperatures.
While we use POE oil for systems that contain any of those three refrigerants, we use one type for R-410A and R-454B (POE-32) and a higher-viscosity type for R-32 (POE-46). You can learn more about oil and A2L refrigerants in the most recent tech tip I wrote before this one.
System Architecture
We won’t see any major changes to how our HVAC systems are set up as we transition to A2Ls. However, you will start to see more labeling to document refrigerant added via charging. There will also be mitigation strategies in systems with 3.9 or more pounds of charge. For example, there will be refrigerant sensors on indoor and outdoor coils (most likely using infrared technology); these will read the percentage of refrigerant concentration in the air, which will shut the system down and activate the air handler.
Line sizes will stay the same in like-for-like applications (always check with the manufacturer), and these new refrigerants don’t react with copper or any of the metals we’ve been using to make HVAC system line sets and components. However, there will be red caps on the service ports, which should help technicians identify A2L equipment.
In other words, you likely won’t need to replace the line sets if you change out R-410A equipment in a like-for-like installation. There will be no change in the way we clean refrigerant lines, whether we use flushes or purge them with nitrogen (again, check the manufacturer guidelines). It’s also a good idea to do a nitrogen pressure test to make sure they don’t leak. Some local codes may even require the pressure test.
Anything that could potentially spark will be insulated, even though A2Ls should NOT ignite under those conditions. Manufacturers are just adding an extra precaution. For example, metal-to-metal spades may be rubber-coated, and some manufacturers may have a protective covering over compressor wires.
The rest of the system architecture will really come down to local building codes. For example, some codes may require striker plates on the tubing to prevent puncture damage (such as by drilling nails or screws). Follow state and national codes, and keep in mind that the authority having jurisdiction (AHJ) will have the final say on what’s allowable in your area.
Conclusion
When you break down the thermodynamic and chemical properties of R-410A and its A2L replacements that will be in most new equipment, there aren’t a lot of big differences between them. Obviously, pressure settings will differ slightly, so components like TXVs will have different part numbers, but the core functions will stay the same.
We may have some changes in refrigerant oil viscosity (if using R-32) and minor differences across the board. However, there’s no need to worry about a large temperature glide, far-off system pressures, different line set sizing guidelines, or any of that. The biggest change is truly in the GWP of the refrigerant.
If you have any questions or want to learn more about the material covered in this tech tip, you can email me at don.gillis@chemours.com. Thanks, everyone!
—Don Gillis
Comments
To leave a comment, you need to log in.
Log In