Get Tech Tips
Subscribe to free tech tips.
Best Practices to Conserve A2L Refrigerants in a Shortage
If you own your HVAC company or are involved in management, you may have realized that our industry is currently facing a shortage of new A2L refrigerants, particularly R-454B and R-32.
Our own company has faced limited availability and long lead times, mainly due to supply chain disruptions and the increased demand now that our industry is primarily installing new systems with these A2L refrigerants. (According to ACHR News, there is a shortage of cylinders that meet the required safety criteria for A2Ls, not a shortage of the actual refrigerant. You can read that article HERE.)
Due to the shortage, prices have risen and will likely continue to do so, at least in the short term. The costs get passed along to our customers, and that’s something we want to mitigate as much as possible. This tech tip will share our company’s current plan to help our techs conserve R-454B whenever they’re on the job.
Tank Usage: Documentation, Documentation, Documentation
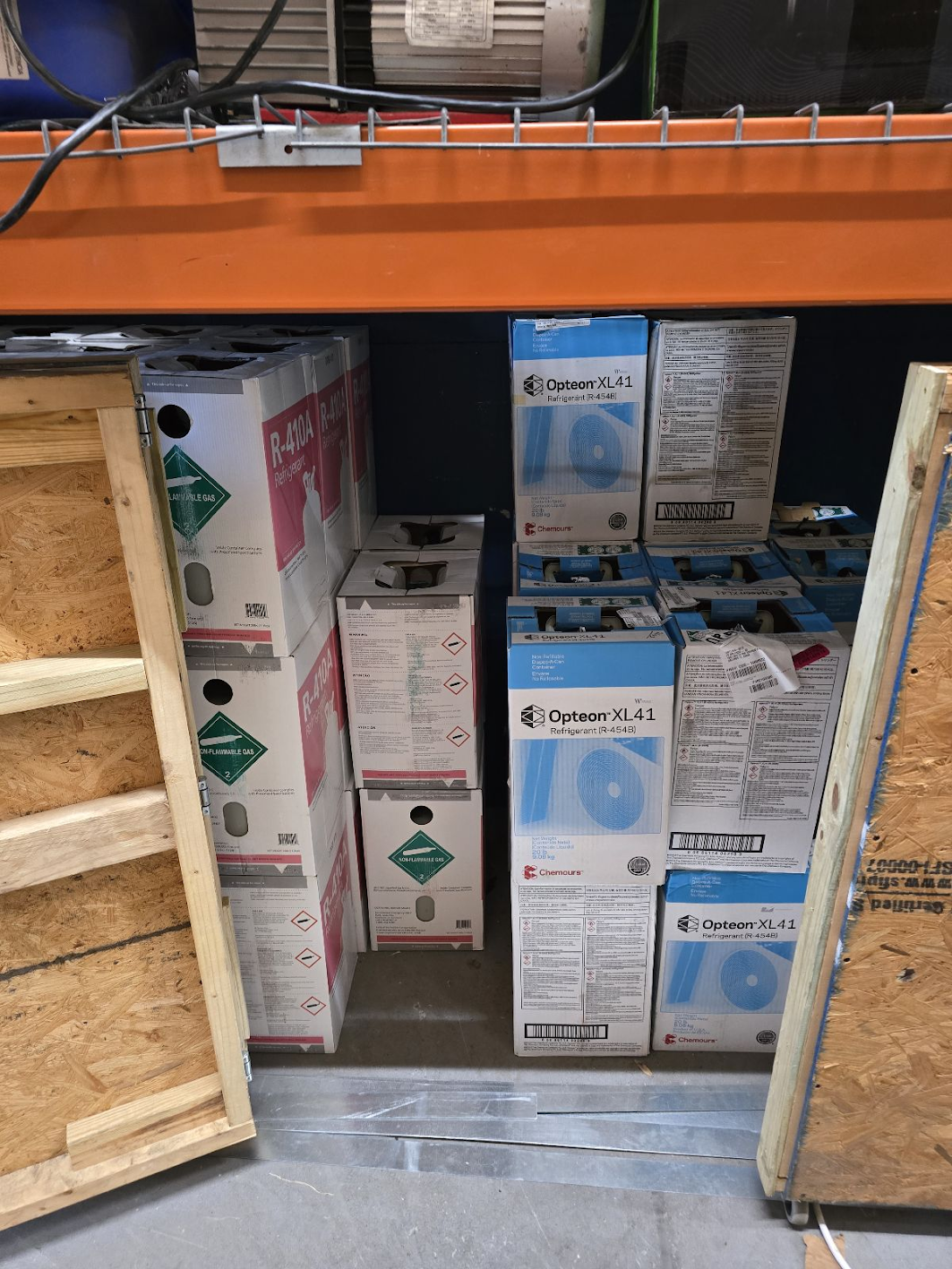
First and foremost, we need to document the use of refrigerant within the company so that we can track how it’s being used and eliminate waste.
At our company, all of our cylinders in use are tagged—both virgin refrigerant and recovery tanks. Our techs document how much refrigerant they use and recover, respectively, for safety and procurement purposes.
Every technician is required to write down the job number and how much refrigerant was used on the tag. This practice also encourages accountability and gives us a record of what was charged or recovered in case we get callbacks related to undercharge or overcharge.
Training for a Zero-Leak Policy
In an ideal world, there would be no leaks, and even if there were leaks, every leak would be found, confirmed, and patched without a hitch. Unfortunately, that’s not exactly realistic.
Thorough nitrogen pressure testing, evacuation, and leak detection are the keys here, as is a solid visual inspection. Each time we braze, we should be checking joints and connections to look for any possible leaks or imperfections—that means using a mirror to see behind and underneath the tubing, too.
We’re not going to get too deep into this topic since we have a comprehensive article about leak detection and mitigation, but the bottom line is that the system needs to be able to hold steady whenever you pressurize it with nitrogen (the exact pressure should be on the equipment data plate).
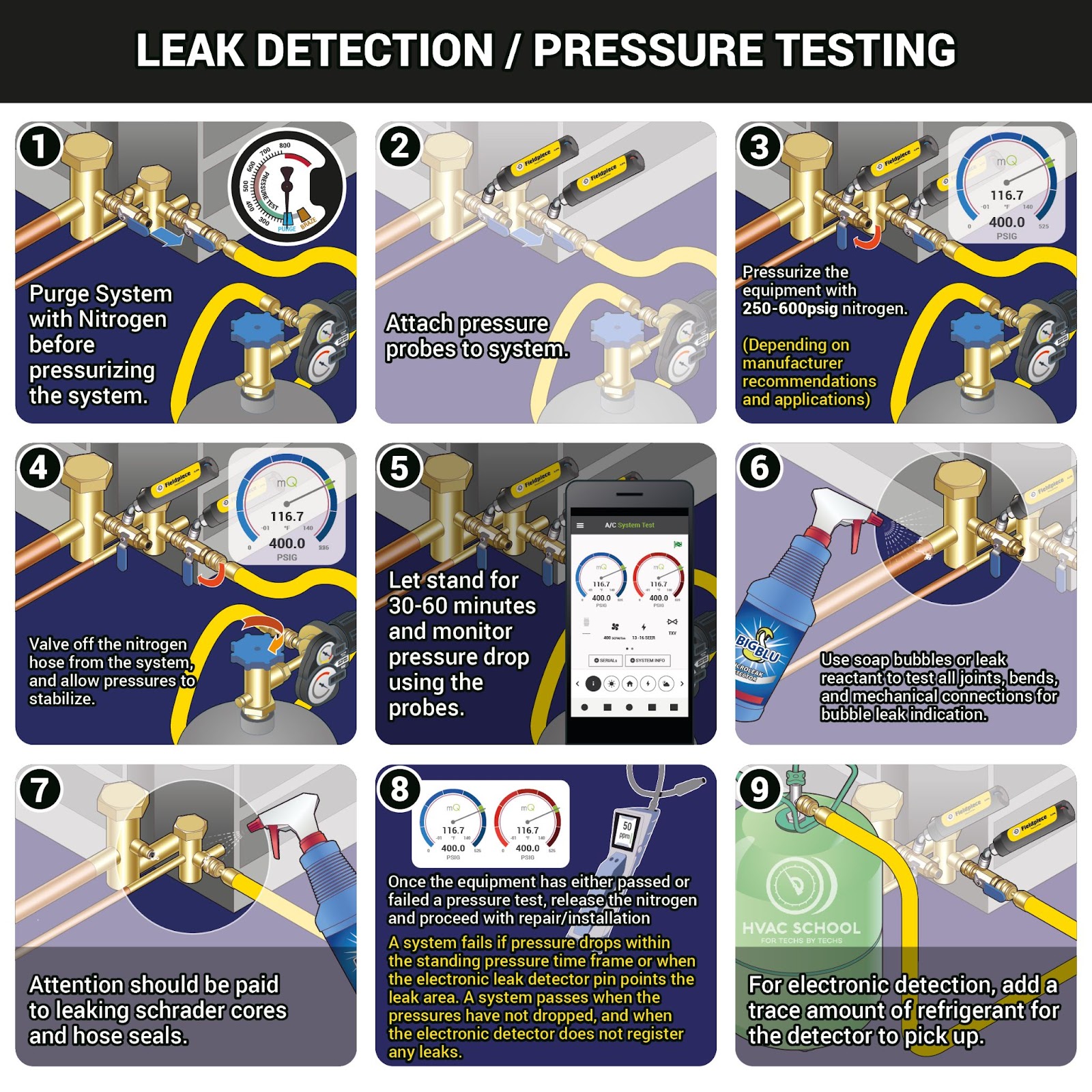
Residential systems up to 5 tons can usually do fine with pressure tests lasting 30–60 minutes, but we’ve asked our techs to make them last an hour. When you have larger equipment with more refrigerant, such as in light commercial settings, you may need to perform a longer pressure test. (On top of that, if the manufacturer calls for a specific duration, you’ll want to follow their instructions.) In refrigeration, the systems are so large that pressure tests may take 24 hours or more.
During the course of a pressure test, there may be significant changes in the ambient temperature, and you don’t want to mistake pressure changes due to temperature for leaks. You can use calculators like our Nitrogen Pressure Calculator in these situations.
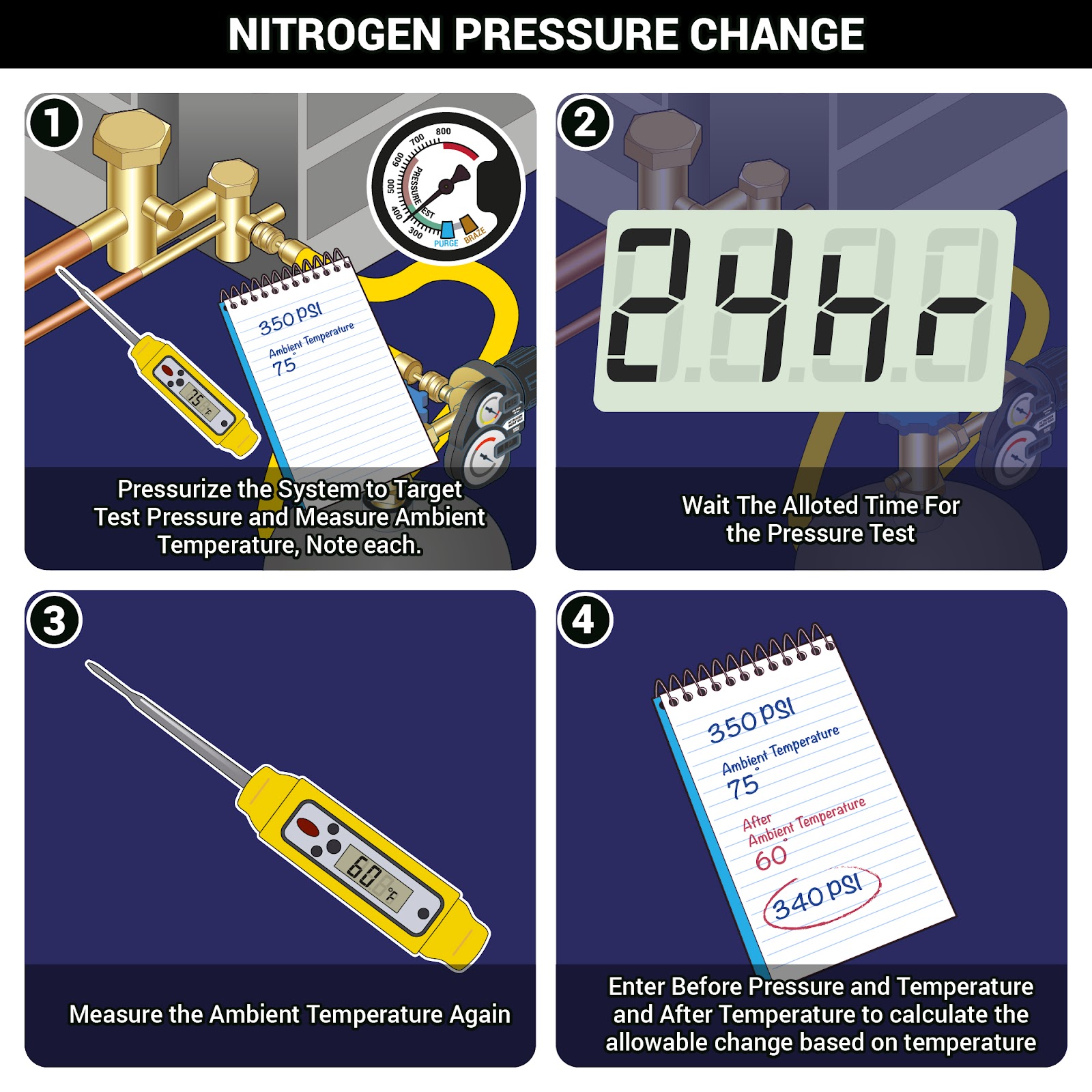
Deep Vacuums—With Documentation
Evacuation gets all of the air, moisture, and non-condensable gases out of the refrigerant tubing. A deep vacuum ensures that a refrigerant is clean, dry, and tight, which reduces the risk of oil contamination and can also confirm whether a system is leak-free.
Our process is to pull a deep vacuum below 300 microns on brand-new systems and at least 500 microns on systems that have been in service. Within 10 minutes, we don’t want to see the vacuum decay to above 500 microns or 1000 microns, respectively.
Apps like measureQuick, MyNAVAC, and BluVac (pictured) may also monitor your decay tests for easy documentation. The system’s behavior under deep vacuum can also tell you if you have a wet or leaky system; a wet system will have a sharp rise and then level off, and a leaky system will have a continuous rise.
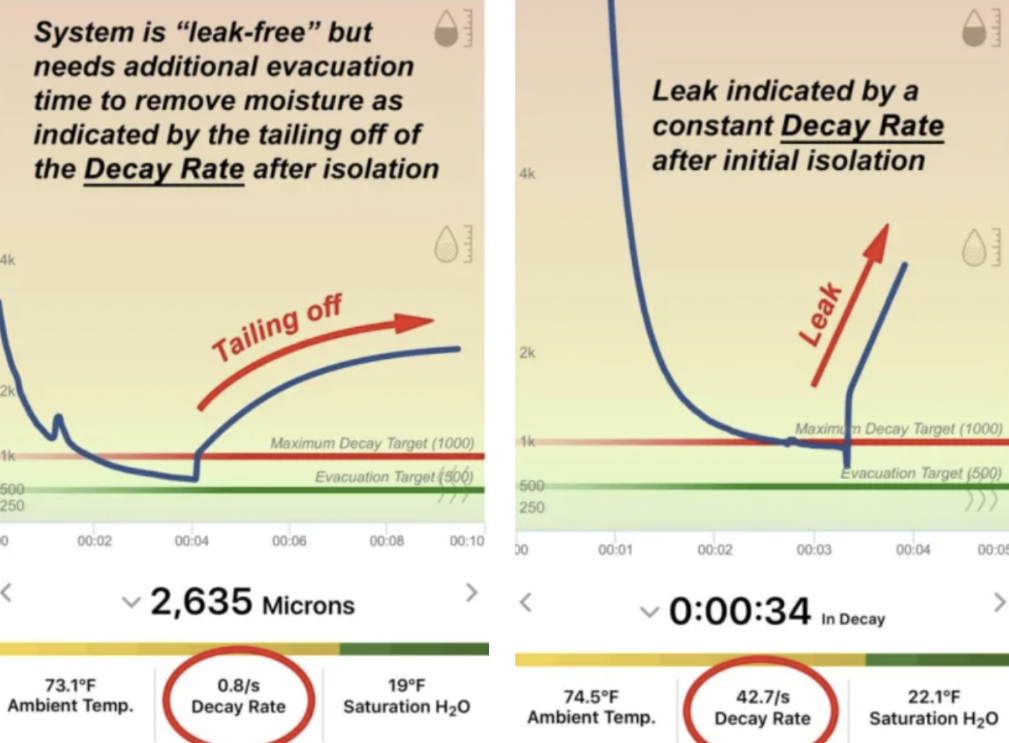
Having a procedure in place for techs to document decay test results, as with the refrigerant usage, also promotes transparency and accountability whenever there are refrigerant-related callbacks.
ALWAYS Use a Charging Scale and Allow Ample Time for the Readings to Stabilize
With leak detection and evacuation out of the way, we can focus on the charging part of the equation.
Whenever we charge or recover refrigerant, we should absolutely use a charging scale. Not just “when in doubt, weigh it out,” but anytime we use these A2Ls. Whenever you’re dealing with long line sets, you can use a calculator (again, like our Additional Charge Weight Calculator) to dial in the extra charge as accurately as possible.
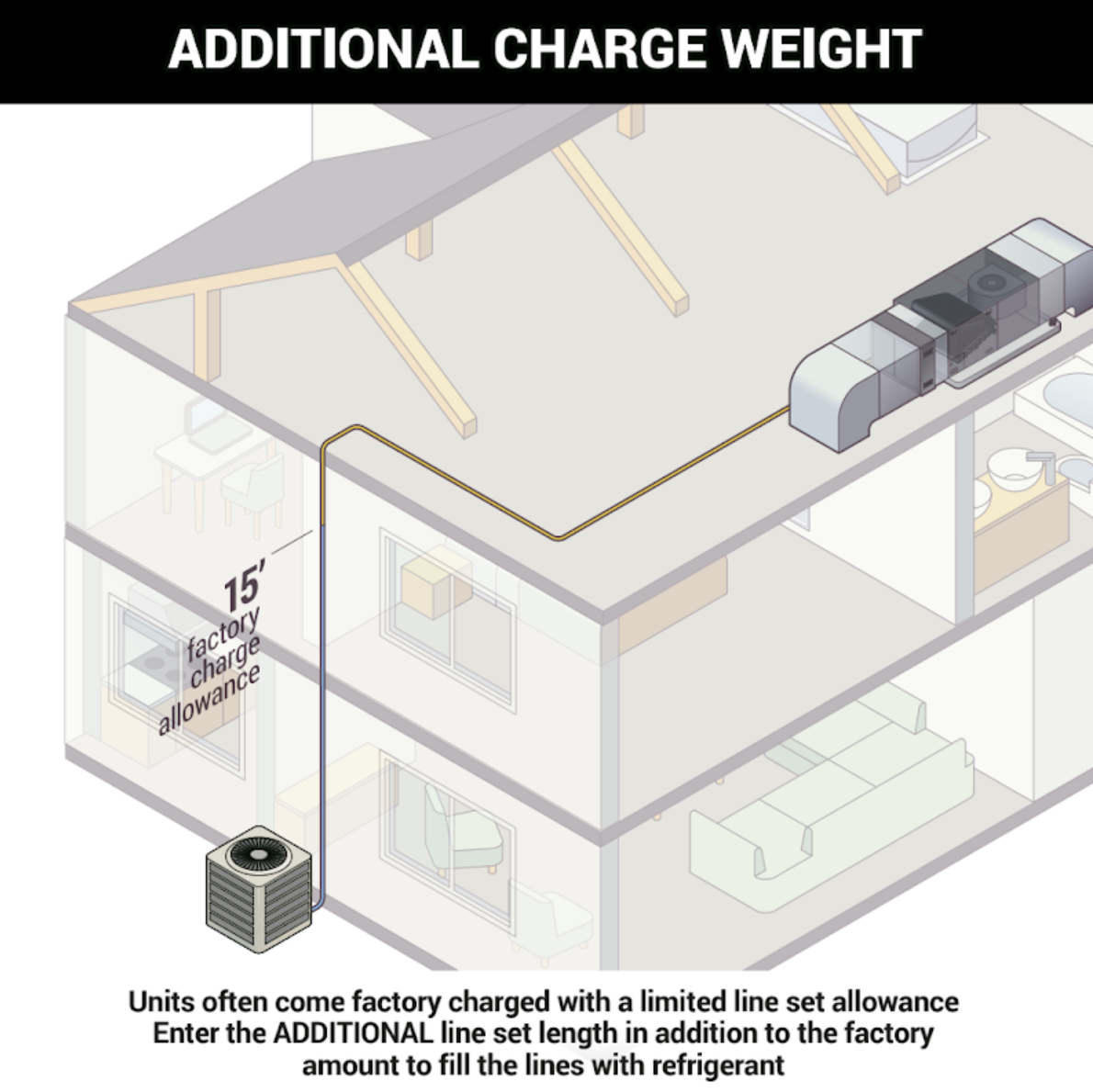
On top of that, allow some time for your temperature and pressure readings to stabilize, about 10 minutes or so, before adding more refrigerant. The less we have to recover later (ideally nothing), the better, even if it takes a little longer.
Every pound of refrigerant we lose through leakage isn’t just expensive—it may soon be irreplaceable if the packaging and supply chain issues aren’t resolved. Customers depend on us to keep their systems running; we must use the refrigerant we have wisely.
Our trainers worked to develop a training program based on leak detection, vacuum, and charging best practices. Below, you can find a list of HVAC School’s free resources in case you want to pull any materials for your company’s training programs.
Leak Detection
- Installation Best Practices: Brazing & Leak Checking (video)
- Leak Search Tips From Bert (video)
- Callback Prevention: Electronic Leak Detection (tech tip)
- Refrigerant Leak Detection and Prevention: Epic Article (tech tip)
Pressure Testing
Evacuation
- How to Evacuate an AC system, Full Vacuum Procedure (video)
- How and When to Use a Schrader Core Removal Tool (video)
- How to Evacuate an Air Conditioning System (Fast and Deep Vacuum) (video)
- Vacuum Best Practices (video)
- Vacuum: Moisture vs. System Leak (tech tip by Don Gillis)
- Two Tips for Tough Vacuum Jobs (tech tip by Matt Bruner)
Charging
- Low AC Refrigerant Charge – How to be SURE (Does it really need Freon?) (video)
- Refrigerant Overcharge Troubleshooting and Prevention (video)
- How to Charge a Brand New AC System (Weighing in Refrigerant by Line Length) (video)
- Charging Best & Worst Practices (video)
- Charging and Recovering with MeasureQuick (video)
- Checking the Charge Without Gauges (Our Process) (tech tip)
- Refrigerant Charging Basics For Air Conditioning & Heat Pump Systems (tech tip)
Comments
To leave a comment, you need to log in.
Log In