Get Tech Tips
Subscribe to free tech tips.
3-Phase Motors—The Basics

Fundamentally, three-phase, alternating current (AC) motors are about as simple as a motor gets. The power company produces three phases by spinning magnets. Then, on the other end, we produce electromagnets that spin the motor according to the same 60 cycles per second frequency (60hz). All three phases are 120 degrees out of phase from one another and work really well at turning a motor.

Let's look at some of the things to consider about three-phase motors.
All the Obvious Things
The motor needs to be a physical size that fits, it needs to be the correct voltage, and it needs to be rated to do the job it is doing. You can't put in a motor with a horsepower/wattage/current rating that is too small. However, you may occasionally use one that is larger than the rating so long as it fits and the conductors, overloads, etc., are appropriately sized.

Internal vs. External Overload
Many motors have internal overloads that will shut the motor off when it overheats. Others will require an external overload either at the motor or, more commonly, built into the “starter,” which is essentially a contactor and an overload relay combined.
Motor Rotation
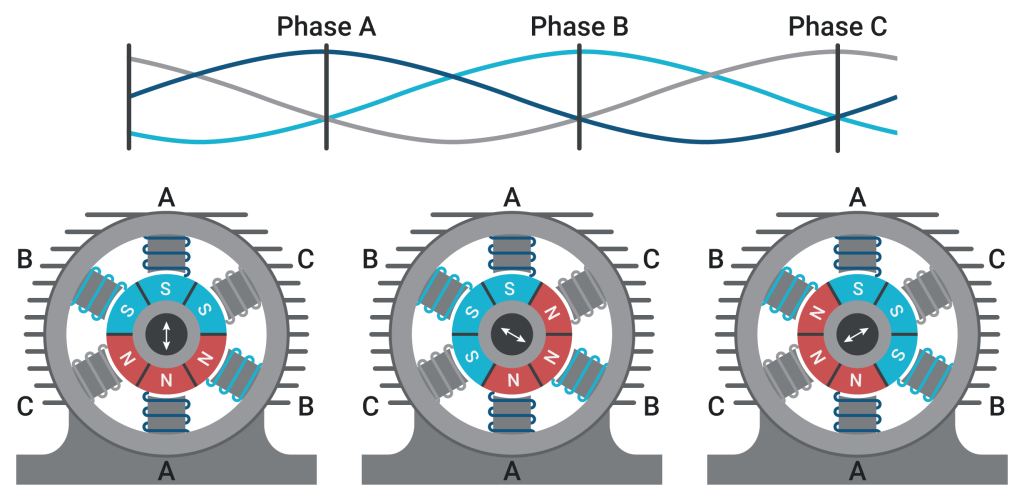
A three-phase motor can easily run in the opposite or possibly the wrong direction by swapping any two phases entering the motor. Blower motors and scroll compressors are the worst about running in the wrong direction if they are wired incorrectly. Also, keep in mind that if the blower is connected to a VFD and the compressor is not, the blower could be running in the correct direction because the VFD can correct the phase rotation.
Always make sure that blowers and compressors are running in the right direction before leaving them running.
Three-Phase Voltage & Current Imbalance
Voltage imbalance is a motor killer. It causes poor motor performance and increases winding heat, which leads to premature failure. In the case of HVAC blowers and compressors, this additional heat ends up in either the refrigerant or the air, which must then be removed, further decreasing efficiency.
To test for three-phase imbalance, always check from phase to phase, not from phase to ground, with the motor running. You simply check the voltage from each of the three phases to one another and find the average (add all three and divide by three). Then, compare the reading that is furthest from the average and find the percentage of deviation. I know that sounds like a giant pain for most of you, so we made this easy calculator for you (top right).

The US Department of Energy recommends that the voltage imbalance be no more than 1%, while other industry sources say up to 4% is acceptable. In general, you will want to make SURE the imbalance is below 4% and work to rectify anything over 1%.
The same thing is true of the current. Because three-phase motors have windings with the same resistance, they should also draw the same current while running. Investigate any major variation by double-checking the voltage imbalance and checking the resistance of each winding. We also have another tech tip with a bit more information about voltage imbalance in three-phase motors.
No Capacitors
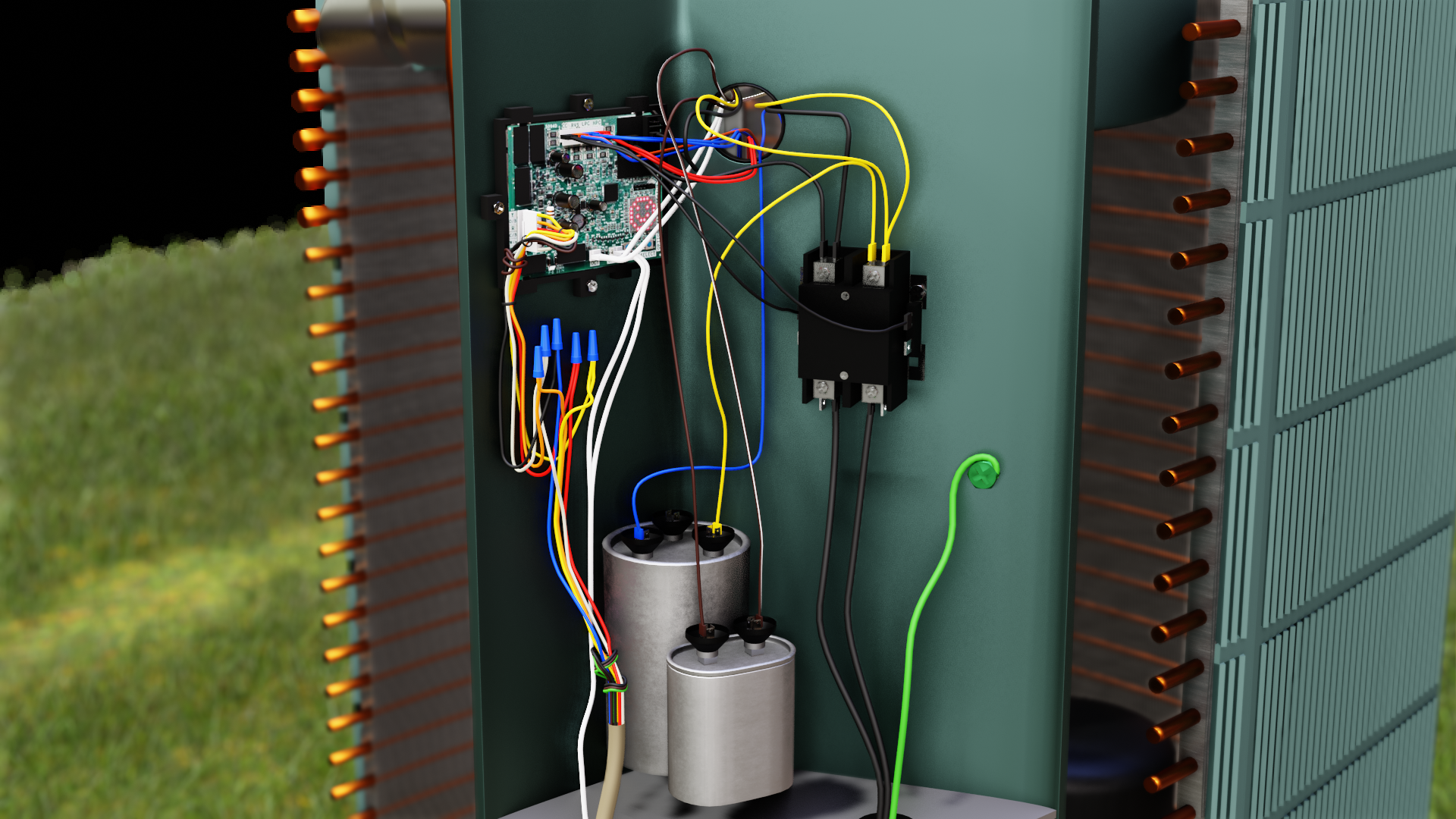
Three-phase motors don't require run or start capacitors, as having three phases solves all those issues. They may be a part start or use other “soft” starting strategies, and there may be capacitors used for power factor correction, but neither of these is the same as the good old single-phase run capacitor, so that's a plus.
There is a lot more to know, but this is just an introduction to the basics I don't want you to miss.
—Bryan
Comments
To leave a comment, you need to log in.
Log In