Why Measure Compressor Discharge Line Temperature?
August 23, 2022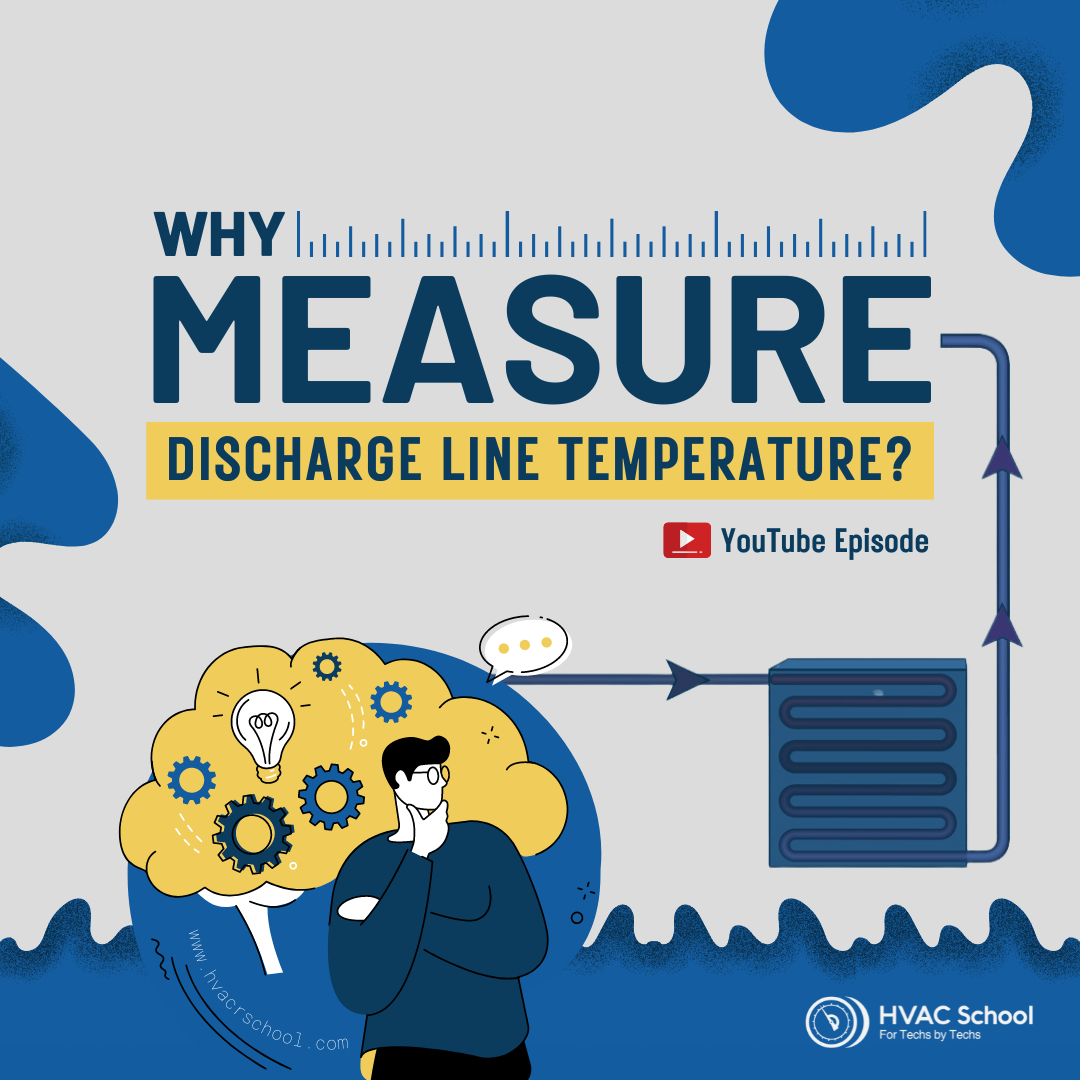
The discharge line is the smaller line that exits the compressor and eventually feeds into the condenser. On a heat pump, it normally goes into the reversing valve from the top.
The discharge line should not be confused with the liquid line, which goes out of the condenser. You can expect the discharge line pressure to be a bit higher than the liquid line pressure, but its temperature will be way higher than the liquid line temperature. That’s because the condenser desuperheats that very hot vapor, condenses it to a liquid, and cools it below the saturation temperature (subcooling).
Like the suction line, the discharge line contains superheated vapor. However, the temperature of the discharge line is much, much higher than that of the suction line.
You can use Bluetooth probes to measure the discharge line. Several things impact the discharge line temperature, including the location. Normally, we want to measure the discharge line temperature about six inches away from the compressor; the temperature can vary quite a bit depending on where we take our measurements, so the industry standard is typically lower than 225 degrees six inches from the compressor outlet. However, individual units may have higher or lower specifications. (The compressor may be around 70 degrees hotter, and the area near the condenser will be significantly cooler.)
Normally, when the compressor exceeds 300 degrees, oil breakdown may occur. Higher temperatures result in oil with reduced viscosity, meaning the oil becomes thinner and cannot lubricate the bearings as well as it should. Mechanical wear in the compression chamber is another problem that can be discovered by finding a high discharge line temperature. So, we want to run compressors as cool as possible.
High compression ratios may cause compressors to overheat. So, we want to do whatever is in our power to reduce the compression ratio. We can find the compression ratio by dividing the absolute head pressure by the absolute suction pressure, and we typically want that quotient to be ~3 for modern air conditioning equipment (refrigeration equipment tends to have higher compression ratios).
We can reduce compression ratios by keeping the compressor cooler, such as by using interstage cooling or liquid or vapor injection to reduce discharge temperatures. Dirty condensers that restrict airflow also raise the head pressure, increasing the compression ratio and resulting in higher discharge pressures. Significantly overcharged systems may also raise head pressure.
Low suction pressure also leads to higher compression ratios; low suction pressure may be caused by low loads or metering devices that feed the evaporator coil poorly. However, cooler suction lines don’t necessarily cause the discharge line to be cooler, especially if the mass flow rate is also low.
Copeland Mobile can show you how operating a system outside its operating envelope can contribute to poor system performance (assuming you’re working with a Copeland compressor). You can adjust the conditions within the app to see what the discharge temperature, compressor capacity, and mass flow rate will be under various operating conditions. You may find it exceptionally helpful when used with the AE Bulletins app, which contains useful information about Copeland compressors.
Comments
To leave a comment, you need to log in.
Log In