Static Pressure and Manometer Basics
June 16, 2022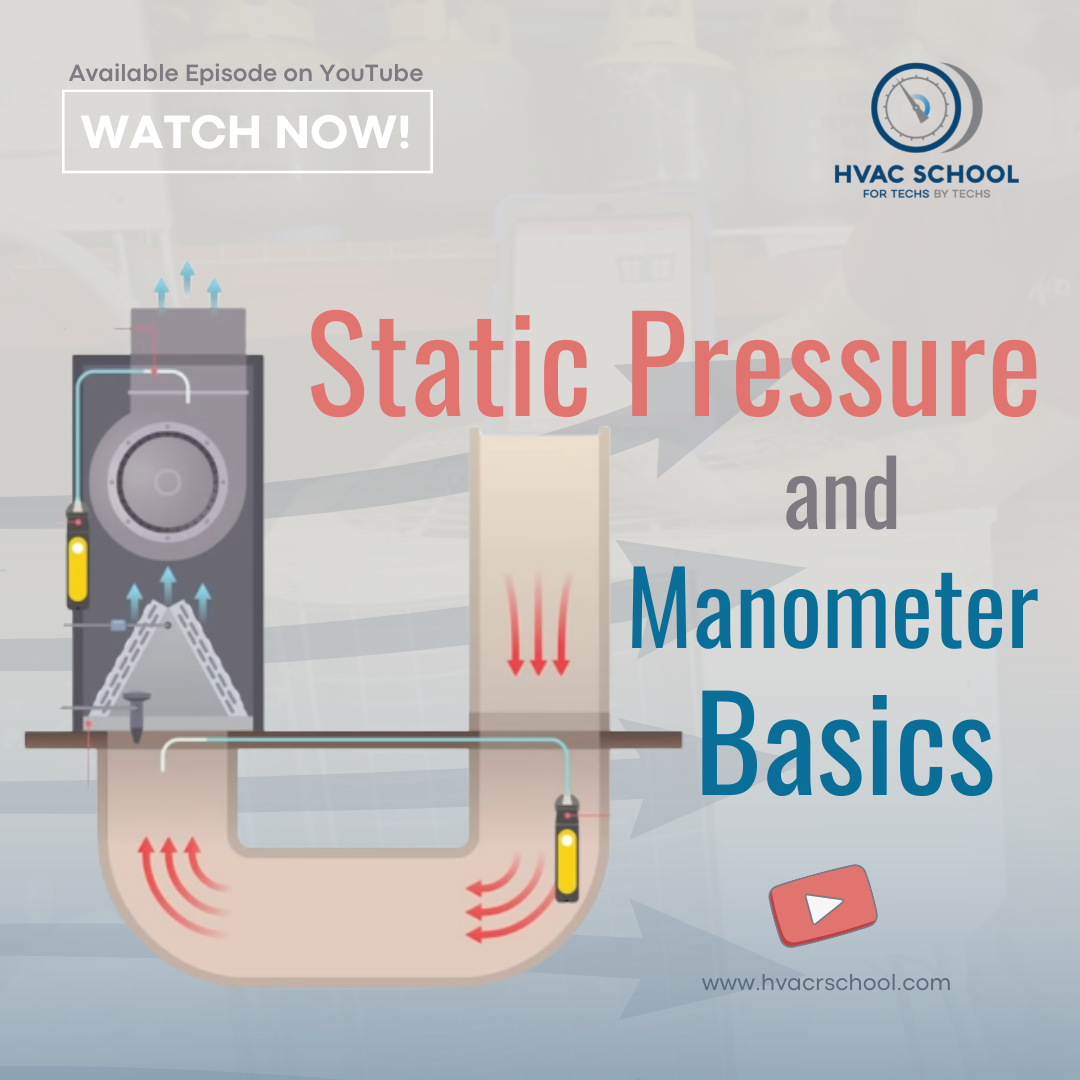
Utility manometers are your typical standard service manometers; they are designed to measure pressure in inches of water column (“WC, “H2O, or inWC). Inches of water column are smaller units of measure than PSI, and they’re ideal for static pressure and gas pressure. Some utility manometers have one port, and others are dual-port manometers. Single-port manometers require you to zero them with the hoses on before taking the measurement. (Accurate zeroing is very important, especially as pressure continuously changes with the weather.) Dual-port manometers are often used for measuring a pressure differential, and zeroing is typically less critical because there is already another baseline for comparing the pressure.
There is no such thing as “zero pressure.” The closest we can get to “zero” pressure is 14.7 PSI, atmospheric pressure, so zeroing out single-port manometers is critical.
Precision manometers use Pascals instead of “WC, which is a much smaller scale. We use precision manometers to measure duct leakage or envelope leakage (such as through a blower door test). We can also use the tiny Pascal scale to measure pressure imbalances between rooms and mitigate pressurization/depressurization problems.
Static pressure probes look an awful lot like pitot tubes, which have tubes within tubes. A pitot tube takes a measurement that’s a combination of static pressure and directional force. Pitot tubes then subtract the static pressure to yield only the velocity pressure; these tools require precision manometers to do their jobs properly. Pitot tube usage is more common on the building science side of the industry than HVAC service.
Static pressure probes each have a closed end at the tip and some side ports, and they only measure static pressure. The probes face the opposite direction of the airflow and measure the force exerted in all directions (against the walls of the duct). Static pressure can be either positive or negative in reference to the atmosphere, and we typically measure it by putting one tube in the return before the blower and the other above the blower in the supply plenum in a fan coil or handler on a heat pump or straight-cool A/C (or below the coil on a gas furnace). In gas furnaces, the coil provides a pressure drop and is separate from the actual unit.
The rated static pressure can be found on the data tag; a static pressure that differs from the rating will affect the system’s performance (though there is typically an operating envelope). If the static pressure is higher than the test static on the data plate, a variable-speed blower will have to ramp up to maintain the airflow, increasing operating costs and the amp draw while negatively impacting the motor’s longevity. Filter changes can cause the static pressure to change over time. You can also measure pressure drops over the filter and evaporator coil to isolate problems with filters or coils.
Static pressure is NOT airflow; it’s a pressure measurement, but it can be an indicator of airflow. Before we can measure the static pressure accurately, we need to make sure the system is producing the proper airflow (high-stage, no dehumidification mode). Although checking static pressure isn’t something we need to do on EVERY call, it’s worth checking when there are airflow complaints. Total external static pressure, supply, and return static are all worth checking to see if there are restrictions across filters or coils or other possible airflow problems.
Filters can cause many problems, and static pressure readings can help you pick up restrictions caused by filters. Larger filters (4″) with greater surface areas tend to create far less of a pressure drop and last longer than shallower filters (1”), which can clog and restrict airflow quickly.
Comments
When calculating CADR of a portable air purifier is it reasonable to use the blower CFM with 0.00 static pressure?
When calculating CADR of a portable air purifier is it reasonable to use the blower CFM with 0.00 static pressure?
To leave a comment, you need to log in.
Log In