Rack Refrigeration 101 Definition and Overview
November 18, 2021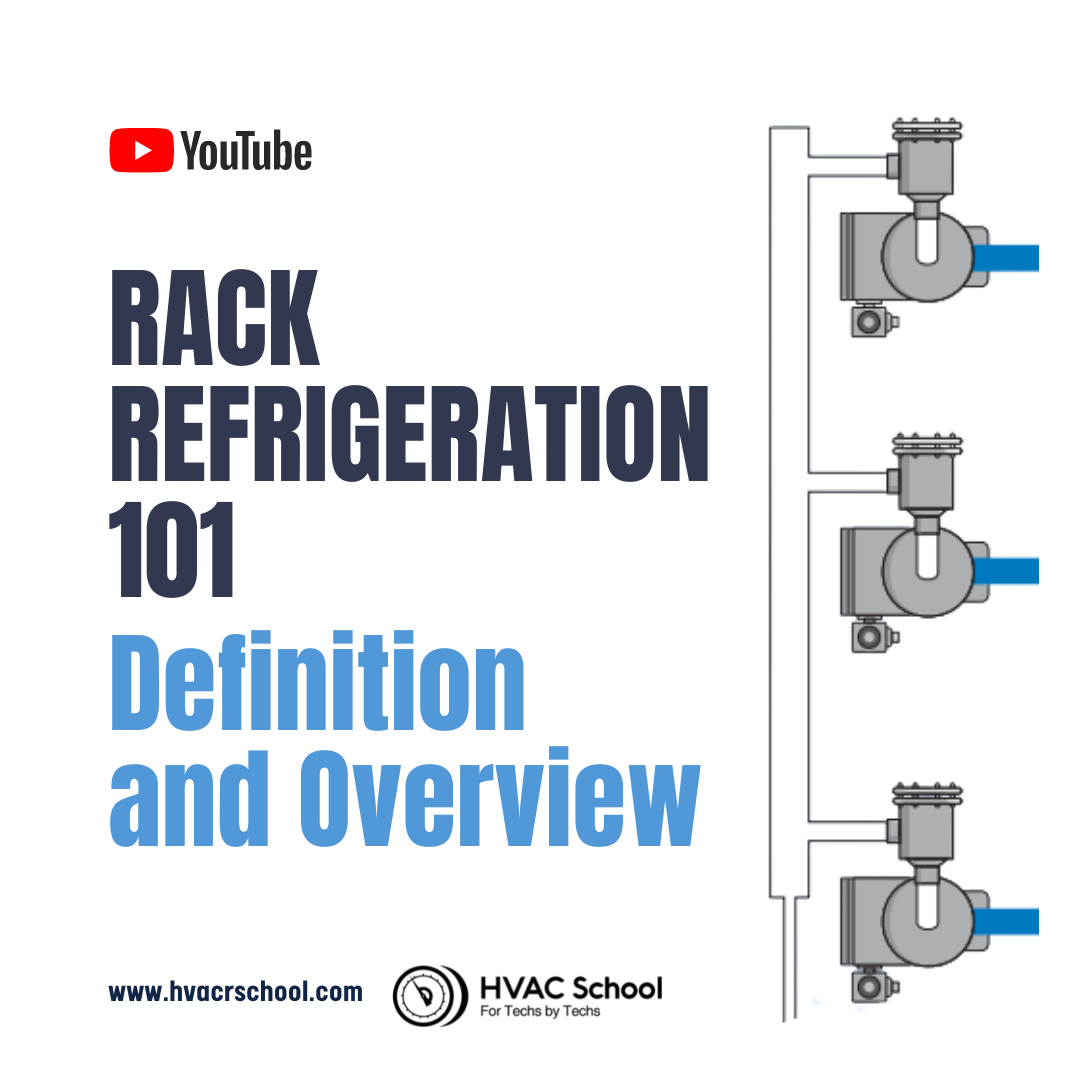
Parallel rack refrigeration systems have multiple compressors that are all tied together in parallel. So, the discharge and suction are all tied in together. Each compressor’s discharge line will drop down into one main discharge line. That main discharge line has an oil separator, which returns the oil to the reservoir and allows the refrigerant to proceed to the condenser outside the rack room.
The refrigerant liquefies in the condenser and comes out via the liquid line. Refrigerant in the liquid line goes to the receiver, which is located underneath the compressors in this system but can be remote as well. The refrigerant then goes through the liquid line drier and to the remote liquid header. The liquid goes down to all of the cases and loads beneath the rack room, which are often walk-in refrigerators (where the heat absorption happens).
Behind the liquid header, we have suction lines with EPR valves. These EPR valves are electronic, which regulate the suction gas to achieve 100% runtime between defrosts. The suction lines all tie together into a common suction header, which then ties into the suction side on each compressor.
The oil separator and reservoir are critical components of rack refrigeration systems. The oil reservoir must be able to supply oil across three (or more) compressors.
Overall, the goals of a rack refrigeration system are to keep compressors running as long as possible, share the refrigerant charge, share the load, and try to achieve 100% runtime between defrosts.
Comments
To leave a comment, you need to log in.
Log In