Pressure Testing Large Jobs
October 26, 2023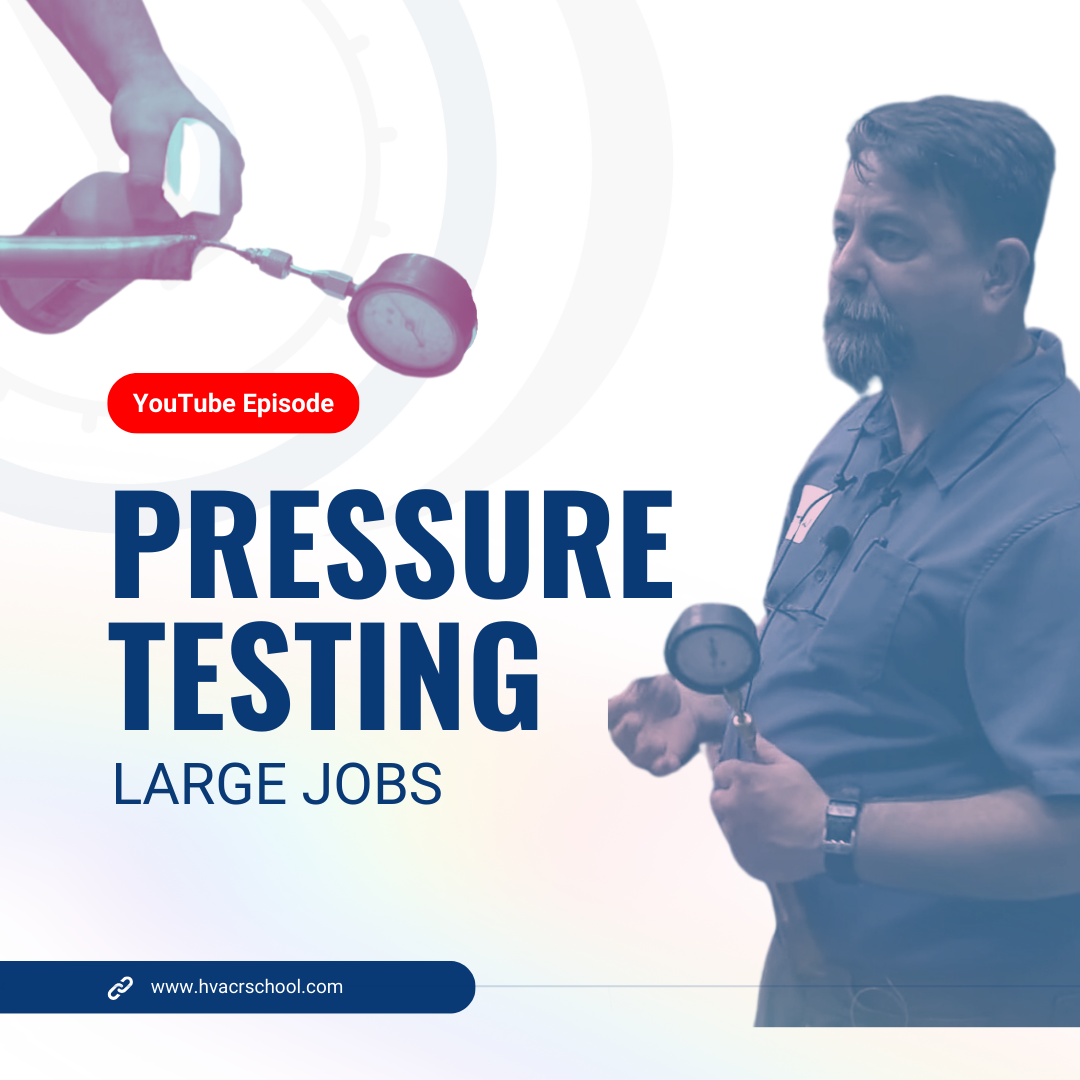
Nitrogen is ideal for pressure testing because it’s inexpensive, and its pressure doesn’t respond significantly to changes in temperature. You can easily fill the entire system with nitrogen and determine if you have leaks in places you can’t reach with a leak detector. You do NOT want to pressure-test a live system with refrigerant in it; you’ll have to isolate the part you want to pressure-test.
Before pressure testing, think through your application; you’ll want to know if you have a new store, a new line set, new cases, or an active rack. Each one will require a unique approach. When starting the test, you’ll want to make sure you have a gauge that you can leave attached to the system for a long time, sometimes upwards of 30 days for new systems; analog gauges are sometimes preferable for that reason, and they don’t need to be perfectly calibrated as long as you can see that the pressure is maintained. The original pressure should be documented so that you will know how much the system has leaked when you return to it.
When you pressurize the system, set the nitrogen regulator to the maximum test pressure as recommended by the manufacturer and apply a leak reactant (bubble solution) to the joints to check for bubbles and microfoam, both of which indicate leaks. When you’ve finished the test, you can release the nitrogen and either address the leaks and redo the pressure test or proceed with evacuation.
Comments
To leave a comment, you need to log in.
Log In