Flaring and Preventing Leaks on Ductless Systems
December 14, 2022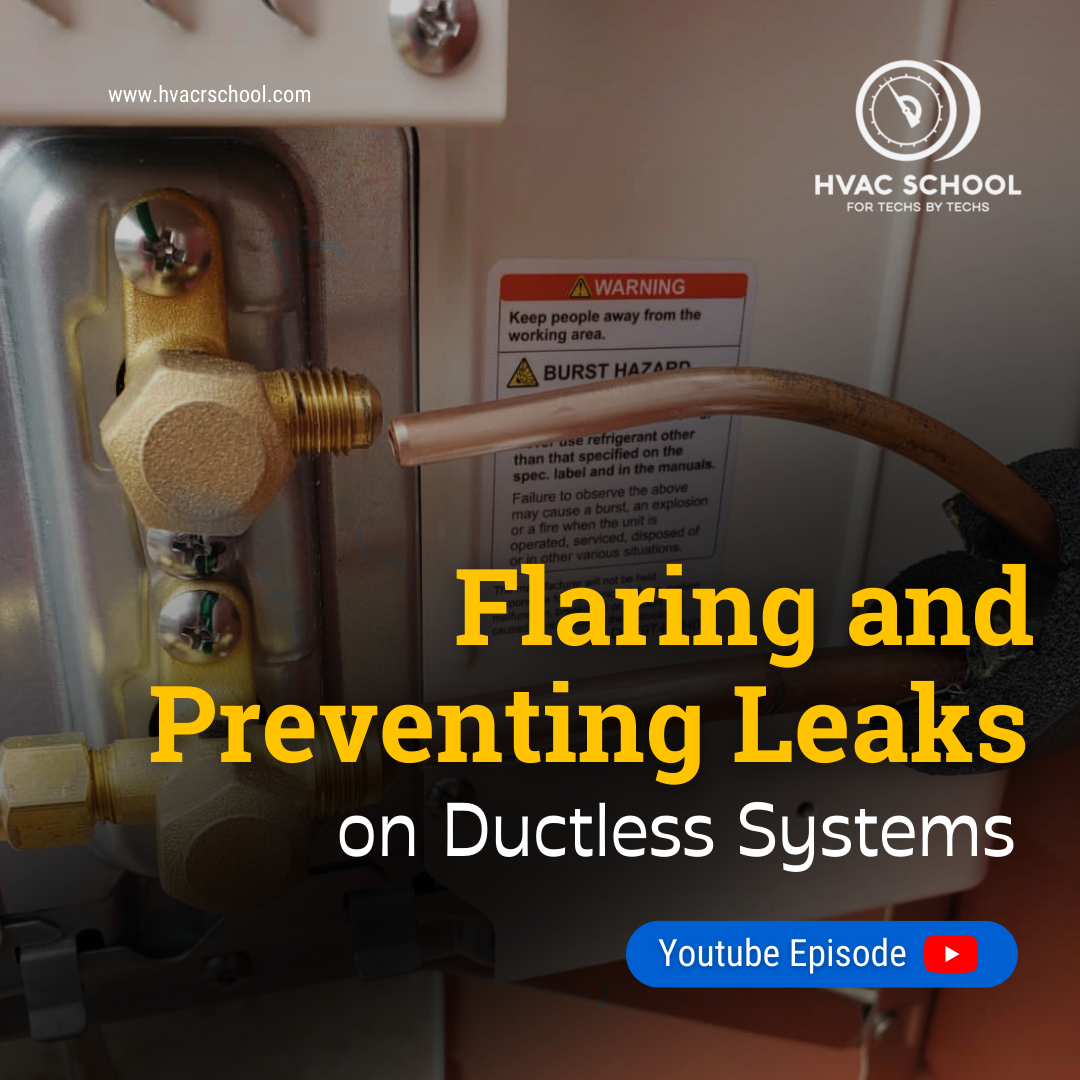
When tightening a flare nut, it’s a good idea to use a special flare wrench; flare wrenches are specifically designed to grab a flare nut and will let you tighten the flare nut without deforming it. You will, however, still need to apply the right amount of torque. Torque wrenches can be difficult to use in tight areas, so you can simply use them to check the torque and let a regular or flare-nut wrench take care of most of the tightening.
A wide variety of flaring tools can be used to flare copper tubing. Although you need to deburr the copper to prevent turbulence from happening inside the tubing, you don’t want to over-ream the copper and weaken it; over-reamed copper may crack when flared. Flares should also be made in the correct size; the goal of a flare is to have a clean, smooth finish on its face with as much contact area between the face and the cone as possible. Do a visual inspection to make sure a flare is round, properly sized, and smooth before you use it. Hold the flare against the cone to verify its shape and size.
The tension should go towards the connection, not away from it. So, pre-bending copper is an advantageous practice when you have to make a flare connection in a tight or tricky spot. We also put a tiny bit of Nylog on the mating surfaces, threads, and back of the flare. Although Nylog will affect the torque a little bit due to the reduced friction, it is a good practice to use an assembly lubricant as long as you know how to adjust the torque and don’t overdo it.
You should thread the nut with the copper in place, as you will establish the contact at the connection. Once you tighten the flare nut, you will want to do a pressure test to ensure that there are no leaks; these pressures should be quite high. Ductless systems with hard shutoff TXVs can be tricky, as the pressures may become unequal between the high and low sides; you don’t want a differential between the high side and the low side during the pressure test because the bleeding-through action could look a bit like a leak.
When you add a leak reactant to check for bubbles, you want to lay the reactant on flat, coat the flare connection, and let it sit for a substantial amount of time. The pressure test time may vary depending on the system type and size. Once you return, check for bubbles, including microfoam bubbles, using a mirror and a flashlight.
Comments
To leave a comment, you need to log in.
Log In