Ductless System Install and Maintenance
January 9, 2023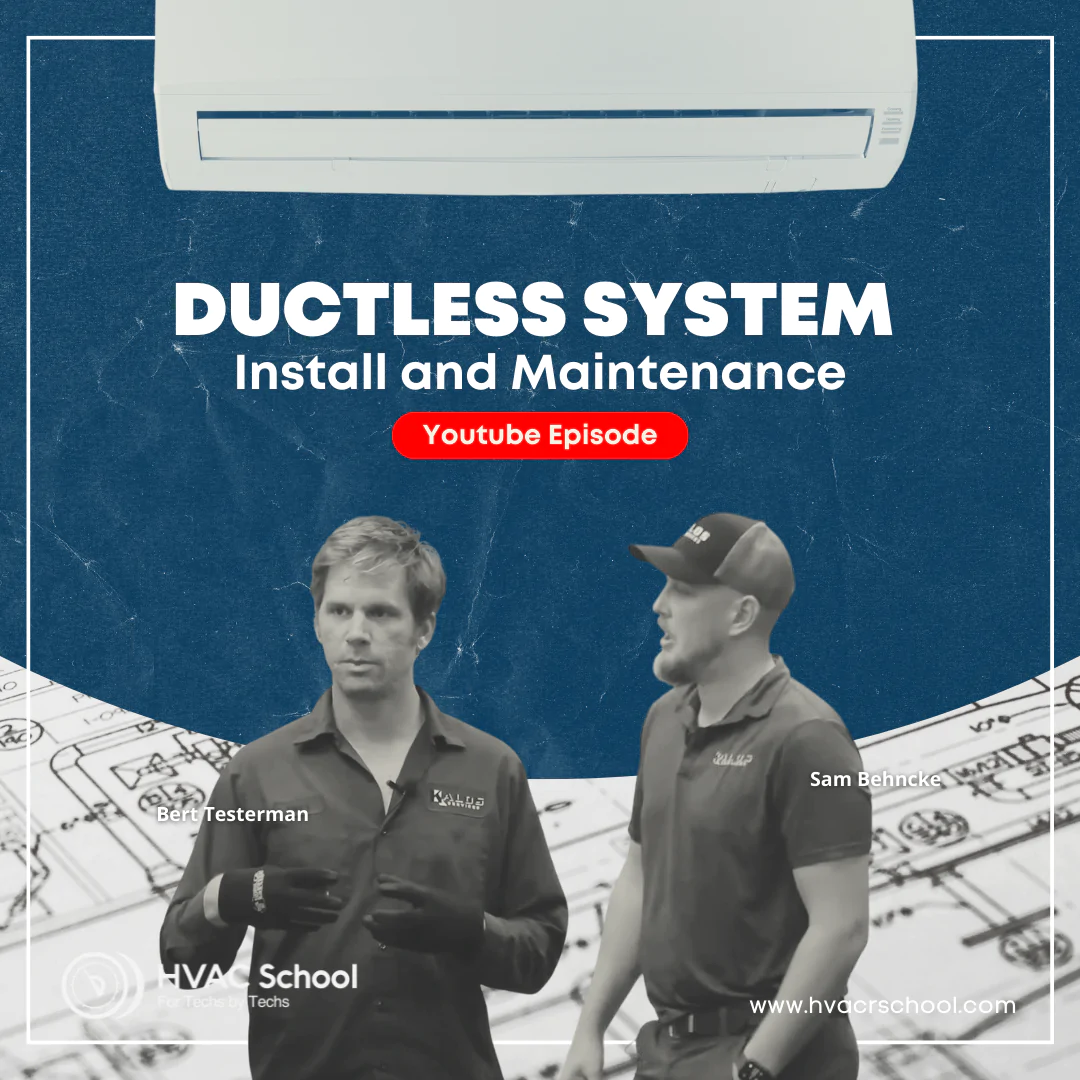
When installing a ductless system, you will need to think about the placement of the head, condenser, drain, line set, and high-voltage components. Before installation, it is best to review the scope of work, make sure you have all the necessary supplies in your van, read the manufacturer’s manual, determine the placement of the components, and communicate all necessary information to the customer. It is also important to have appropriate PPE for procedures like cleaning and drilling, and you’ll want to make sure you don’t strain yourself while you work.
Flare joints are prone to leaking if we don’t thoroughly test them, so we need to make sure we make flare connections that are tight and have strong copper. Make sure the copper has been deburred after being cut to avoid causing turbulence in the lines or creating ridges and cracks. You also want to use a high-quality flaring tool, whether you use a flaring block or power flaring tool; that way, the flare should have the proper diameter and depth. When torquing the flare nut, use a torque wrench set to the proper specs for the best results.
All line sets should also be insulated, though some technicians have reported that some sheaths may contribute to premature leaking. Cork tape and thumb gum are also inadequate for insulating ductless line sets. Pressure testing is also critical for identifying leaks early on. You will want to coat the joints in a bubble solution, wait for a little while, and make sure you inspect each joint with a flashlight and a mirror to check for microbubbles. Vacuum practices are very similar to the best practices for traditional split A/C units and heat pumps. The decay test can also help you realize that a system has a leak.
Ductless mini-splits usually have a relatively small charge compared to other types of systems. Be sure to follow the manufacturer’s instructions and account for line length when setting the charge. You’ll also want to make sure your condensate disposal methods are appropriate and working properly at the end of the installation. Generally, you will use either a gravity drain or a condensate pump. In many cases, gravity drains are ideal because they are quiet, have little maintenance compared to pumps, and have a lower chance of causing damage indoors. Condensate pumps may be the only feasible option when the unit is on an interior wall.
When you close out an installation, be sure to explain the most important aspects of equipment and remote operation, maintenance expectations, and condensate pump noise levels to the customer.
Regularly maintained ductless systems often don’t take long to maintain, but they need attention to that they don’t smelly and dirty quite quickly. PMs require you to talk to the customer and work inside their home, so customer service is critical. Ask the customer about their system, go over the scope of work with them, and show care for their home by wearing shoe covers and placing down drop clothes.
The maintenance process can be broken down into roughly five stages: pre-inspection, communicating issues, cleaning, confirming operation non-invasively, and having a closing conversation with the customer about what you did.
Before testing the system, let it run for at least 10 minutes. Then, do non-invasive testing, including checking the delta T. Watch out for things like low suction, ice on the expansion line, low split, or sloshing noises.
When it comes to cleaning, you will want to pull the filters and clean them with water. Try to wash condensers with water only unless they get impacted by soil, animal hair, or other debris. You’ll probably have to expose the evaporator coil, drain pan, and blower wheel. You will likely need to remove the blower wheel for cleaning. When the evaporator coil is only a little bit dirty, you might use a rag or soft bristle brush, but you may need to clean the evaporator coil in place if there is significant soil. You can clean an evaporator coil in place using a bib kit.
To clean a gravity drain, flush and vacuum it and clean out the pan. You may need to remove the pan to access it. To clean a condensate pump, clean the reservoir, tubes, and screen, ensuring that the float is positioned correctly. Avoid using cleaners on pumps.
To finish up a maintenance job, make sure you leave the customer’s home exactly how you found it. Check the make sure the system runs as it should. Communicate everything with the customer and allow them to raise questions or concerns.
Comments
To leave a comment, you need to log in.
Log In