Callback Prevention Part 2 – Technical Practices
September 20, 2022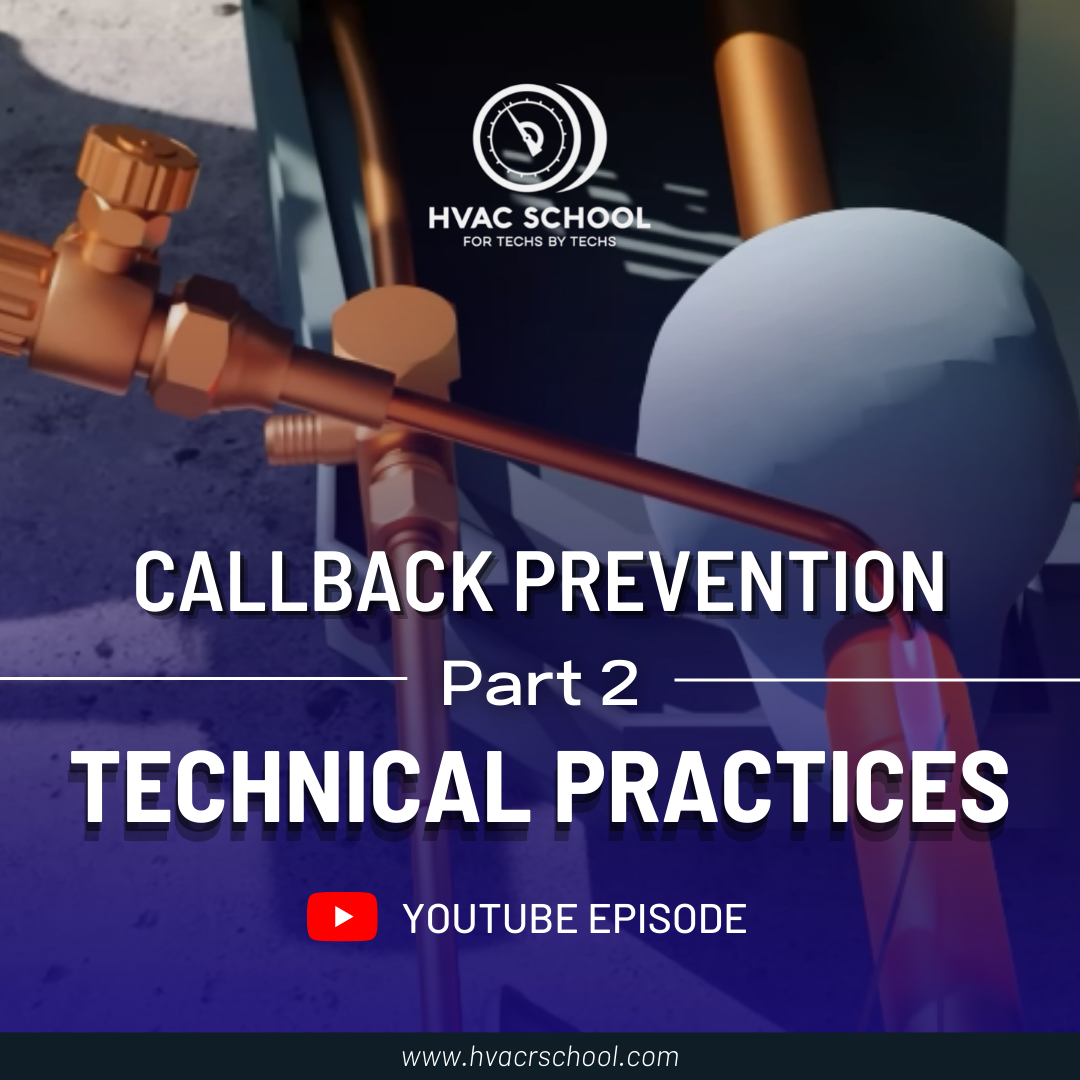
When it comes to brazing, you have to use enough heat to draw the alloy into the joint, but you don’t want to use too much, either. If you braze too long or use too much heat, you could end up burning surfaces or components. You can avoid burning components in the work area by using a heat shield.
An air-acetylene torch has a larger heat area, but it has a more convective flame than an oxy-acetylene flame; the actual flame isn’t as hot, but the area around the flame tends to be hotter. In any case, you will want to heat the joint to a dark cherry red color, not bright red, and apply the brain rod. To protect heat-sensitive components, use a wet towel or a heat-blocking putty, like Refrigeration Technologies WetRag.
Thorough leak detections also prevent callbacks. Start with a visual inspection, using a mirror to check all the joints. Then, pressurize the lines with nitrogen and apply a leak reactant (bubbles) to the joints and look for microbubbles. Follow up with a nitrogen pressure test lasting at least 20 minutes (though longer is better). Make sure to remember your starting pressure to get an accurate idea of the PSI drop.
Once you’ve done your pressure test, pull a deep vacuum. If you can, pull below 300 microns; use large hoses and pull your cores to get a deeper vacuum. Then, valve off at the core tool and do the decay test. The system should not decay to 500+ microns in 10 minutes, though there may be some variation depending on system conditions. A failed decay test may indicate a leak. You will also get different decay rates when you use a one-hose evacuation instead of a two-hose evacuation because the methods cause different rates of equalization.
Sound, sensible system infrastructure will also help prevent callbacks. You need the drain line and system to be placed far enough away from each other (about 2 feet), and the system should be away from walls or shrubbery. If you have to use long line sets, you need to make sure you charge the system appropriately; you can use the long line calculator on the HVAC School app.
To ensure that you have the proper refrigerant charge, try to use non-invasive testing to minimize losses through hoses. Make sure the superheat and subcooling are within appropriate ranges for the system. If you have to add or recover refrigerant, make sure you use a scale to know how much refrigerant you’re adding or removing from the system. If a system is low on charge, fit a leak detection into your quote to prevent future heartbreak.
Drains are also common reasons for callbacks. We need to make sure that the drains are clean and properly pitched (at least ⅛” of fall for every foot of horizontal run). Bacterial zoogloea cases need to be resolved, as those can cause recurring problems in systems with all-aluminum coils. Drains also shouldn’t have double traps, and cleanouts and vents should be accessible. When cleaning a drain, be mindful of toxic chemicals, and handle those carefully. If you use a cleaner, flush the drain with a lot of water.
Although some callbacks happen due to exotic system problems, many callbacks can be prevented by being thorough when brazing, doing pressure tests, pulling a vacuum, and cleaning drains.
Comments
To leave a comment, you need to log in.
Log In