A Rack Refrigeration Oil Issue Resolved
January 31, 2022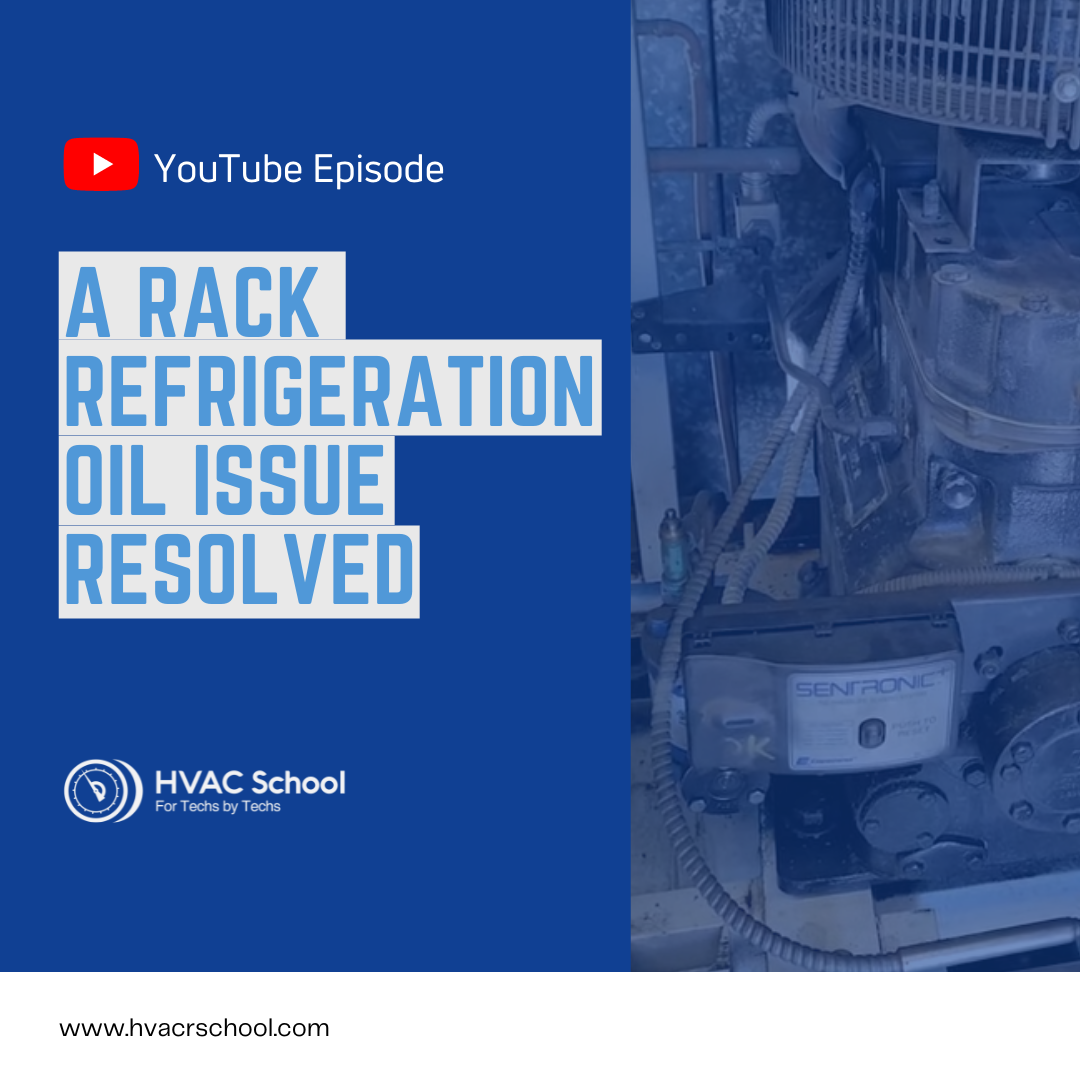
Before Corey begins cleaning, he needs to get as much oil out of the compressor and into the reservoir as possible. He does that by valving off the oil regulator and attaching a hose from the pump to the reservoir with the compressor ON. That way, the compressor uses its own power to pump the oil out and into the reservoir until it goes out on safety. When that happens, the M and L contacts on the Sentronic safety will have voltage; we can measure that voltage with a meter to confirm that the compressor has been locked out.
Before Corey pumps down the system, he valves off the line feeding the demand cooling module and the King valves. Once everything is valved off, Corey and Chad move any additional gas in the compressor to the next compressor on the rack. They drain any excess oil at the bottom of the compressor. Then, they pull out the oil pickup screen and tube using a pick and clean those. Corey also pulls out the Sentronic sensor and demand cooling sensor, and he cleans those and sands the demand cooling sensor down. He then reinstalls the clean demand cooling sensor using Nylog as an assembly lubricant.
After cleaning the oil components, Corey takes a vacuum pump and evacuates any additional contaminants from the compressor.
Then, Corey balances the oil regulator using an OCV-5 check valve. He determines the pressure differential between the oil reservoir and crankcase suction pressure. After taking measurements and coming up with a differential of 5 PSI, Corey checks the manufacturer’s graph to see how many times he needs to turn the check valve. According to the graph, he needs to make 10 counterclockwise turns to maintain a half-full sight glass. It takes some time for the oil to fill to the proper level, so we recommend waiting a day for the oil level to adjust after you balance the regulators.
Comments
To leave a comment, you need to log in.
Log In