Get Tech Tips
Subscribe to free tech tips.
Troubleshooting 90%+ Gas Furnaces
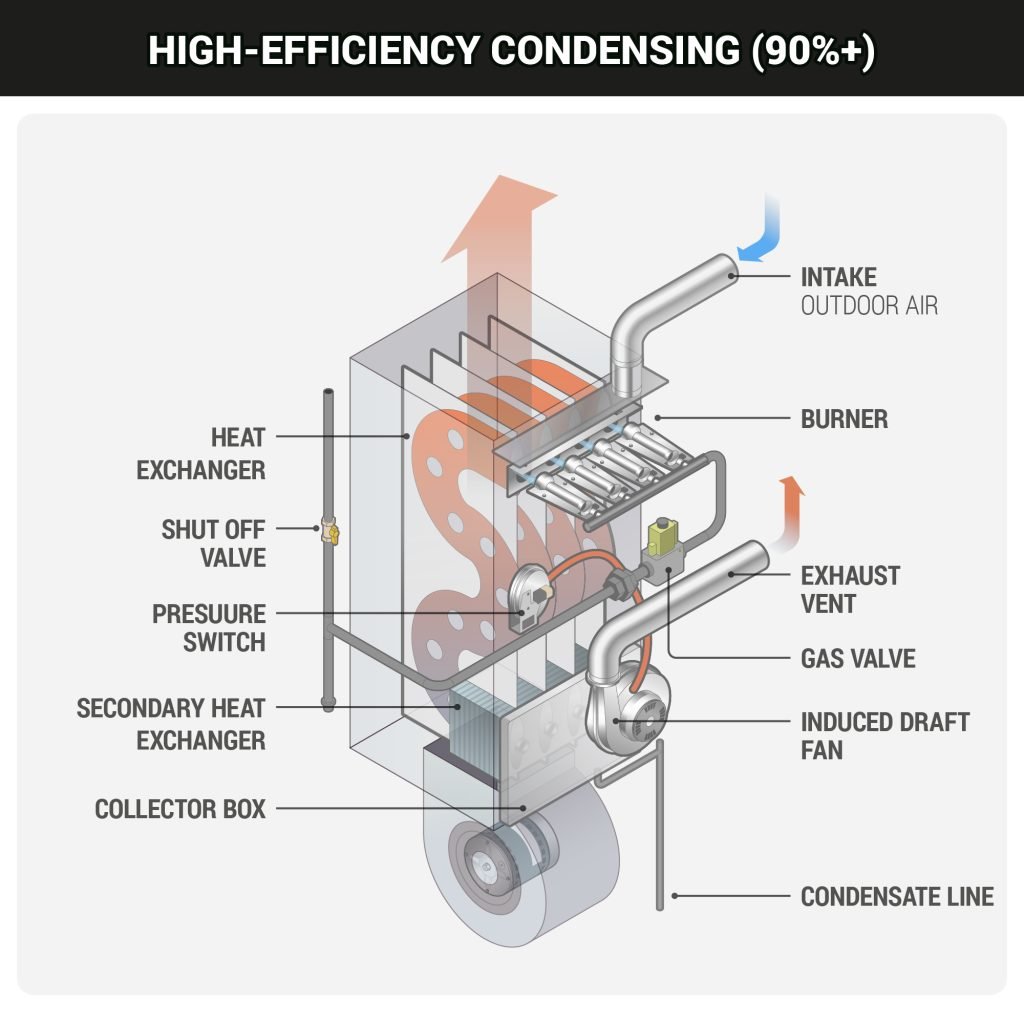
This tech tip recaps the livestream by the same name, featuring HVAC School contributors Matt Bruner and Adam Mufich and special guest Ty Branaman. You can watch that livestream on our YouTube channel HERE and visit Ty’s at https://www.youtube.com/@love2hvac.
While 80% gas furnaces are relatively commonplace in the Southeastern United States, where HVAC School is based, 90%+ high-efficiency condensing furnaces are popular in more northern markets. 90%+ efficient furnaces have the fastest return on investment in the northern climate with longer heating seasons. They are also commonly used in well-sealed high-performance homes, such as homes with spray-foamed attics. These high-efficiency furnaces differ from 80% induced-draft furnaces in that they have a dedicated air intake, a primary and secondary heat exchanger, and a condensate assembly.
We get more energy efficiency out of these furnaces because there is more heat transfer over a greater surface area, which we owe to the secondary heat exchanger. With that added efficiency, we get cooler flue gases and condensation; since water vapor is a byproduct of combustion, cooling it will cause it to condense into water. Water vapor changing state to a liquid releases many BTUs of latent heat energy. Condensation on an 80% furnace will eventually lead to corrosion because acidic flue gases are involved, but 90%+ furnaces manage condensate removal by design.
As a result, 90%+ furnaces have unique troubleshooting challenges compared to less efficient appliances.
Common Problems with Water Management
When it comes to piping condensate assemblies, we must be mindful of where we direct the water.
That water mixes with flue gases and will be acidic, so we must keep the water away from corrosive materials, including metal plumbing pipes, or use an acid neutralizing device. 90%+ furnaces typically use specialized PVC for condensate drainage for that reason. Inside the unit, our secondary heat exchangers are usually made of stainless steel to reduce corrosion, but they’re not immune to it. Pitching the furnace slightly forward can help keep acidic water from accumulating inside the furnace’s secondary heat exchanger.

Drainage assembles that go straight to the outdoors may also pose problems in low ambient temperatures. The water can freeze into solid ice at the outlet, which will cause the drain to back up.
Water management is one of the trickier parts of dealing with 90%+ furnaces, as the furnaces that preceded it never had to deal with it to the same degree. When in doubt, you can look up the manufacturer’s literature for help. Those manuals may have insulation guidelines and considerations based on your climate. For example, if the furnace is installed in an unconditioned space, such as an attic, the condensate drain may require heat tape to be applied.
Combustion Air Intake
80% induced-draft furnaces pull air in from around the unit (and are sometimes called “open combustion” furnaces). High-efficiency condensing furnaces have dedicated piping assemblies that bring combustion air in from the outdoors.
This design allows you to have more control over the combustion air. It especially reduces the risk of contaminated combustion air due to VOCs, such as in nearby cleaning products or off-gassing paints. The combustion of a 90%+ furnace is “sealed” as a result.
This difference is also important for home performance since 90%+ furnaces aren't using combustion air from the home that will need to be replaced by outside air or backdrafting through other appliances or exhaust. Sealed combustion is especially important in applications with encapsulated attics that have nowhere to draw combustion air from. That's why 90%+ gas furnaces are often seen in performance homes, even in the South.
Sequence of Operations
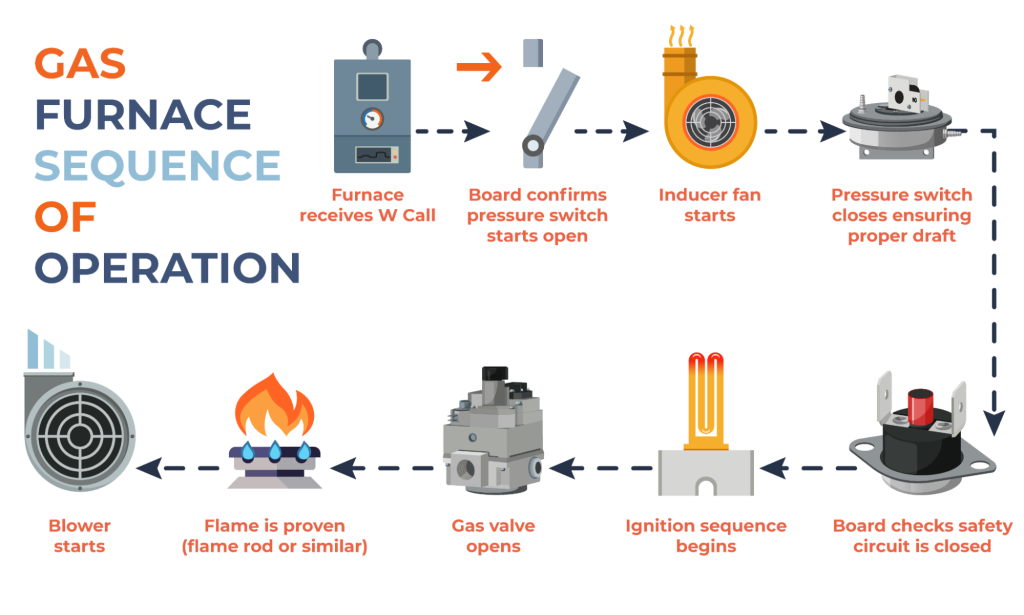
We can get a clue where to begin diagnosing a 90%+ high-efficiency furnace by going through the sequence of operations.
The overall sequence of operations is practically identical to that of an 80% furnace. You’ll start in the same place: with a W call from the thermostat. The control board then has to verify that the pressure switch is open. From there, the inducer fan motor starts, closing the pressure switch.
Pressure Switches
It’s worth noting that 90%+ furnaces come in single-stage, two-stage, and modulating models, each with different ratings and types of pressure switches. Different manufacturers may also have different equipment designs.
You’ll probably notice that many single-speed furnace pressure switches aren’t that much different from those on 80% furnaces. Two-stage furnaces often have a pressure switch for each stage, and modulating furnaces might use a pressure transducer.

The secondary heat exchanger may have multiple pressure switches, which can be overwhelming for techs who aren’t used to seeing that. Those pressure switches are designed to respond to pressure drops between the primary and secondary heat exchangers.
The manufacturer’s literature, including schematics, may include detailed instructions on testing those. The instructions usually include the pressures needed for the switches to open and close. If you’re not achieving those pressures, it’s time to ask why and investigate. The problem could be as simple as a cracked or dirty hose, or the problem could lie within intake and or exhaust piping.
If you are indeed achieving the pressures needed to open or close the switch, then you can narrow the problem down to the pressure switch. Some tools also test pressure switches, like this Fieldpiece manometer.
It’s also worth noting that improperly sized flue piping might not allow the inducer fan to create enough pressure to close the switch. Make sure you size the exhaust to the manufacturer’s vent tables.

Source: Goodman
Ignition Sequence
Once the pressure switch closes, the board checks all safety circuits to make sure they’re closed before beginning the ignition sequence. (Remember: the rollout switch is a manual reset switch.)
Combustion requires there to be a proper draft (confirmed by the pressure switch), heat (from the igniter), and fuel (from the gas valve). The igniter and gas valve will start the flame, which will be proven via a flame rod. Once the flame is proven, the blower can start moving heat throughout the home via the ductwork.
Thinking Through the Troubleshooting Process
Ty’s troubleshooting process starts by looking for the obvious: loose wires, water buildup, debris in the burner compartment, obstructed exhaust and intake venting, and a lack of natural gas (such as if the customer didn’t pay the gas bill). Your senses of sight and smell come in handy here, especially if you notice a rotten egg smell or water leak.
Water can be pretty destructive, and it’s a big indicator that something is amiss. Again, we don’t want to see water leaking from the heat exchanger, but water leaks can also cause equipment to fail, especially if it leaks onto the circuit board.
Secondary Heat Exchanger
The secondary exchanger consists of a tube and fins, like the evaporator of an A/C system or heat pump. Similar to an evaporator, those fins can collect debris, and heat transfer becomes more difficult, which doesn’t allow for good airflow over the heat exchanger.
Internally, a clogged secondary heat exchanger doesn’t allow the flame to be drawn through its passageways, and that can lead to flame rollout. Externally, secondary heat exchangers can get dirty without regular filter changes and blower cleanings, so regular maintenance is a must.
Preventing Animal Nests from Getting Into the Flue
It’s an age-old problem: bird’s nests, squirrels, or even raccoons in the flue.
A common “solution” is to put a screen over the outdoor exhaust piping, but water vapor can condense and freeze over that screen in cold weather. However, flush mount kits and concentric piping that draw air from the back side of the vent kit may help.
A flush mount wall termination kit is an oblong-shaped fitting where both of the pipes are terminated through the wall next to each other. There is a hole in the face of the fitting that allows the exhaust to blow away from the home. The rest of the fitting has rounded edges and draws the air in from the backside of the fitting around its perimeter. A concentric exhaust kit is essentially a pipe inside of a pipe, so only one hole is needed in the home. The functionality is very similar to a flush mount kit but takes up less wall space. Concentrics can be used in both horizontal and vertical applications, while flush mount kits are designed for horizontal only use.
Speaking of exhaust venting, it’s important to note its location. While a roof mount location might be more susceptible to freezing, a wall mount may be in an area that gets covered in snow. A flue opening next to the condensing unit can cause corrosion of the condensing coil. The vent termination should be installed away from places where people might congregate, such as a back porch or walkway, when possible. If the flue pipe is in an unconditioned space, such as a vented crawl space or an unconditioned attic, it may need to be insulated or even need heat tape applied. Again, check with the manufacturer’s installation guide for the specific requirements.
Gas Pressure
When the gas valve opens, the inlet pressure shouldn’t drop below the manufacturer's rated inlet pressure, but it can definitely drop. Ultimately, that pressure drop shouldn’t be a problem unless it causes the outlet pressure to drop.
If there is a significant drop, we can rule out a possible problem with the gas valve by running multiple gas appliances. If the pressure drops below the rated output pressure, then we can be confident that the issue is in the piping or the gas regulator, not the appliance.
CO Sources
AHRI Guideline X (available for free download on the AHRI website) tells us where to take CO readings (and unacceptable CO thresholds) before it’s necessary to look for cracks in the heat exchanger.
Even before we start looking at the appliance, before we go through the five steps laid out in Guideline X, we can start looking for CO in the home. If we see CO on our personal monitors, we’ll want to rule out sources like a backdrafting water heater, car exhaust in a nearby garage, or even the occupants’ lifestyle choices (like smoking).
And, for the 5,000th time, please invest in a personal low-level CO monitor to protect yourself. (Let your customers know about the benefits of low-level CO detection, too.)
Flame Rectification
Flame rods are small parts that play a vital role in furnaces. For them to work as intended, they need to be kept clean, and the system needs to be properly grounded.
Flame Rods: Clean or Replace?
It’s best to measure the DC microamp signal before deciding to clean or replace the flame rod. If the signal is weak (usually less than 1.5 microamps), then we can take a closer look at the flame rod.
Most dirty flame rods that don’t show signs of damage (cracks or even melting) can be cleaned and put back into service. It’s best to use steel wool to clean these, not sandpaper or a grinder. If you still don’t read an acceptable signal after cleaning the flame rod, then replacing it would be the next logical step.

Flame rods tend to foul more quickly on LP units than natural gas ones, and they’re also more likely to get dirty if a furnace’s air intake is in an area with lots of VOCs, such as those given off by household cleaners.
Keep in mind that you’ll want to check the burners, too. Dirty or rusted burners can affect flame rectification, and they can even lead to higher CO levels.
Grounding
Correctly grounding a 90%+ furnace is necessary for flame rectification. During flame rectification, an electrical current flows through the flame and to the rod to close the switch. (The electrical potential in the flame-sensing terminal and the ions in the flame allow an electrical path to form between the rod, through the flame, and to ground.)
Reversed polarity or improper grounding won’t allow a completed DC microamp flame signal to travel to the board and prove the flame.
The system needs to be grounded from the burner to the cabinet, the board, and the furnace plug. Corrosion and cracks on the grounded components will indicate that there is a problem.
Tools and Parts for 90%+
The most important tool you could keep on hand when troubleshooting a 90%+ furnace isn’t an HVAC tool at all. It’s your phone. Your smartphone allows you to look up service manuals, many of which have diagnostic flow charts. And if the service manual doesn’t help, you can always call tech support.
Apart from having a means of looking up information, your most important tool for troubleshooting 90%+ gas furnaces will be a manometer to measure pressure and test pressure switches. Another important tool would be a good digital thermometer to measure temperature rise across the furnace. It’s also a good idea to have a way to measure airflow, such as with a TrueFlow grid. You can also calculate airflow with temperature rise and blower charts.
An underrated tool is the humble level. If you have a level on hand, you can rule out problems with the drain pitch and ensure that the unit and drainage assembly were installed according to the manufacturer’s specs (and local codes).
While 90%+ high-efficiency furnaces are quite different from 80% furnaces and can be intimidating at first glance, you’ll get the hang of them as you spend more time looking at them and reading manuals. You’ll eventually grasp the unique needs of these systems and the most common things that could go wrong, several of which we’ve covered here and in the livestream, which you can watch in its entirety HERE.
Comments
To leave a comment, you need to log in.
Log In