Get Tech Tips
Subscribe to free tech tips.
Tool Selection: Analog vs. Digital vs. Probes
The original tools of the trade were all analog: electrical meters, gauges, and even manometers (Magnehelic, anyone?). However, digital tools have also become a staple of the skilled trades—where would most of us be without digital multimeters? And then probes also joined the fray with the rapid improvements to smartphone technology over the last 15–20 years.
All three of these tool types still exist today, and a lot of people have their personal preferences. However, we’re going to cover the main differences between analog, digital, and wireless probe tools so that you can pick out what’s best for you, especially in the context of taking pressure readings with gauge manifolds or pressure probes.
Analog Tools
Those of you who have been in the industry for a long time probably cut your teeth on analog tools. You can read measurements on these tools on a dial with a needle and markings; the classic gauge manifold is an example, though you may also see analog electrical meters (like the megohmmeter below) and pressure gauges.
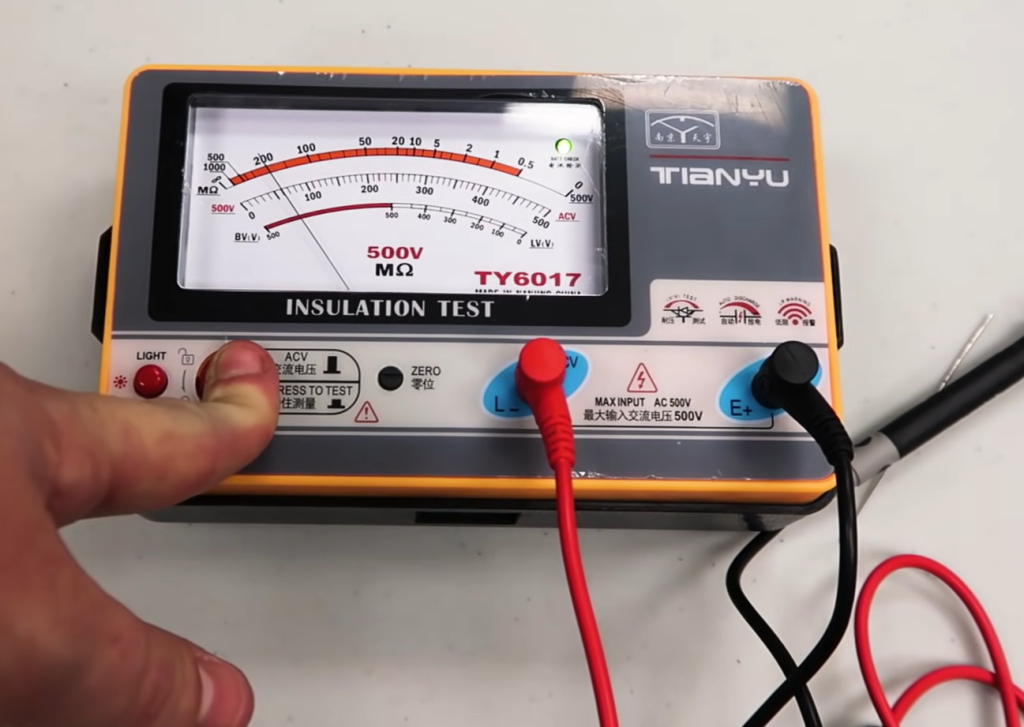
While it’s great to have experience with analog tools, they usually aren’t as accurate as digital tools and probes. The needle width can make it easy for techs to misinterpret their readings. Not to mention, they have a lower resolution than most digital tools; while digital gauge manifolds usually have a resolution of a tenth of a PSI, analog gauges usually won’t give you those decimals. However, they’re a good visual learning tool to help newcomers understand the P-T relationship.
Digital Tools
Digital tools have a numeric display instead of a dial. These often have a higher resolution. For example, a digital gauge manifold may read tenths of a PSI instead of only whole numbers.
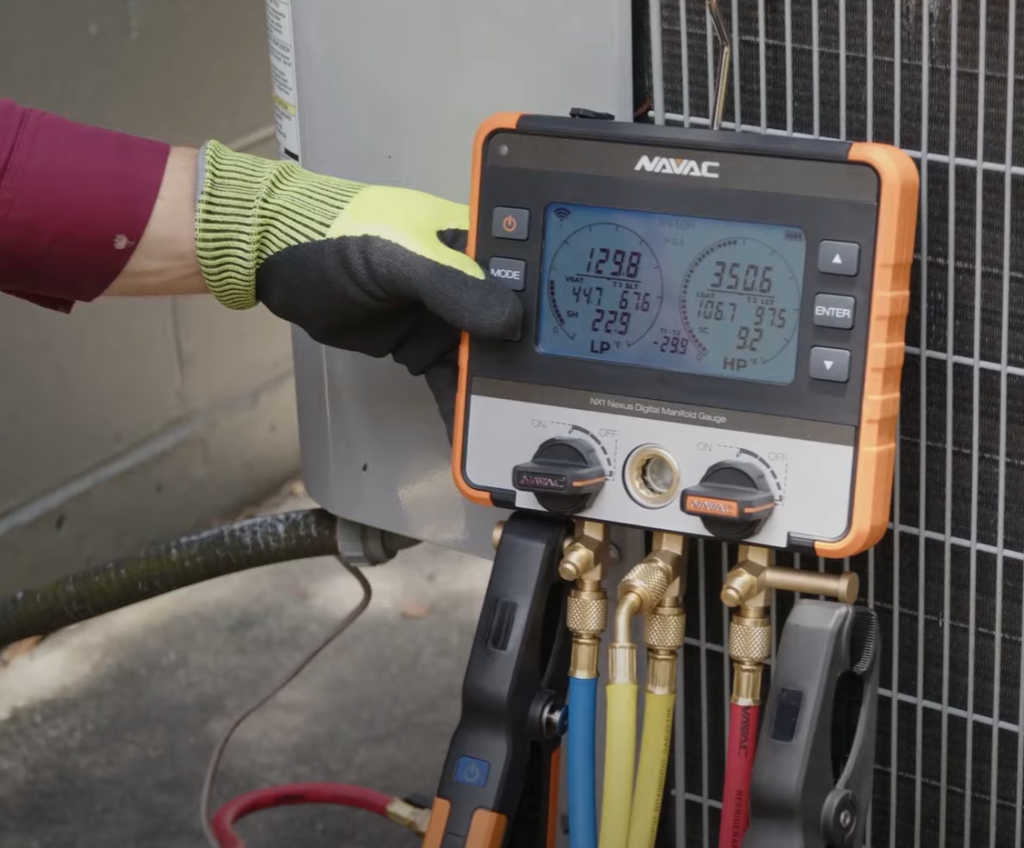
It’s also much easier to interpret the readings when the numbers are right in front of you; you’re not splitting hairs over which tick the needle is pointing at. The argument in favor of digital tools is that they’re less prone to human error because we can look at a digital gauge manifold and see 152.6 PSI right in front of us; if we had an analog gauge, we’d have to figure out where exactly the needle is pointing between 150 and 155.
Most of the tools we use nowadays will be digital, though one ubiquitous tool that we still see in analog and digital forms is the gauge manifold. However, there are some special points to consider apart from the analog vs. digital debate when selecting a gauge manifold.
Quick Note About Selecting Gauge Manifolds
Whether you’re in the analog or digital manifold camp, you’ll want to pay attention to the rated refrigerants and pressures when you consider buying a new set of gauges.
You’ll want to make sure the manifold is compatible with the refrigerants you’ll be working with—especially with A2L refrigerants popping up in new installations. The manufacturer and retailer should have that information on their website. I’ll show the N2D72 digital gauge’s specs as shown on NAVAC’s website (under “Technical Data”) and TruTech Tools (under “Specs”) side by side:
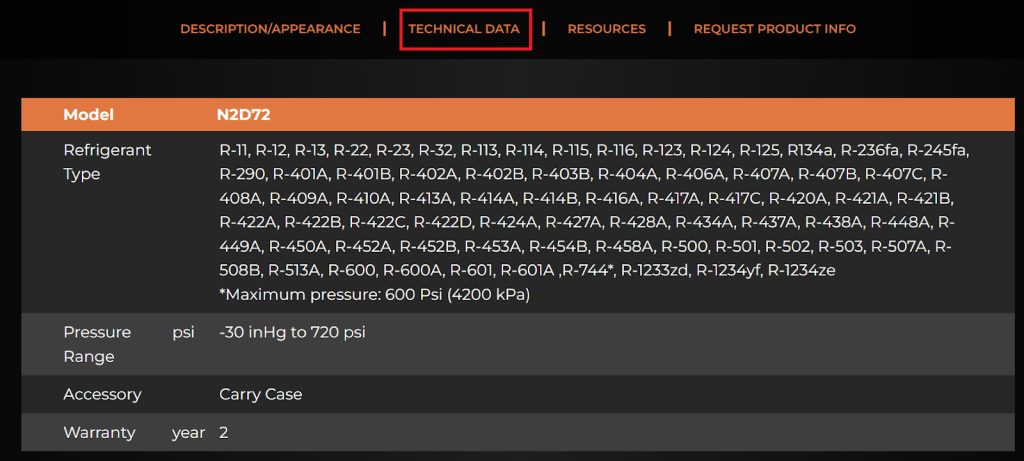

You can see the list of compatible refrigerants, which is quite comprehensive. Many analog gauges are a lot more limited in their capabilities because all of their compatible refrigerants’ scales have to fit on the same dial, but you may only work with R-22, R-410A, R-32, and R-454B, so one of those might serve you perfectly fine.
Manifolds also have a pressure range. These are critical because some refrigerants have higher operating pressures; gauges have to be able to register and withstand the operating pressures you’ll need to measure. Transcritical CO2 systems are a great example; transcritical high-side pressures may exceed 1300 PSI, and most gauges won’t be right for the job. You’ll want to look for gauges that can read those high pressures. (Yellow Jacket has a gauge manifold specifically for transcritical CO2 that can read up to 3000 PSI on the high side, and the included hoses are rated for 1740 PSI.)
Probes
Probes are the most advanced tool type of the three, and they’re quite possibly the best tools for accuracy and efficiency. If you have a set of probes, you can attach them to the system at several different points and receive all of the readings at once in apps like measureQuick. You can then save these reports, making it far easier to collect and store data about a system and take a holistic approach to commissioning and diagnostics.
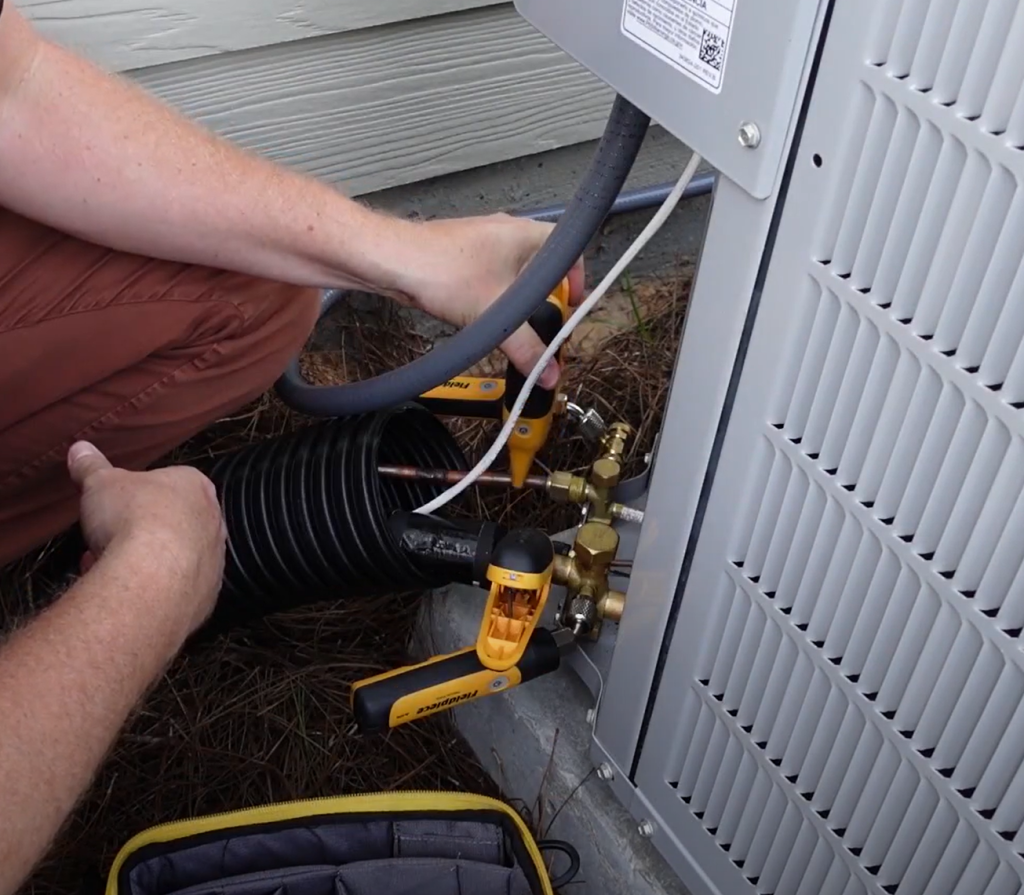
Instead of using a gauge manifold to check the charge, you can use pressure probes and line temperature clamps to take pressure and temperature readings. Using probes to check the charge will also minimize refrigerant losses, which is especially useful for systems with critical charge (like mini-splits) or microchannel coils.
Wireless Probe Considerations
Many wireless probes connect to phones and tablets using Bluetooth. You’ll want to ensure that you have solid communication between your tools and your device, and the specs can usually tell you the maximum distance between your device and tool before the connection drops off. (Those are also line-of-sight values, so walls and other obstacles will reduce that maximum distance.) For example, Fieldpiece JobLink tools have a 1000’ line of sight range.
Of course, you don’t want to push those limits. You’ve probably walked a fair distance away from your phone with earbuds in and heard the music (or HVAC School podcast) start to cut in and out past a certain point. Music is one thing, but your customers’ entire comfort system is quite another. When you’re using important information to make decisions, stay well within the limits and consider walls, elevation, etc.
Digital tools and probes have clear benefits over analog tools in the resolution and accuracy departments, but that doesn't mean they don't have their own limitations. Each tool type has its limitations, whether in practice or in theory; someone might not feel comfortable using probes if they've used analog gauges for decades, and a set of digital gauges probably won’t have the same educational value as a set of analog gauges in those early stages of learning about the pressure-temperature relationship, superheat, and subcooling.
Analog, digital, or probes—the choice all depends on personal preference and application. As HVAC professionals, we want to do our best with the information we have, and the quality of that information (and our comfort levels with the tools we use to get that information) makes a huge difference.
Comments
To leave a comment, you need to log in.
Log In