BACK
3 Bad Reasons To Work Overtime
Nomenclature and How to Use It
Wide, Narrow, Wide Diagnosis
The Residential Service Call Approach A-Z (Part 1 & 2)
#service tech
Tech Tips:
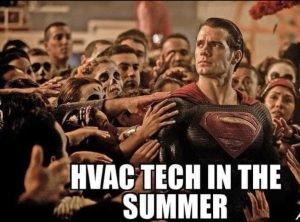
It’s easy to see yourself as a hero during the summer months. Desperate families in sweltering houses sing your praises after you quickly swap out that capacitor or install that new unit and the first blast of cold air comes out of the vents. Most companies make or break in the summer months, using the […]
Read more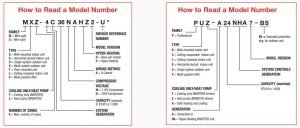
Nomenclature on HVAC/R equipment is a sequence of numbers and letters a manufacturer uses to speak directly to the technician. Lots of initial upfront information is handed to the technician by the manufacturer the moment the technician reads the nomenclature in the model and serial numbers. So, how do we make sense of these seemingly […]
Read more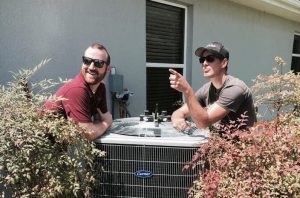
When you walk up to a piece of equipment, you want to follow a process to ensure that you accomplish five things: #1 – You diagnose the fault correctly. #2 – If possible, you find the “why” of the failure. #3 – Find any other problems or potential problems with the system that can cause […]
Read morePodcasts:

PART 1 PART 2 In this two-part series, Les Fork helps us break down some simple best practices from the time a residential service HVAC/R tech wakes up in the morning until the end of the day. Before the service call and good housekeeping Before a technician even leaves to go to work, they […]
Read more