BACK
Flame Sensing – The Basics
Some Furnace Questions
Preparing Non-Techs for a Southern Winter
#furnaces
Tech Tips:

Proving flame is an important part of the gas firing sequence. Without proof of flame, you risk dumping unspent gas into the heat exchanger, resulting in an explosion. There are many ways to “prove flame,” but we are focusing on the flame sensing rod (flame rectification) method here. Here are the facts: Flame sensing rods, […]
Read more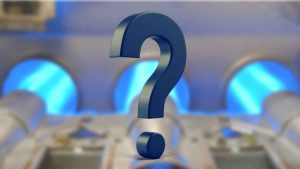
I received an email from a podcast listener with some furnace-related questions. Based on the nature of the questions, I figured it would be better to ask an experienced furnace tech. Benoît Mongeau agreed to help by answering the questions. My name is Matt and I am a newer tech (fully licensed this September, have […]
Read morePodcasts:
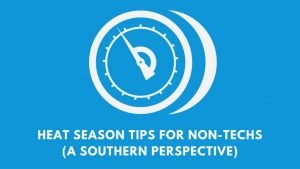
Central Florida techs know the Southern winter all too well. Let's face it. It doesn't get super cold here regularly, but when it does, EVERYONE FREAKS. We get an abundance of service calls for unpleasant but not truly problematic conditions when people use their heaters. When people first turn on their heat, they can get […]
Read more