BACK
HVAC/R Refrigerant Cycle Basics
Condenser Fan Blade Placement
Universal Condenser Fan Wiring Options
How to Replace a Condensing Fan Motor
Condensing Temperature, Condenser Split, and Subcool
The Basic Refrigeration Circuit
#condenser
Tech Tips:
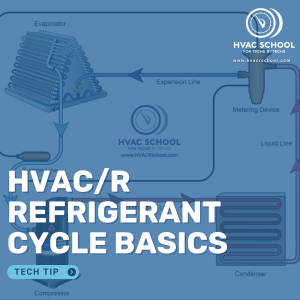
This is a basic overview of the refrigeration circuit and how it works. It isn't a COMPLETE description by any means, but it is designed to assist a new technician or HVAC/R apprentice in understanding the fundamentals. First, let's address some areas of possible confusion: 1. The word “condenser” can mean two different things. Many […]
Read more
In a previous article, I talked about wiring permanent split capacitor (PSC) condenser fan motors. While researching the topic, I realized that there isn’t as much information available on condenser motors as there is on their counterpart—the indoor blower motor. I had never really given it much thought, as I assumed that the condenser motor […]
Read more
Assessing the Situation It is fairly common for a service technician to come across a failed condenser fan motor in the field. It doesn’t matter if we are talking about really old or fairly new equipment—condenser fan motors sometimes fail. The issue is deciding whether to use an OEM (Original Equipment Manufacturer) or a universal […]
Read more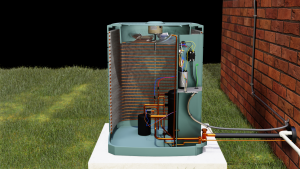
Service calls about condensing fan motor failure are quite common. Even though fan motor replacement is a standard procedure for residential split systems, it requires careful attention to safety and detail. This article will give you a step-by-step guide to replacing condensing fan motors. Along the way, we will also explain a few best practices […]
Read morePodcasts:
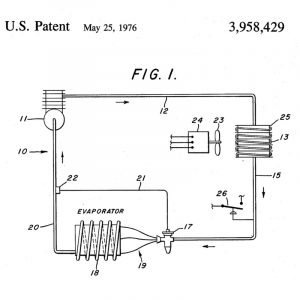
In this podcast, Bryan talks about condensing temperature, condenser split, and subcooling. All three of the values are proportional. If one changes, all three of them will change. Saturation is also a critical concept that relates to all three of those, so we also cover those relationships. As you remember, a condenser rejects heat and […]
Read more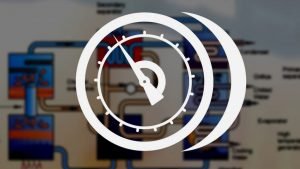
In this episode of HVAC School, we discuss the entire basic refrigerant/compression refrigeration circuit. We are in the business of moving heat. Heat refers to motion in the molecules. Temperature is the average velocity of those molecules. Heat needs a temperature differential to move. So, HVAC systems absorb heat when the refrigerant is colder than […]
Read more