BACK
Léon Creux’s Scroll Design: From Initial Failure to an Enduring Legacy
Three Levels of Acid Testing
3 Ways to Reduce Compression Ratio in a Heat Pump
High-Pressure vs. Low-Pressure Shell Scrolls: A Deeper Dive
HVAC/R Refrigerant Cycle Basics
Why Discharge Line Temperature is a Useful Reading
Why Compression Ratio Matters
Scroll Compressor Pump Down, Megohm Test & Fusite Terminals
Common Causes of Compressor Failure
Locked Compressor Mistakes w/ Bert
Compressor Ohm Mistakes w/ Bert
Preventing Slugging & Flooding w/ Copeland
Pumping vs. Compression – Short #218
Circuit Board Diagnosis Basics
Cutting Compressors, iManifold, and Thermal Imaging w/ Ulises Palacios
The Basic Refrigeration Circuit
Diagnosing & Replacing a Compressor
How To Properly Inspect a Failed Compressor
Compressor Teardown
#compressor
Tech Tips:
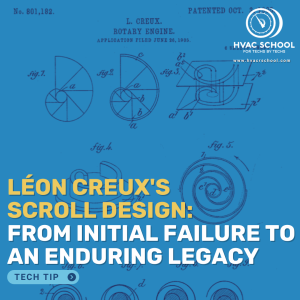
The HVAC/R industry isn’t short on tragic figures. There’s John Gorrie, whose ice machine showed a lot of promise but didn’t have enough financial backing due to the lucrative ice industry and the death of his business partner. While Gorrie may have died without seeing his vision reach the masses, he was ahead of his […]
Read more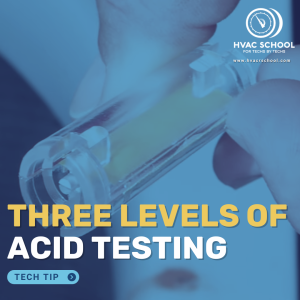
Anytime we have a compressor failure, we can’t just pull out the bad compressor and drop a new one in. We have to put our detective hats on and find the culprit so that it doesn’t happen again. In many cases, acid is a prime suspect. Whenever there’s acid in the system, the next compressor […]
Read more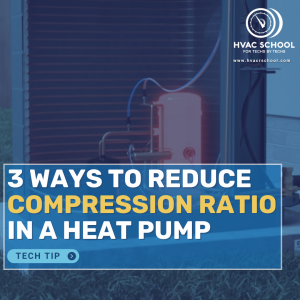
We’ve talked about compression ratio a lot over the years. Compression ratio is the number you get when you divide the absolute head pressure (PSIG + 14.7) by the absolute suction pressure (PSIG + 14.7). It measures the efficiency of a compressor, and lower numbers indicate that the compressor is moving more refrigerant while consuming […]
Read more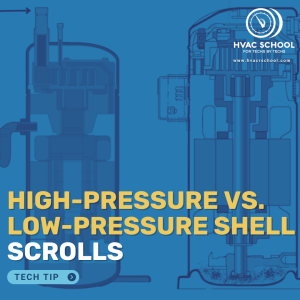
I want to share something that came up in a recent discussion with Roman Baugh about VRF systems, and it made me realize I might have had a blind spot regarding scroll compressor designs. We were talking specifics, and he brought up high-pressure shell compressors. My immediate thought was, “Hold on, aren't scrolls low-pressure shell […]
Read more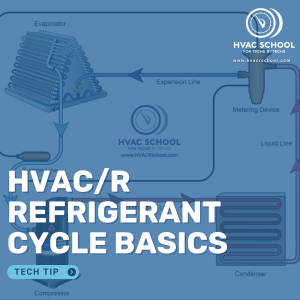
This is a basic overview of the refrigeration circuit and how it works. It isn't a COMPLETE description by any means, but it is designed to assist a new technician or HVAC/R apprentice in understanding the fundamentals. First, let's address some areas of possible confusion: 1. The word “condenser” can mean two different things. Many […]
Read more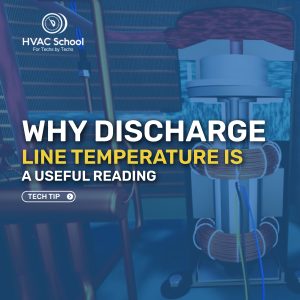
I’d like to give special thanks to Roman Baugh for the section about compressor superheat. It’s not something we talk about very often outside of chiller and commercial refrigeration applications, but it definitely has value in the HVAC world as well. Thanks, Roman! Since I started in the trade, we would take discharge line temperature […]
Read more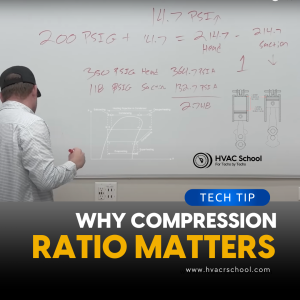
In HVAC/R, we are in the business of moving BTUs of heat, and we move BTUs via pounds of refrigerant. The more pounds we move, the more BTUs we move. In a single-stage HVAC/R compressor, the compression chamber maintains the same volume no matter the compression ratio. The thing that changes is the number of […]
Read more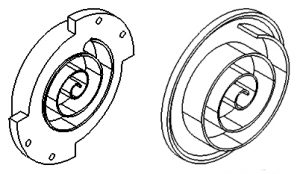
This tip will be like an episode of Columbo; we will start with the what and who and then get to the why. Don't pump down a scroll into a vacuum. Don't run a scroll in a vacuum. Don't run a high voltage megohmmeter or Hi-pot test on a scroll (As a general rule, don't […]
Read more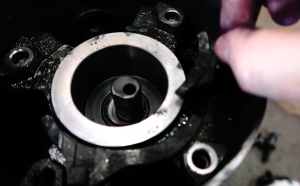
This article was written by Don Gillis, the technical training manager at Chemours. Thanks, Don! Refrigerant compressors are essential components of air conditioning and refrigeration systems, as we all know. They work by compressing refrigerant vapor, which then flows through the system and changes state as pressure and temperature conditions rise and fall. Unfortunately, these […]
Read moreVideos:
Podcasts:
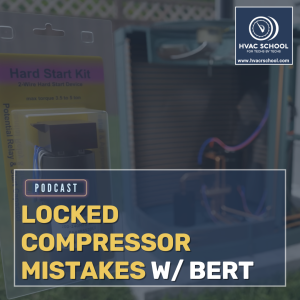
In this informative HVAC podcast episode, Bryan and Bert dive deep into the complex world of locked and internal overload compressors, focusing specifically on single-phase residential units. The discussion begins with Bert explaining one of the most common challenges technicians face: diagnosing a locked compressor. He describes how compressors that are locked will typically […]
Read more
In this episode, Bryan and Bert dive into the often misunderstood world of compressor testing, focusing on common mistakes technicians make when using ohmmeters, compressor testers, and megohm meters. The conversation highlights how diagnostic errors can lead to unnecessarily condemned compressors and wasted time and resources. The hosts begin by discussing fundamental concepts like […]
Read more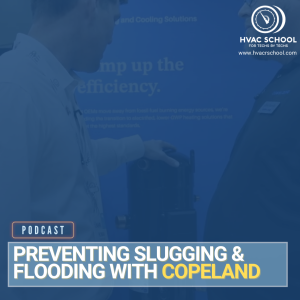
In this episode of the HVAC School Podcast, host Bryan welcomes Jeff from Copeland to discuss the critical topic of flooding and slugging in compressors. Jeff, calling in from frigid Minnesota (at negative 19°F), explains the differences between these harmful conditions and how they can damage compressor systems. The conversation begins by differentiating between […]
Read more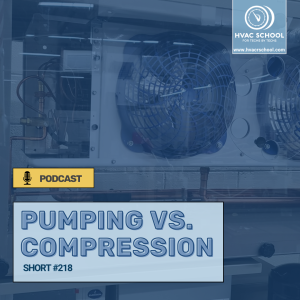
In this short episode, Bryan clears up the confusion behind pumping vs. compression. Pumping is usually associated with liquid. Liquid, like vapor, is a fluid, but it's a lot denser and is essentially incompressible because the molecules are close together. Liquid volume varies based on temperature and density, but we can't squish the molecules […]
Read more
In this unedited episode of HVAC School, Bryan and Nathan talk about some basic rules for circuit board diagnosis. So, circuit boards are boards with circuits in them. They come in two types. The traditional printed variety contains switches, relays, and resistors. The other type contains silicon chips and uses logic and processing inside the […]
Read more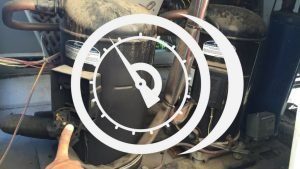
In this episode of HVAC School, Bryan talks with Ulises Palacios about some cool technology. Ulises has become a technology expert through his many years of working with new tools. He has recently been involved in testing new technologies, and he has worked with Jim Bergmann. Cutting open a compressor is one of the most […]
Read more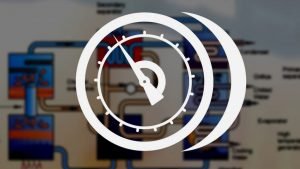
In this episode of HVAC School, we discuss the entire basic refrigerant/compression refrigeration circuit. We are in the business of moving heat. Heat refers to motion in the molecules. Temperature is the average velocity of those molecules. Heat needs a temperature differential to move. So, HVAC systems absorb heat when the refrigerant is colder than […]
Read more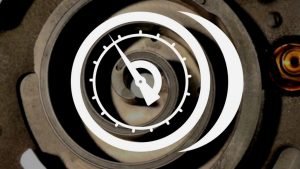
In this podcast episode, Bryan goes over best practices for diagnosing and replacing an A/C or refrigeration compressor. When testing for a shorted compressor, make sure the compressor is isolated from all of its circuitry. You would see low ohms to ground in a shorted compressor. Do NOT measure from winding to winding or terminal […]
Read moreEvents:
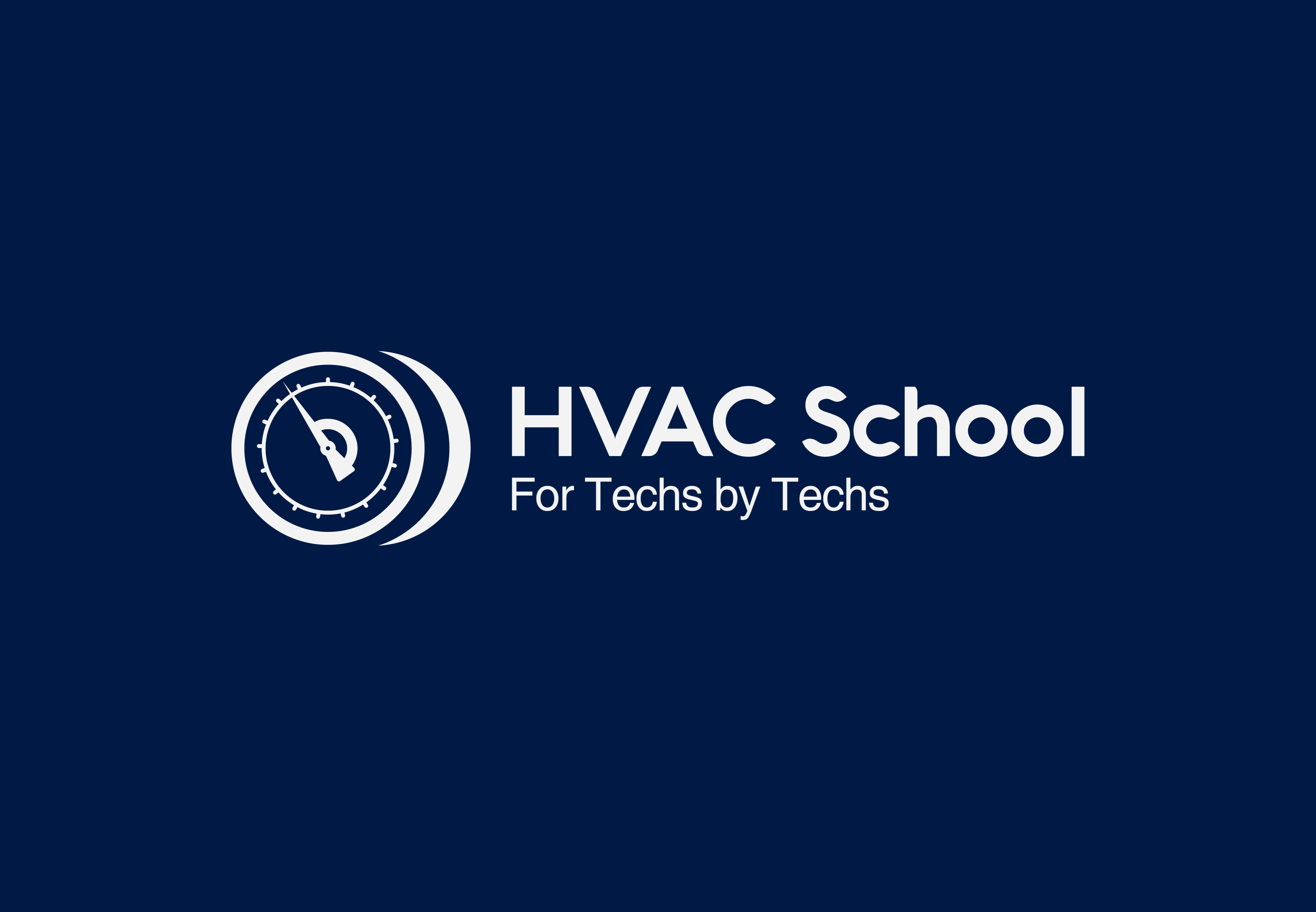
NOTE: If you cannot view the recording, the video may still be processing. The maximum wait time is 24 hours. We apologize for the delay and appreciate your patience.
Read more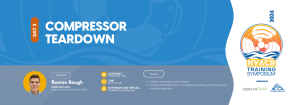
NOTE: If you cannot view the recording, the video may still be processing. The maximum wait time is 24 hours. We apologize for the delay and appreciate your patience.
Read more