BACK
3 Ways to Reduce Compression Ratio in a Heat Pump
3 Things to Check When the Unit Won’t Keep Up
The HVAC Technician’s Guide to Ensuring Comfort: Lessons from a Real-World Experience
Troubleshooting with DTD
Better Temperature Measurements
An Evaporator Coil With No Fins?
Air Velocity Quick Tips
How to Use a Manufacturer Fan Table and Why They are Important
ACFM, SCFM, & Baseball dents
Delta T Talk w/ JD Kelly
The PATH to High Performance HVAC w/ David Richardson
Oversized Evap Coils? – Short #237
Static Mistakes – Short #232
What Is Up With Blower Amps & Watts w/ Steve Rogers
Residential & Rack Startup and Commissioning (Part 1)
Spidey Sense – Airflow – Short #205
ECM and RTFM, This Is the Way!
#airflow
Tech Tips:
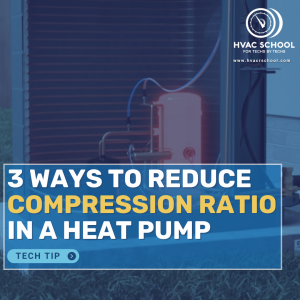
We’ve talked about compression ratio a lot over the years. Compression ratio is the number you get when you divide the absolute head pressure (PSIG + 14.7) by the absolute suction pressure (PSIG + 14.7). It measures the efficiency of a compressor, and lower numbers indicate that the compressor is moving more refrigerant while consuming […]
Read more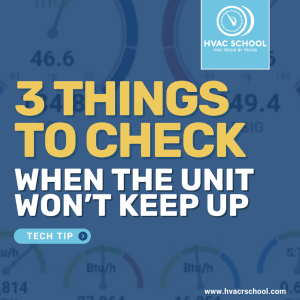
What is your methodology for troubleshooting an HVAC system that “can’t keep up” on the hottest days of the summer? Let me walk you through my process and hone in on one or two ideas that have been overlooked for too long in our industry. In this article, I’m assuming we have ruled out intermittent […]
Read more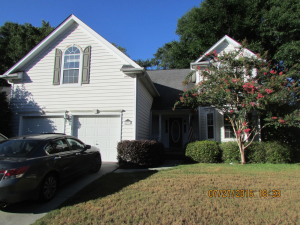
This tech tip was written by Luke Peterson, the president of The Maintenance Department in Louisville, KY. Luke was a speaker at the 5th Annual HVAC Training Symposium in 2024 and has been on HVAC business panels at the symposium in 2023 and 2024. Thanks, Luke! As an HVAC technician, your primary goal is not […]
Read more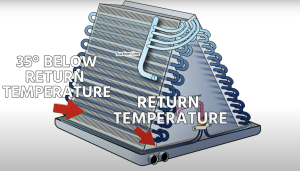
The temperature of the refrigerant in the evaporator coil can really help us with diagnostics, but we need to know the targets we’re aiming for if we want to get the most out of it as a troubleshooting tool. If we take the return air temperature and subtract 35 degrees from that number, we get […]
Read more
I am in the midst of testing the accuracy and repeatability of different types of airflow measurements for techs in search of the most practical methods for different applications. A commonly taught method for measuring airflow is the temperature rise method, where you use a heat source that produces a set number of BTU/h, such […]
Read more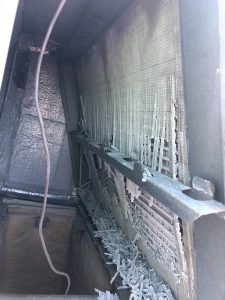
Let's use a bit of imagination for a minute. Imagine you have two totally identical 3-ton systems. One of them is completely normal, and the other has no fins at all on the evaporator coil. They both have the same charge, airflow, and compressor capacity. What will be different in terms of readings and performance […]
Read more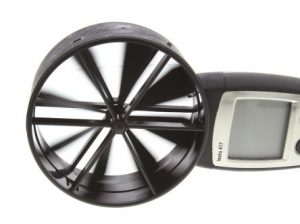
Recommended Duct Velocities (FPM) Duct Type Residential Commercial / Institutional Industrial Main Ducts 700 – 900 1000 – 1300 1200 – 1800 Branch Ducts 500 – 700 600 – 900 800 – 1000 As service technicians, we are often expected to understand a bit about design to diagnose a problem fully. Duct velocity has many […]
Read more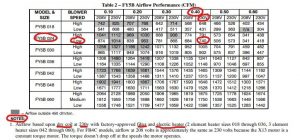
Many installers and service technicians know how to read and use a manufacturer fan table, but this is a quick review with a few extra tips for newer techs. It’s also a good reminder to senior technicians about how this easy-to-use practice can also be easily abused. At installation, properly setting up airflow is imperative to the […]
Read more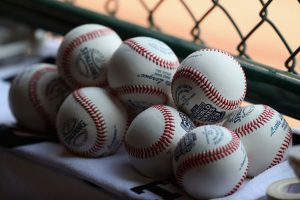
This is a VERY in-depth look at ACFM vs. SCFM and why it matters to airflow measurement from Steven Mazzoni. Thanks, Steve! Imagine your job is to figure out how fast baseballs were traveling before they hit a sheet-rock wall. The only method you have is to measure the depth of the dent left in […]
Read moreVideos:
Podcasts:
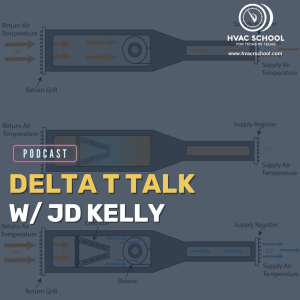
Bryan from HVAC School interviews JD Kelly, known as “student of HVAC” on Instagram, about Delta T measurements in HVAC systems. This episode dives into the fundamentals of Delta T, common misconceptions, and proper measurement techniques. JD explains that Delta T is simply a temperature difference between two points of the same medium, which […]
Read more
In this engaging session, David Richardson breaks down the concept of high-performance HVAC, offering a clear roadmap for industry professionals looking to elevate their craft. Richardson argues that the HVAC industry has long been focused on equipment rather than complete systems, leading to widespread inefficiencies. The average system delivers only about 57% of its […]
Read more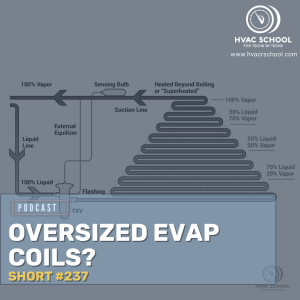
In this short podcast episode, Bryan answers a listener-submitted question about oversized evaporator coils, particularly when they're half a ton or a full ton larger than the condenser. The expanded performance data contains the information that'll tell you whether the coil is right for the system. However, when it comes to the specific issue […]
Read more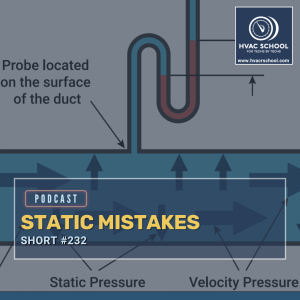
In this short podcast episode, Bryan covers some common mistakes when measuring static pressure. Static pressure is balloon pressure, not CFM or velocity pressure, but it can be an airflow indicator. The best way to start learning about static pressure is to start measuring total external static pressure. Gas furnaces and heat pumps are […]
Read more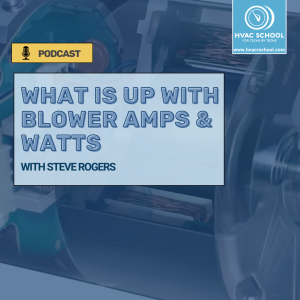
Bryan Orr and Steve Rogers dive deep into measuring power consumption in HVAC blower motors, particularly focusing on the differences between PSC (Permanent Split Capacitor) and ECM (Electronically Commutated Motor) technologies. The discussion stems from a question raised at an educators' conference about the accuracy of clamp-on meters in measuring blower motor watt draw, […]
Read more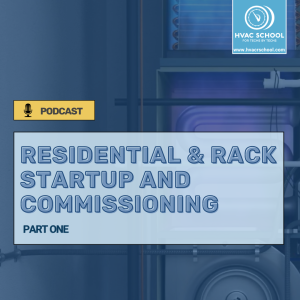
In this episode of the HVAC podcast, Bryan and Max Johnson from Kalos discuss the critical role of a startup and commissioning technician in the HVAC industry. Max, who has experience in both residential and commercial HVAC, shares his insights on the importance of understanding the scope of work, equipment specifications, and code requirements. […]
Read more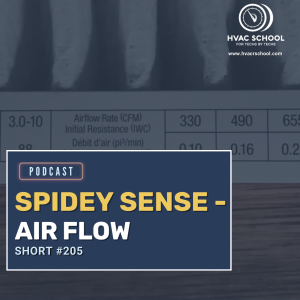
In this short podcast, Bryan talks about how to pay close attention to airflow issues and use your “spidey sense” when you're doing a visual inspection or commissioning a system. He also covers some causes of common airflow problems and some services and upgrades you can offer to your customers. The skill of being […]
Read moreEvents:

NOTE: If you cannot view the recording, the video may still be processing. The maximum wait time is 24 hours. We apologize for the delay and appreciate your patience.
Read more