Short 15 – Testing Capacitors, A Practical Approach (Podcast)
In this short podcast episode, Bryan Orr discusses the best practice methods for testing run capacitors in the field.
We understand the capacitor to be a voltage storage device. We can benefit from comparing the capacitor to a balloon that inflates and deflates with electrons as the alternating current changes (60 times per second). A capacitor causes a phase shift and allows there to be current on the start winding. So, when a run capacitor fails, you won't have current on the start winding.
The old-fashioned way of testing a run capacitor was to take an ohmmeter and charge/discharge the capacitor. Nowadays, we have capacitor testers, and many multimeters also have capacitance testers. Capacitance is merely a mathematical equation that you use when you compare the amount of voltage to the amount of current entering and leaving.
A good way to test a capacitor on a running system is to test it under load. You take the amperage of the wire feeding the start winding and multiply it by 2652. Then, you divide that product by the incoming voltage across the capacitor to get the capacitance. While this method is probably the most practical, it still has a caveat; some meters may have a hard time getting a proper amp reading on the start winding. So, tool accuracy will also determine your success when testing capacitors under load. To increase accuracy, make sure your wires are isolated from others. Under-load testing may also be unsafe in some cases, such as with a blower capacitor.
Testing with the system off is called bench testing, and it is slightly more accurate but does not represent under-load conditions. It will be more practical than under-load testing if the system is already off or if it is unsafe to test the capacitor under load.
Learn more about Refrigeration Technologies HERE.
If you have an iPhone, subscribe to the podcast HERE, and if you have an Android phone, subscribe HERE.
Author:
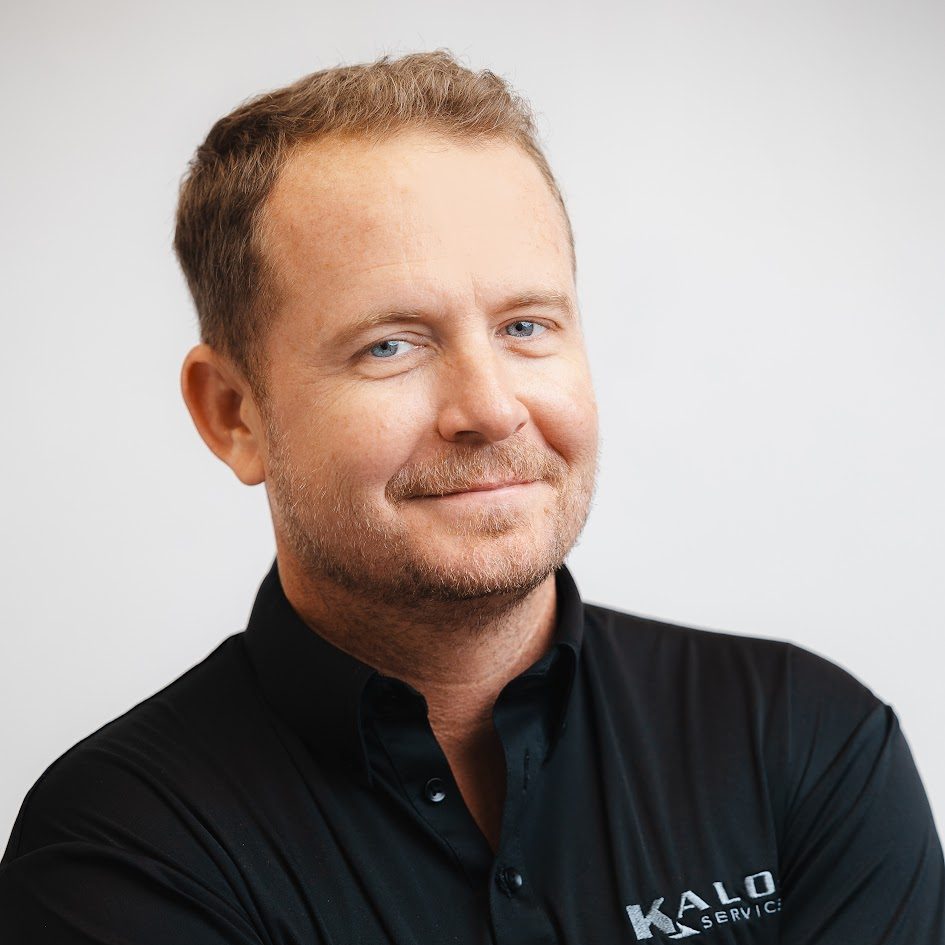
Comments
You are correct, do to degradation over time a capacitor does slowly lose capacitance. The question I have is at what point do you change it? I have seen some capacitors that’s say +/- 3%, some say +/- 5%, some say +/- 6%, and some say +/- 10%. I have a co-worker who says he has seen capacitors brand new out-of-the-box that’s say +/- 6% that are already 6% low so he goes by the rule of thumb when it reaches 10% low he will change it. What are your thoughts?
You are correct, do to degradation over time a capacitor does slowly lose capacitance. The question I have is at what point do you change it? I have seen some capacitors that’s say +/- 3%, some say +/- 5%, some say +/- 6%, and some say +/- 10%. I have a co-worker who says he has seen capacitors brand new out-of-the-box that’s say +/- 6% that are already 6% low so he goes by the rule of thumb when it reaches 10% low he will change it. What are your thoughts?
vente de mГ©dicament en ligne: pharmacie en ligne pas cher – pharmacie en ligne avec ordonnance pharmafst.com
vente de mГ©dicament en ligne: pharmacie en ligne pas cher – pharmacie en ligne avec ordonnance pharmafst.com
Cialis sans ordonnance 24h [url=http://tadalmed.com/#]Acheter Cialis[/url] Acheter Cialis tadalmed.com
Cialis sans ordonnance 24h [url=http://tadalmed.com/#]Acheter Cialis[/url] Acheter Cialis tadalmed.com
Cialis generique prix Acheter Cialis 20 mg pas cher or cialis generique
http://www.redloft.de/url?q=https://tadalmed.com Pharmacie en ligne Cialis sans ordonnance
[url=http://www.google.fm/url?q=https://tadalmed.com]Acheter Cialis 20 mg pas cher[/url] Tadalafil achat en ligne and [url=http://foru1f40m.bunbun000.com/bbs/home.php?mod=space&uid=9580900]Cialis en ligne[/url] Cialis sans ordonnance 24h
Cialis generique prix Acheter Cialis 20 mg pas cher or cialis generique
http://www.redloft.de/url?q=https://tadalmed.com Pharmacie en ligne Cialis sans ordonnance
[url=http://www.google.fm/url?q=https://tadalmed.com]Acheter Cialis 20 mg pas cher[/url] Tadalafil achat en ligne and [url=http://foru1f40m.bunbun000.com/bbs/home.php?mod=space&uid=9580900]Cialis en ligne[/url] Cialis sans ordonnance 24h
Achat Cialis en ligne fiable [url=http://tadalmed.com/#]Pharmacie en ligne Cialis sans ordonnance[/url] Pharmacie en ligne Cialis sans ordonnance tadalmed.com
Achat Cialis en ligne fiable [url=http://tadalmed.com/#]Pharmacie en ligne Cialis sans ordonnance[/url] Pharmacie en ligne Cialis sans ordonnance tadalmed.com
pharmacie en ligne pas cher pharmacies en ligne certifiГ©es or pharmacie en ligne
http://images.google.bf/url?q=https://pharmafst.com Pharmacie sans ordonnance
[url=https://maps.google.com.ly/url?sa=t&url=https://pharmafst.com]pharmacie en ligne fiable[/url] acheter mГ©dicament en ligne sans ordonnance and [url=https://www.soumoli.com/home.php?mod=space&uid=183507]pharmacie en ligne france livraison belgique[/url] pharmacie en ligne fiable
pharmacie en ligne pas cher pharmacies en ligne certifiГ©es or pharmacie en ligne
http://images.google.bf/url?q=https://pharmafst.com Pharmacie sans ordonnance
[url=https://maps.google.com.ly/url?sa=t&url=https://pharmafst.com]pharmacie en ligne fiable[/url] acheter mГ©dicament en ligne sans ordonnance and [url=https://www.soumoli.com/home.php?mod=space&uid=183507]pharmacie en ligne france livraison belgique[/url] pharmacie en ligne fiable
kamagra gel Achetez vos kamagra medicaments or kamagra 100mg prix
https://www.google.ml/url?sa=t&url=http://kamagraprix.shop kamagra pas cher
[url=http://images.google.gm/url?q=https://kamagraprix.shop]kamagra pas cher[/url] kamagra 100mg prix and [url=https://jutianwang.cn/home.php?mod=space&uid=21675&do=profile&from=space]kamagra 100mg prix[/url] kamagra oral jelly
kamagra gel Achetez vos kamagra medicaments or kamagra 100mg prix
https://www.google.ml/url?sa=t&url=http://kamagraprix.shop kamagra pas cher
[url=http://images.google.gm/url?q=https://kamagraprix.shop]kamagra pas cher[/url] kamagra 100mg prix and [url=https://jutianwang.cn/home.php?mod=space&uid=21675&do=profile&from=space]kamagra 100mg prix[/url] kamagra oral jelly
kamagra pas cher: Acheter Kamagra site fiable – Acheter Kamagra site fiable
kamagra pas cher: Acheter Kamagra site fiable – Acheter Kamagra site fiable
pharmacie en ligne france livraison internationale: Meilleure pharmacie en ligne – pharmacie en ligne sans ordonnance pharmafst.com
pharmacie en ligne france livraison internationale: Meilleure pharmacie en ligne – pharmacie en ligne sans ordonnance pharmafst.com
olympe: casino olympe – olympe casino en ligne
olympe: casino olympe – olympe casino en ligne
To leave a comment, you need to log in.
Log In