Combustion Analyzer Facts and Mistakes
Our main man, Bill Spohn, joins us again to talk specifically about combustion. He also explains how to select and properly utilize a combustion analyzer.
It's critical to do combustion analysis when you service equipment for the first time or just after installation. We need benchmarks, so that's when our combustion analyzers can come in handy. (Of course, you also want to use your senses to inspect the equipment.) Commissioning is another good time to bust out your combustion analyzer.
Combustion analyzers should properly measure oxygen, temperature, and CO. Oxygen and temperature sensors tell you the combustion efficiency, and the CO sensor tells you about the carbon monoxide content. However, the CO sensor should also have a NOx filter to prevent nitric oxides from showing up as CO. The goal is to have no CO present in the living space, and sensors that pick up NOx can raise a false alarm.
Some combustion analyzers also have pressure sensors, which can detect static pressure drops across heat exchangers or filters. You can use these for some building-performance tests, including zonal pressure diagnostics. You can also potentially measure ambient CO with your combustion analyzer.
Once you have your combustion analyzer, you need to calibrate it and maintain it. Temperature sensors rarely need recalibration, but your CO sensor needs occasional recalibration after repeated exposure to gas. NOx filters can also expire and may need replacement.
Overall, combustion analysis is a critical part of gas furnace inspection. However, it's best to use other inspection methods too, such as looking for heat exchanger leaks.
Bill and Bryan also discuss:
- Flame displacement
- Condensation buildup
- Nitric oxides on CO sensors
- Dilution of CO and base signals
- CO alarms
- How CO sensors work
- How air enters the home
- Induced-draft systems under negative pressure in the flue
Learn more about Refrigeration Technologies HERE.
Author:
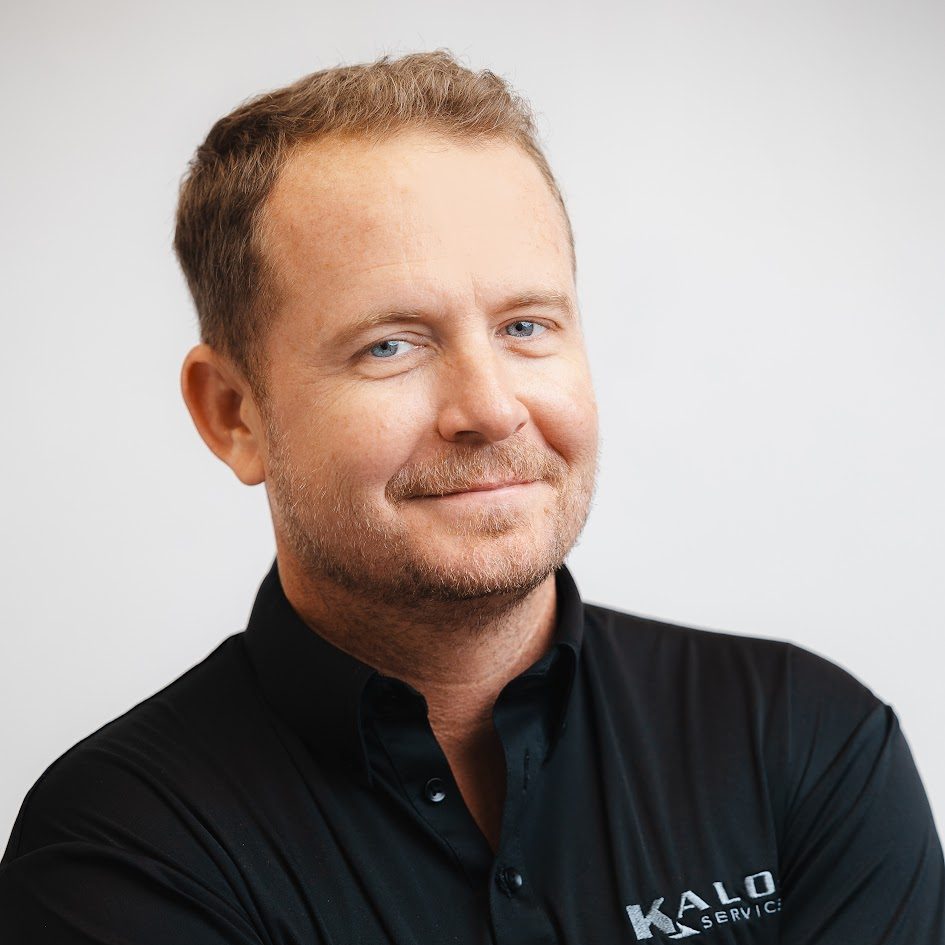

Comments
To leave a comment, you need to log in.
Log In