Get Tech Tips
Subscribe to free tech tips.
How Do Communicating Systems Work?

This tech tip recaps the livestream by the same name, featuring HVAC School contributors Matt Bruner and Adam Mufich, as well as special guest Steve Cook from Hisense. You can watch that livestream on our YouTube channel HERE. We also owe special thanks to Roman Baugh, who added some extra information on the topic.
Communicating systems can be a bit intimidating for techs who don’t regularly work on them. Sure, 24v AC systems “talk” to their components by sending signals from the thermostat, but we have wires for each function (like O or B for the reversing valve and R for constant 24v cooling or heating). But communicating systems seem to be in another league; they use different voltages, have blocky sine waves, and so many sensors.
However, communicating systems are far more efficient for transmitting information than mere relays. They send and receive data in binary packets (think 1s and 0s) very quickly, enabling the system to modify things like compressor speed for better efficiency.
We’re going to demystify them a little and cover the key differences between communicating systems and those with 24v AC controls. We’ll also cover some common considerations for troubleshooting and best practices for installation and service.
What is a Communicating System?

Traditionally, unitary non-communicating systems use thermostats that use 24v AC controls. There are several wires attached to the thermostat, each one with a specific function. For example, a Y call energizes the contactor coil, energizing the compressor, and a G call energizes the blower.
Communicating systems exist in residential and commercial HVAC, and the definition boils down to systems that have controls that are a little more advanced than traditional 24v AC controls. Communicating systems include VRF/VRV systems and inverter-driven equipment that relies on DC signals from sensors, including transducers, to adjust the operation. Some ductless mini-splits fall into this category.
Transducers
Transducers are modulating devices that read pressure at a point in the system and give feedback to the board in the form of DC signals. They don’t open or close quite like a switch, but they modulate a specific DC voltage supplied to them and send that modified signal back to the board about suction, head, and discharge pressures. The board can then decipher the new information and tell the compressor to run faster or slower to get back within the target pressure range(s).
Thermistors and thermocouples carry out the same function as transducers, but they give feedback to the board about the temperature, not the pressure. Instead of a constant voltage being supplied and then modified, they are resistors that change resistance based on temperature. Most thermistors within communicating equipment are 20-kilohm, but there are 10-kilohm and 5-kilohm thermistors that are used in other brands of equipment.
How Communication Happens
Communicating system signals run on two wires: one for sending signals and the other for receiving them; you can think of it as two people having a conversation. You may think of 24v AC controls as a one-way conversation with several people at the same time.
The DC signal generated by the main communication board acts as a carrier wave or highway in which information is carried to other control components within the system. Each OEM has a communication protocol unique to its brand, so there are language barriers when you use components that aren’t from the communicating system’s OEM. (Think of one manufacturer’s equipment as speaking English and another as speaking Spanish or Mandarin Chinese. No meaningful communication can occur if the languages aren’t mutually understood.) Modbus and BACnet are examples of protocols. The voltages of the DC carrier signal also vary by manufacturer, but the actual communication process is the same across all of them.
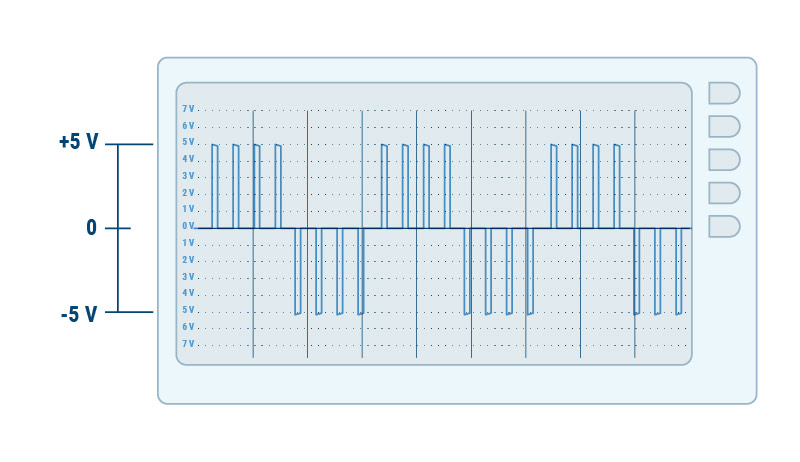
The DC voltage provides the electromotive force that pushes signals along the path, but the actual data packets are embedded in pulses. So, we can think of the DC voltage signals as carrying the pulses (and the data). There are two points on each system that you can use to measure these voltages, though the point names also vary by manufacturer.
Benefits of Communicating Systems Over 24v AC Systems
Many of the benefits of communicating systems deal with efficiency. High-efficiency equipment allows the components to communicate with each other to match the system’s operating speed and capacity to the situation. As government regulations shift in favor of higher-efficiency equipment, HVAC systems will need to monitor and respond to more sensors and system data to meet those higher standards.
Traditional split systems that use 24v AC signals aren’t equipped to handle much more than an on/off function for their respective components. The indoor and outdoor units can’t “talk” to each other, so that’s why systems run business as usual despite the fact that a coil may be completely frozen.
It’s unrealistic to increase the number of conductors, terminals, and relays to transmit the sheer amount of information that communicating systems work with. Communication along two wires also makes it easier for the equipment to fault under poor operating conditions, which cuts back on wasted energy.
Constant communication between the indoor and outdoor unit allows the system to flex or adjust to changes in ambient conditions and heat load within a structure. A communicating system is always adjusting compressor work to achieve targets and demand while maximizing efficiency.
VRF/VRV Equipment
Variable refrigerant flow (VRF) or variable refrigerant volume (VRV, Daikin-specific) systems are able to run several different ductless units on the same system. These are inverter-driven systems with a lot of moving parts, but these systems aren’t complicated just for the sake of being complicated.
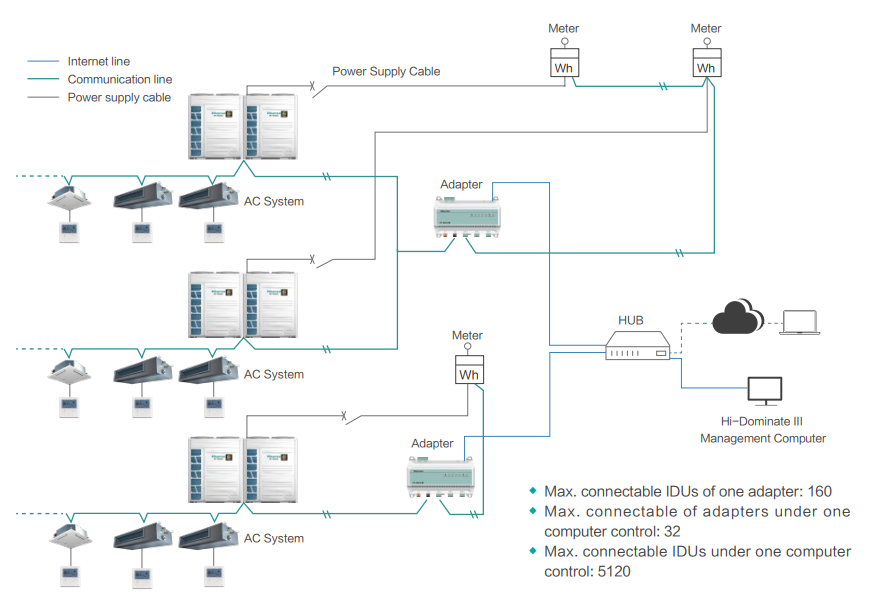
Credit: Hisense
VRF/VRV systems need to know what all other units and parts are doing at all times to work as intended. For example, discharge temperature is a major indicator of compressor performance, and the system needs to know that value to change the compressor’s motor speed.
Roman Baugh wrote a tech tip about troubleshooting inverter boards for those of you who want to learn more about inverter boards—the heart of what drives these types of compressors.
Reading DC Signals and Pulses
If you attempt to use a multimeter to read the voltage on a communicating system, you’re not going to get a lot of information about the pulses being communicated. Sure, you’ll read that voltage is present, but you won’t catch the individual pulses.
Oscilloscopes are the only types of devices that can pick up DC signals in their entirety. As opposed to a smooth sine wave, you’ll see waves that look more like alternating positive and negative blocks. Those digital signals carry the “pulses” being communicated between components. The pulses are only a fraction of the actual voltage (for example, Hisense’s DC signals are 5 volts, but the pulses are only 2.8 volts of that).

Now, catching those pulses won’t always be relevant. But you’ll want to make sure that the wires are sized and selected correctly so that the signals can be transferred.
Wire sizing varies from brand to brand, and the wires need to be stranded and usually shielded (not solid). Bending creates microfractures in solid wire, which can interfere with the pulses being sent and received; you may not get a communication fault automatically, either, which can make diagnosis tricky.
The main communication board, typically in the outdoor unit, is where the source of our communication signal is generated. Some manufacturers have auto-addressing capabilities, but others require DIP switches to be enabled to add resistance to the communication line. This added resistance tells the system where the last indoor or outdoor unit is in the communication circuit.
Installation Practices
As with communication between people, communicating systems are prone to having their signals interfered with. Interference can happen when you run communication wires in the same conduit as high-voltage wires. The magnetic interference of the high-voltage wires will corrupt the data embedded in the signals. So, the ideal installation practices will aim to reduce interference as much as possible.
To minimize interference, you’ll want to use shielded wires and avoid running them with other wires that could induce voltage. You can run communication wires with refrigerant piping as long as those wires have weatherproof jackets; otherwise, you should use a conduit just for communication wiring. You’ll also want to ground only one side of the shielded conductor; grounding both will create an antenna, which will ultimately create more interference rather than resolve it. Remember to never ground the shield on communication wire under the same ground for high voltage devices. Doing so can lead to ground faults traveling along the communication wire and damage other components.
It’s also best to reduce junctions as much as possible and get the straightest shot from unit to unit. Communication wires can be finicky, and too many bends can interrupt the signal. (Those of you who have worked on case controllers that use Cat5 ethernet cable probably know that problem all too well.)
Additionally, wire nuts allow moisture to make its way to the surface of the electrically charged copper wire, creating the perfect conditions for corrosion. Think of the positive terminals on a car battery over time.
In general, the longer and more complicated the run from unit to unit, the more important the shielded cable will be for reducing the risk of interference. And surge protection won’t be much help in high-voltage events like lightning strikes.
Troubleshooting Communicating Systems
Communicating systems often have fault codes that will give you a starting point for troubleshooting. Fault codes will let you know what type of failure the system is experiencing.
However, in some cases, the data within the signal isn’t transmitted from Point A to Point B, and nothing is happening. There may not be a fault code in these cases. The pulse is being lost, and the diagnosis comes down to an issue with the board or the wiring. You would need to understand the protocol and have an oscilloscope to troubleshoot precisely, but many technicians will lack at least one of those.
Luckily, we rarely ever have to go that deep to fix the problem if we inspect the communication wires and check for possible sources of interference. Replacing the wiring is one of the most likely solutions. Remember, communication wires are quite fragile and finicky. The two most common issues are either with faulty communication wires or addressing; you’ll receive a fault code for the latter. When in doubt, run a temporary wire to see if communication can be restored.
While communicating systems may be more complex than systems that use 24v AC controls, their issues won’t often be that tricky. There’s often a psychological barrier rather than a skill barrier when it comes to troubleshooting these. On a basic level, the same investigative skills and urgency that we use to troubleshoot 13-SEER split systems will apply to just about any system; you just need to account for the context of each situation.
And remember: the ultimate goal of troubleshooting is to get equipment back online, not necessarily to understand exactly what went wrong from the inside out.
Troubleshooting Daisy-Chained Communicating Systems
Daisy-chained systems tend to be relatively easy to troubleshoot. You’ll be able to tell if there’s a problem at indoor unit #5 if there are no signals from units #6–10. If you don’t have a fault code, you can take voltage and resistance readings throughout the system to figure out what’s wrong.
Best Practices
No matter if you’re working on residential HVAC or commercial refrigeration, here are some best practices to use when working on communicating systems:
Visual Inspections
As with any other HVAC system, a visual inspection will go a long way. A thorough visual inspection will allow you to notice clues about what could be wrong with a system, and it could also help you learn more about the system.
If possible, check the communication wires. Are they bent? Near wires that could induce voltages (and cause interference)?
Remember, although these systems may be complex, they still require the same skills and troubleshooting mindset as any other piece of HVAC equipment.
Tight Connections
Ideally, crimp connections should only be done at the terminal block, not in the middle of a run. Soldered connections are the most effective, but they’re not always practical. That said, it’s best to avoid using junctions at all because it’s too easy for the system to lose communication through a junction. If you have absolutely no other choice, then a soldered connection is better than a crimp connection.
Whenever you make a crimp connection, you must use the correct crimp for the type of wire—insulated or uninsulated.
Make sure your connections are snug and won’t come loose easily. Give them a decent tug once you’ve made the connections so that you can make sure they stay firmly in place.
Addressing
DC communicating systems will be addressed to allow communication to happen. You can think of the system number as the street name, and the address is the building number (which corresponds to each individual unit).
Many unitary systems are addressed from the factory, so we don’t need to worry about it in those cases. VRF/VRV systems often need to be field-addressed; some brands have auto-addressing capabilities, which is a software set. However, they may be prone to resetting, especially during long power outages.
Whenever we have a centralized control with more than one system, we want to do a hardware set. Hardware setting requires us to configure rotary dials, DIP switches, or a binary code to set the address instead of relying on software to do it. Many of these sorts of address errors are caused by DIP switches that have been set improperly during service.
The individual indoor units need to be addressed separately so that all of the parts can talk together at the same time. For that reason, you will get a fault code if the same address is used for multiple units in a system.
Lastly, isolate communication wires and check resistance (not Continuity) between both wires. Remember, we are looking for high-resistance shorts or damage to the wire. Typically, anything less than 540 ohms between communication wires or to ground will cripple a system without generating an error code.
Communicating System Reliability
We’ll end on the million-dollar question: are communicating systems more reliable than traditional HVAC systems with 24v AC controls?
The answer isn’t that simple.
On the surface, there is more that could go wrong in communicating systems because there are more components involved in the system’s operation. However, if everything is installed properly (i.e., the best practices mentioned above were followed), then reliability shouldn’t be any more of a concern than it is in systems with traditional 24v AC controls.
Installation, commissioning, and maintenance are the keys to reliability. Whether you work on a traditional standard-efficiency split heat pump or a commercial VRF/VRV communicating system, you will usually have good results if you give the installation and maintenance procedures the attention they deserve. Of course, there will always be outliers with defects from the start, but communicating systems are no more or less reliable than the systems most of us have worked with for years.
No matter what type of HVAC/R system you work on, the same principles will always prevail: use your senses to investigate, make sure your installations are done well and properly commissioned, and make maintenance worthwhile.
Comments
To leave a comment, you need to log in.
Log In