Get Tech Tips
Subscribe to free tech tips.
Heat Pump Defrost Troubleshooting Tips
We’ve entered that season of service calls for “smoking heat pumps,” and I figured now is as good a time as any to share a few quick tips for troubleshooting defrost. Of course, the “smoking heat pump” calls can be solved over the phone with a quick explanation of normal defrost conditions—as can the service calls for a slightly frozen outdoor coil. However, problems with the defrost cycle can happen, and we should know the basics of how to solve them.
The good news is that defrost issues can be narrowed down to just a few possible problematic parts. These parts are the circuit board, temperature sensors, and wiring or harnesses. Defrost control boards will also usually have fault codes for when things go wrong, so you should have a basic idea of where to start looking.
Time and Temperature vs. Demand Defrost
The defrost cycle requires the reversing valve to shift, the auxiliary heat to come on, and the fan to stop working. However, there are two different defrost methods: time and temperature (T/T) defrost and demand defrost.
Time and temperature (T/T) defrost requires the coil sensor (thermostat) to close, which then starts a timer. (Carrier defrost thermostats close at 32°F.) If the equipment continues to run for a specific time interval—usually 30, 60, or 90 minutes—and the defrost sensor or thermostat remains closed, then it will initiate defrost.
From there, the defrost cycle will happen, and the defrost cycle will terminate once the coil temperature sensor reaches a set temperature. (Again, the Carrier defrost thermostat will open at 65°F.) There is also a maximum timeframe for defrost, like 10 minutes for the Carrier defrost board; that can usually be configured when you have universal boards, but that timeframe is built into many OEM boards.
On the other hand, demand defrost checks the coil temperature sensor and outdoor air temperature sensors at all times. Instead of going into defrost after 30–90-minute runtimes, it only goes into defrost when the temperature difference between the sensors exceeds a set difference. However, there is usually a maximum time between defrosts; six hours is a common timeframe. Demand defrost can offer major energy savings.
Checking Fault Codes
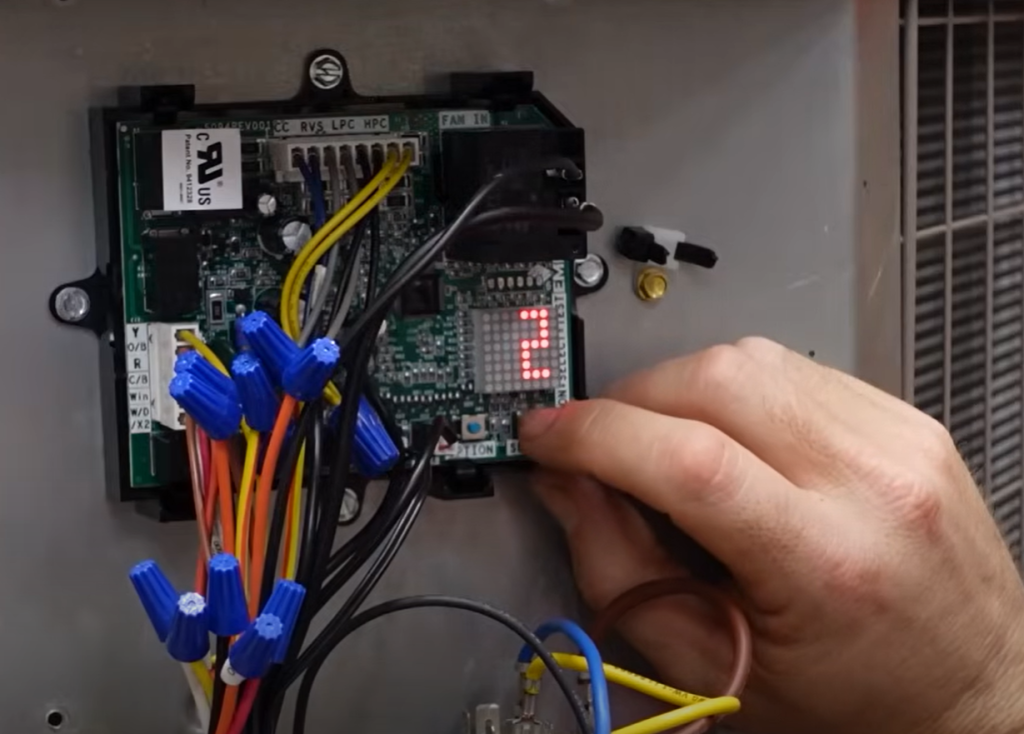
After you’ve done a visual inspection of the entire system, the first place to start in the “narrow” part of your diagnostics is by looking at the fault code. That fault code will tell you which switch has tripped, and you can start narrowing down your diagnoses from there. These fault codes will be in the defrost control’s manual (though some defrost controls, like the White-Rodgers 47D01U-843 universal defrost board, come with stickers of the fault codes and their meanings that you can affix to the unit).
Below is an example of fault codes (and other conditions) on the White-Rodgers 47D01U-843 universal defrost board’s display:
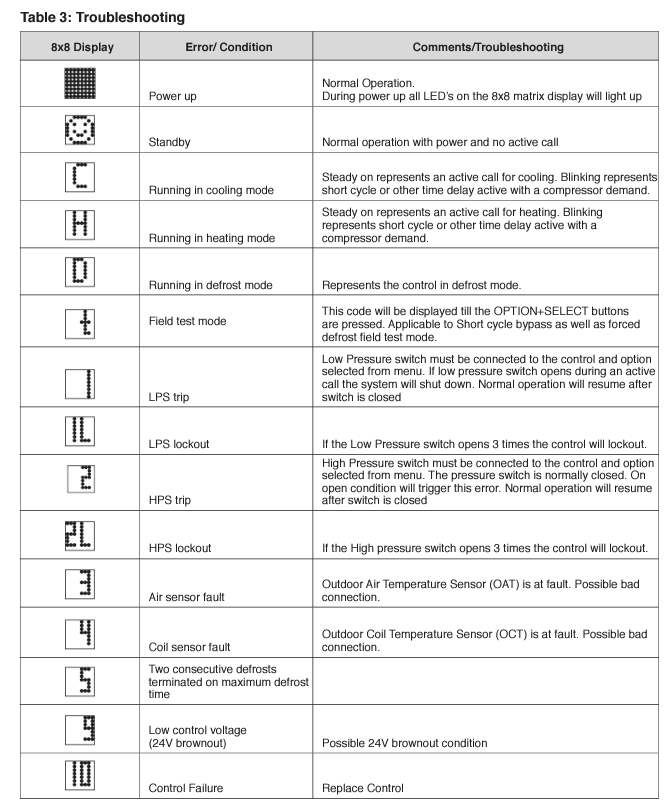
Credit: White-Rodgers by Copeland 47D01U-843 Installation Instructions
And here is one of Lennox's defrost boards with blinking lights instead of digital displays:
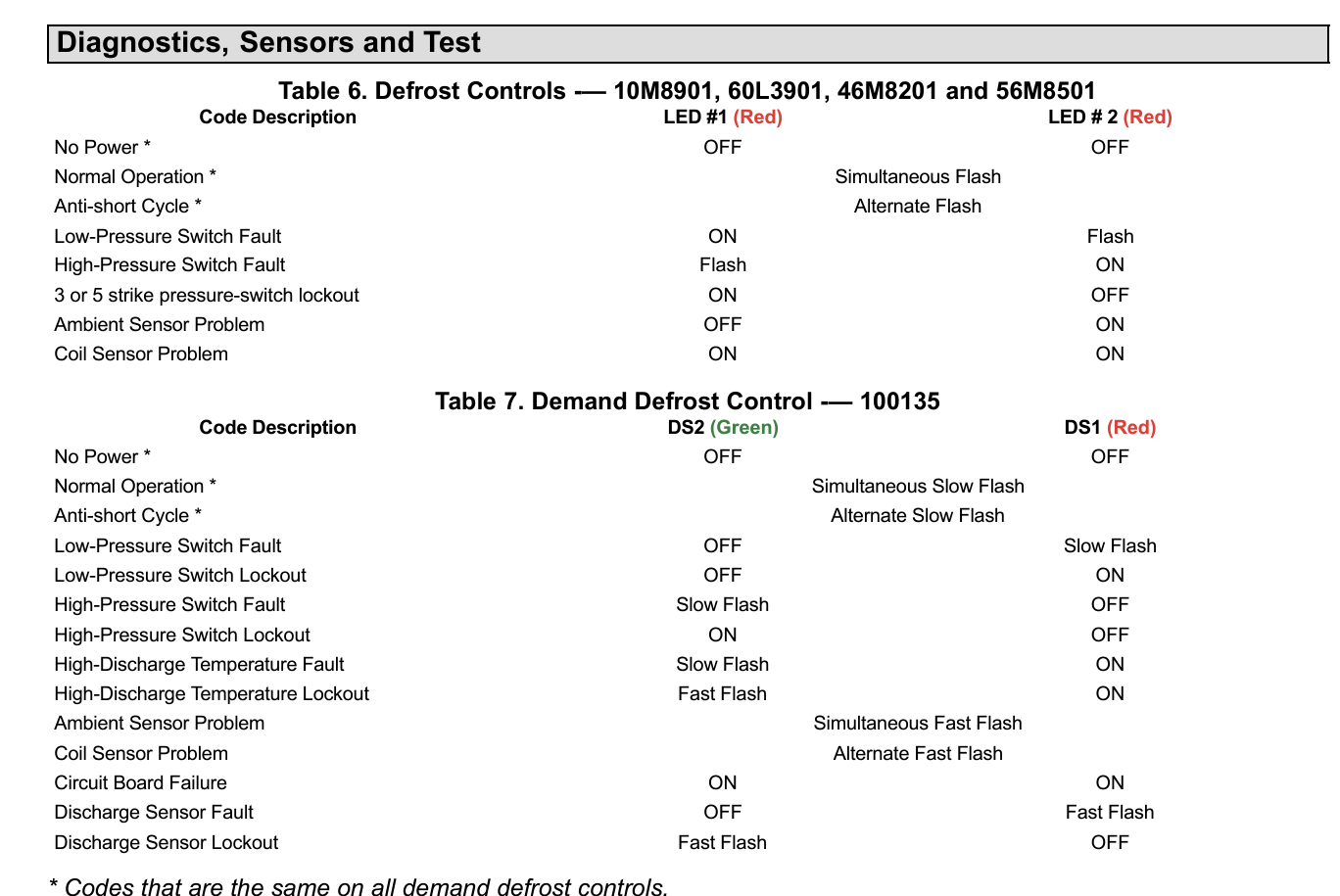
Credit: Lennox – Installation Instructions For Replacement Defrost Control Kit (15D57) Used With Various Heat Pumps (pg. 9)
Of course, not many of those codes are directly related to the defrost cycle, but they provide a solid starting point for diagnosis.
Since the defrost cycle is a function of several controls, we mostly want to make sure that the sensors work properly (i.e., that they either open and close when they should or that they have the right amount of resistance) and that there is voltage in the right places.
Testing Defrost
We can test the system in defrost to make sure we’re getting the right voltages a heat pump needs to operate as intended. We can jumper out the defrost board to test the defrost cycle itself, but that doesn’t allow us to test the thermostat and whether it opens or closes as it should.
Therefore, it’s a good idea to run the unit in heat mode with the fan off to allow a little bit of frost to build up on the coil. Then, the speedup tap makes the board check for defrost at quicker intervals than the timer that’s been set.
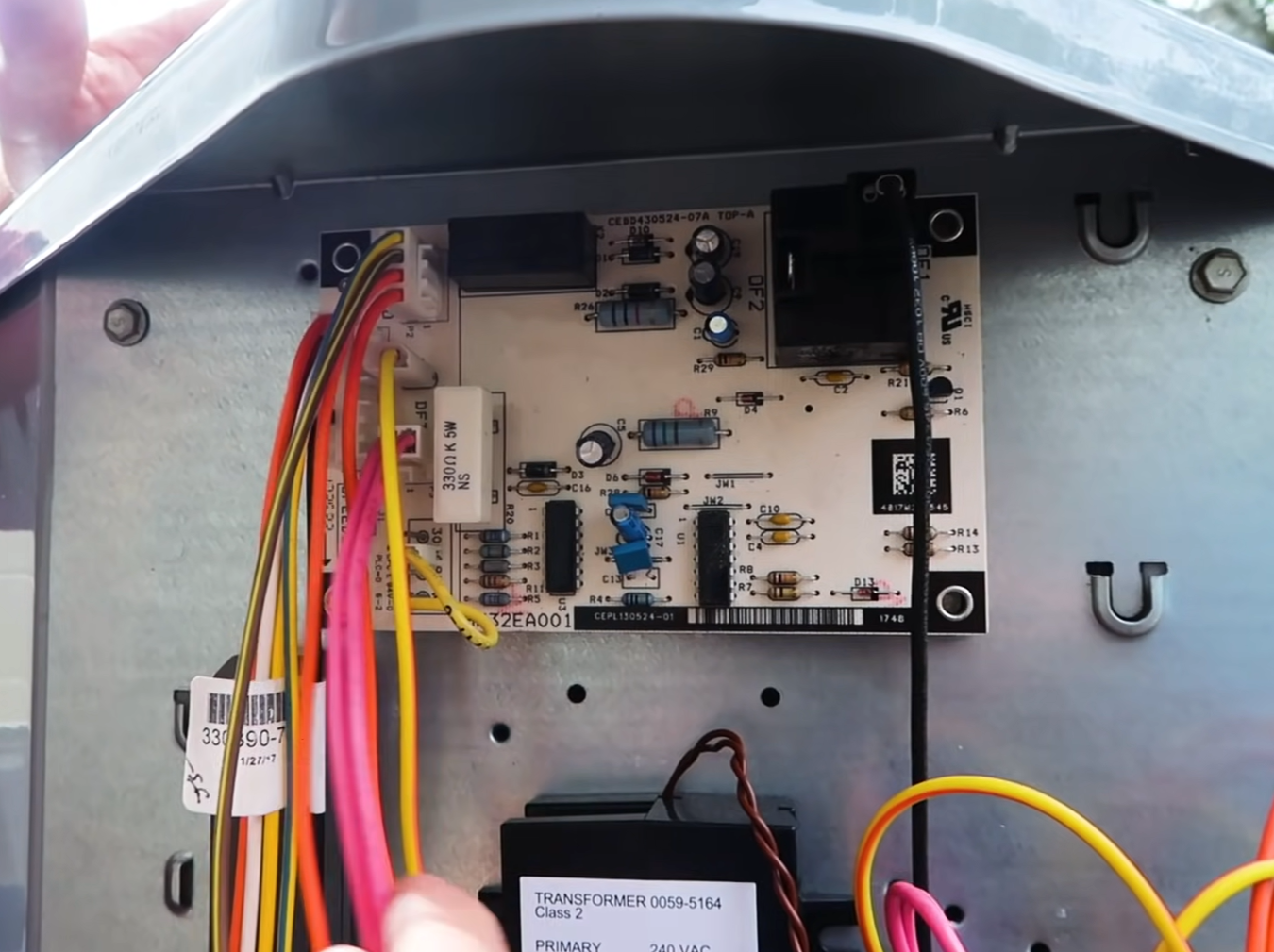
The following process is typical of a Carrier defrost board. Each manufacturer will have its own method, and some universal controls have their own testing protocols.
- Disconnect the fan from the defrost board while the system runs in heat mode.
- You can jumper out the defrost thermostat if the temperature sensor is a thermocouple, but this step will allow frost to accumulate on the coil and make sure the thermostat recognizes that it needs to go into defrost.
- Speed up the defrost with the speedup tap, and then plug the fan back in.
- Measure voltage between O and Common (24v).
- Measure voltage between W and Common (24v).
- Watch the system come out of defrost and verify that the condenser fan comes back on.
Electrical Diagnostics
Connections to the board must be tight and configured properly for the climate and application (e.g., for demand defrost). When you do your visual inspection, make sure the connections are snug and that there are no signs of arcing.
During the defrost cycle, the reversing valve switches over to cool mode and the auxiliary heat comes on (usually electric heat strips in our market, but the aux heat may be gas if there is a dual fuel setup). When you test defrost, you can verify these by measuring the voltage between their respective terminals and common.
- Voltage between O (reversing valve) and Common = 24v
- Voltage between W (backup heat) and Common = 24v
Ruud and Rheem heat pumps utilize the B terminal instead of the O terminal, and they energize the reversing valve in heating mode.
In ALL operating modes, you should read around 24v between Y and Common and R and Common at the defrost board. Y connects to the contactor coil, and R runs constant 24v power. The board will run without R because there will be a Y call, but defrost can’t occur because R redirects on O and W, and your heat strips and reversing valve can’t work if there isn’t 24v on R.
Coil Sensor Problems
Defrost boards like the 47D01U-843 universal defrost board have a fault code for coil sensor faults. In our experience, temperature sensor failure is relatively uncommon. Many of the problems that deal with coil temperature sensors involve damage to the conductors (such as by animals or lawn equipment) or shorting out. That’s why a visual inspection is one of your most valuable skills when it comes to troubleshooting defrost. You can spot damage, loose wiring connections to the board, or sensors with poor contact on the coil.
When we have snap-action thermocouples as temperature sensors, our main goal is to make sure that they close at the defrost control’s set point to begin the defrost cycle and open at the temperature needed to terminate defrost. Thermistors behave a bit differently, and you will need to ohm them out and compare your resistance reading to the temperature per the manufacturer’s recommendation.
If you’ve verified that the connection is solid and still notice that the sensors aren’t closing properly or have resistance values that don’t match up with the manufacturer’s recommendations, you can condemn the bad sensor and replace it.
This tip isn’t a comprehensive guide to heat pump defrost by any means, but it goes to show that a lot of the issues with defrost will be electrical, and you’ll usually have fault codes or visual indicators that something is wrong. Each manufacturer is a little bit different, so be sure to read the manual each time you need to mess around with a heat pump’s defrost board.
Comments
To leave a comment, you need to log in.
Log In