Get Tech Tips
Subscribe to free tech tips.
Blower Fan Watt Draw Considerations for ECMs
I'd like to give special thanks to Steve Rogers from TEC for helping write this tech tip and sharing some helpful visuals. Thanks, Steve!
ACCA Standard 310 introduced a grading protocol for HVAC systems. While HVAC practitioners won’t be the ones carrying out the tasks laid out in Standard 310, energy raters will conduct them so that builders and homeowners can get tax credits based on system efficiency. Systems will need to hit certain minimum grades to qualify for tax credits, and it’s on HVAC installers and technicians to set systems up for success. However, one potentially confusing task in ACCA Standard 310 is the blower fan watt draw, especially when you’re dealing with ECMs.
The blower fan watt draw is the fourth test under ACCA Standard 310, and HVAC systems can qualify for the highest possible rating with results of ≤0.45 watts per CFM. It can be performed in three different ways: a plug-in wattmeter, a clamp-on wattmeter, or by essentially clocking the utility meter. Those obviously aren’t things most techs will have in the field to test blower fan watt draw themselves, but techs may have a direct impact on the watt draw based on field practices.
Once we understand some basic electrical principles and are aware of the unique features of PSC motors and ECMs, we can think about how a system and fan motor might work together to get a passing efficiency grade and still perform well.
Inductive Loads and Power Factor
Motors are inductive loads because of the magnetism of the motor. AC motors reverse polarity 120 times per second in the USA (as 60 hertz is the standard utility frequency in North America, and the polarity reverses twice in each cycle.). We can graph that electrical activity on a sine wave.
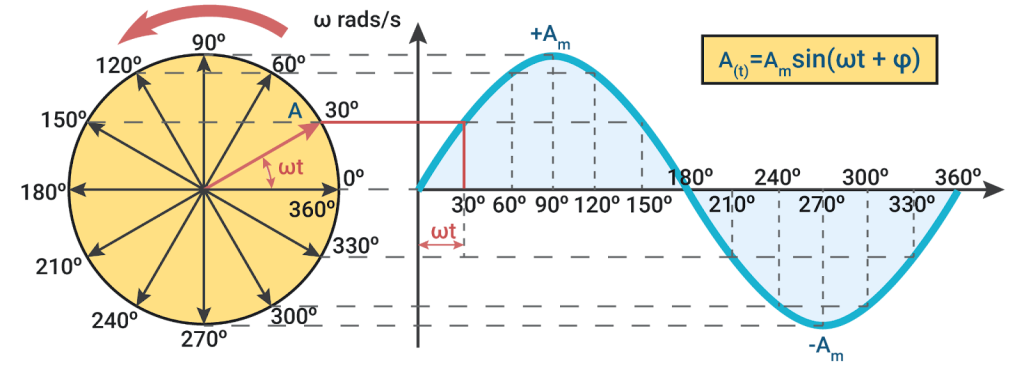
Inductive loads are subjected to inductive reactance. If you want to get into the nitty gritty of inductive reactance, you can read THIS tech tip, but it’s basically a force that resists the flow of electrical current, like resistance. In resistive loads, like electric heat strips or a toaster, that resistance creates heat.
However, inductive reactance causes the current to lag behind the voltage in inductive loads like motors. That current is still heating up the wires the entire time, but it’s not moving in the same direction as the voltage and can’t help turn the motor if the current and voltage are acting in opposite directions. (See the “phase shift” note in the attached diagram.)
Credit: Steve Rogers (TEC)
While you can multiply the volts by the amps to get volt-amps, that lag renders some of those volt-amps useless, so they don’t count towards the real power. You can think of it as the motor mostly pushing on the shaft in the direction it's turning. But for a tiny bit of the time (about 2 microseconds in each electrical cycle), it pulls back in the wrong direction, which wastes some of the energy.
Volt-Amps (VA) vs. Watts
On the surface, Watt’s law states that power (wattage) is equal to volts x amps, but when the voltage and the amperage are both changing very quickly—like every millisecond, we have to be careful how we apply it. The math still works, but if the voltage and current are changing every millisecond, then we can’t just measure the RMS voltage and current over a much longer time and multiply them together. If we just multiply the RMS voltage by the RMS current, we get the apparent power. That’s why we make the distinction between volt-amps (VA) or apparent power and watts or real power.
In a world where all electrical loads are pure resistance, like heat strips, the voltage and current will peak and valley at the exact same point on a sine wave. But with an inductive load, the inductance pushes the current back in time, so the current doesn’t peak at the same time as the voltage. More importantly, this means that as the current changes from positive to negative, it doesn’t cross zero at the same time as the voltage does, either. So, for a short period, we have a positive voltage and a negative current or vice versa; some of the power can’t perform any work because of the lag caused by impedance.
That’s where power factor comes in. The highest possible power factor is 1 or unity, which indicates that the current and voltage switch polarity (cross 0 on a sine wave) at the same time. With a unity power factor, volt-amps and watts are equal because the voltage and current are always acting in the same direction.
On a PSC motor, a more realistic scenario would be if the voltage crossed 0 slightly before the current, resulting in a power factor of around 0.91. This value would indicate that 91% of the apparent power (volt-amps) is performing usable work, and the remaining 9% consists of reactive power, which doesn’t perform work (and the utility company doesn’t charge for it). But that doesn’t mean we can completely ignore the apparent power; it still has some significance. That’s because electric current heats up the wires regardless of which direction it flows. So, when we look at electrical codes to decide what gauge of wire is required, it may depend on apparent power, not just real power.
The Catch
Everything I just said applies to alternating current (AC) with inductive loads. Unlike PSC motors, in which the current is determined by the inductance and resistance inherent to the motor’s windings, ECMs have a non-sinusoidal current that is controlled electronically. The electronic controls send out a quick pulse of current that is timed to be near the peak of the voltage sine wave. But for most of the electrical cycle, about 80% of it, the current is zero.
On an oscilloscope, the ECM’s current waveform consists of pulses of current that look like you chopped off just the peak of a sine wave.—so the current waveform is not sinusoidal. Like AC inductive loads, the power factor won’t be unity (as it would be with something like electric heat strips), but it’s not because of a lag between voltage and current as it is with a PSC motor. In this case, the power factor is low just because of how the math works out when the current is not a sine wave.
Credit: Steve Rogers (TEC)
As a result of these differences, ECMs have significantly lower power factors than PSC motors—usually 0.5–0.6. But this doesn’t mean ECM motors are less efficient than PSC motors. Power factor is NOT a measure of motor efficiency. In fact, ECM motors are significantly more efficient than PSC motors because the power doesn’t become negative at any point in the electrical cycle. So it doesn’t “fight itself” for part of the cycle like a PSC does.
With all that in mind, how can we meaningfully evaluate the performance and efficiency of an ECM in a way that puts PSC and ECM motors on an equal footing?
ECM Performance and Efficiency
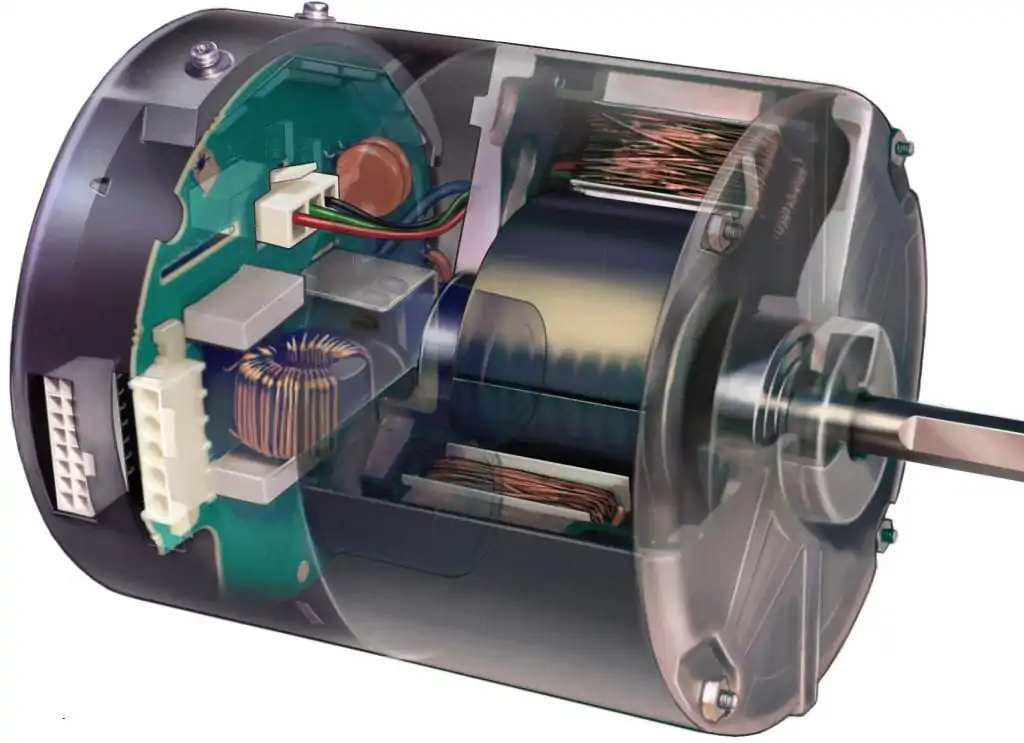
First, we need to understand that we can only accurately measure ECM wattage with an electrical meter that can accurately calculate the real power fast enough to capture the fast current pulses used by an ECM. That would be a “true RMS” meter.
“True RMS” meters sample waveforms a lot more quickly than non-true RMS meters, which mostly calculate voltage and current based on assumptions about how all 60-Hz sine waves work. However, current pulses don’t follow those assumptions, so you need to have a true RMS meter anytime you have an inverter-driven system or ECM to sample all of those pulses to form an accurate average.
In a recent study conducted by The Energy Conservatory (TEC), two out of three tested clamp-on electrical meters were found to have produced accurate readings at the currents we’d expect of residential blower fan motors. (The third one was >10% inaccurate when taking measurements <2 amps; however, the power accuracy specification in the meter manufacturer’s literature indicated there was no specification at that level.) The meter performance was compared to that of a laboratory-style benchtop power analyzer that electrical engineers would use.

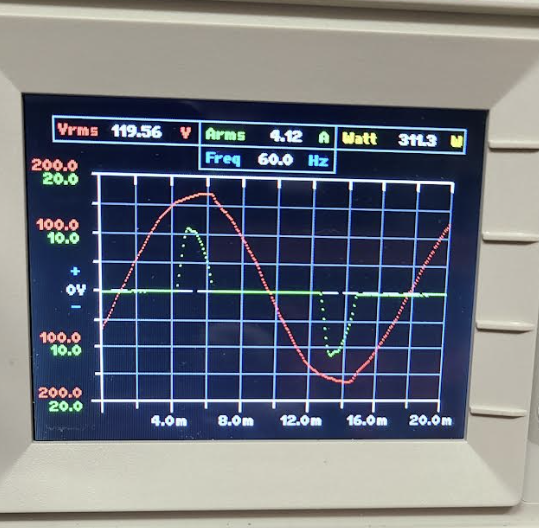
Credit: Steve Rogers (TEC)
You will need to pay attention to the accuracy specifications of any meter you intend to use, looking beyond the basic specs sheet and diving into the manual to see if it is adequate for what you intend to measure with it.
Taking ECM Blower Measurements Correctly
If you were to measure the amperage with your typical amp clamp (and possibly wattage with a fancy power quality meter), you’d notice a massive difference between a measurement with the air handler open and with it closed; the readings are a lot lower (and more favorable) with the door open. However, we can only get accurate measurements with the door closed.
The static pressure is a lot lower with the door open, and that doesn’t accurately represent operating conditions. When an energy rater comes in to evaluate the blower fan watt draw, they must take voltage and amperage readings at the same time, either at a junction box or with the meter installed inside the cabinet with the door on.
Amperage, Power Factor, and System Efficiency
ECMs have a lower power factor than PSC motors, and there is less power consumption when duct systems are designed properly.
PSC motors put out fewer CFM and draw less power when they have to overcome high static pressures. On the other hand, constant-airflow ECMs can ramp up to overcome high static pressure and maintain airflow, but they do so at a cost; they draw more power.
That’s why people may notice better sensible cooling and decreased dehumidification when replacing a PSC motor with an ECM. ECMs will ramp up to maintain a set airflow (and capacity by extension), but PSC motors will not. The slower airflow of a derated PSC motor will allow the evaporator to get cold and run for a long time, but the capacity and efficiency will take a hit.
ECMs are typically more efficient than PSC motors on the power consumption front up to roughly 0.8”w.c. That’s a threshold we should never reach in an ideal world where a system has been thoughtfully designed, installed, and commissioned. Alas, we don’t live in an ideal world. Technicians may wonder if the ECMs are running inefficiently when they’re actually trying to maintain a specific airflow rate in the face of bad ductwork.
Techs & Installers: Make the Most of the ECM
So, what’s the takeaway here for the average HVAC professional? Techs and installers are not energy raters and probably aren’t going to measure the watt draw on most of our ECMs, but they’re the ones who have a strong say in how well an ECM will work—how much wattage it will draw. They may also be the ones that need to fix the HVAC system if the builder doesn’t get their HERS points because the energy rater gives a failing grade on the blower fan watt draw test. It all comes down to keeping static pressure as low as possible in the ductwork so that the ECM has less resistance to airflow.
Tax credits for builders and homeowners are just a part of the equation; ECM longevity is also on the line. While a constant-airflow ECM will ramp up to overcome static pressure, it’ll draw more power to achieve that and won’t last as long. Then, it becomes a warranty issue or another expense that customers (and techs) probably don’t want to deal with.
ECMs’ low power factor isn’t a bad thing; it’s not like the occupant has to pay for the reactive power that isn’t being consumed. However, it’s the HVAC tech and installer’s due diligence to ensure that the ECM is set up for success and doesn’t draw more current than it needs due to poor system design or installation.
Comments
To leave a comment, you need to log in.
Log In