Get Tech Tips
Subscribe to free tech tips.
Why A/C Systems Freeze
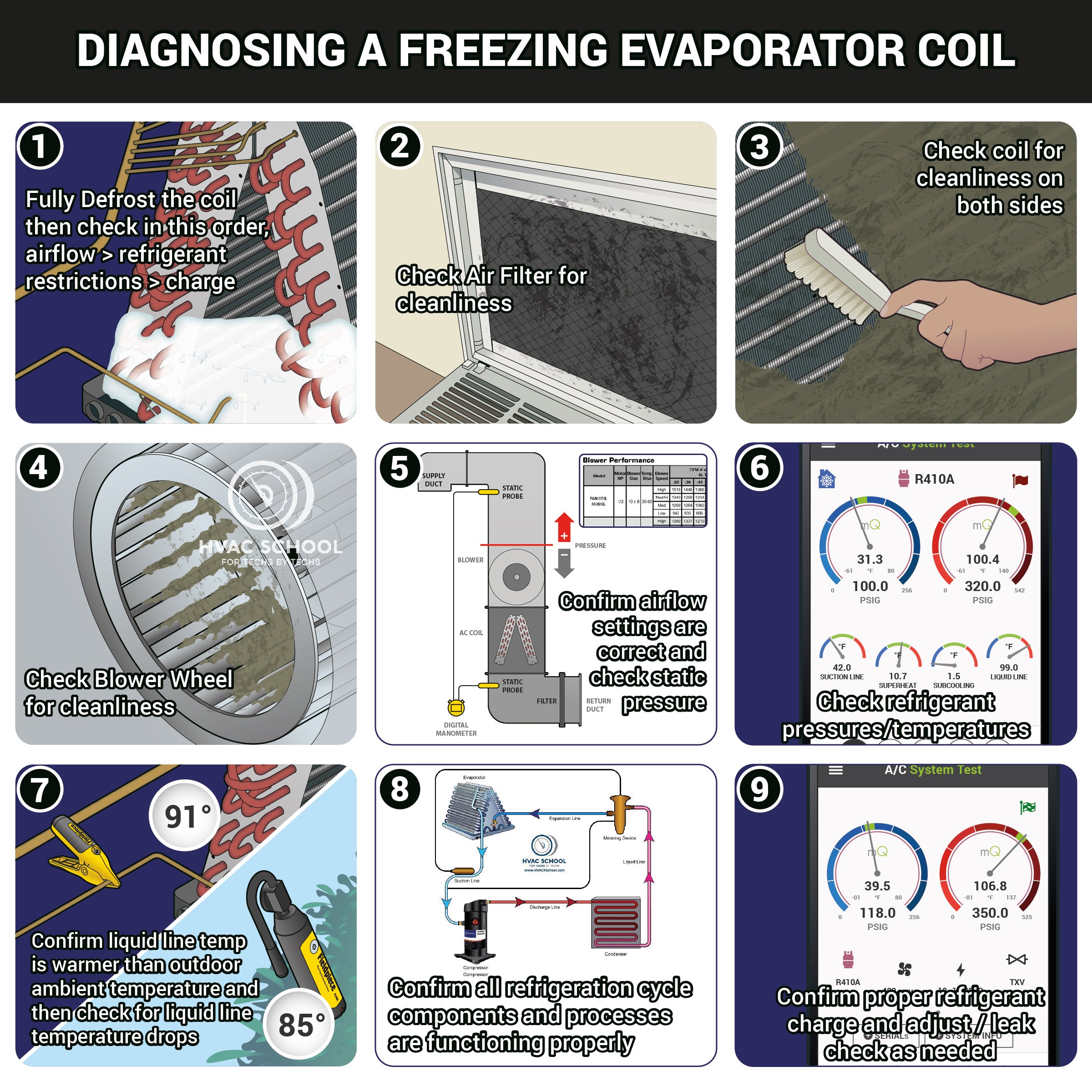
Let's start with the basics.
Water freezes at 32° Fahrenheit (0° Celsius) at sea level and at atmospheric pressure. When any surface is below that temperature, and the air around it contains moisture, ice/frost will form. You can see how water freezes at the molecular level in the GIF below:
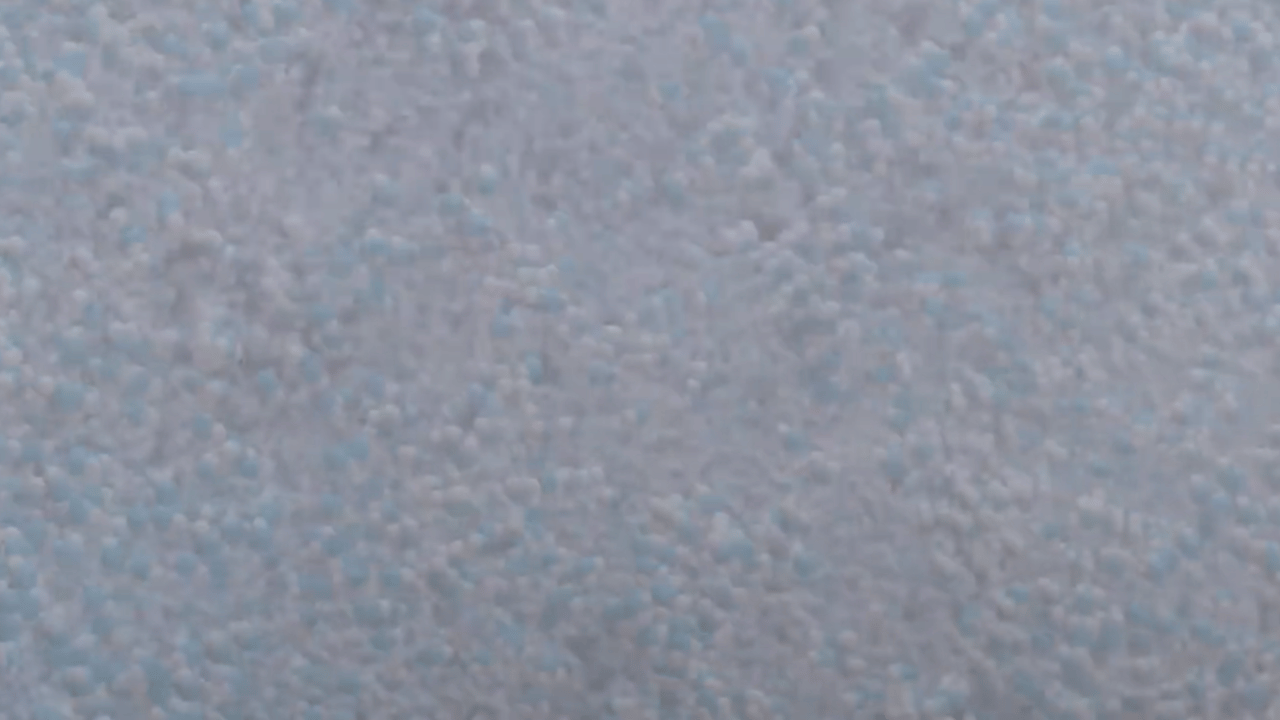
In some situations, ice is to be expected, such as in refrigeration evaporators and exposed portions of the refrigeration suction line and the metering device outlet in refrigeration applications. Frost and freezing are also likely in heat pumps operating in heat mode. The outdoor coil on a heat pump becomes the evaporator coil, and during low outdoor ambient conditions, it is expected that the outdoor coil will eventually freeze and require defrost. (Normal freezing will look like the photo below; completely ice-bound coils are NOT normal and indicate a problem.)
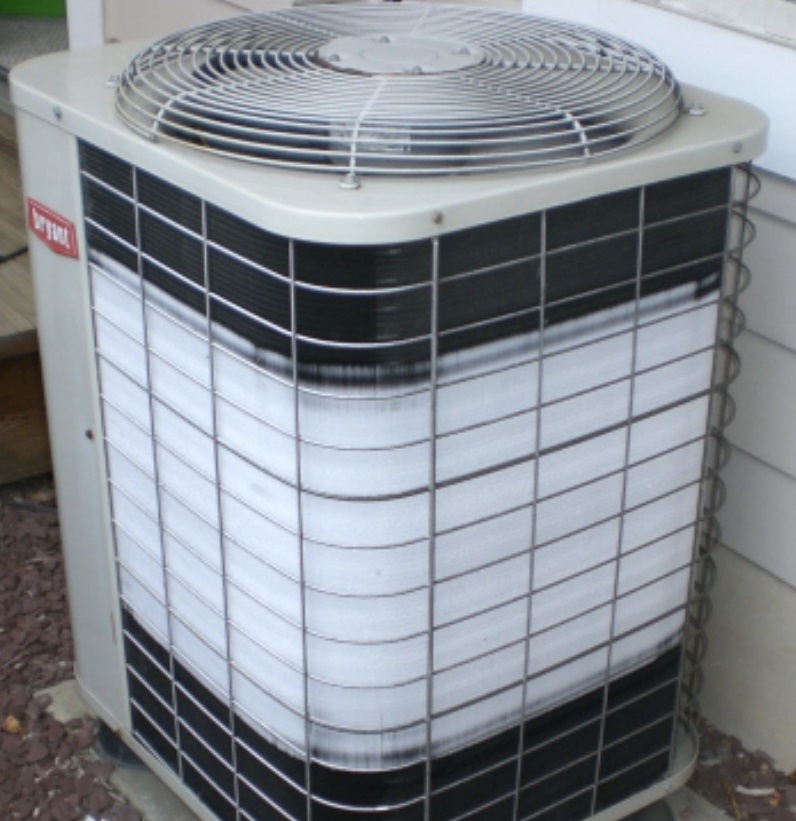
The reason that frost/ice is inevitable in some applications is just due to the laws of thermodynamics (moving heat). To get heat from one place to another, you need to have a temperature difference. So, inside a freezer where you hope to get the box temperature to 0°F, the coil temperature needs to be BELOW 0° to transfer heat out of the freezer and into the coil and then down the suction line to the compressor. If you have a freezer with a design coil temperature difference of 10° and a design superheat of 8°, the coil will be at -10°F, and the suction temperature at the evaporator outlet will be -2°F.
On a heat pump running in heat mode, you will commonly find an evaporator (outdoor coil) that runs 20°-30° colder than the outdoor temperature. That means that if it is 30°F outside, the outdoor coil temperature could easily be 0°F. In these cases, ice is normal, and periodic defrost is expected and required.
Some systems we work on and install will freeze. Straight-cool air conditioning is not one of them.
In an air conditioning system, we must keep the evaporator temperature above 32°F. We can easily know the evaporator temperature by looking at our suction saturation temperature (suction gauge temperature for the particular refrigerant). For R-22, 32°F is 57.73 PSIG at sea level, R-410a is 101.58 PSIG, R-454B is 91.1 PSIG, R-32 is 103.2 PSIG, and R407-C is 67.80 PSIG. If we don't keep our evaporator coils above these coil pressures/temperatures, the systems will freeze. The rate at which it will freeze is a function of:
- Time – The longer it runs at or below 32°, the more frost/ice will build.
- Moisture – The more humidity the air contains as it passes over the coil, the more frost/ice will form.
- Temperature Difference – The colder the coil, the faster ice will build.
- Air Velocity/Dwell Time – The faster the air moves over the coil, the slower ice will build; the slower it moves, the quicker it will build.
- Coil Design – Closer fins will freeze faster.
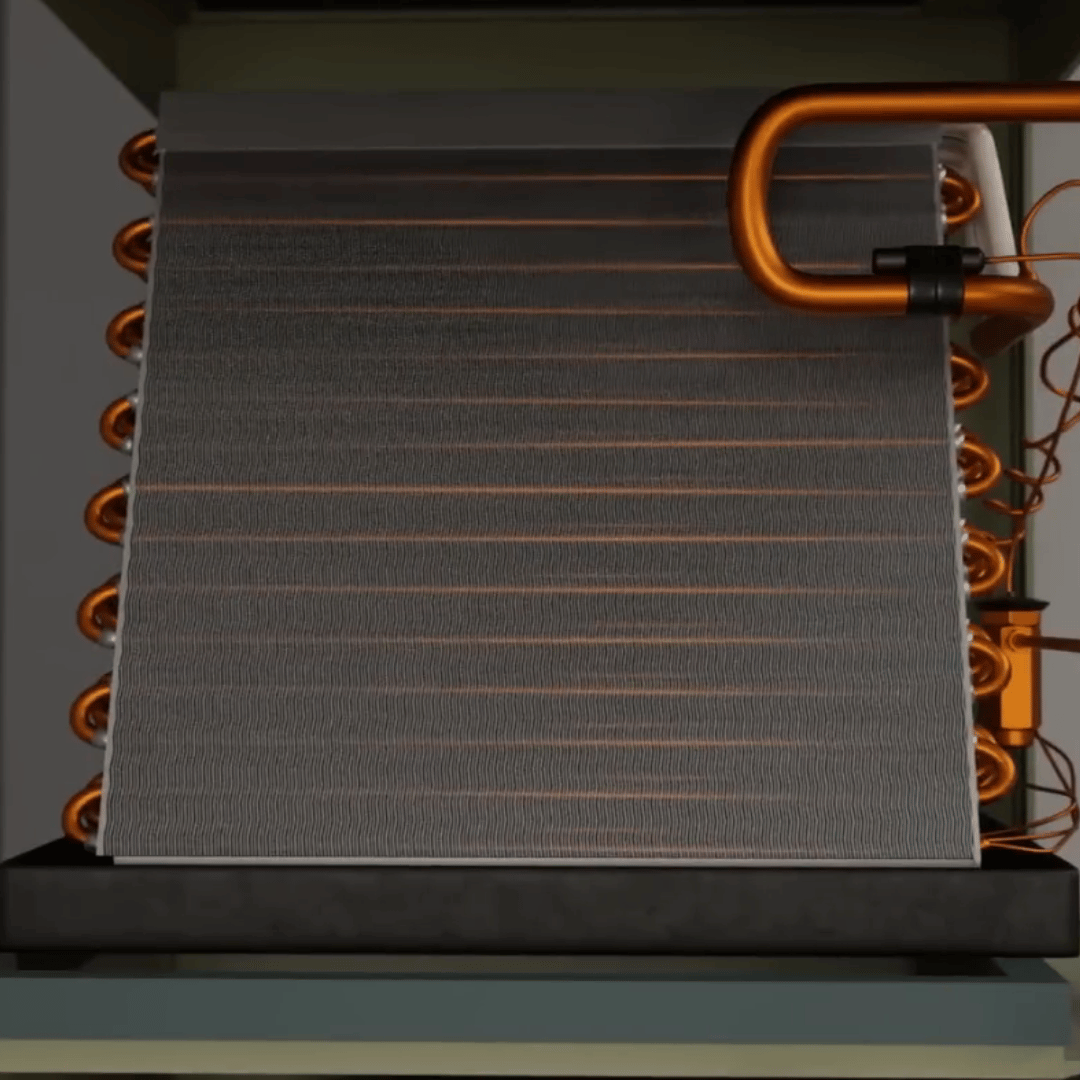
The ice buildup always starts in the evaporator and works its way outside. If you have a frozen compressor, you have a frozen evaporator. When you find a frozen system, take your time and get it fully defrosted. Take care to manage the ice meltwater and keep it away from motors and boards; it can cause damage and present a shock hazard. A shop vac and some towels are great to have handy when defrosting a unit. When possible, allow it to defrost slowly and naturally to prevent damage.
So, what circumstances can result in low coil temperature?
Low Evaporator Load
Low load is often equated with low airflow, and it usually is low airflow, but there is a bit more to the story than that.
An air conditioning system has one final design result, one big end goal that we are shooting for: matching the refrigeration effect to the evaporator load.
We must match the quantity of refrigerant moving through the evaporator coil to the amount of heat the evaporator coil is absorbing.
That is our mission, and that is the primary reason we measure superheat. Superheat gives us a look at how well we are matching refrigerant flow to heat load. High superheat means evaporator underfeeding; low superheat means overfeeding.
There is an issue, though. We could have a correct superheat and still have a coil temperature of under 32°—this is unacceptable in an air conditioning system. When the coil absorbs less heat than designed, the coil temperature and suction pressure will drop. In cases where a TXV or EEV controls suction superheat, the suction pressure will drop even further as the valve attempts to keep the superheat from plummeting.
This is why we must size a system and its ductwork appropriately for one another and the space, climate, and even the altitude. Suppose we install a system that requires 1200 CFM of airflow to properly balance the refrigeration effect to the load at 75° design indoor temperature, and that system is only receiving 900 CFM of airflow. Under those conditions, you run an excellent likelihood of freezing. This is especially true when the outdoor temperature drops or the customer drops the thermostat lower than usual.
Low load is often due to low airflow, low indoor ambient conditions, and equipment oversizing. Low load conditions will have symptoms of low suction pressure, low superheat, low head, and high evaporator delta T. Start by looking for the obvious: dirty coils, dirty filters, dirty blower wheels, blocked returns, mismatched equipment, improper blower settings, closed registers and undersized ducts. You can then move on to performing static pressure tests to locate more difficult issues.
Low load is the most common cause of persistent freezing and should be top of mind when a technician is diagnosing a freezing system.
Low Refrigerant In the Evaporator
System undercharge or underfeeding due to restricted refrigerant flow (restricted filter driers, plugged screens, failed expansion valves, or undersized pistons) can also result in freezing over time. Low refrigerant can result in fewer refrigerant molecules in the evaporator coil, which results in lower coil pressure because the coil contains saturated liquid at the beginning of the coil and superheated vapor towards the end. This type of freezing requires time because less refrigerant in the coil equals less refrigeration (cooling) effect.
If the coil temperature is below 32° in an undercharged situation, the coil will simultaneously build frost at the beginning of the coil after the metering device AND underfeed the coil, resulting in high superheat. As the frost builds over time, it will start to block the opening of the coil, which blocks airflow and insulates that portion of the coil from airflow, reducing the coil load. Eventually, once the coil is blocked with frost, almost all of the load is removed from the coil, and you have a low refrigerant issue that LED to a low load issue that resulted in a complete freeze up.
Once you defrost the system and test, you will find that low refrigerant charge conditions result in low suction, low subcool, high superheat, and low head pressure. Refrigerant restrictions will be low suction, high superheat, and high subcooling.
Often, once you resolve the charge issue, you may also find another low load issue that contributed to the freezing. In many cases, when a low charge is the main cause, the customer will notice the issue before the system is FROZEN SOLID.
Low refrigerant will often result in a partially frozen coil more than a full block of ice. Remember, low COIL refrigerant can be caused by restriction or low charge, but you will have low subcooling if it's a low charge. If it is a restriction, it will have high subcooling.
Low Outdoor Ambient
When a cooling system is operated during low outdoor temperatures, the condensing temperature and head pressure will drop. If the head pressure drops low enough, the suction pressure will also drop, resulting in freezing. The only way to resolve this cause is to install some type of head pressure control, such as fan cycling or fan speed control, to keep the head pressure from dropping significantly.
Blower Issues
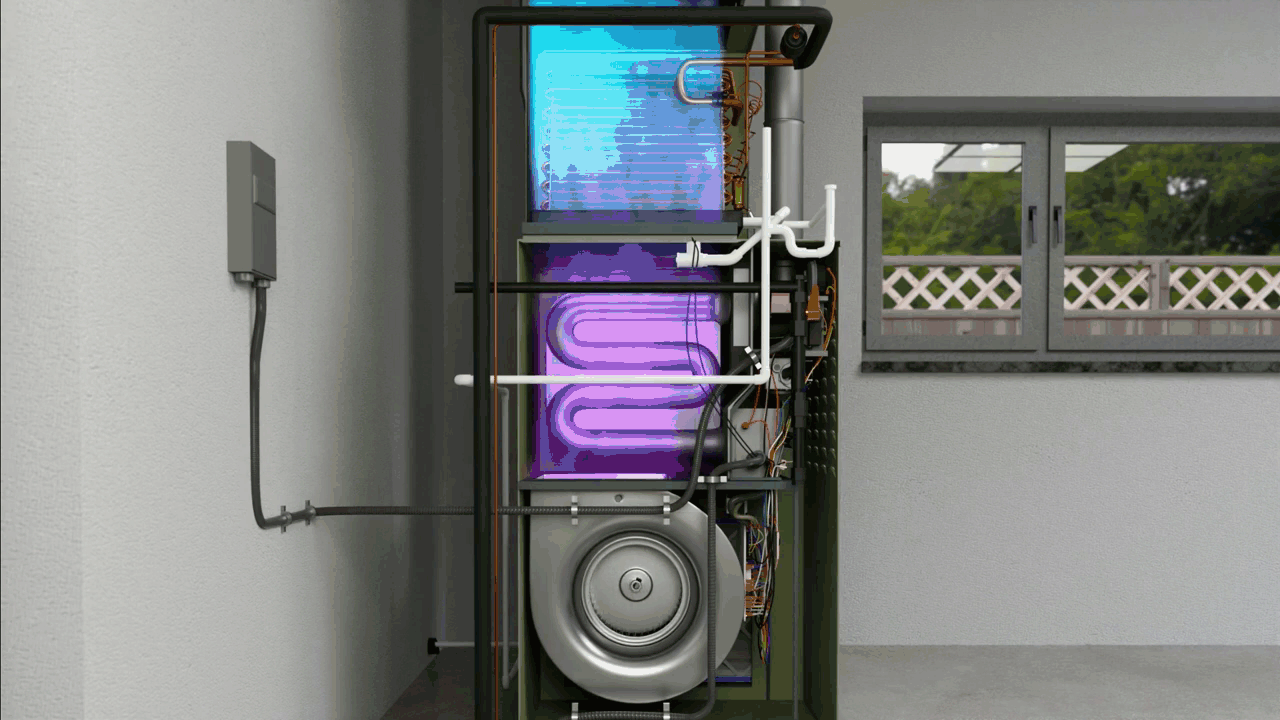
If the indoor blower shuts off, the coil temperature will drop. Sometimes, a blower motor will have internal issues or control issues that cause it to shut off periodically. This can cause intermittent freezing, which can be hard to diagnose. Checking controls, belts, blower amperage, bearings, and motor temperature can help diagnose these issues. Sometimes, leaving an amperage data logger on the motor along with a coil or supply air temperature sensor can give you the ammunition you need to pinpoint an intermittent issue.
When diagnosing a freezing situation, don't jump to conclusions; get all the ice defrosted before making a diagnosis, and keep a sharp eye out for airflow and design issues. Freezing is often due to multiple issues combined that act to turn your customer's air conditioner into an ice machine.
—Bryan
P.S. — We also have a 3D video about freezing in HVAC systems, which you can watch HERE.
Comments
Nice.thanks..👍
Nice.thanks..👍
It would be interesting to see a discussion on restrictions in the liquid circuit and how they relate to sub cooling and head pressure. Many techs assume a liquid restriction causes high head pressure (and high sub cooling) Most often these are a result of a previous visit during which the tech noted low suction pressure and added refrigerant before checking sub cooling.
It would be interesting to see a discussion on restrictions in the liquid circuit and how they relate to sub cooling and head pressure. Many techs assume a liquid restriction causes high head pressure (and high sub cooling) Most often these are a result of a previous visit during which the tech noted low suction pressure and added refrigerant before checking sub cooling.
Is Having 2 Liquid Line Dryers On A System Overkill?
Meaning That If The Condenser Unit Has A Liquid Factory Installed And You Add One Is That Over Kill?
Is Having 2 Liquid Line Dryers On A System Overkill?
Meaning That If The Condenser Unit Has A Liquid Factory Installed And You Add One Is That Over Kill?
Sorry for such basic question. i am brand new to this site. enjoy it lots.
can someone explain why the term saturation pressure/temp is used on a liquid line even though the refrigerant may not be saturated at the moment the liquid line is being inspected?
how do we know the gas has been heated, pressure elevated, cooled and so condensed ?
drives me nuts not knowing this. i am sure there is a fundamental and extremely key point here and i am missing it.
example, how high can we allow pressure to get in a condenser/high side, per refrigerant blend and know we are condensing well?
i understand touching coils, feeling balance of u-bends, looking for even temp from top to bottom. there has to be more:)
Sorry for such basic question. i am brand new to this site. enjoy it lots.
can someone explain why the term saturation pressure/temp is used on a liquid line even though the refrigerant may not be saturated at the moment the liquid line is being inspected?
how do we know the gas has been heated, pressure elevated, cooled and so condensed ?
drives me nuts not knowing this. i am sure there is a fundamental and extremely key point here and i am missing it.
example, how high can we allow pressure to get in a condenser/high side, per refrigerant blend and know we are condensing well?
i understand touching coils, feeling balance of u-bends, looking for even temp from top to bottom. there has to be more:)
Good question. Because of subcooling wouldn’t the high side pressure at the liquid service port be slightly lower than where the refrigerant is saturated?
Good question. Because of subcooling wouldn’t the high side pressure at the liquid service port be slightly lower than where the refrigerant is saturated?
Achetez vos kamagra medicaments [url=https://kamagraprix.shop/#]kamagra gel[/url] achat kamagra
Achetez vos kamagra medicaments [url=https://kamagraprix.shop/#]kamagra gel[/url] achat kamagra
Acheter Cialis 20 mg pas cher: Acheter Viagra Cialis sans ordonnance – Cialis en ligne tadalmed.shop
Acheter Cialis 20 mg pas cher: Acheter Viagra Cialis sans ordonnance – Cialis en ligne tadalmed.shop
https://kamagraprix.com/# Kamagra Commander maintenant
https://kamagraprix.com/# Kamagra Commander maintenant
olympe casino en ligne: olympe casino cresus – olympe casino
olympe casino en ligne: olympe casino cresus – olympe casino
But there’s no demand for you to stress over dating Colombian women, as long as you have the appropriate perspective and an excellent set of dating suggestions in hand. Although you’re not going to move Latinas off their feet by taking them to a lavish day, it still pays to have a little additional cash simply in situation. Latinas are very loyal to their partners. If you are interested, you can always look for more details concerning it heard. They can be helpful lovers and can also train you a great deal about their practices. After a year of dating about in London, I think it is safe to state that the communication skills of the average mid-twenties Anglo-Saxon male have a great deal of room for improvement. And after your day, constantly use to accompany her on her way home to see to it she’s secure. We also make use of both the complimentary and paid variation of each app for numerous months to make informed suggestions.
⤠ColombiaLady. A Latin dating app that offers a variety of communication tools, exciting attributes like sending actual flowers, and insightful accounts of girls online. Width of ladies’s Latin dance shoes. Whether you’re hopeless for some cha-cha and merengue to wow your visitors or samba or bossa nova to bring a new degree of energy to your occasion, contact us today to inquire about our talented dance professionals. Despite where your day is mosting likely to happen, you’re still mosting likely to need to spend a buck or 2. Still, I don’t advise mosting likely to such places as a first, date, for the factors I stated early. Of program, this can be an instead harmful date for an initial date, but if you seem like the various other side is comfortable with you, she could like the idea. You can offer to pick her up prior to your day or fulfill someplace hassle-free so that she will not have problem mosting likely to where your date is supposed to take location. It is something that fits people that such as to enjoy, and appreciate the concept of going out, taking the sunlight, dancing, playing loud songs while cleaning and being extremely acquainted.
Due to the fact that online chat and video clip chatting have actually ended up being much more prominent, not everyone is using the email solution. Think about the immediate video clip calls function as an upgrade to the Chat function. While many people believe attracting a Latina expense of mail order bride-to-be female is tricky, it’s no unattainable. I do not believe the “-e” need to eliminate the existing “-o” and the “-a.” Instead, it can be a grammatically acceptable addition to the Spanish language. Along with this, they likewise love charming and an exceptional feel. You have to make a great impact prior to you stress regarding earning her love and love. We love to enjoy our good friends. Solitary latin girls net dating is a superb way to meet women that are searching for a major enchanting relationship. We specialize in discovering that best Latin lady for you! I am separated catholic latino woman with children from Quebec, Quebec, Canada. We are [url=https://medium.com/@toniadamsusa/latamdate-review-my-impressions-after-three-months-of-use-0dde913fb1bd]latamdate scam[/url] functioning 7 days a week to maintain all the info approximately day and besides that obtaining to recognize even more women. Unlike their younger counterparts, grown-up latina people are responsible parents who’ve already developed themselves monetarily.
Distort up since dating a Latina implies going into the world of romance. To start, remember that the beginning of dating a Latina are one of the most vital, which implies that the very first day is very vital. That’s just how you’ll be making a connection nevertheless; by determining your compatibility based on how your very first day ends up. Apart from your cultural distinctions, you’ll be amazed to know that Latinas are extremely friendly and at times relatable. The initial point to remember is that Latinas are really loved ones- oriented and enthusiastic ladies. “The finest thing in your life is escaping your hands,” she sings. And it’s constantly best to foot the bill on your initial day to reveal that you’re familiarized with the dating culture well sufficient. Just outfit clever to reveal your date that you are actually eagerly anticipating investing a wonderful evening with her. Merely be the finest version of on your own to reveal her just how sincere you are. Nonetheless, there are specific requirements that a lot of the day go unfilled since of either temperament or traditions.
But there’s no demand for you to stress over dating Colombian women, as long as you have the appropriate perspective and an excellent set of dating suggestions in hand. Although you’re not going to move Latinas off their feet by taking them to a lavish day, it still pays to have a little additional cash simply in situation. Latinas are very loyal to their partners. If you are interested, you can always look for more details concerning it heard. They can be helpful lovers and can also train you a great deal about their practices. After a year of dating about in London, I think it is safe to state that the communication skills of the average mid-twenties Anglo-Saxon male have a great deal of room for improvement. And after your day, constantly use to accompany her on her way home to see to it she’s secure. We also make use of both the complimentary and paid variation of each app for numerous months to make informed suggestions.
⤠ColombiaLady. A Latin dating app that offers a variety of communication tools, exciting attributes like sending actual flowers, and insightful accounts of girls online. Width of ladies’s Latin dance shoes. Whether you’re hopeless for some cha-cha and merengue to wow your visitors or samba or bossa nova to bring a new degree of energy to your occasion, contact us today to inquire about our talented dance professionals. Despite where your day is mosting likely to happen, you’re still mosting likely to need to spend a buck or 2. Still, I don’t advise mosting likely to such places as a first, date, for the factors I stated early. Of program, this can be an instead harmful date for an initial date, but if you seem like the various other side is comfortable with you, she could like the idea. You can offer to pick her up prior to your day or fulfill someplace hassle-free so that she will not have problem mosting likely to where your date is supposed to take location. It is something that fits people that such as to enjoy, and appreciate the concept of going out, taking the sunlight, dancing, playing loud songs while cleaning and being extremely acquainted.
Due to the fact that online chat and video clip chatting have actually ended up being much more prominent, not everyone is using the email solution. Think about the immediate video clip calls function as an upgrade to the Chat function. While many people believe attracting a Latina expense of mail order bride-to-be female is tricky, it’s no unattainable. I do not believe the “-e” need to eliminate the existing “-o” and the “-a.” Instead, it can be a grammatically acceptable addition to the Spanish language. Along with this, they likewise love charming and an exceptional feel. You have to make a great impact prior to you stress regarding earning her love and love. We love to enjoy our good friends. Solitary latin girls net dating is a superb way to meet women that are searching for a major enchanting relationship. We specialize in discovering that best Latin lady for you! I am separated catholic latino woman with children from Quebec, Quebec, Canada. We are [url=https://medium.com/@toniadamsusa/latamdate-review-my-impressions-after-three-months-of-use-0dde913fb1bd]latamdate scam[/url] functioning 7 days a week to maintain all the info approximately day and besides that obtaining to recognize even more women. Unlike their younger counterparts, grown-up latina people are responsible parents who’ve already developed themselves monetarily.
Distort up since dating a Latina implies going into the world of romance. To start, remember that the beginning of dating a Latina are one of the most vital, which implies that the very first day is very vital. That’s just how you’ll be making a connection nevertheless; by determining your compatibility based on how your very first day ends up. Apart from your cultural distinctions, you’ll be amazed to know that Latinas are extremely friendly and at times relatable. The initial point to remember is that Latinas are really loved ones- oriented and enthusiastic ladies. “The finest thing in your life is escaping your hands,” she sings. And it’s constantly best to foot the bill on your initial day to reveal that you’re familiarized with the dating culture well sufficient. Just outfit clever to reveal your date that you are actually eagerly anticipating investing a wonderful evening with her. Merely be the finest version of on your own to reveal her just how sincere you are. Nonetheless, there are specific requirements that a lot of the day go unfilled since of either temperament or traditions.
To leave a comment, you need to log in.
Log In