BACK
What Should My Subcooling Be?
Flash Gas
Know the Limits of Subcooling
The “5 Pillars” of Residential A/C Refrigerant Circuit Diagnosis
Subcool and Liquid Line Length
Setting a Refrigerant Charge by Subcool
Condensing Temperature, Condenser Split, and Subcool
The 5 Readings Every Tech Must Know Well
#subcool
Tech Tips:

This is the article you read BEFORE you call and ask a senior tech what your subcooling should be. It's also the one you send to a junior tech when they call and ask you: So, what is subcooling? (Or subcool, as many call it.) Subcooling is a measurement of the temperature DECREASE of a […]
Read more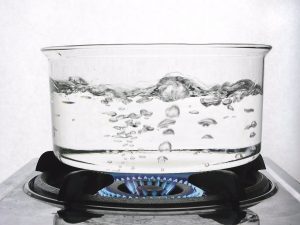
When we say that there is “flash gas” at a particular point in the system, it can either be a bad thing or a good thing, depending on where it is occurring. Flash gas is just another term for boiling. It is perfectly normal (and required) that refrigerant “flashes” or begins boiling directly after the […]
Read more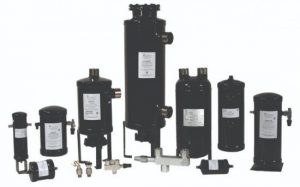
This article was written by RSES CM and excellent market refrigeration tech Jeremy Smith. Thanks, Jeremy! I frequently see techs online struggling with charging or troubleshooting refrigeration equipment and using subcooling as a diagnostic or charging method. Please don't do this unless you understand it fully. Many times, trying to charge a refrigeration system to […]
Read more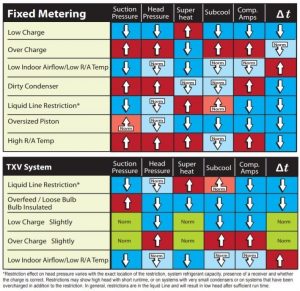
Suction pressure, head pressure, subcooling, superheat, delta T. Taking all five of these calculations into account on every service call is critical. Even if you must do further diagnostic tests to pinpoint the problem, these five factors are the groundwork before more effective diagnostics can be done. I would also add static pressure as an […]
Read more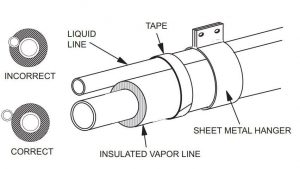
The primary role of setting an appropriate level of subcooling is to ensure that we deliver a full line of liquid refrigerant to the metering device. We want to do this at: A pressure differential required by the metering device At a temperature and pressure no higher than required for maximum capacity and efficiency But […]
Read moreVideos:
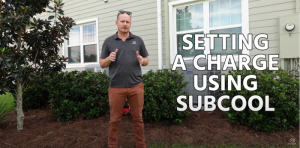
Bryan demonstrates an in-depth tutorial on how to set a refrigerant charge by Subcool.
Read morePodcasts:
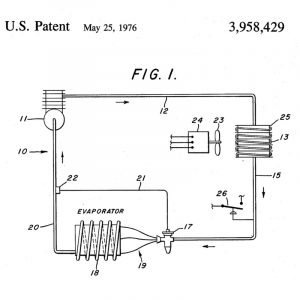
In this podcast, Bryan talks about condensing temperature, condenser split, and subcooling. All three of the values are proportional. If one changes, all three of them will change. Saturation is also a critical concept that relates to all three of those, so we also cover those relationships. As you remember, a condenser rejects heat and […]
Read more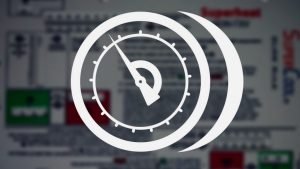
In this episode of HVAC School, Bryan covers the “5 pillars of refrigerant circuit diagnosis” and why they matter. They are: Superheat Subcool Suction pressure Head pressure Air temp split (delta T) These 5 readings give you a holistic idea of the A/C system. Instead of getting hooked on checking only superheat and subcool […]
Read more