BACK
3 Things to Check When the Unit Won’t Keep Up
Drain Trap Depth and Negative Pressure
Static Pressure, Manometers, and Magnehelics
Making Duct Systems Work
Replacing Residential HVAC Equipment With “Predictable Results”
Manual D Speedsheet Walkthrough
Why Measuring Static First Isn’t Always Productive
Use Static Pressure Responsibly
Static Pressure – Why Measure It?
Static Mistakes – Short #232
Q&A – Drain Traps & Static – Short #209
Measuring Airflow Podcasts w/ Jim Bergmann
#static pressure
Tech Tips:
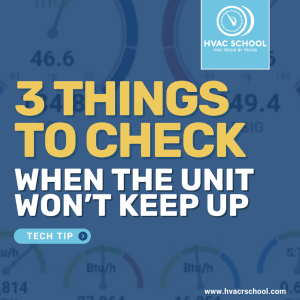
What is your methodology for troubleshooting an HVAC system that “can’t keep up” on the hottest days of the summer? Let me walk you through my process and hone in on one or two ideas that have been overlooked for too long in our industry. In this article, I’m assuming we have ruled out intermittent […]
Read more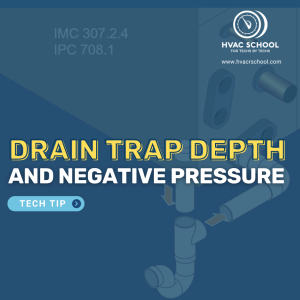
We recently received a Speakpipe question for the podcast about a common nuisance call on straight-cool A/C units and heat pumps. The systems, often retrofit units, were backing water up into the secondary drain pan and overflowing it. This issue isn’t happening on furnaces, which are positively pressurized, which means we have to take a […]
Read more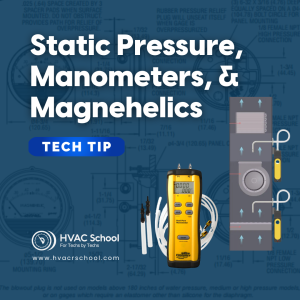
When you start talking airflow, it can get pretty in-depth pretty quickly. There is a big gap between what is useful for the average tech to apply every day and the whole story, so let's start with the simplest part to understand: static pressure. Static pressure is simply the force exerted in all directions within […]
Read more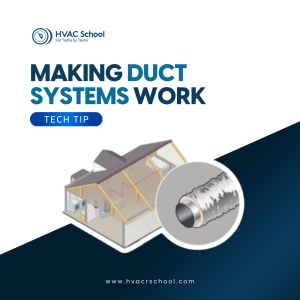
This tech tip recaps the livestream by the same name, featuring HVAC School contributors Matt Bruner and Adam Mufich, as well as special guests Ed Janowiak and David Richardson. You can watch that live stream on our YouTube channel HERE. It’s one thing to install a piece of equipment, but it’s another thing entirely to […]
Read more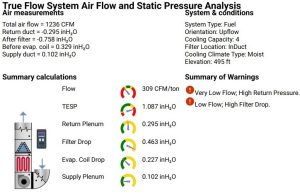
When replacing a furnace or air handler for a customer, there is nothing worse than starting up the equipment and having it sound like the latest SpaceX rocket taking off. You insert your static pressure probes into the duct, and your stomach drops as you read the numbers. You realize the new high-end system you’ve […]
Read more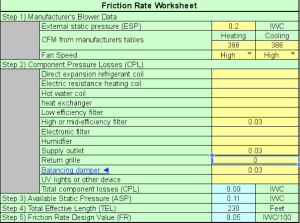
Bryan recently released a podcast on rules of thumb and how they can really get us in a pickle with sizing ductwork. With that in mind, I thought this might be a good time to do a walkthrough of Manual D from start to finish on a project I just finished up. My good friend […]
Read more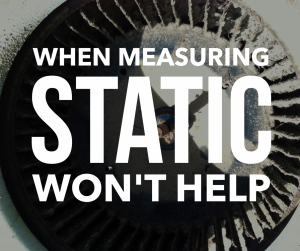
There is a big move in residential and light commercial HVAC toward measuring static pressure regularly during commissioning, service, and maintenance. Don't get me wrong… Measuring static pressure is VERY important. The challenge comes in when techs begin taking measurements without understanding where to take them, what they mean, or worse: they use measurements as […]
Read more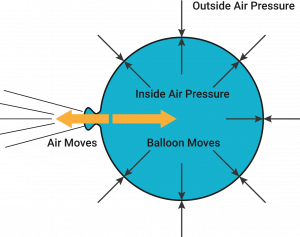
The topic of static pressure comes up frequently in HVAC, and it’s sometimes presented as a test that can be all-knowing and insightful about what is happening with regard to airflow in a system. To use static pressure responsibly, we need to understand what it really is and what it means for an HVAC system. […]
Read more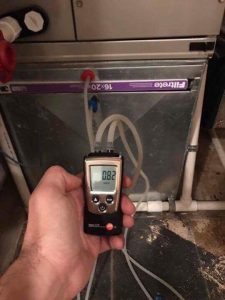
This article was written by Neil Comparetto. Neil is one of the smartest and most thoughtful techs I know online. Thanks, Neil. Why measure static pressure? Because it's fun. I enjoy drilling holes in things. I rarely leave a house without drilling a hole in something. I also believe it’s an essential step to commissioning […]
Read moreVideos:
Podcasts:
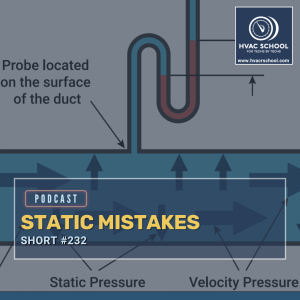
In this short podcast episode, Bryan covers some common mistakes when measuring static pressure. Static pressure is balloon pressure, not CFM or velocity pressure, but it can be an airflow indicator. The best way to start learning about static pressure is to start measuring total external static pressure. Gas furnaces and heat pumps are […]
Read more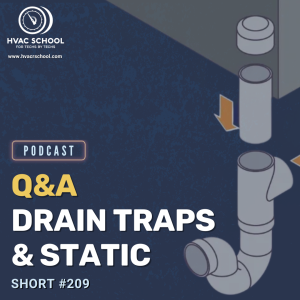
In this short Q&A podcast episode, Bryan answers a question about drain traps and static pressure. This question was sent by Stephen with The Comfort Squad when he noticed an uptick in nuisance calls on retrofit systems that kept having their secondary drain pans filled. In negatively pressurized systems (i.e., straight-cool or heat pump […]
Read more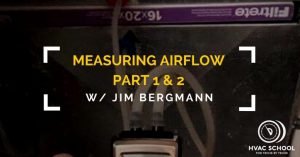
In this two-part podcast series, Jim Bergmann covers measuring airflow in HVAC systems. He covers a wide range of airflow measurement instrumentation and readings. In the HVAC industry, many techs confuse static pressure for airflow. Although you need static pressure to have airflow, it is NOT airflow and can fluctuate rather wildly depending on the […]
Read more