BACK
Refrigerant Charging Basics For Air Conditioning & Heat Pump Systems
R-454B vs. R-410A Side by Side
New A2L Refrigerants – “Easy as ABC”
One Way to Picture Superheat and Subcool
Weighing Refrigerant In and Out
Retrofitting Existing R-404A/R-507A Systems
Crankcase Heaters
Refrigerant Basics
Electronic Leak Detection
Setting a Refrigerant Charge by Subcool
What’s up with Refrigerant & System Regulations w/ Copeland
Preventing Slugging & Flooding w/ Copeland
Manufacturer Responsibility – Manifesto
A2L Update With Chemours Live from AHR
What Is A2L Mitigation Going To Look Like? W/ Clifton B.
The 5 Readings Every Tech Must Know Well
#refrigerant
Tech Tips:
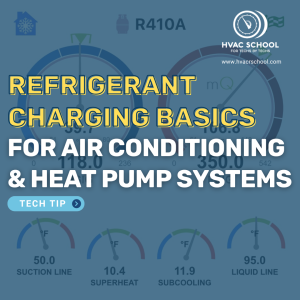
Before I start on this one… At HVAC School, we focus on a wide range of topics. Many of them are very basic. My experience as a trainer for over 20 years has taught me that no matter what I assume others SHOULD know, it doesn't change the fact that they often do not. This […]
Read more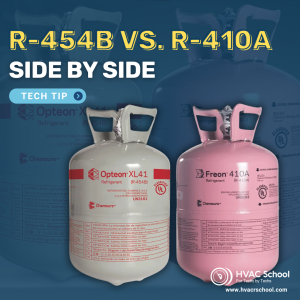
This tech tip was written by Dr. Chuck Allgood from Chemours. Thanks, Dr. Chuck! As the ramp-up of new AC units and heat pumps with low-GWP refrigerant R-454B accelerates, it may be useful to look at some of the basic properties of R-454B refrigerant as compared to the legacy gas it’s replacing: R-410A. This tech tip […]
Read more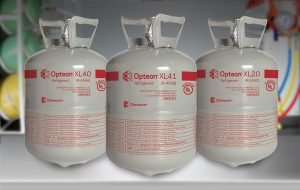
This tech tip was written by Dr. Chuck Allgood with Chemours. Thanks, Dr. Chuck! While the ever-evolving world of refrigerants can often seem overwhelming with what seems like a never-ending parade of new gases being developed, taking a simplified approach may help clear the clutter. It can be as easy as A, B, C—that is, […]
Read more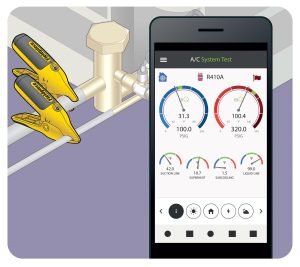
It took me years to build a picture in my head of what superheat and subcool mean. They were these strange words that dropped out of nowhere when I entered the HVAC world, and in the midst of grappling with so many other things, I could tell they were very important. Over time, I have, […]
Read more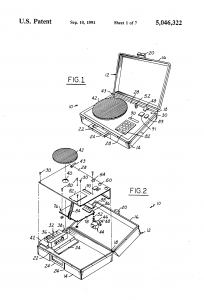
If you don't use a scale every time you add or remove refrigerant, I suggest you begin doing so immediately, if not sooner. Weighing in while charging is fairly obvious, and it's useful so you can keep track of what you are using and how much to charge a customer. When you have a system […]
Read more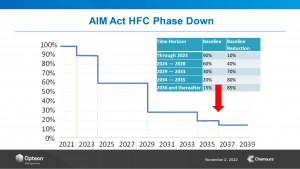
This article was written by Don Gillis with Chemours. Thanks, Don! With the American Innovation Act (The AIM Act) in place and the reduction of the supply of hydrofluorocarbons (HFCs) in effect, the need to retrofit systems with lower global warming potential (GWP) refrigerants will become commonplace in the very near future. So, what does […]
Read more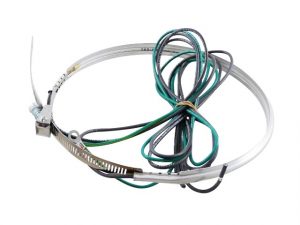
Belly band crankcase heater When I first started in the trade as an apprentice, we worked on many Trane heat pumps that used crankcase heaters. These crankcase heaters slid into the compressor sump on the big orange Tyler reciprocating compressors. They looked like the one in the picture below. It was very common for these […]
Read more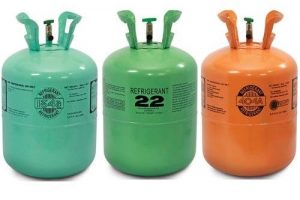
A refrigerant is anything we use to move heat from one place to another using the compression refrigeration circuit. However, the history of refrigerants and the different kinds is quite diverse and interesting. Have you ever noticed how your skin feels cool after you apply some rubbing alcohol to it? For a long time, scientists […]
Read more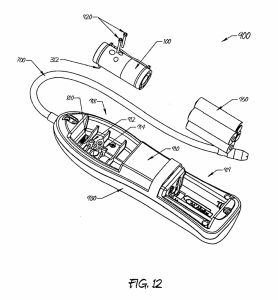
Electronic leak detection is a critical part of any HVAC technician's common practice. Unfortunately, it is also one of the most common sources of misdiagnosis. Here are my tips to make your leak detection more successful: Use Your Senses First and Your Detector Second Before starting to use your detector, STOP! Look for signs of […]
Read moreVideos:
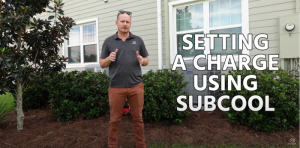
Bryan demonstrates an in-depth tutorial on how to set a refrigerant charge by Subcool.
Read morePodcasts:
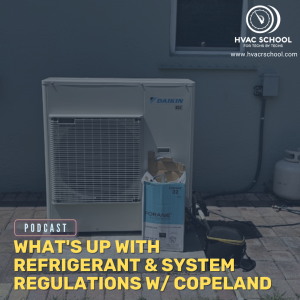
In this insightful episode of the HVAC School podcast, host Bryan sits down with Jennifer Butsch, Director of Regulatory Affairs at Copeland, to discuss the rapidly evolving regulatory environment affecting the HVAC industry. With eight years of experience at Copeland and a background spanning codes, standards, and regulatory affairs, Jennifer provides a unique perspective […]
Read more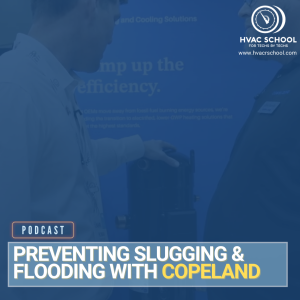
In this episode of the HVAC School Podcast, host Bryan welcomes Jeff from Copeland to discuss the critical topic of flooding and slugging in compressors. Jeff, calling in from frigid Minnesota (at negative 19°F), explains the differences between these harmful conditions and how they can damage compressor systems. The conversation begins by differentiating between […]
Read more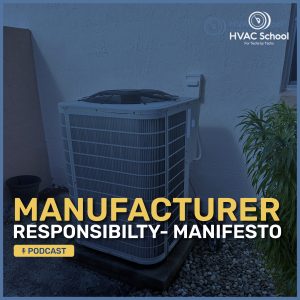
In this episode of the HVAC School podcast, Bryan shares his “Manufacturer Responsibility Manifesto,” a document he wrote over two years ago but held back from publishing until now. The manifesto addresses growing concerns about the burden being placed on HVAC contractors, particularly smaller businesses, due to manufacturing quality issues and warranty policies. The […]
Read more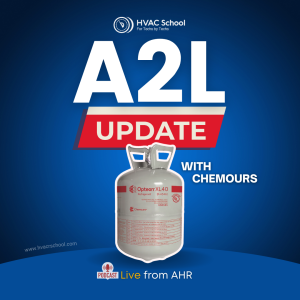
Don Gillis and Dr. Chuck Allgood from Chemours join the show to discuss their new easy as “1,2,3” branding around the A2L refrigerants R454A, R454B, and R454C. They explain that A2Ls are not actually flammable like hydrocarbons; they are just mildly combustible with much lower burning velocity and energy than propane or butane. The […]
Read more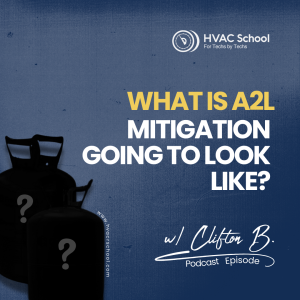
In this podcast, Bryan and Clifton discuss the upcoming transition to A2L refrigerants, like R-32 and R-454B, and what A2L mitigation is going to look like. These mildly flammable refrigerants will be used in place of R-410A for residential air conditioning systems due to an HFC phase-down driven by legislation and international agreements. They […]
Read more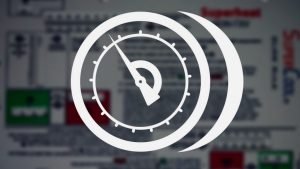
In this episode of HVAC School, Bryan covers the “5 pillars of refrigerant circuit diagnosis” and why they matter. They are: Superheat Subcool Suction pressure Head pressure Air temp split (delta T) These 5 readings give you a holistic idea of the A/C system. Instead of getting hooked on checking only superheat and subcool […]
Read more