BACK
Inches of Water Column
Gas Pool Heater Components and Common Issues
The Case for Buying a Combustion Analyzer
Combustion Air
Combustion and Confined Spaces
Flame Sensing – The Basics
Some Furnace Questions
Testing a Thermocouple
Condensate Drainage in a High Efficiency Gas Furnace
Preparing Non-Techs for a Southern Winter
#gas
Tech Tips:

Low pressures are often measured in inches of water column or “WC. Like most units of measure, it has a very simple origin; in a water manometer, 1″ of water column is literally the amount of force it takes to raise the column of water by 1”. While some water manometers (water tubes) are still […]
Read more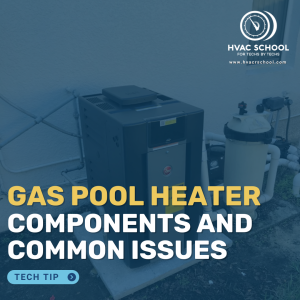
I know, I know. You came here for HVAC content, so why are we talking about pool heaters? Since we live in Florida and don’t have that much of a heating season, we have to look for other forms of work during the winter months. Pool heaters fit the bill quite nicely since they’re actually […]
Read more
Last year, I bought my first combustion analyzer. I had just started my own company and felt the additional weight of responsibility to sit down and determine the best way to verify that the furnaces I was servicing were working safely. In the past, the most extensive testing I had done was a visual inspection […]
Read more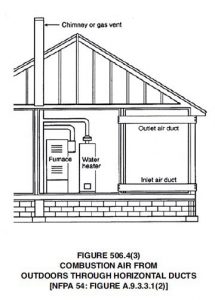
To maintain combustion (burning), you need three things: fuel, heat, and oxygen. If you have all three in the proper proportion, you can maintain a continuous state of combustion. Remove one (or reduce one sufficiently), and the triangle of combustion can collapse. In a common natural gas (NG) furnace, the heat is the igniter, the […]
Read more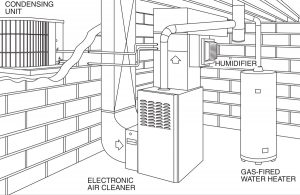
All fuel-burning appliances require oxygen to burn. They require sufficient oxygen to burn clean and safely, without soot and CO (carbon monoxide). I live and work in Florida, where most of our fuel-burning appliances are 80% efficient with open combustion. (You can learn more about the basics of combustion on a podcast with Benoit Mongeau.) […]
Read more
Proving flame is an important part of the gas firing sequence. Without proof of flame, you risk dumping unspent gas into the heat exchanger, resulting in an explosion. There are many ways to “prove flame,” but we are focusing on the flame sensing rod (flame rectification) method here. Here are the facts: Flame sensing rods, […]
Read more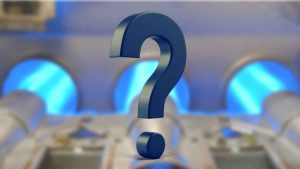
I received an email from a podcast listener with some furnace-related questions. Based on the nature of the questions, I figured it would be better to ask an experienced furnace tech. Benoît Mongeau agreed to help by answering the questions. My name is Matt and I am a newer tech (fully licensed this September, have […]
Read more
First, a thermocouple is not a flame rectifier like a modern flame sensor. A thermocouple actually generates a millivolt potential difference when it is heated by a flame—just to get that out of the way for any of you newer techs who are used to modern flame sensors. With higher efficiency gas-fired equipment being the […]
Read more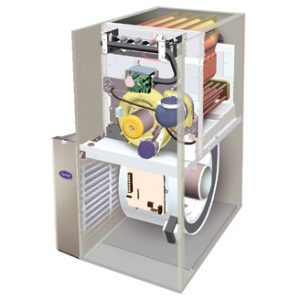
This article was written by HVAC/furnace technician Benoît Mongeau. Thank you, Ben. High efficiency (or 90%, or condensing) furnaces use a set of two heat exchangers to retrieve more heat from the combustion products than their mid-efficiency counterparts. Because of this, they generate flue gases much colder than those of a mid-efficiency or […]
Read morePodcasts:
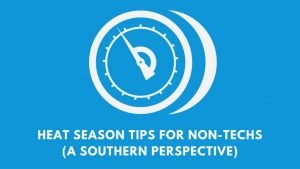
Central Florida techs know the Southern winter all too well. Let's face it. It doesn't get super cold here regularly, but when it does, EVERYONE FREAKS. We get an abundance of service calls for unpleasant but not truly problematic conditions when people use their heaters. When people first turn on their heat, they can get […]
Read more