BACK
Why A/C Systems Freeze
Two Ways to Prevent Freezing in 90%+ Furnace Condensate Lines
Does Setpoint Lead to Freezing?
Can Pulling a Vacuum too Fast Freeze Water/Moisture?
Water Issues – Spidey Sense
Why A/C Units Freeze w/ Eric Shidell (Podcast)
#freezing
Tech Tips:
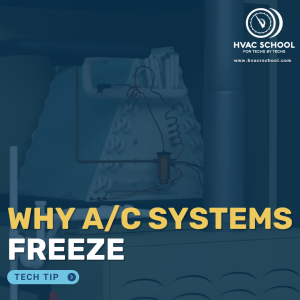
Let's start with the basics. Water freezes at 32° Fahrenheit (0° Celsius) at sea level and at atmospheric pressure. When any surface is below that temperature, and the air around it contains moisture, ice/frost will form. You can see how water freezes at the molecular level in the GIF below: In some situations, ice […]
Read more
This tech tip came from an email sent by Adam Blunkall, a Tennessee-based HVAC technician. He shared some tips to help overcome this issue in his market, and we appreciate his insight. Thanks, Adam! If we’re draining our 90% furnaces (or any condensing heating system) outside the structure in a similar fashion as we would […]
Read more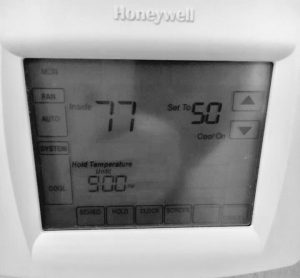
Does setting a thermostat too low cause an air conditioning system set in cool mode to freeze? The answer is no, at least not directly. However, low evaporator load (low return temperature or low airflow) and low outdoor ambient temperature can lead to evaporator coil freezing. Low indoor setpoint can lead to low return air […]
Read more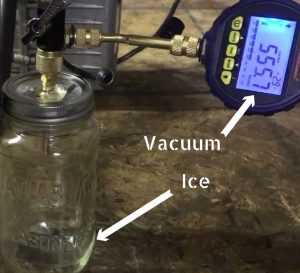
First, I want to give credit where credit is due. This post is made possible by the fantastic demonstration video by Neil Comparetto that I embedded below. Before you get bored and stop reading, I want to get the conclusion out in the air. Ice can form in a vacuum, but I still advise pulling a […]
Read morePodcasts:
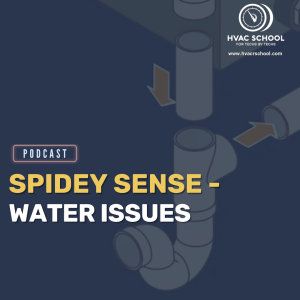
This episode of the HVAC School podcast dives deep into the often-overlooked but critical topic of water issues in HVAC systems. Bryan and Bert discuss the various causes of water leaks and condensation problems, and they explain how to prevent them. They emphasize that water damage is not an inevitable part of HVAC systems […]
Read more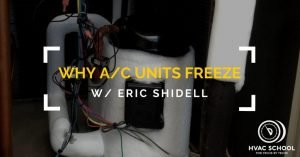
In this episode, Bryan speaks with Eric Shidell about some of the basics of system freezing, what causes it, and what to do about it. Freezing is a normal part of some equipment, such as low-temperature freezers and outdoor units on heat pumps. On straight-cooling systems, freezing is NOT normal and indicates poor operation. Ice […]
Read more