BACK
3 Things to Check When the Unit Won’t Keep Up
Make Plenum Pressures Work for You
The One Duct Leak You Didn’t Expect
When Ducts Get Too Big
Making Duct Systems Work
Manual J Field Data: Ducts
Sizing Return Grilles
Plenum Takeoffs Best Practices
The Ten Duct Commandments (Plus a Few More)
Reading CFM and Duct Velocity with a Testo 510i, the Smart Probe app and a Pitot Tube
Duct Cleaning – How Long & How Often?
Can Ducts Be Cleaned Ethically?
Should I Fog or “Sanitize” My Ducts? – Short #220
A Duct Up Situation
Friction Rate. Why the Fuss? (WTF)
#duct
Tech Tips:
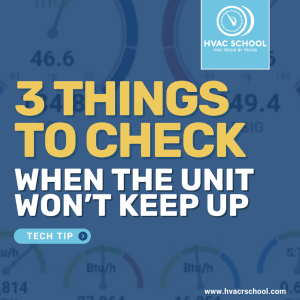
What is your methodology for troubleshooting an HVAC system that “can’t keep up” on the hottest days of the summer? Let me walk you through my process and hone in on one or two ideas that have been overlooked for too long in our industry. In this article, I’m assuming we have ruled out intermittent […]
Read more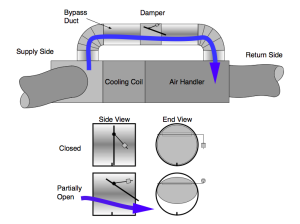
There are several neighborhoods in my area with two—and three-story townhomes with zoning, and I always wonder how long those systems will survive. Zoning can be notoriously hard on HVAC equipment if not set up properly. A single-stage system running full tilt with half the airflow it was designed for because a zone is closed […]
Read more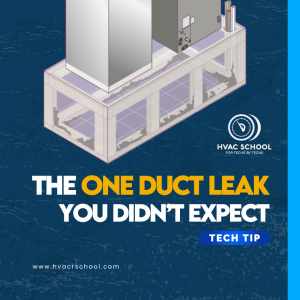
Sometimes, you just get lucky. Sometimes, you get sent out to install a unit in a closet! Although these types of installs have their challenges, at least for me, they have appeared easier on the surface. There is no return ductwork, as the unit sits on a platform. We are rarely disconnecting ducts in the […]
Read more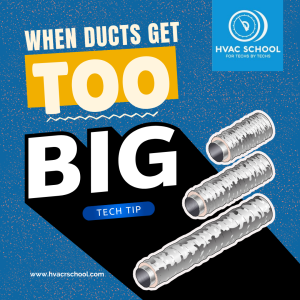
This tech tip recaps the livestream by the same name, featuring HVAC School contributors Matt Bruner and Adam Mufich, as well as special guests Russ King, Steve Rogers, and Tony Amadio. You can watch that live stream on our YouTube channel HERE. It was a beautiful day outside. The sun was shining, the birds were […]
Read more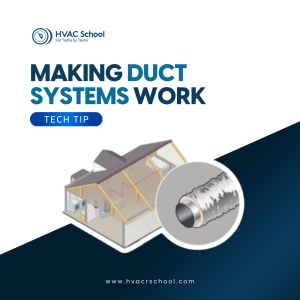
This tech tip recaps the livestream by the same name, featuring HVAC School contributors Matt Bruner and Adam Mufich, as well as special guests Ed Janowiak and David Richardson. You can watch that live stream on our YouTube channel HERE. It’s one thing to install a piece of equipment, but it’s another thing entirely to […]
Read more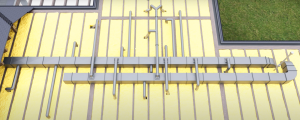
Understanding the relationships between ductwork, home comfort, and the load on a house is a complicated and dynamic problem. There are a large number of variables. Some of the data is fairly straightforward, like the other elements of field data collection we have covered so far in this series. Ductwork has different levels of insulation […]
Read more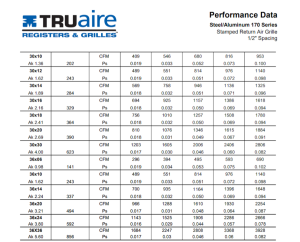
A few weeks ago, I spent several days redoing a duct system and replacing a furnace for a friend. I had static pressure readings from before the system was replaced, and with the new furnace that I had picked out, I had created a static pressure budget and felt confident I could significantly lower the […]
Read more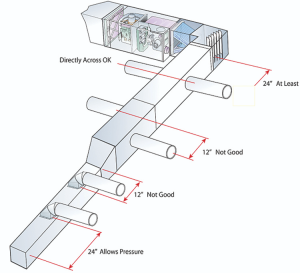
In my second year in HVAC, I went out with a senior technician to install a supply duct for a bathroom in a house. While he ran the duct, I cut a hole in the plenum and attached the collar. He crawled back across the attic and very nicely told me that people don’t typically […]
Read more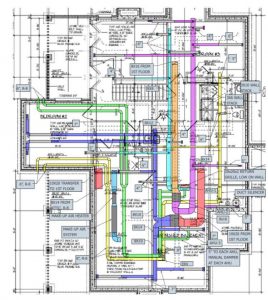
This article was written by my good friend, Neil Comparetto. He is one of the all-around best dudes in the industry and a guy who practices what he preaches on duct design. Thanks, Neil! These are some fundamentals for designing and installing duct systems that I’ve learned over the years. Included are links to […]
Read moreVideos:
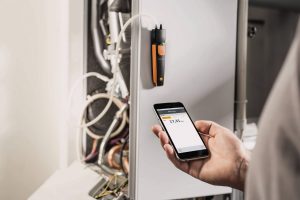
Reading CFM and Duct Velocity In this video, we cover the basics of using the Testo 510i with a pitot tube to do a duct traverse and easily calculate Velocity in FPM and volume in CFM on a small 8″ duct. Using this method is handy because you can use the reliable, accurate and inexpensive […]
Read morePodcasts:
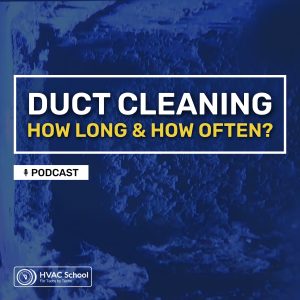
In this episode of the HVAC School podcast, Bryan interviews Zach from Southeast Clean Air Solutions about the intricacies of professional duct cleaning. Zach specializes in addressing duct cleaning challenges specific to the Southeastern climate, with a particular focus on fiberglass-lined ducts. The conversation delves into the complexities of cleaning different types of duct […]
Read more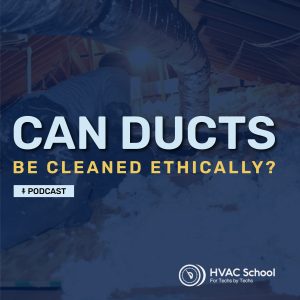
In this episode of the HVAC School Podcast, Bryan interviews Zachary Ortwine, a duct cleaning professional who provides insights into ethical duct cleaning practices. The conversation delves deep into the complexities of cleaning different types of ductwork, the importance of proper assessment, and the potential challenges in maintaining indoor air quality. Zach emphasizes the […]
Read more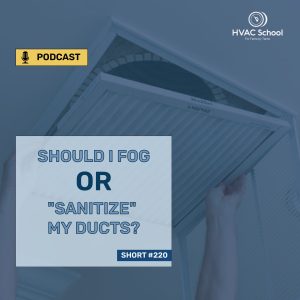
In this short podcast episode, Zach joins Bryan to answer a common duct maintenance question: Should I fog or sanitize my ducts? The National Air Duct Cleaners Association (NADCA) outlines the uses of chemical products. Adding chemicals is usually a last resort in flex or sheet metal (externally wrapped) duct systems; they should NOT […]
Read moreEvents:
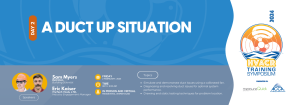
NOTE: If you cannot view the recording, the video may still be processing. The maximum wait time is 24 hours. We apologize for the delay and appreciate your patience.
Read more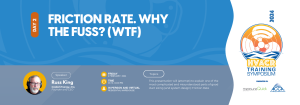
NOTE: If you cannot view the recording, the video may still be processing. The maximum wait time is 24 hours. We apologize for the delay and appreciate your patience.
Read more