All Videos
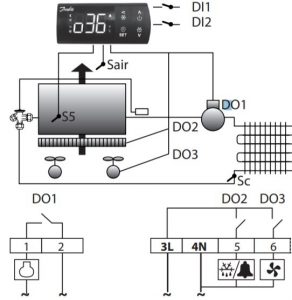
I was talking about dry contacts with one of my techs, and he looked at me like I had three heads—and one of them was on fire. So, I figured it would be good to cover the difference between wet and dry contacts in a tech tip. Basically, “dry” contacts are switches with no shared […]
Read more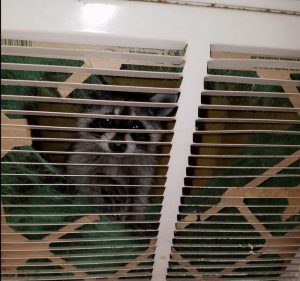
Today's tech tip is a video put out by my friend Brad Hicks from the HVAC in SC YouTube Channel. Thanks, Brad! Seal boots to prevent raccoon leaks. Ok, this has nothing to do with raccoons, but I like that photo. Whenever you are installing duct boxes (also called boots or cans) in an aftermarket […]
Read more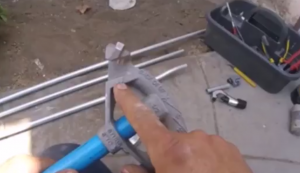
I was about 13 years old the first time I bent EMT with my uncle. We were doing a renovation at a church; watching him bend EMT and then getting to do it MYSELF was a truly religious experience. There are a few things in the trade where workmanship really comes into play, such as […]
Read more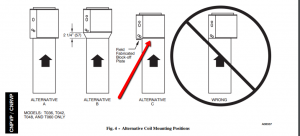
On occasion you will either find a furnace or be tasked with installing a furnace where the coil overlaps the edge of the furnace because the coil is wider. In the case of a Carrier CNPVP coil you need to ensure that you align the coil according to manufactures specs or you risk cutting off […]
Read more
I hear many techs complain about the finicky and ineffective nature of electronic leak detection. So much so that some claim that it is a waste of time altogether. We recently located a leak inside the fins of a ductless evaporator coil—pinpointed to an exact spot—using an electronic leak detector. For demonstration purposes, we took […]
Read more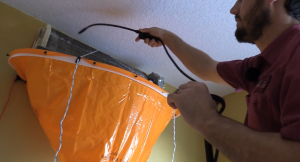
Cleaning ductless systems is critical… and a pain.. Rather than just telling you how we do it let me show you some of the key points. This video demonstrates cleaning and testing a ductless system including pulling the blower wheel and washing the evaporator with a bib kit. I also wrote a process for […]
Read more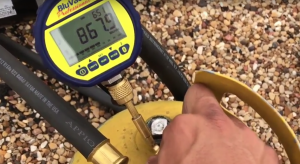
As a technician gains skill they will learn that regularly testing your tools is a huge part of success. It isn't long in the field before techs find out that just because a meter or gauge gives a particular reading it doesn't ALWAYS mean it is correct. Vacuum is one of these areas. Everything in an […]
Read more
Evacuation Start to finish with some of the best evacuation practices. Click below to see the video. –Bryan
Read more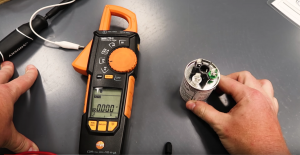
I got a lot of comments that many of you discharge run capacitors with a voltmeter. I test this method vs. the capacitor discharge tool I created. Obviously, many of you use needle nose pliers or a screwdriver. While this is widely practiced, it could result in an arc, shock, or damage to the capacitor. […]
Read more