January 2021
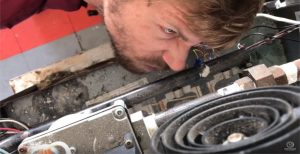
This article is an extension of HVAC School’s “How to Measure Gas Pressure” video. Additional input was provided by Jim Bergmann. Bubble test procedures and standards were provided by Honeywell. Links to source materials are available at the end of this article. If there’s one complaint that HVAC techs should never take lightly, it’s a […]
Read more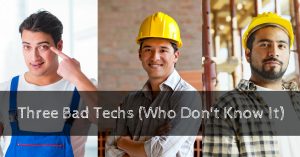
First, let's state the obvious and clear the air a bit. The photo above is SUPER CHEESY! But this story is about three bad techs who don't know it, so a photo of three models clearly posing in clean clothes makes as good of a proxy for a bad tech as anything else. First off, I'm […]
Read more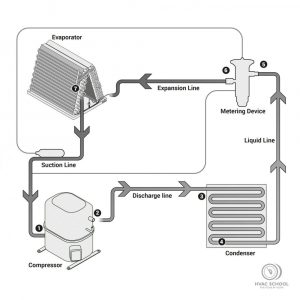
Many in our industry can misunderstand the differences between temperature and heat, although these are related. Substances are composed of many moving molecules that change their speed as they release or gain heat. When we heat a glass of water in a microwave, its molecules start to move more quickly. The velocity increase results in […]
Read more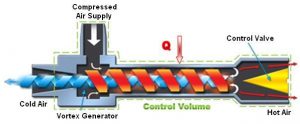
We just wrote about rejecting heat to the atmosphere via radiant cooling. That’s one example of cooling without refrigerants, but there are quite a few others out there. In this article, we’ll look at some other cooling methods that don’t use refrigerants. Vortex tubes Vortex tubes swirl gas in a chamber, separating it into hot […]
Read more