February 2019
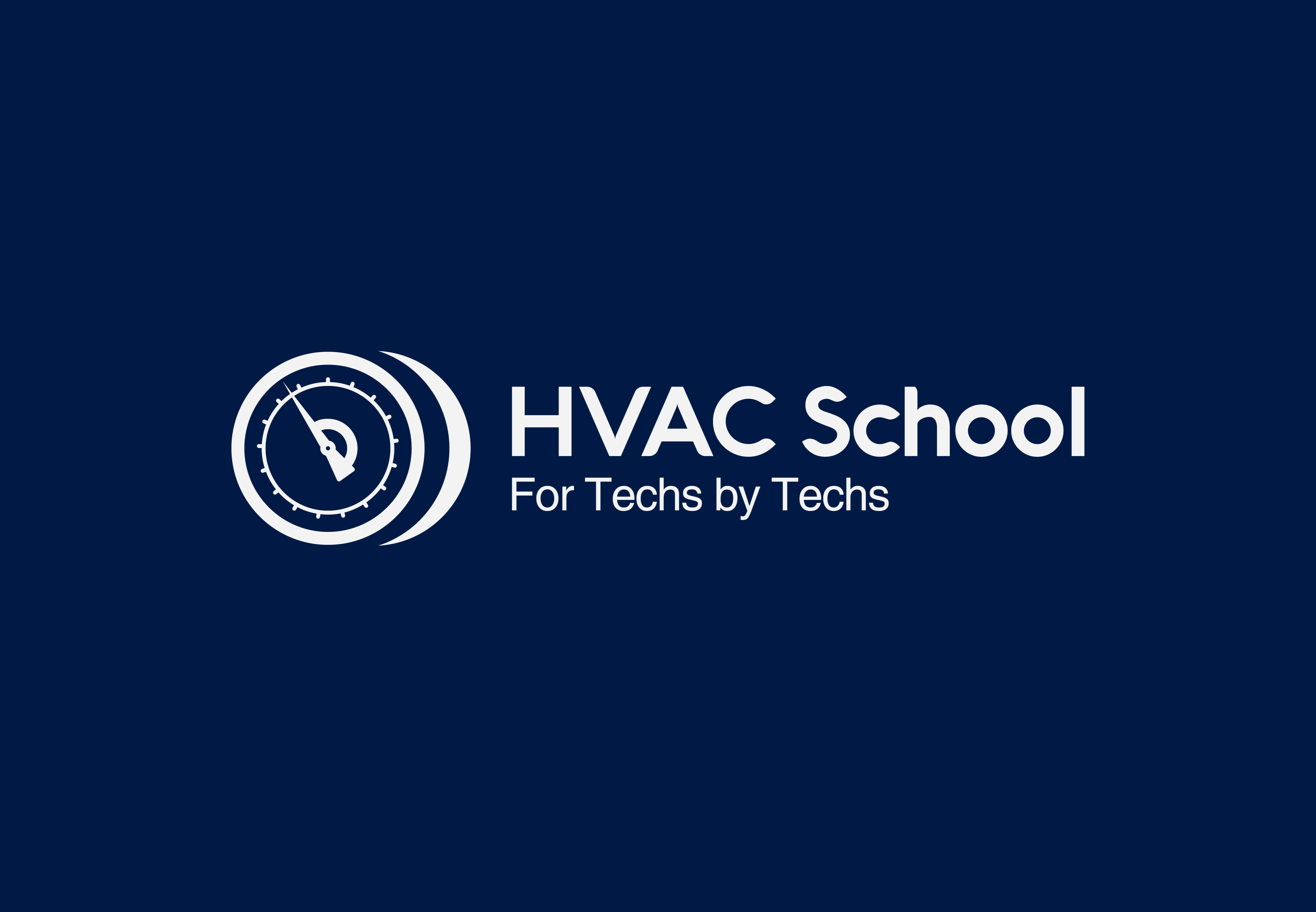
Mark from Goodway talks about chiller and cooling tower cleaning best practices and techniques
Read more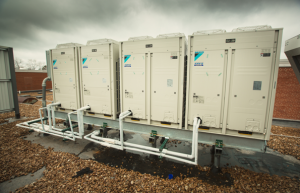
This tech tip is written by experienced tech and VRF / VRV specialist Ryan Findley. Thanks, Ryan! (Note: Ryan refers to VRV rather than VRF because he specializes in Daikin, and these articles are written from a Daikin VRV perspective. Ryan has also written an article about VRV basics and some VRV installation tips.) This […]
Read more
Remote Ice Machines Why would someone want to take an already complicated machine and make it even more complicated? The answer: human arrogance and engineer's hubris. (Just kidding.) Fortunately, thousands of these ice machines have been installed and serviced. Let's take a little overview of a few of the critical differences and things to consider […]
Read more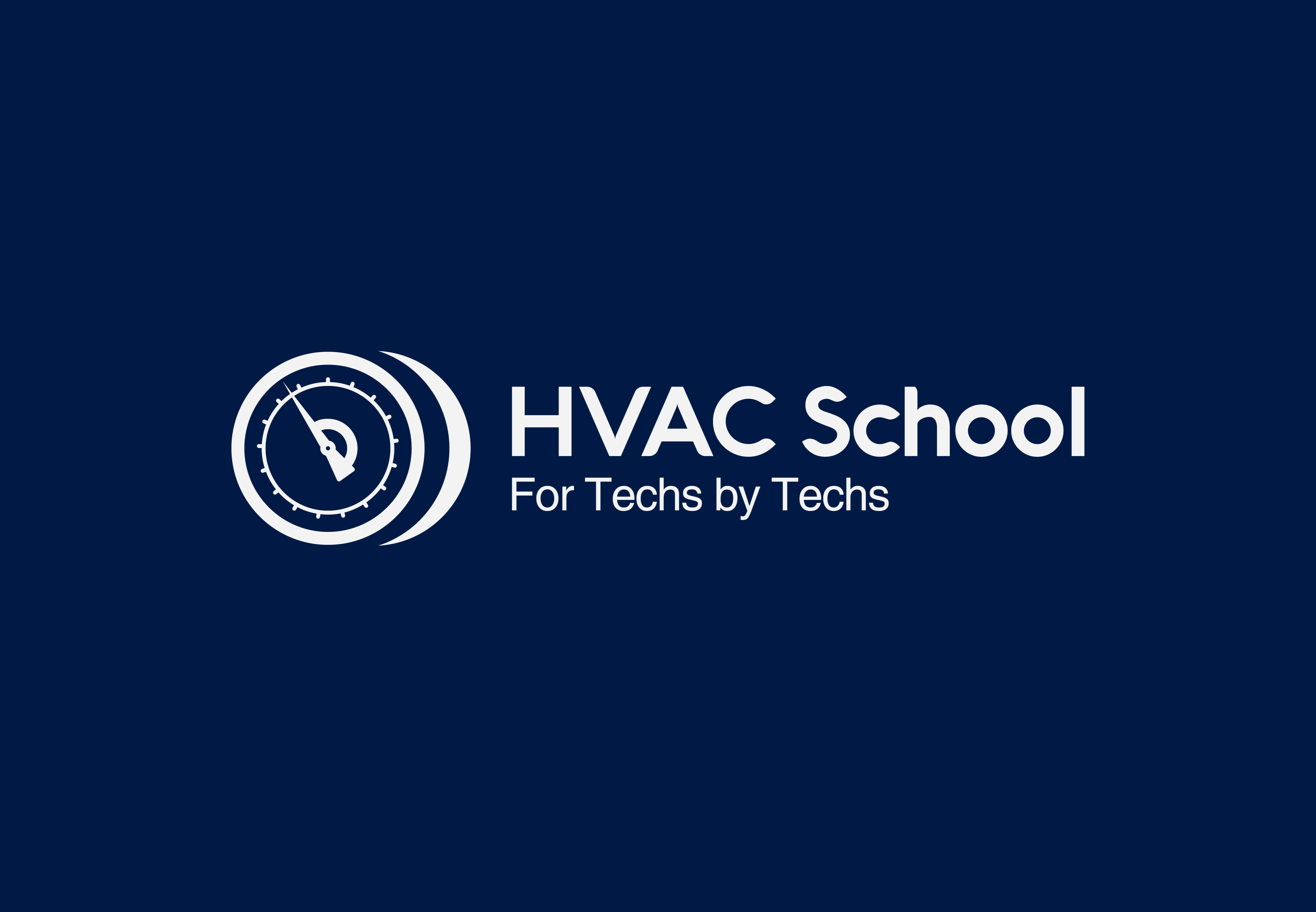
In this episode we address the myth that IAQ is a joke and how to think about IAQ correctly
Read more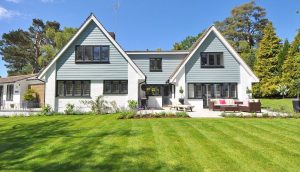
How an A/C System got to be Oversized (Maybe) But My Old Unit Worked Fine?! Most of us have heard this at some point. This complaint typically comes from a particularly unhappy customer after the installation of a brand new A/C system. Throughout this article, we’re going to explore the possible root causes of this […]
Read more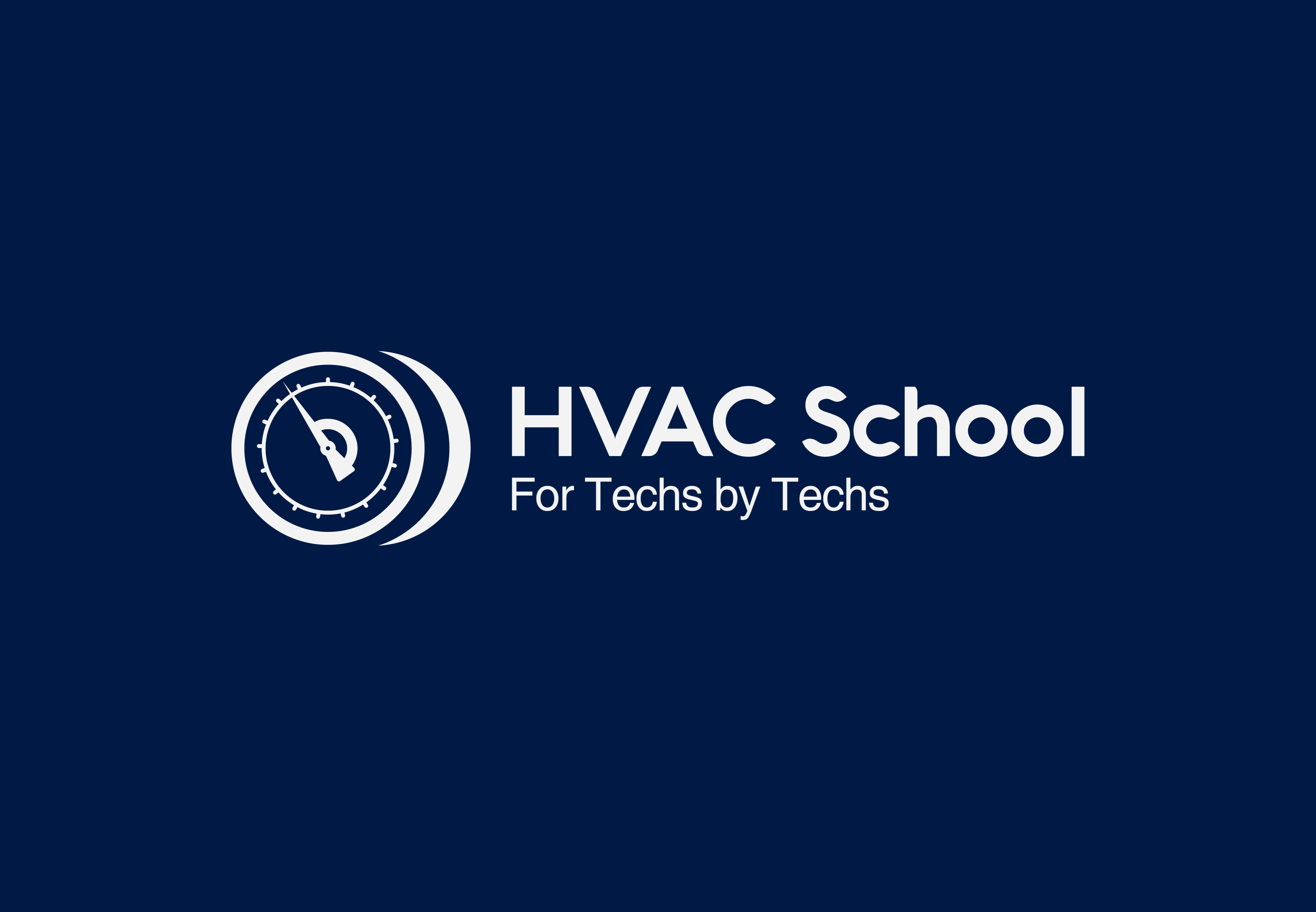
Chris Stephens from HVACR Videos joins us to talk about his experiences with and perspective on R290 (propane) refrigerant in restaraunt refrigeration
Read more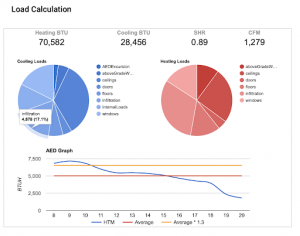
This article was written by HVAC contractor and Building Science Whiz, Michael Housh. Thanks, Michael! For a while, I’ve fallen into this camp where I feel Manual J overshoots heating loads. First off, I would like to say that Manual J is only as good as the information you give it, but we often run […]
Read more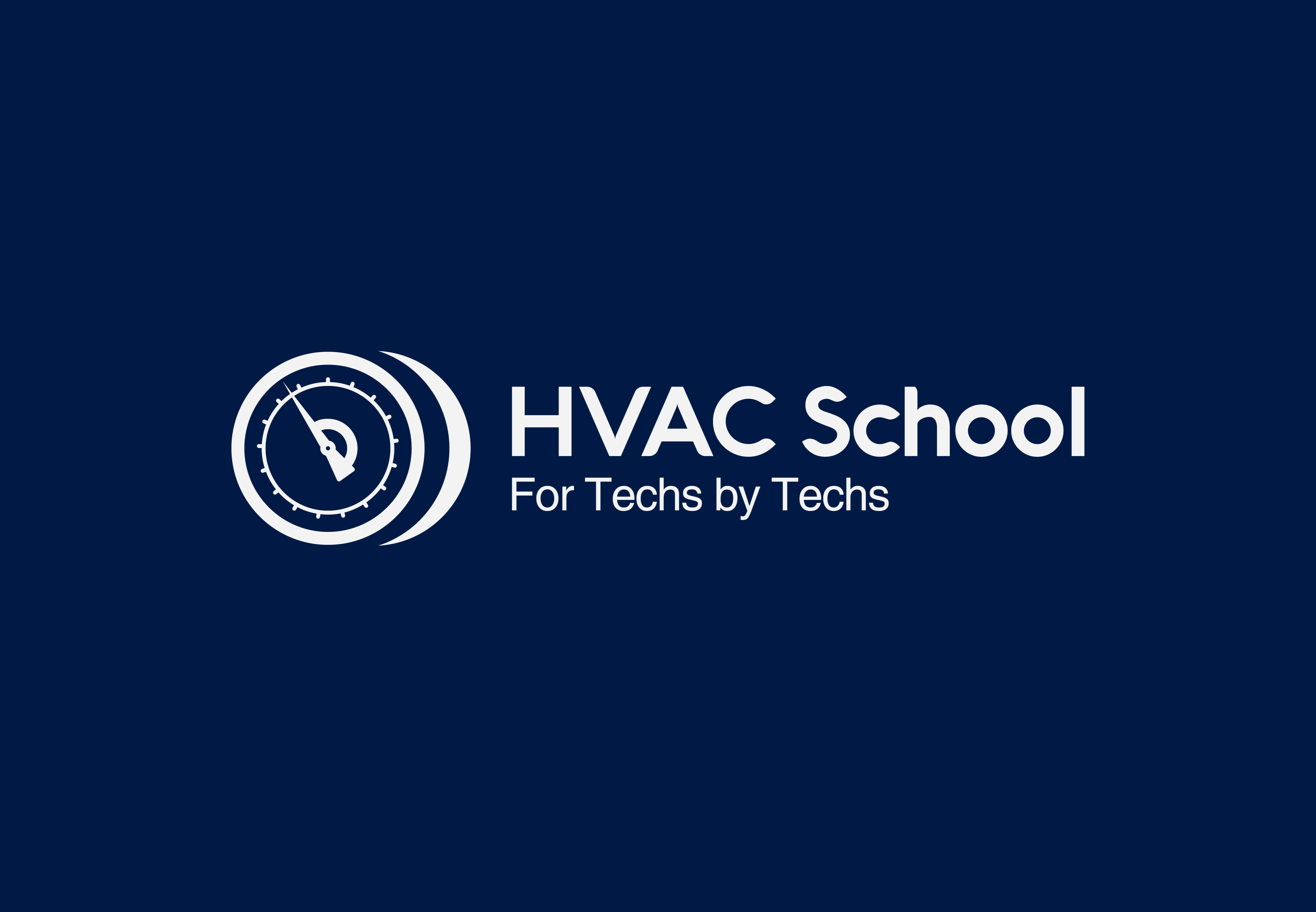
In this podcast we discuss the common myth about flame rod / semsor / rectification cleaning
Read more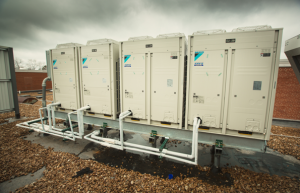
This tech tip was written by experienced tech and VRF/VRV specialist Ryan Findley. Thanks, Ryan! (Note: Ryan refers to VRV rather than VRF because he specializes in Daikin, and these articles are written from a Daikin VRV perspective. He also wrote a great introductory guide to VRV systems, which you can find here.) In this […]
Read more