January 2019
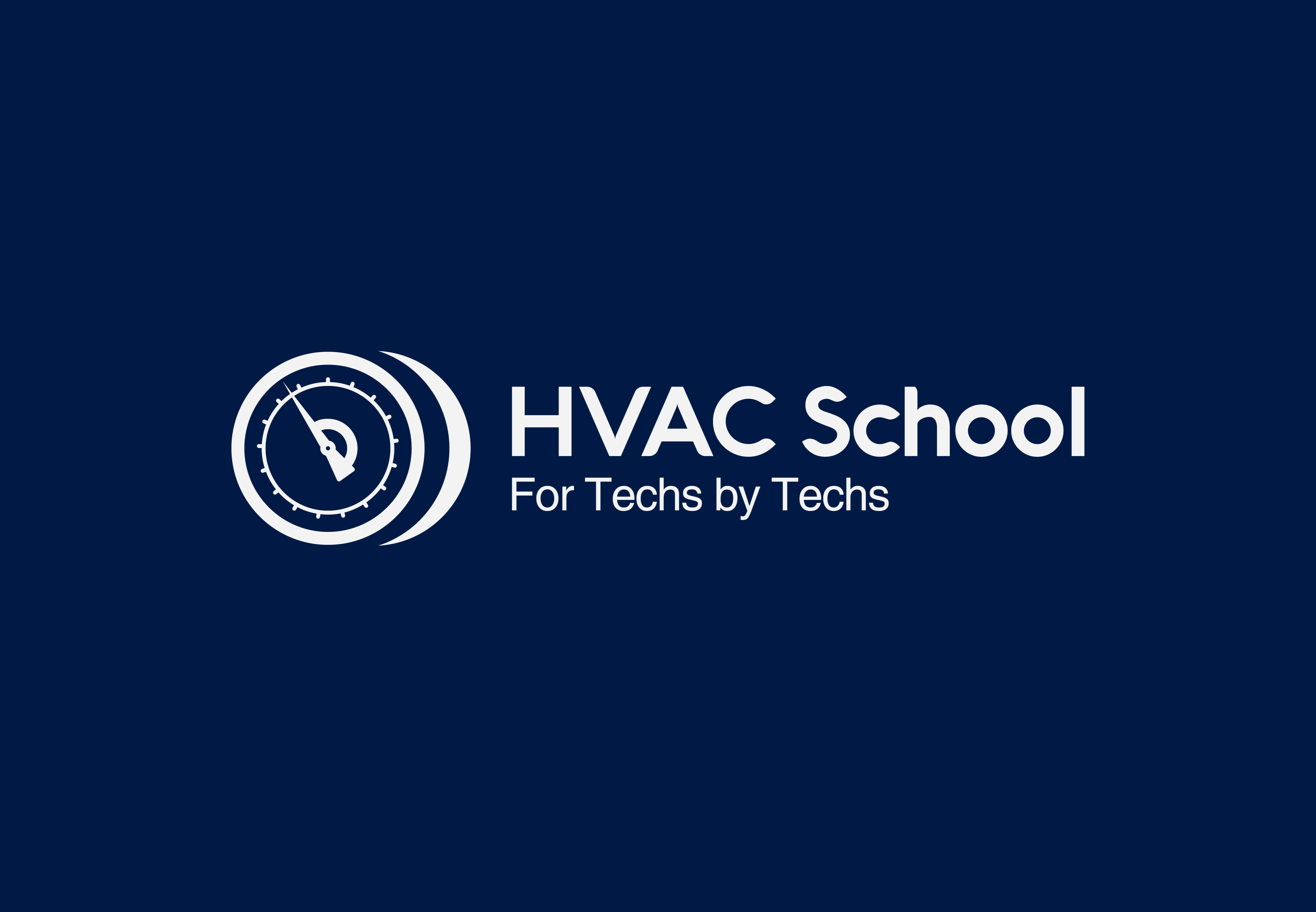
In this episode we speak with Embraco about R290 (Propane) refrigerant, Hydrocarbons and what you need to know about them. Links: http://refrigerationclub.com/ http://naturalrefrigerants.info/ http://embraco.com/Default.aspx?tabid=40
Read more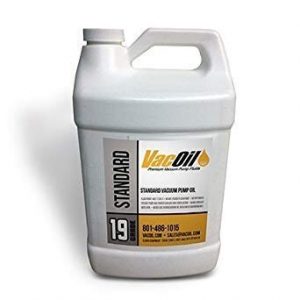
We all understand that vacuum pump oil is the lifeblood of our vacuum pumps. We know what the function of vacuum pump oil is and how it functions. But how do we apply that knowledge when choosing the oil best suited for our pumps? Many of us simply pick up what’s in the stock room […]
Read more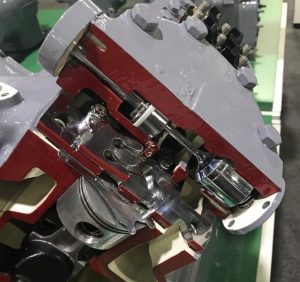
Basic Compressor Functions The compressor's job is to circulate refrigerant through the system by means of vapor compression, similar to the way your heart moves blood through your circulatory system. Refrigerant circulation is measured in lbs/min or lbs/hour; this is called mass flow rate—the mass flow rate changes depending on the density of the refrigerant […]
Read more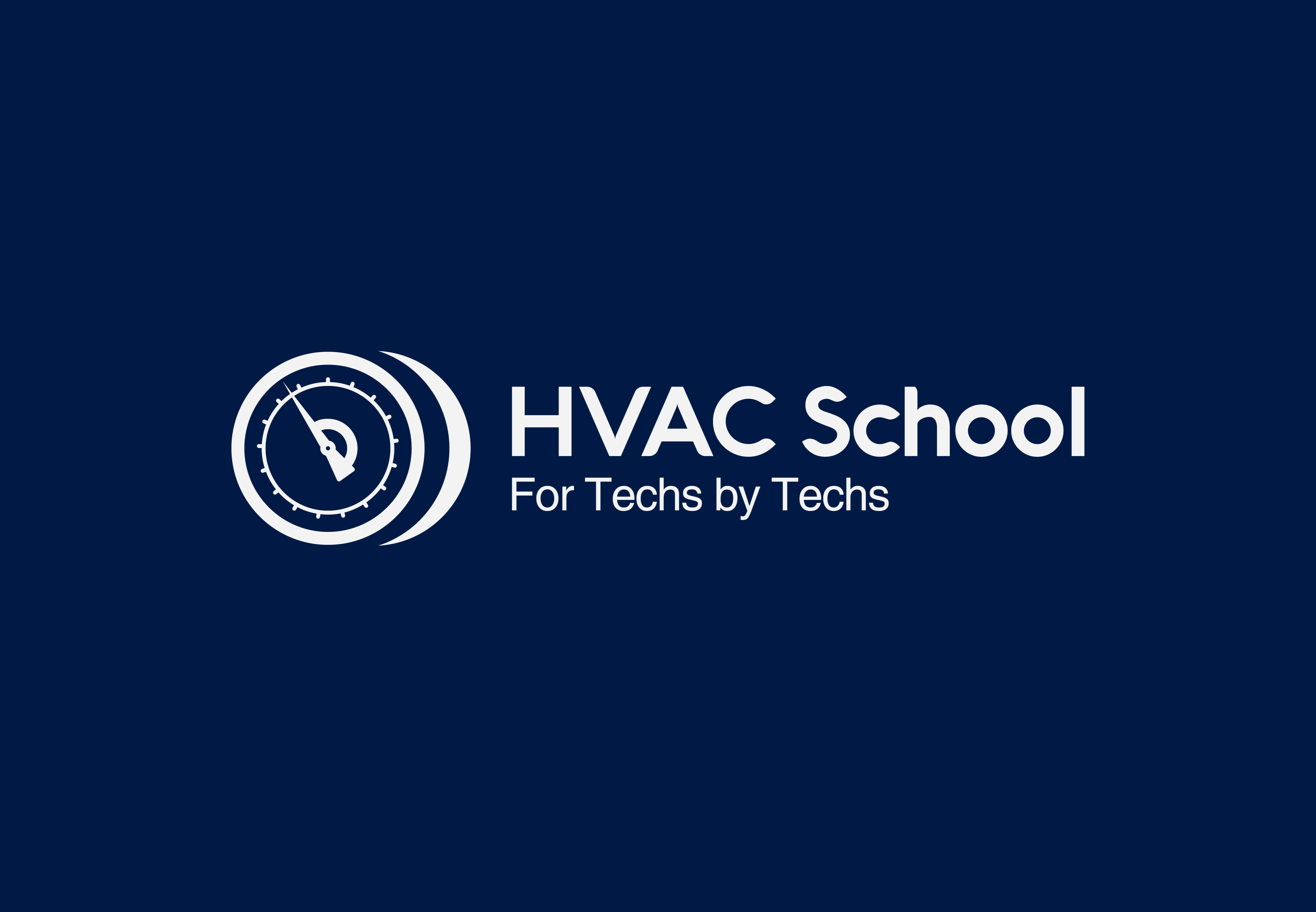
We talk through measuring amperage on a blower and condensing fan motor and why you may be measuring innaccurately resulting in a misdiagnosis
Read more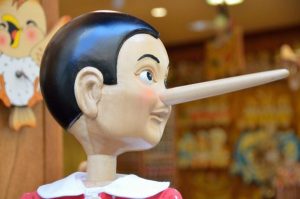
This article is written by longtime tech Shaun McCann sharing his experiences with a big problem in our trade. Thanks for this, Shaun. I started in the HVAC business working for a small commercial union shop in the late '80s. I left that job within a year and worked in the bar and restaurant business […]
Read more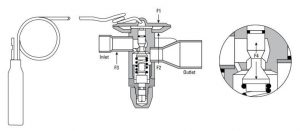
This quick article was written by market refrigeration tech Clayton Peeples. Thanks, Clayton! Adjusting the TXV should be done last after checking all other causes of the case being warm or floodback on the rack. TXVs very rarely go bad; generally, it's a dirty screen or a failed powerhead, both of which can be addressed […]
Read more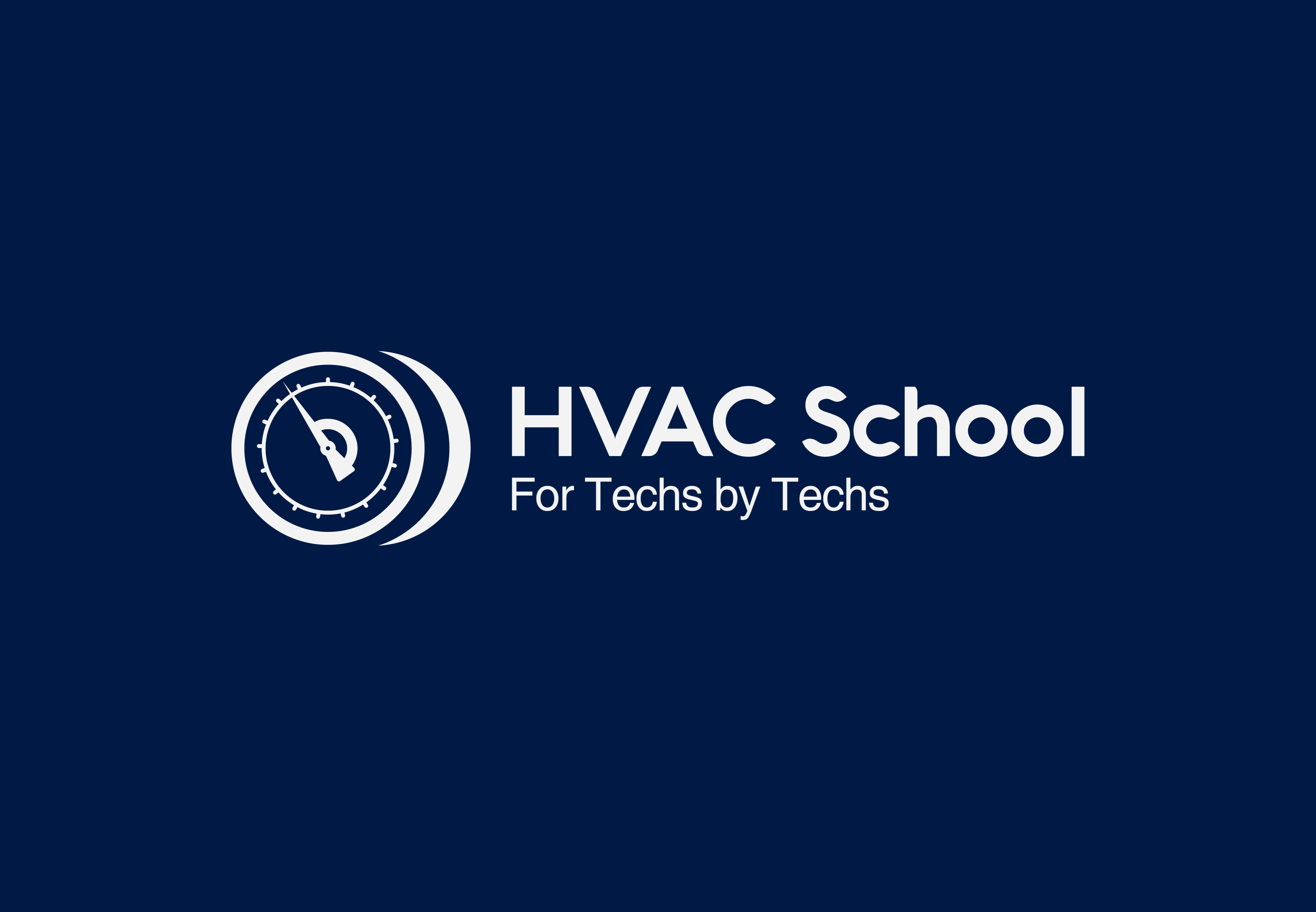
In this service manual talk through episode we discuss the Heatcraft Beacon 2 refrigeration system and what it entails
Read more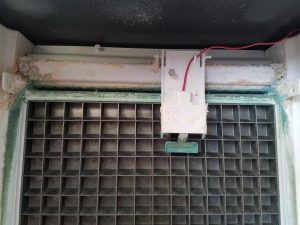
This article was written by Austin Higgins, an experienced commercial service tech from Iowa. Thanks, Austin! Ice machines and limescale Any seasoned refrigeration technician knows that ice machines can be extremely finicky contraptions. Modern commercial ice makers have become a complex symphony of tubing, valves, pumps, and water directed by advanced microprocessor control boards. Newer […]
Read more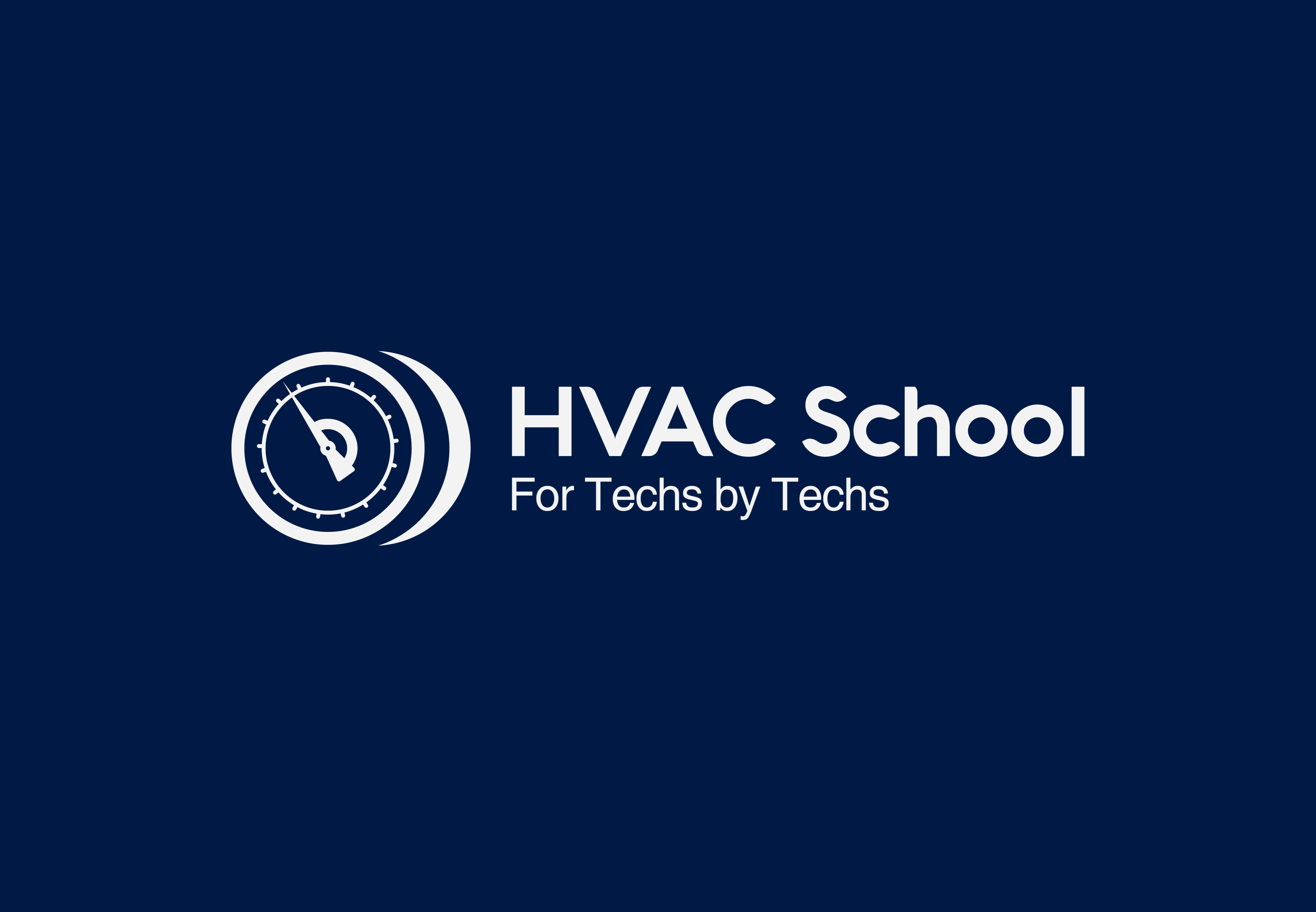
This episode covers the why and the how of low ambient cooling and refrigeration
Read more