December 2018

This article was written by my buddy and Canadian Supertech Tim Tanguay. Thanks, Tim! This P/E chart shows R410a at 100°F saturated condensing temp, 10°F SC, 40°F saturated suction temp, 20°F SH at the compressor. The green highlighted thumb shape is the saturation zone. Everything that occurs in the saturation zone is a latent (change […]
Read more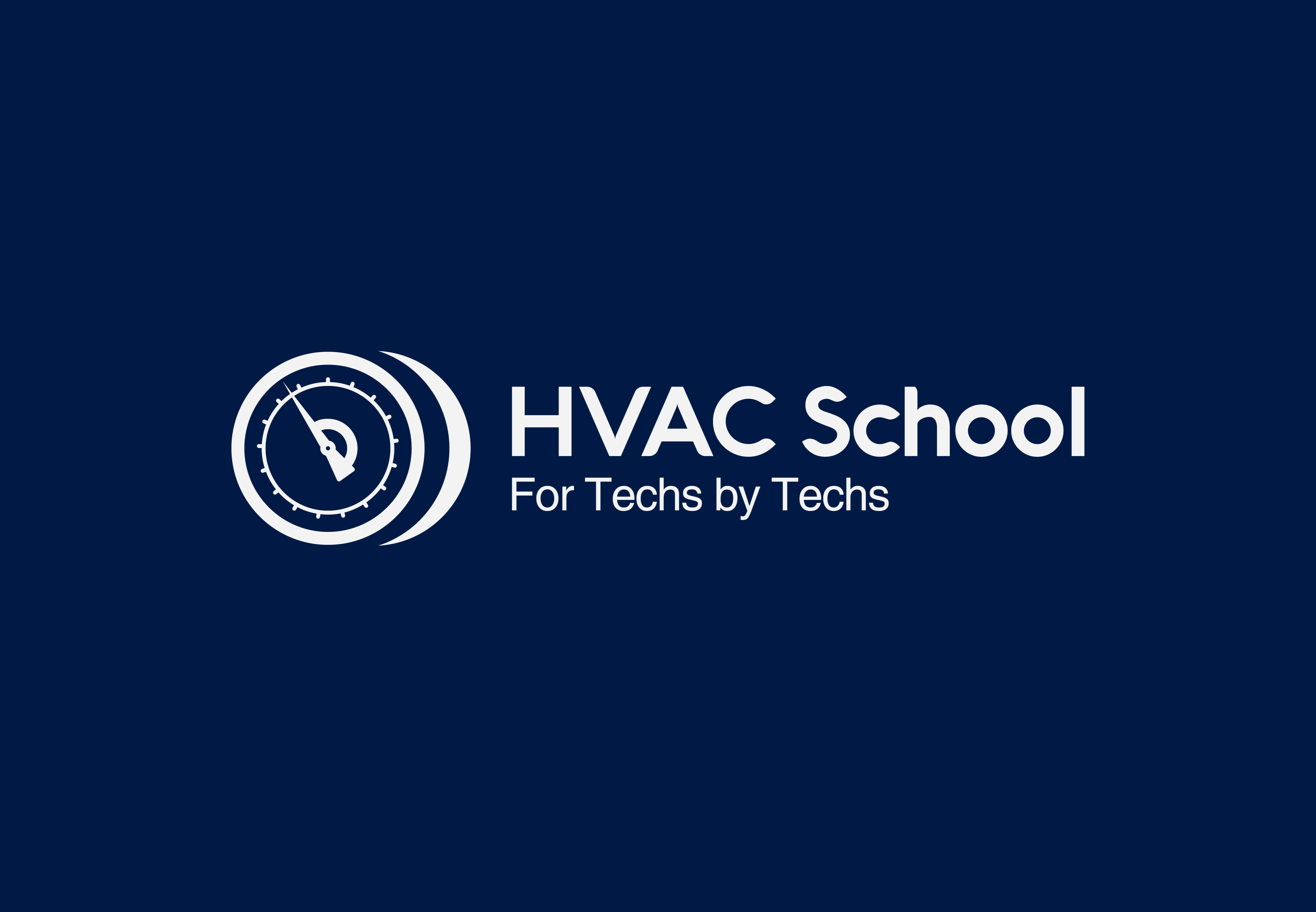
In our first ever ask me anything podcast we talk about the trade as whole and answer random questions about Kalos and myself
Read more
I hear many techs complain about the finicky and ineffective nature of electronic leak detection. So much so that some claim that it is a waste of time altogether. We recently located a leak inside the fins of a ductless evaporator coil—pinpointed to an exact spot—using an electronic leak detector. For demonstration purposes, we took […]
Read more
I hear many techs complain about the finicky and ineffective nature of electronic leak detection—so much so that some claim that it is a waste of time altogether. We recently located a leak inside the fins of a ductless evaporator coil—pinpointed to an exact spot—using an electronic leak detector. For demonstration purposes, we took that […]
Read more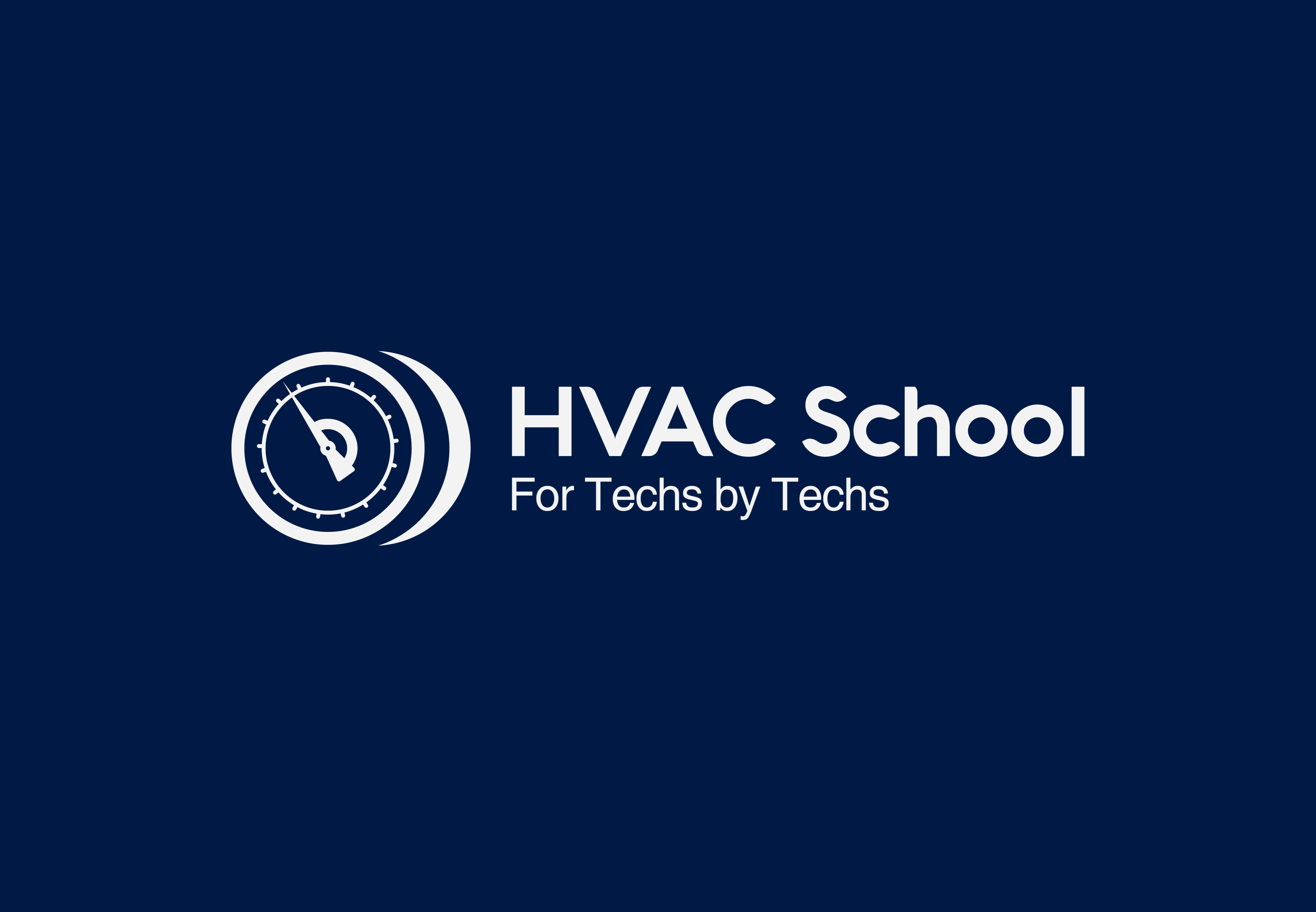
Here are some things to consider before replacing that old A/C with a bigger one
Read more