October 2017
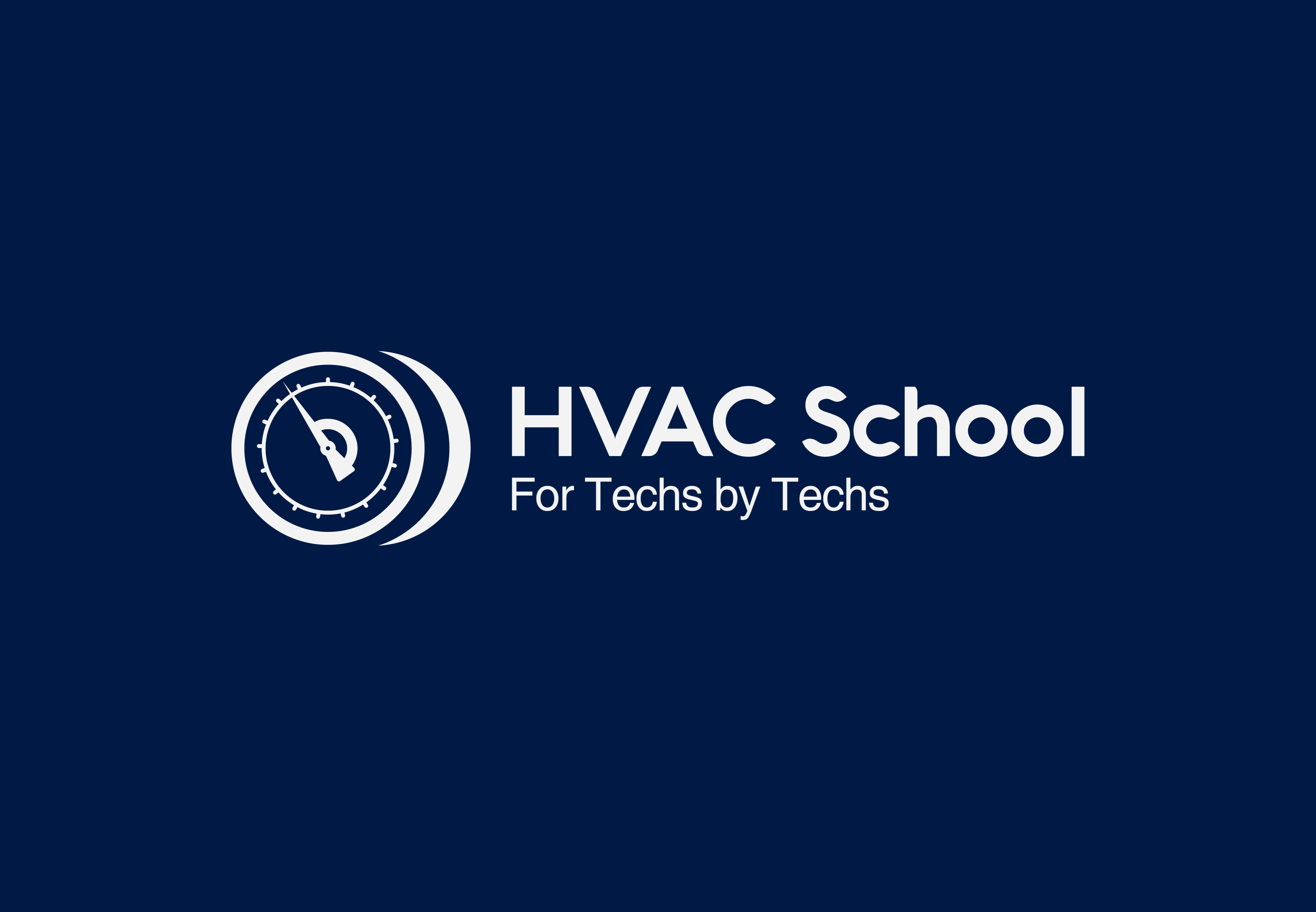
Do you think of the Building envelope as a duct? Do you test it? In this episode Joe Medosh talks to us about envelope testing and why it’s the future of Building health and comfort
Read more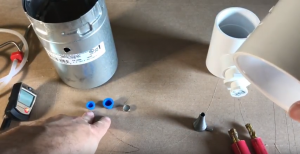
My good friend and contributor to HVAC School, Neil Comparetto, made this video showing how he creates access ports for static pressure and gas combustion analysis. As techs, we find ourselves in the tough position of needing to drill access holes to take measurements, but the drilling and sealing of the holes can sometimes create […]
Read more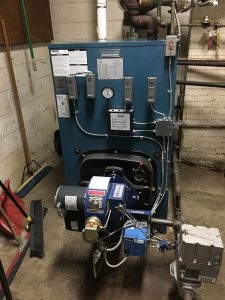
This article is the second in a series on boiler basics by senior boiler tech Justin Skinner. Thanks, Justin. There are many types of boilers that do many different things, but almost all of them have some of the same basic components. It's partially because regulatory agencies require them, and other times, it's because they […]
Read more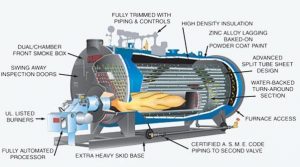
This series of articles is written by senior boiler tech (and all-around swell guy) Justin Skinner. Thanks, Justin. There are quite a few different types of boilers out in the world. They come in all shapes, sizes, pressures, and types of fuel burned. I'm going to go over some of the more common ones, their […]
Read more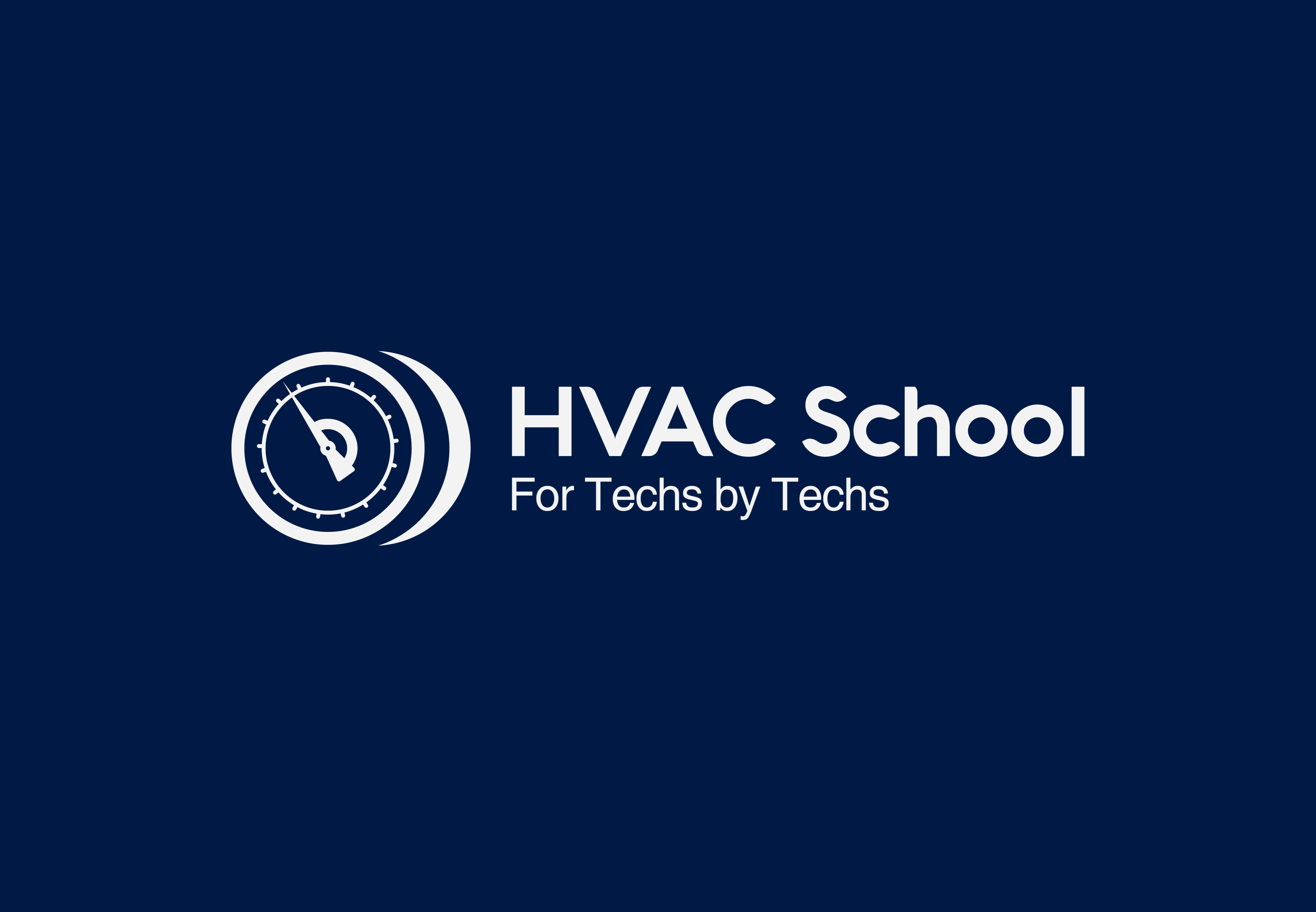
Ductless expert Jesse Claerbout talks about his best practices for maintaining ductless air conditioners and heat pumps part 2
Read more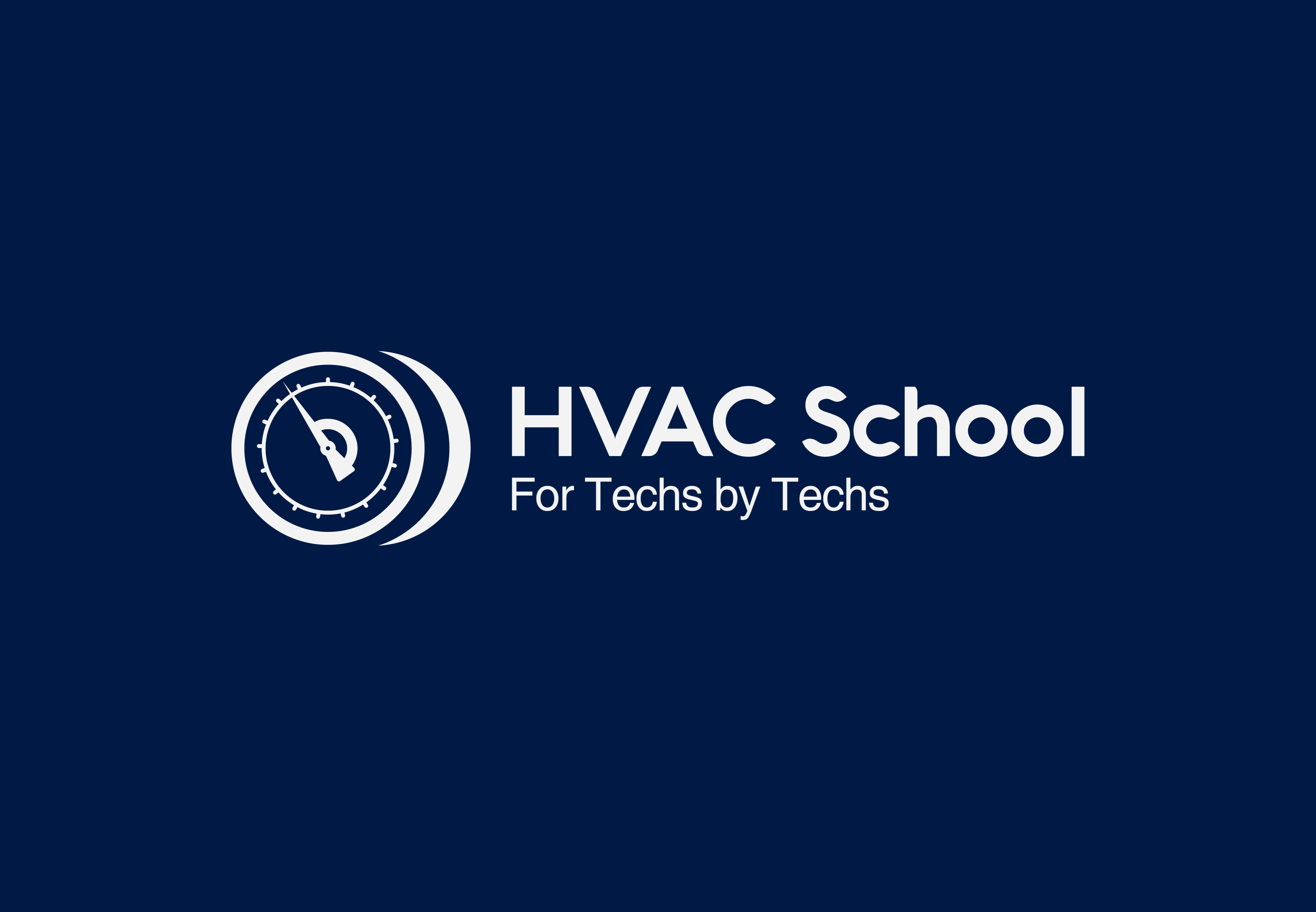
Ductless expert Jesse Claerbout talks about his best practices for maintaining ductless air conditioners and heat pumps part 1
Read more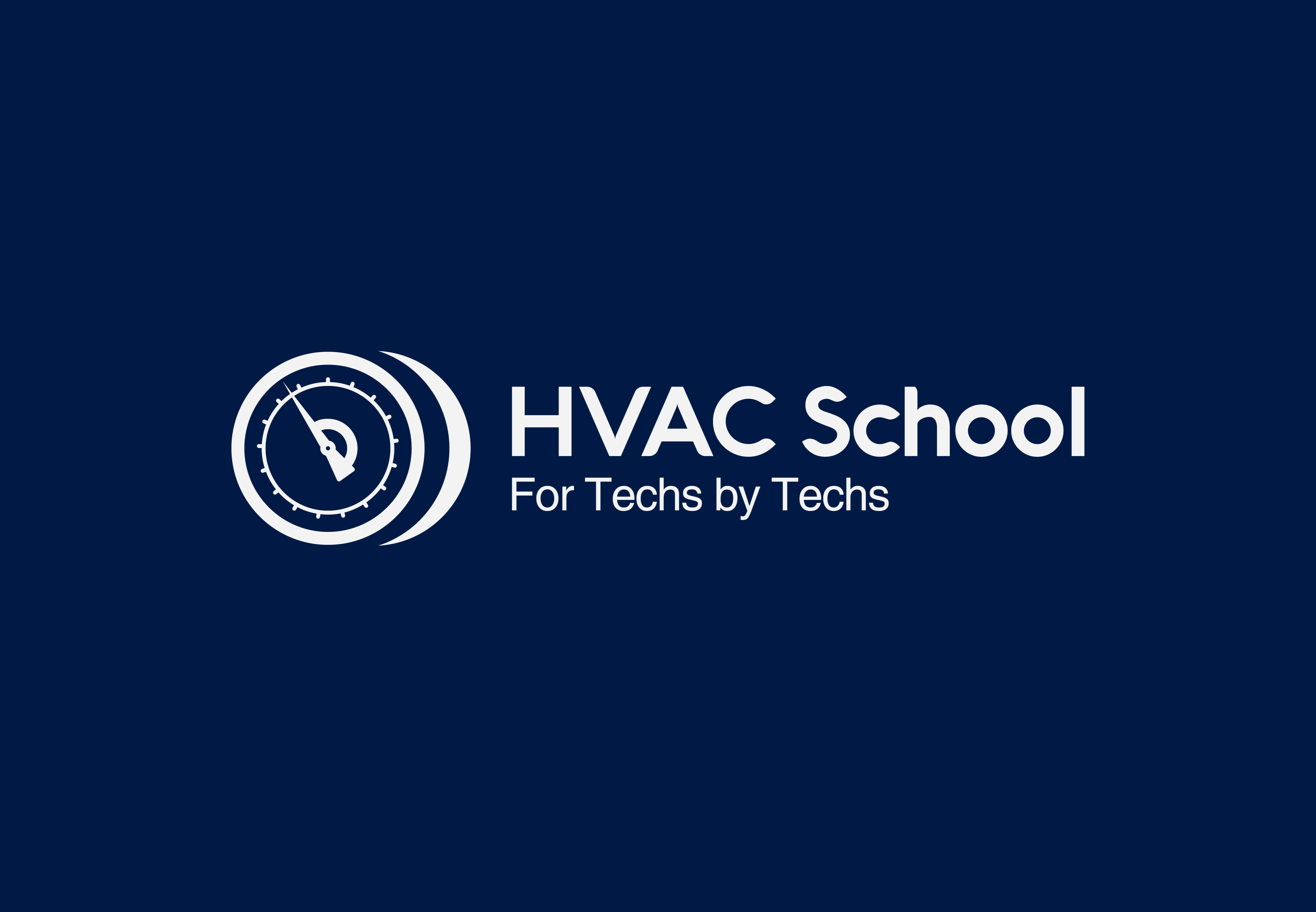
In this epsiode, we cover some common misconceptions about run capacitors as well as some easy ways to test and some tips.
Read more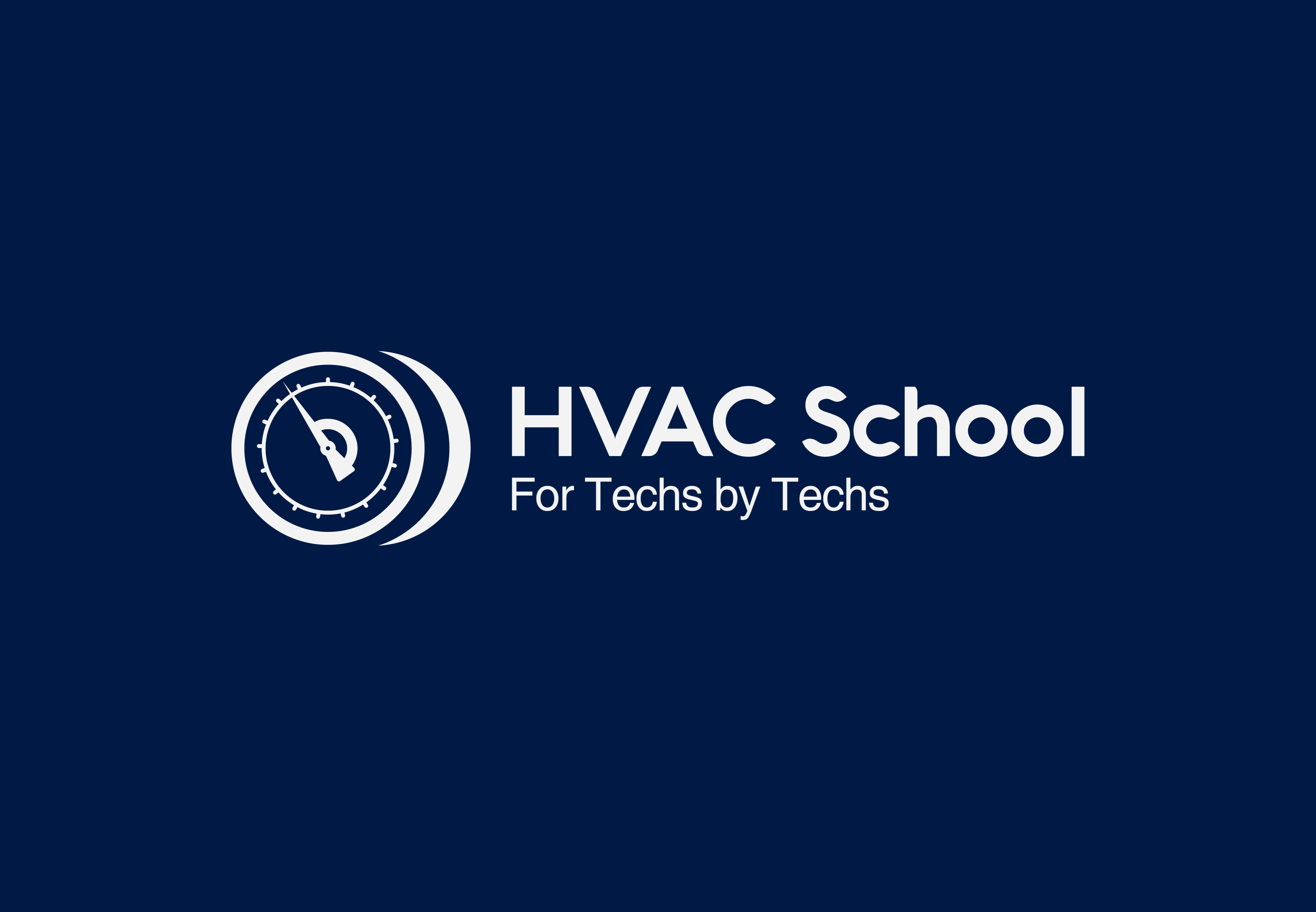
James from Rectorseal talks about the IMC codes relating to tamper resistant caps and why you may consider installing them now
Read more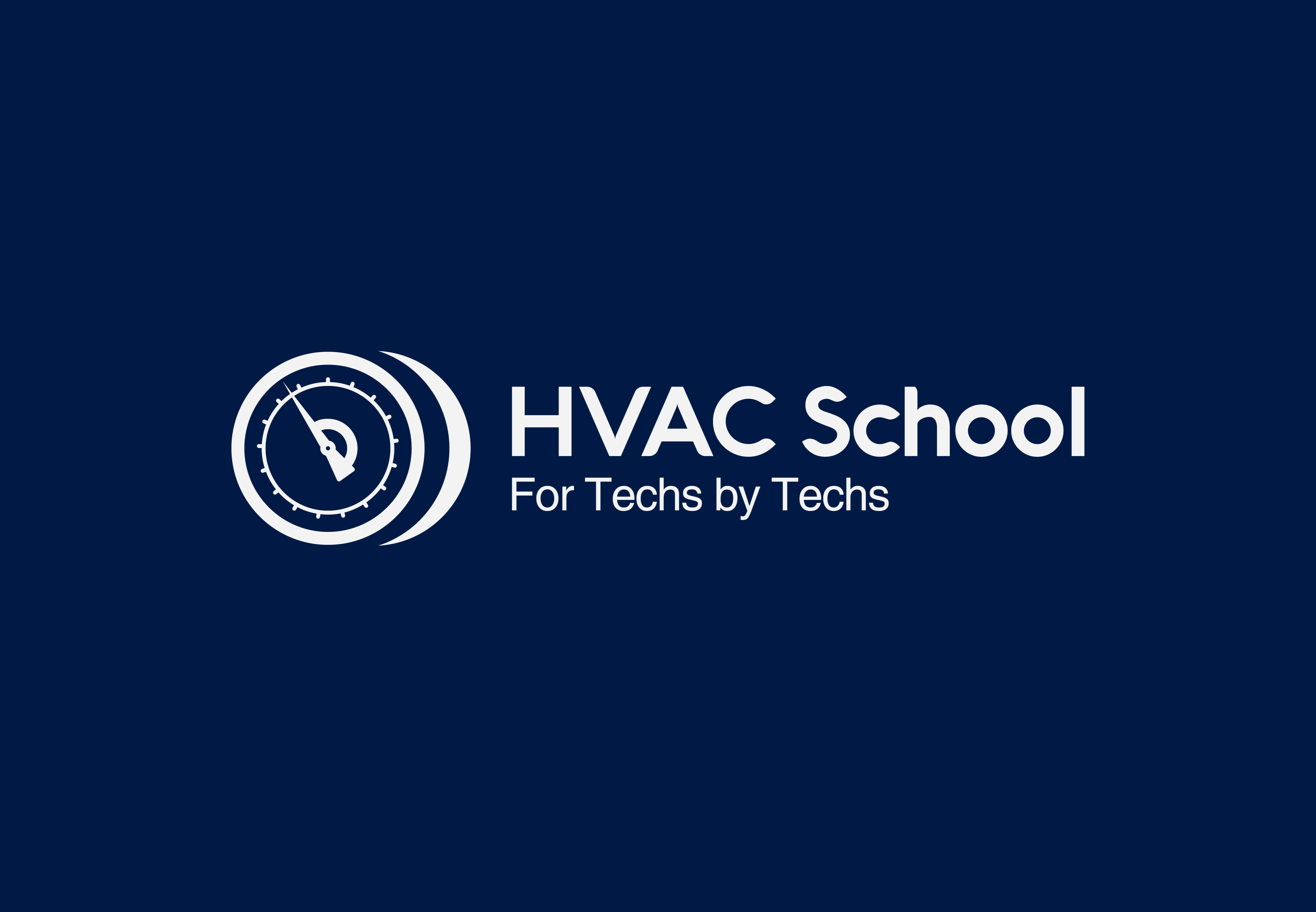
Many techs know just enough about economizers to bypass them. In this podcast we talk about the basics of what they are and ow they function,
Read more