July 2017
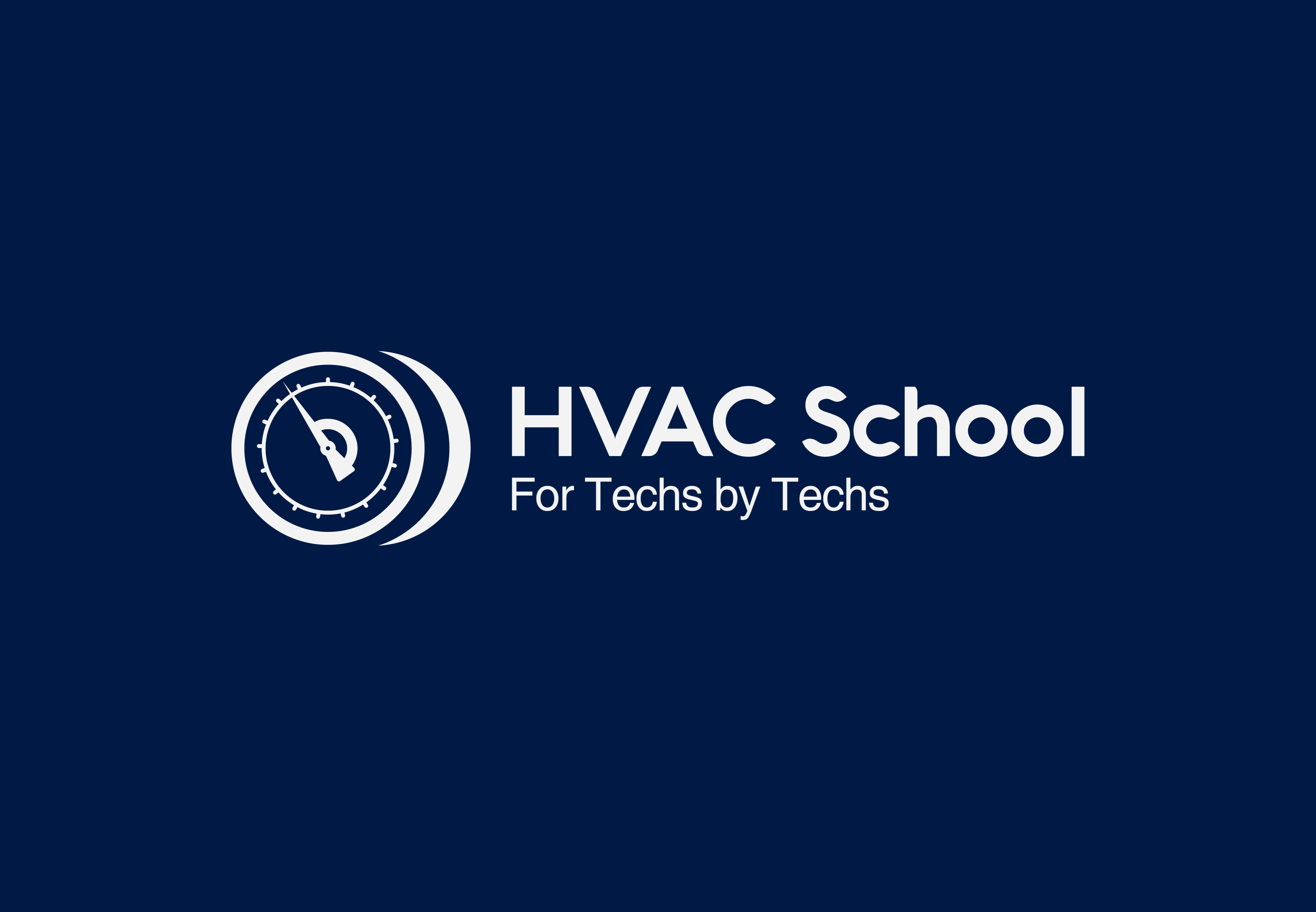
In this episode, we talk about being on call as a technician as well as delve into some best and worst practices.
Read more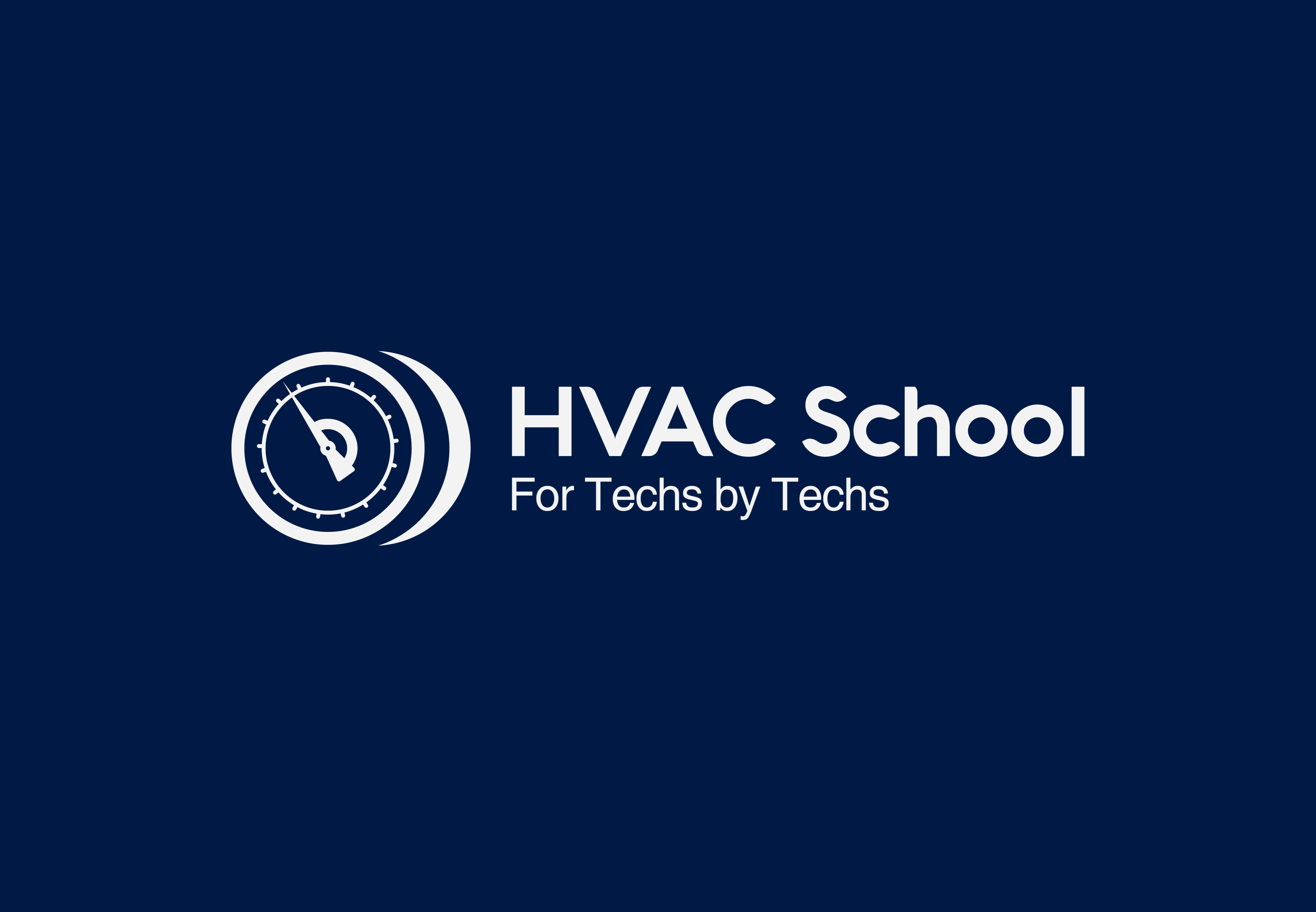
In This episode we talk a lot about standard air, air density and mass vs. volume as well as some other methods of “directly” measuring airflow… it gets pretty deep
Read more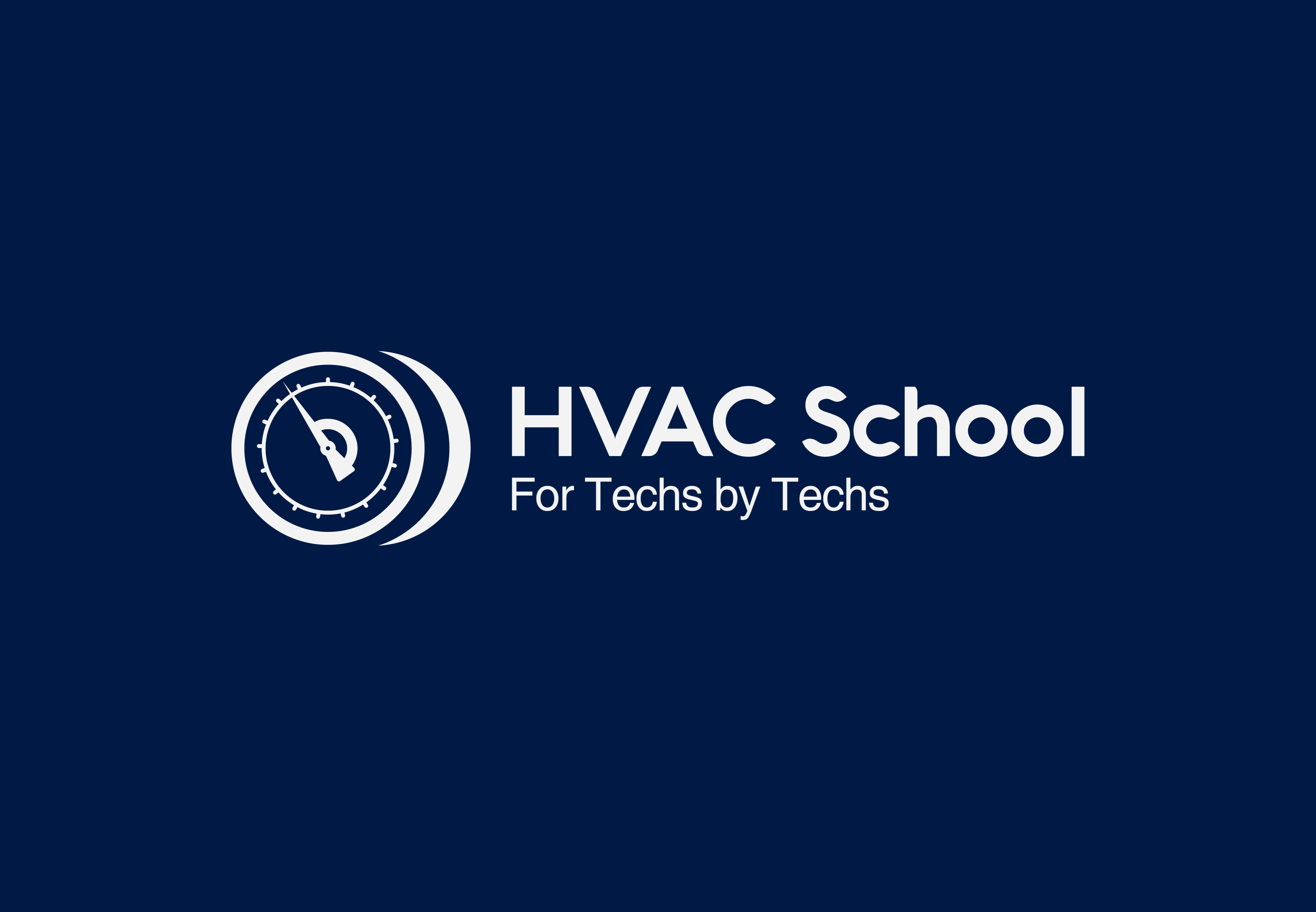
Bill Spohn Jr. is going to college for a business degree but he took a week to see what it is like to work as an HVAC tech. He shares his impressions on this podcast.
Read more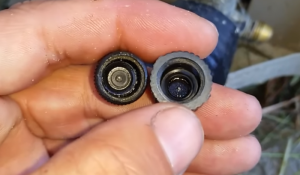
This is a video tech tip from our friend Brad at HVAC in SC. In this video, Brad demonstrates that using a cap off of a refrigerant tank on a system can depress the Schrader core on the system in some cases. Make sure to use proper caps that have seals or brass flare cones. […]
Read more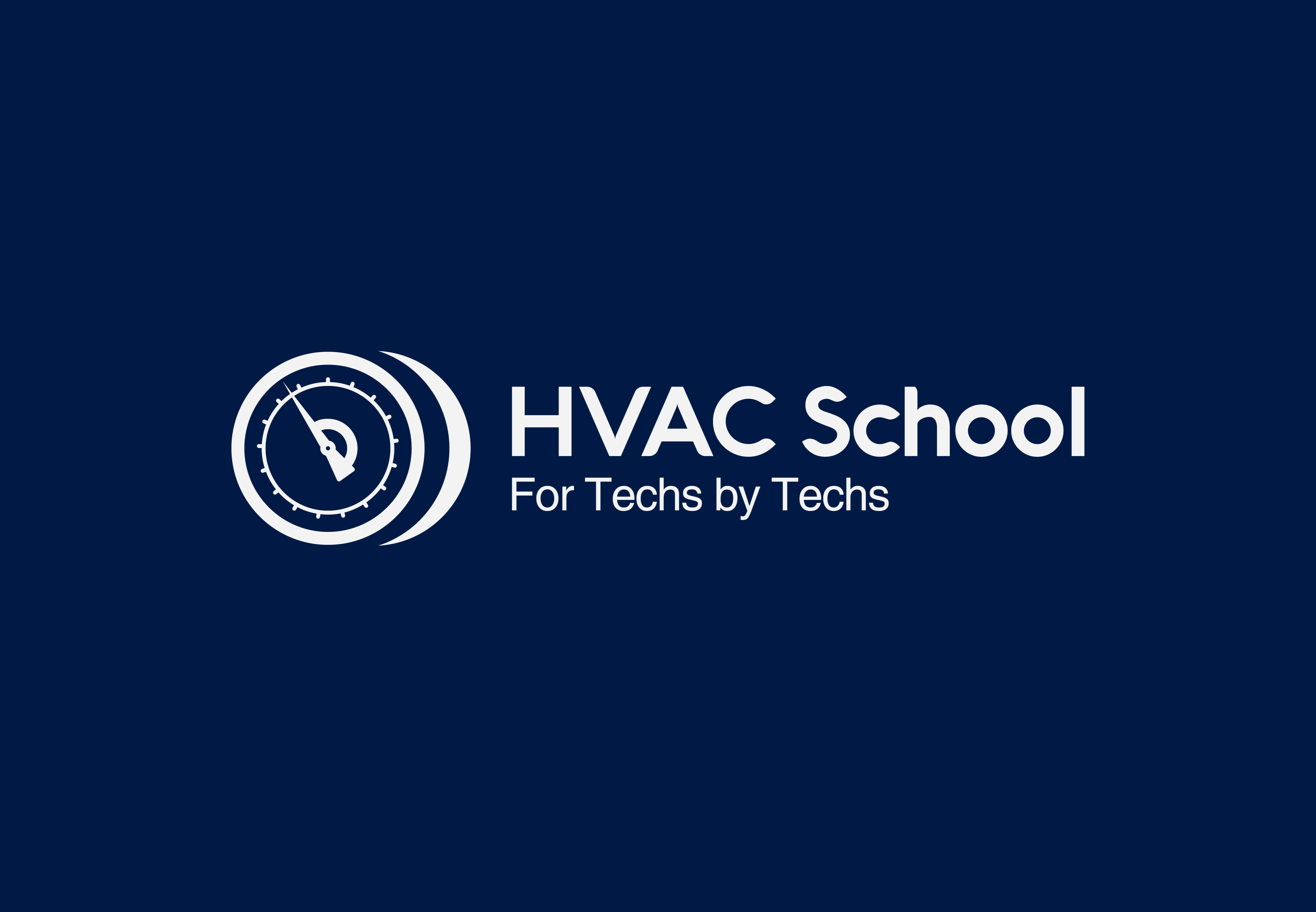
In this episode Jim Bergmann covers static pressure, measuring delivered capacity and ECM motor considerations
Read more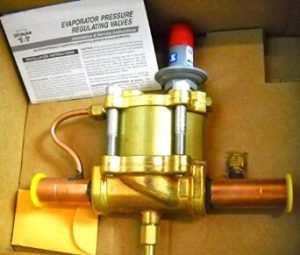
I don't do much in the way of “rack” refrigeration. However, I recently had a conversation with experienced rack refrigeration tech Jeremy Smith, and he got me thinking about EPR valves. I've heard EPR (evaporator pressure regulator) valves called suction regulators or hold back valves. In essence, they hold back against the suction line to […]
Read more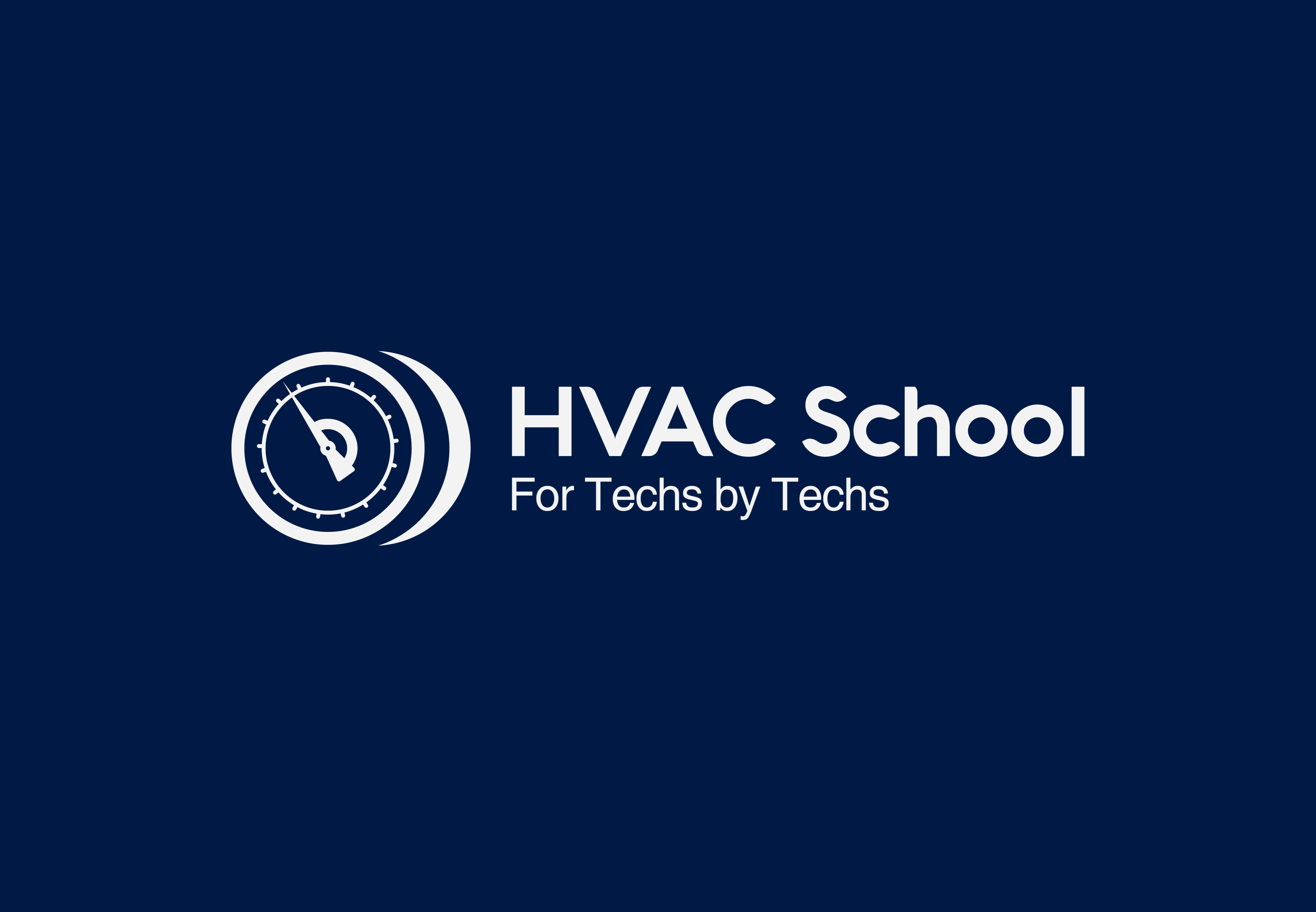
In this episode Bryan talks about brazing safety, regulator settings, torch positioning, flowing nitrogen, heat control and more….
Read more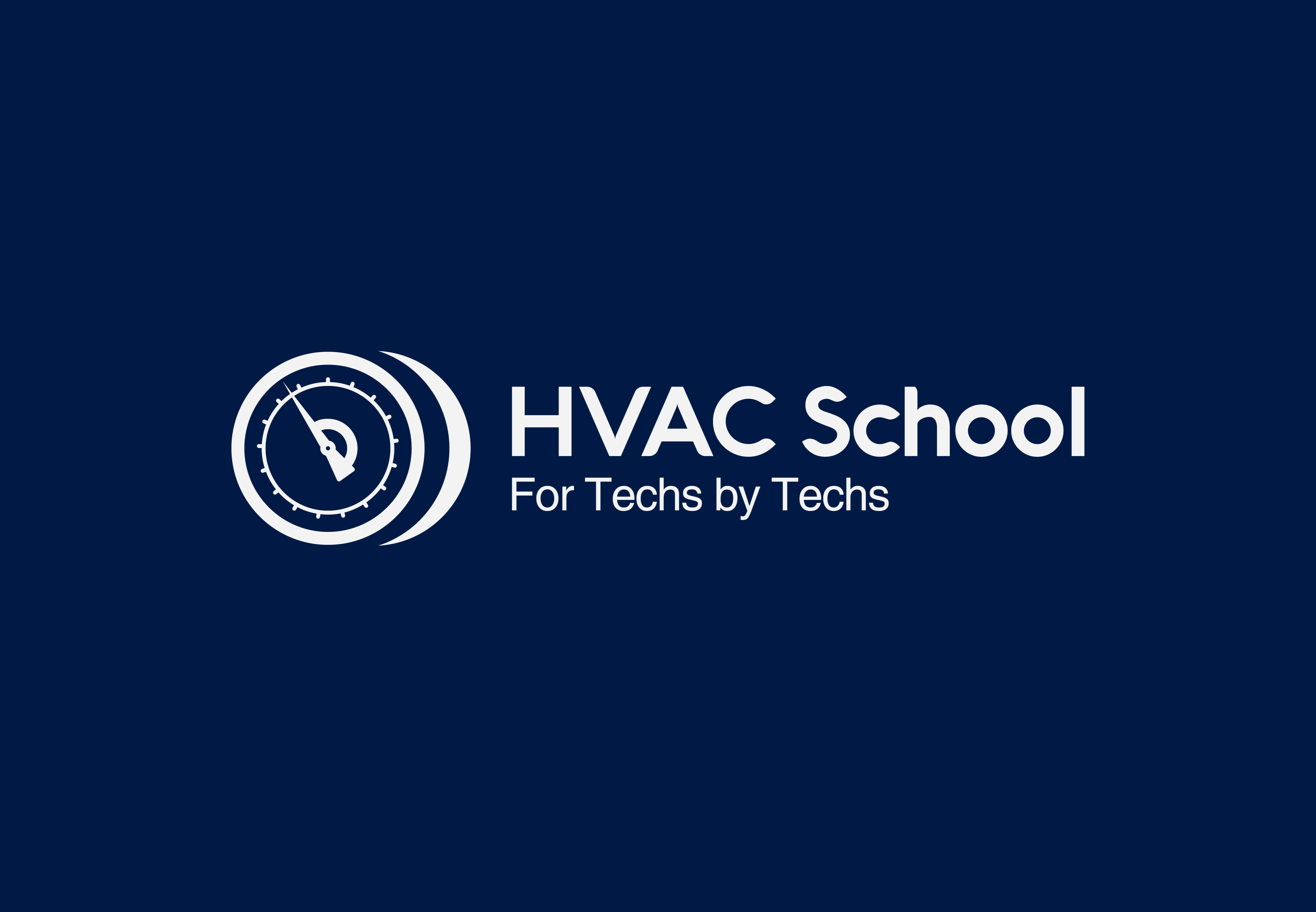
In this episode Bryan talks to Ralph Wolf from T&N Services on Youtube and the Working Joe's podcast. We talk about how the trade has changed for us and what experience gives a tech that can't be read in a book. You can enter the giveaway at hvacrschool.com/summer17
Read more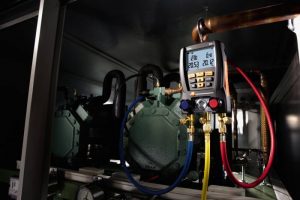
The title says it all. It should be one of the first things you learn when you started. However, I have seen a lot of experienced techs who seldom (if ever) do it. When connecting to a tank, purge your hose by cracking the center connection at the manifold for a second. When connecting to […]
Read more