December 2016
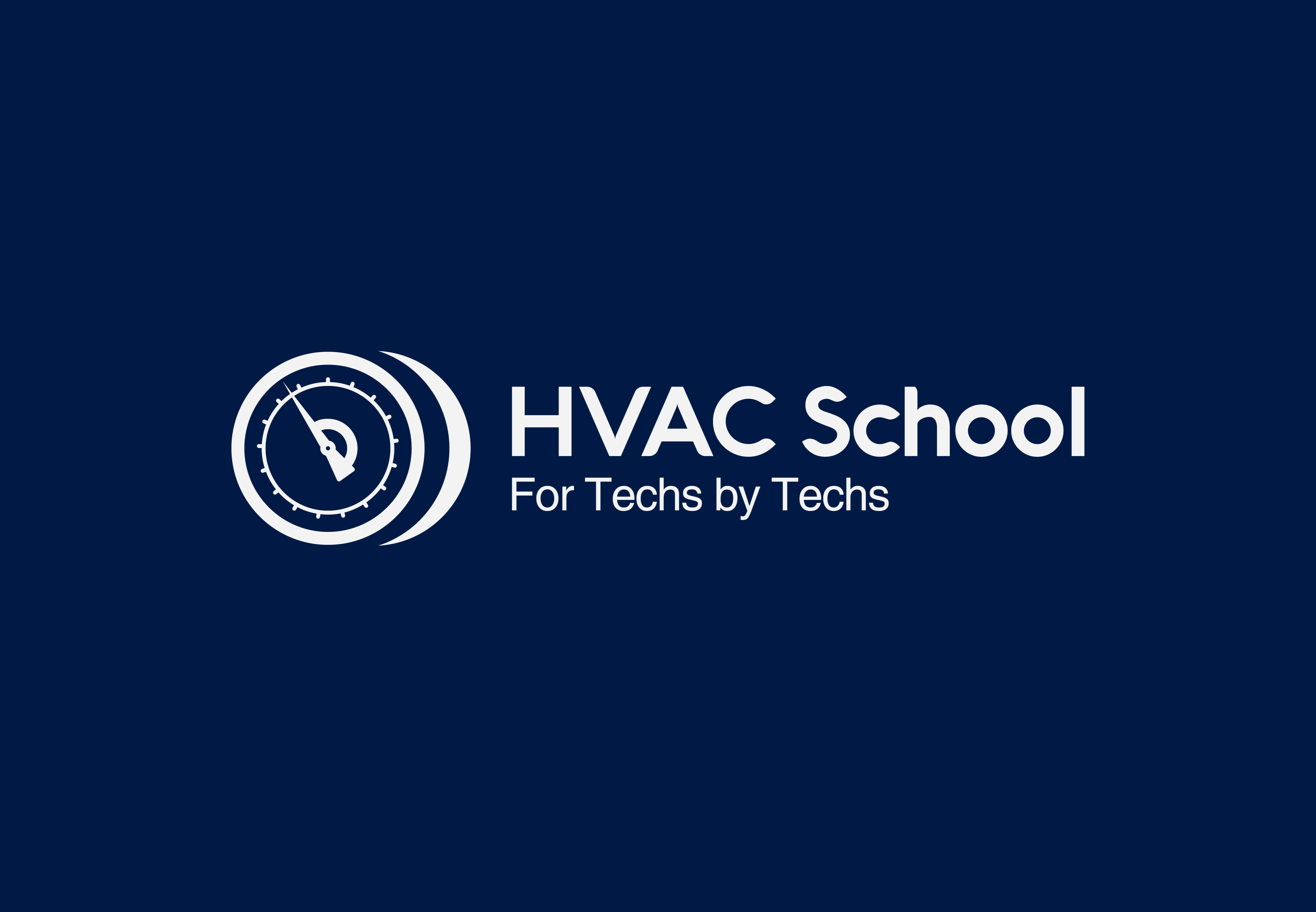
In this unedited episode of HVAC School Bryan and Nathan talks about some basic rules for circuit board diagnosis including – – Isolation Diagnosis – Open Circuits – Short Circuits and many other best practices.
Read more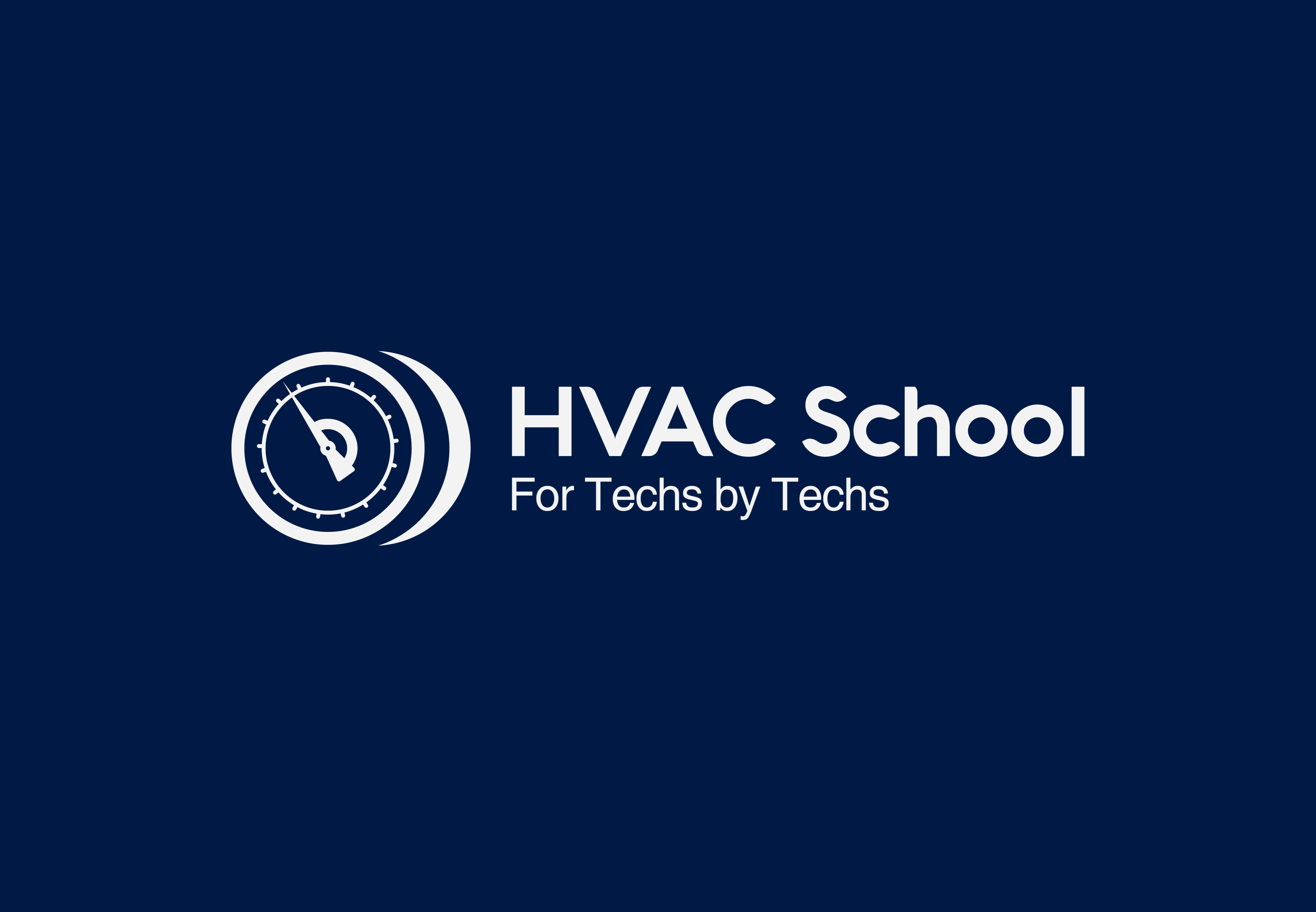
Bryan talks to Ben from Canada about gas furnace basics as well as high-efficiency furnace basics and maintenance.
Read more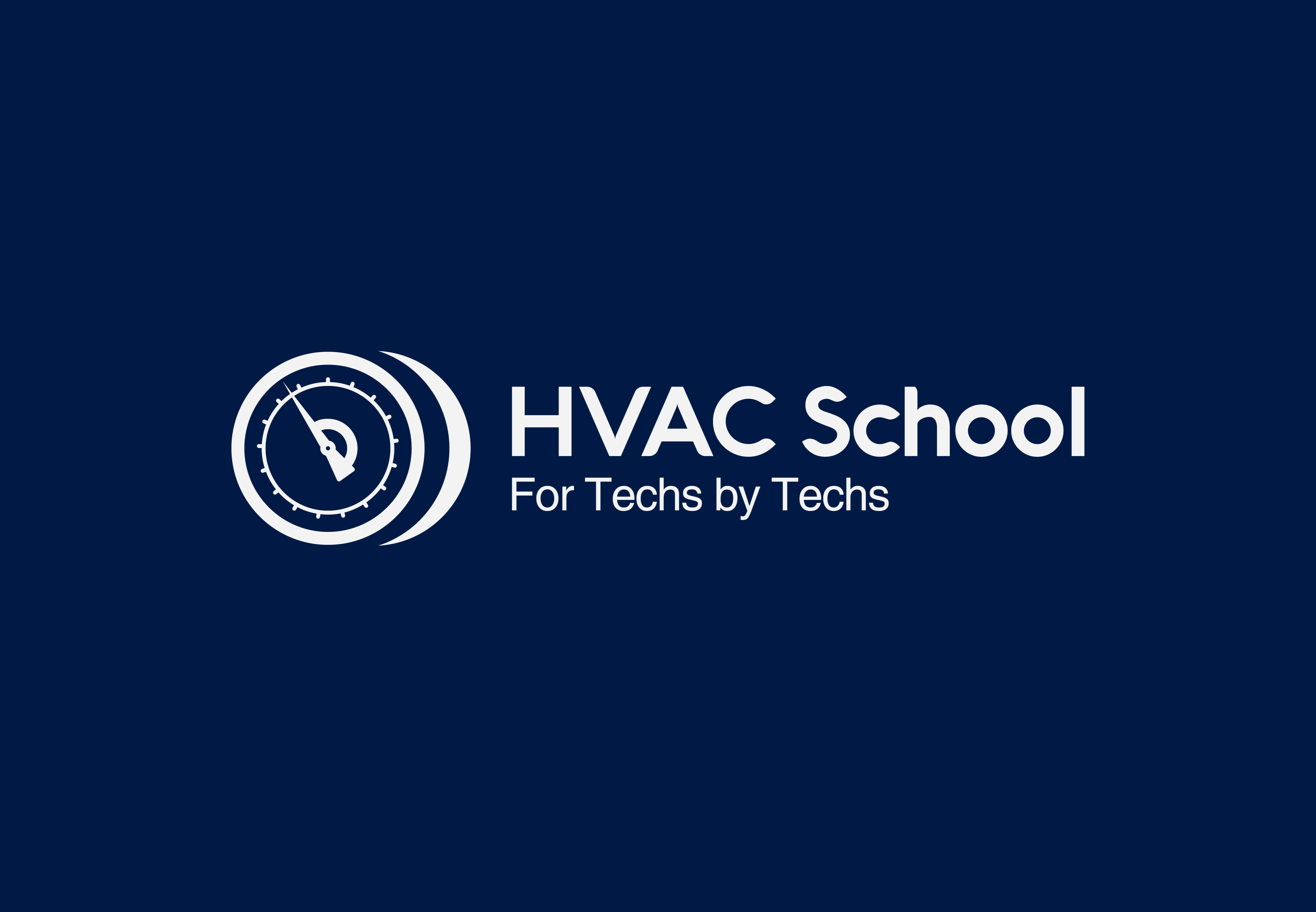
In this episode I get Ulises Palacios on the phone and we talk about some of the things he has been up to. Specifically the iManifold / Bluvac integration, cutting compressors open and thermal imaging.
Read more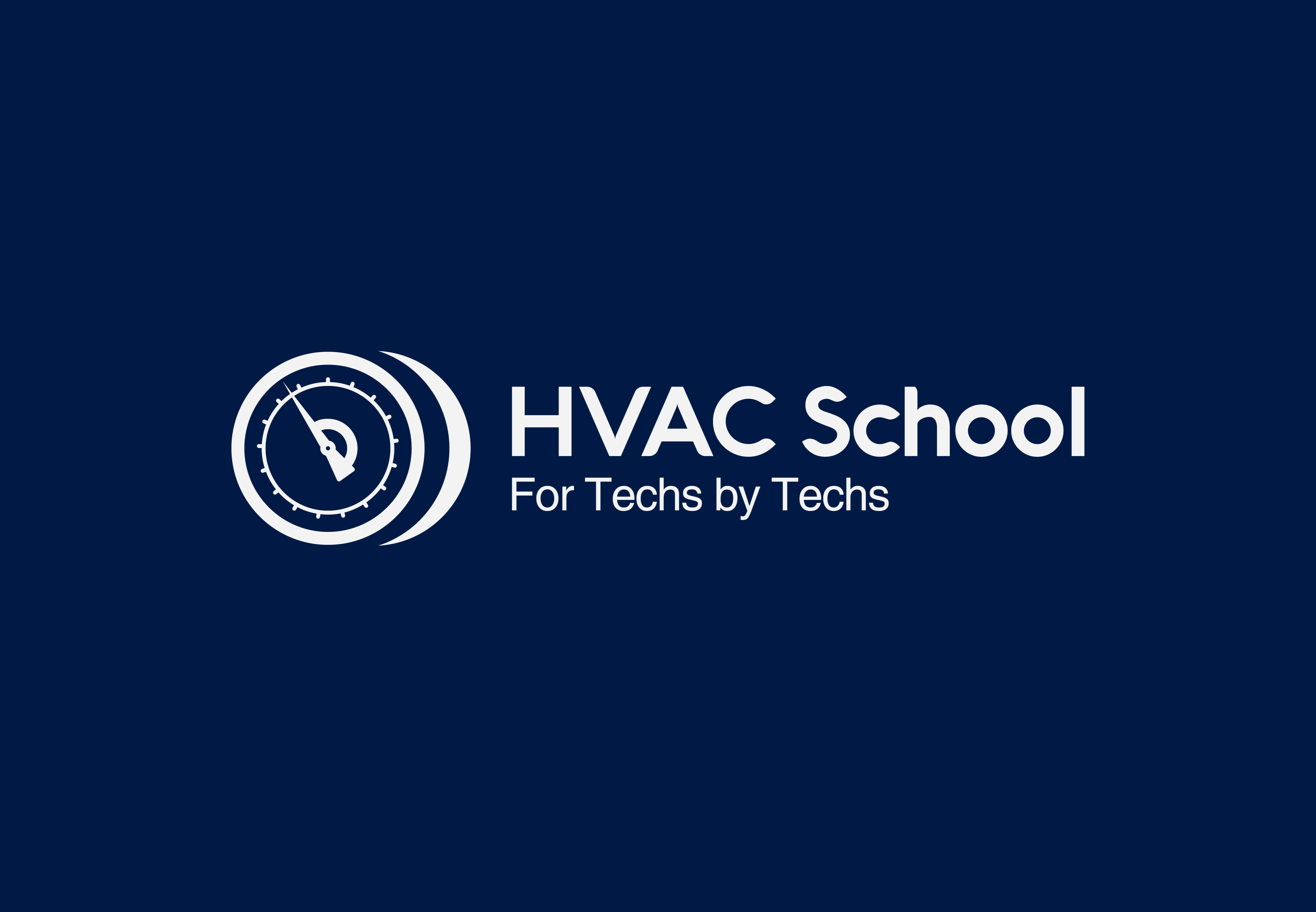
In this episode Bryan talks about heat pumps, reversing valves, defrost, common issues, checking charge in heat mode and diagnosing the dreaded bypassing reversing valve.
Read more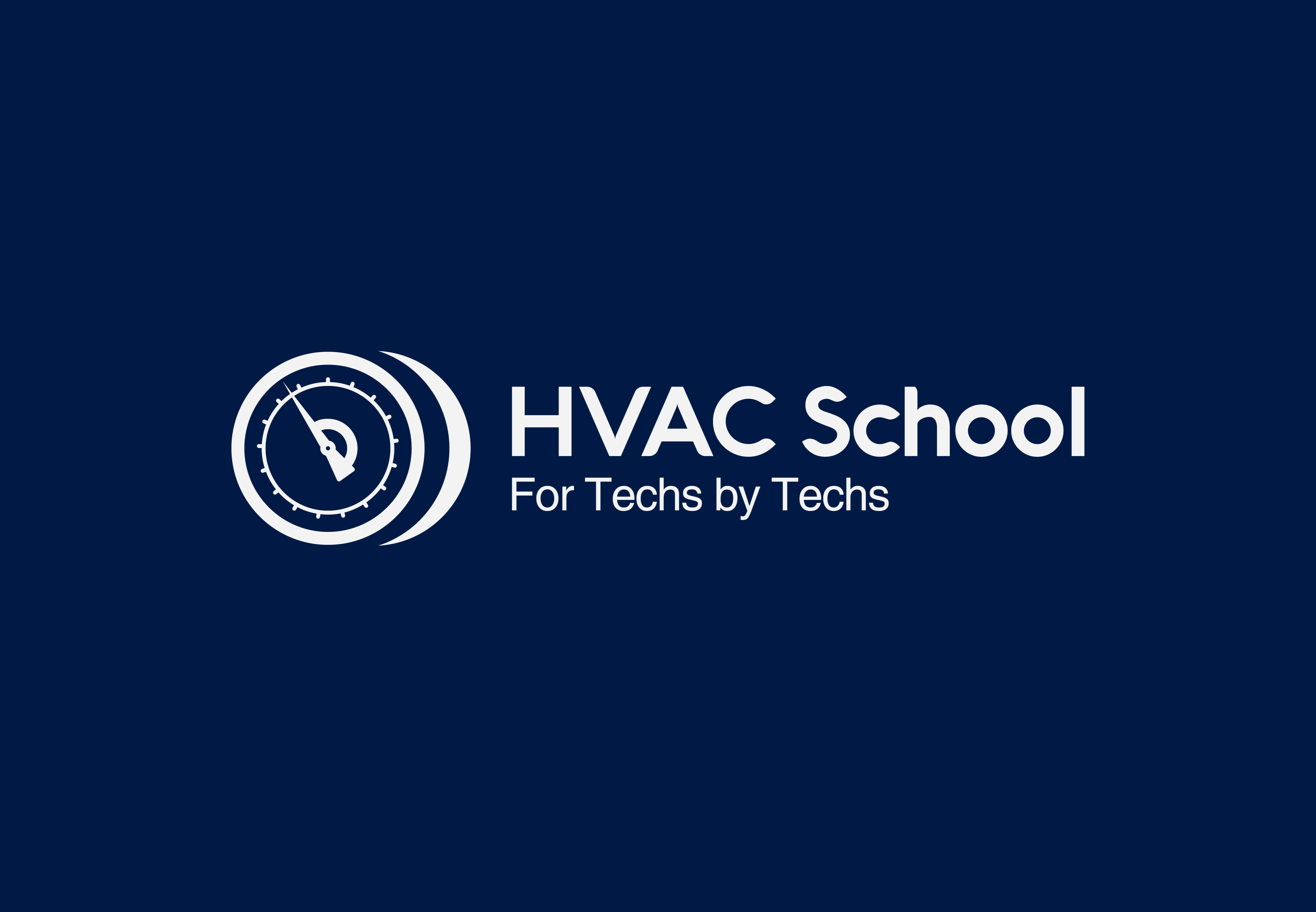
In this episode Nathan and Bryan talk about Relays, Sequencers, Transformers, Contactors, open and Closed Circuits and much more.
Read more