May 2017
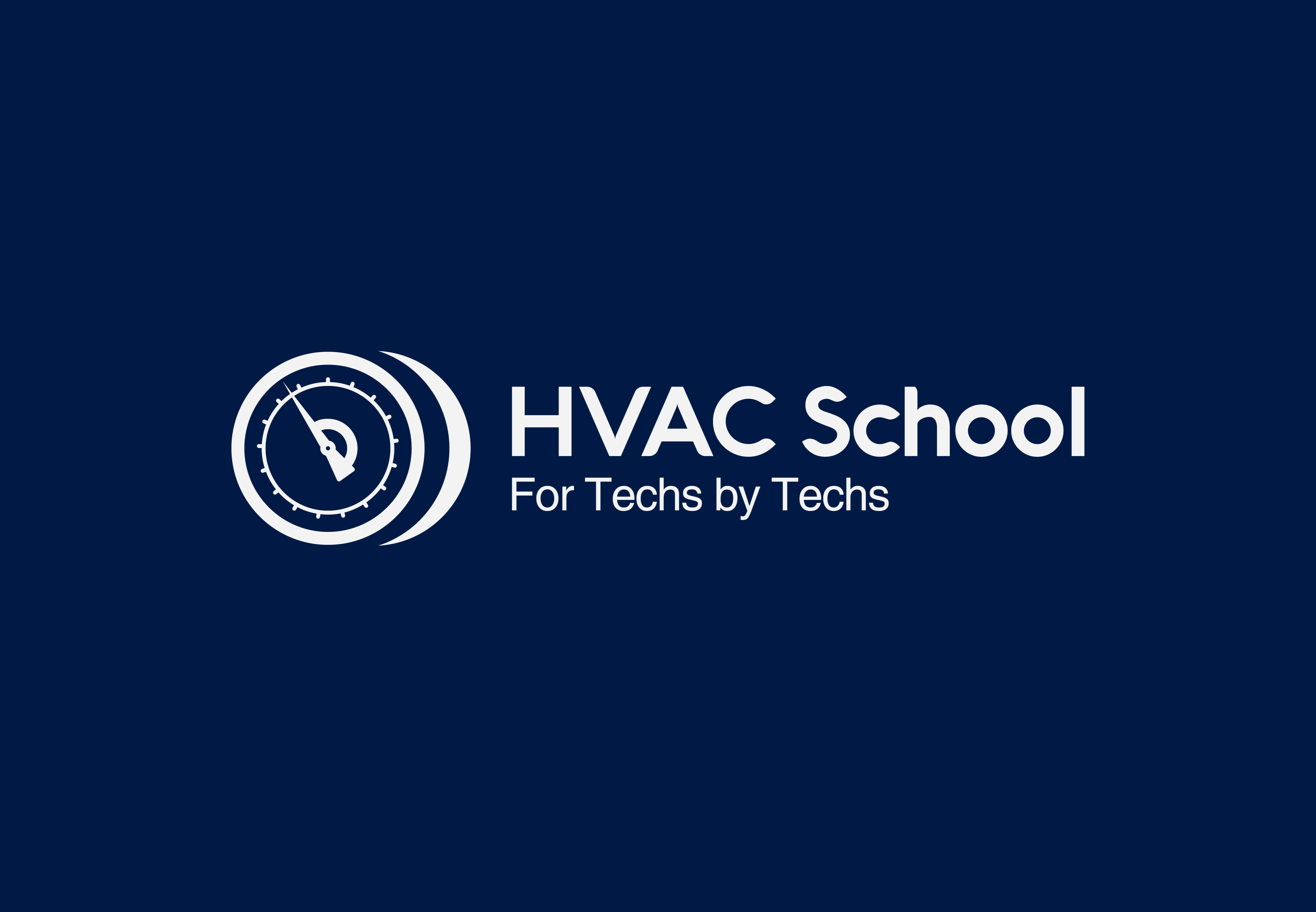
Corbett Lunsford from the Building Performance Workshop and the Proof is Possible tour talks to us about the moral superiority of building performance testing, blower door testing and much more.
Read more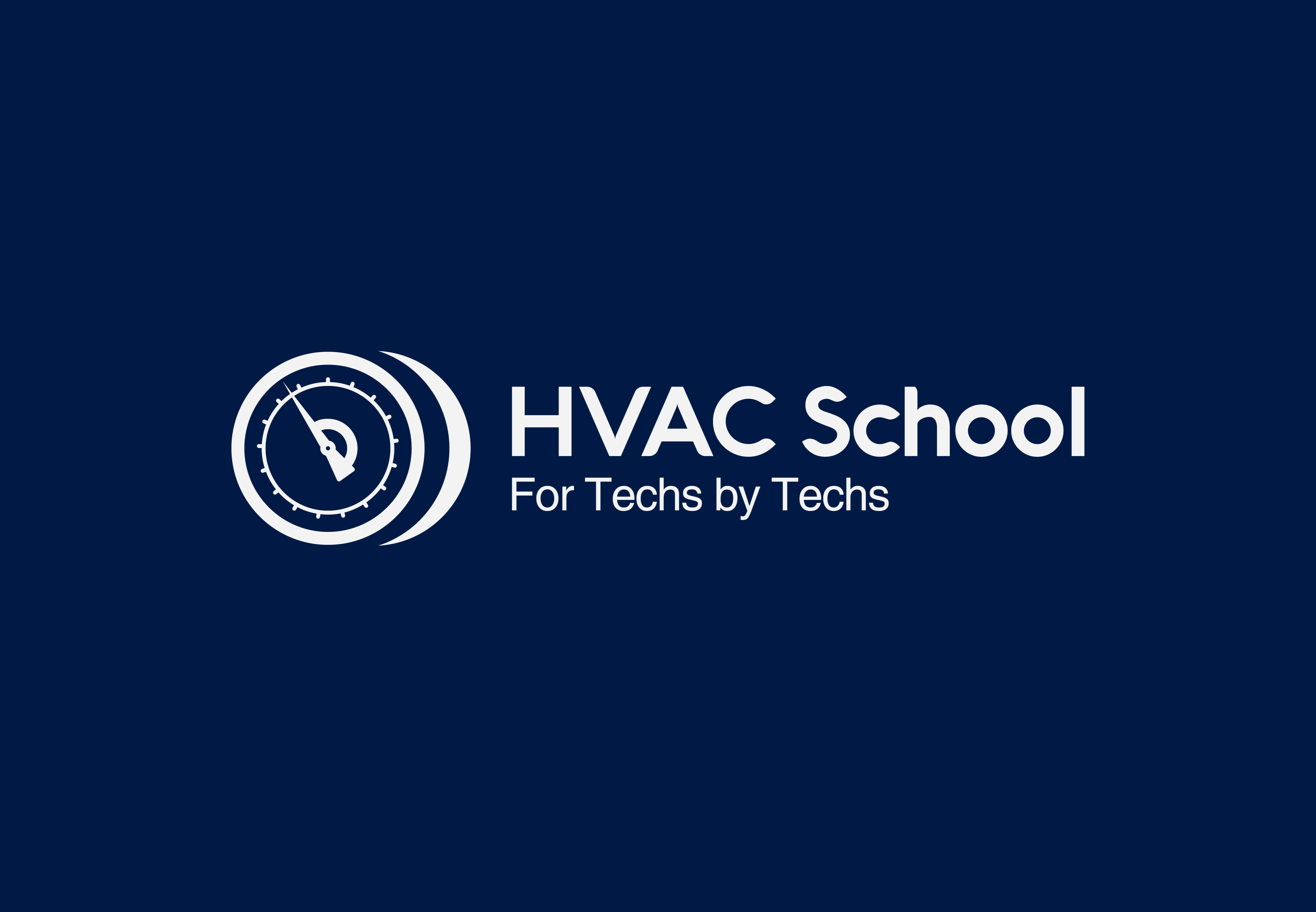
Andre Patenaude talks to us about the basics regarding CO2 as a refrigerant, CO2 refrigeration and Transcritical booster systems. Find out more at HVACRSCHOOL.com/CO2
Read more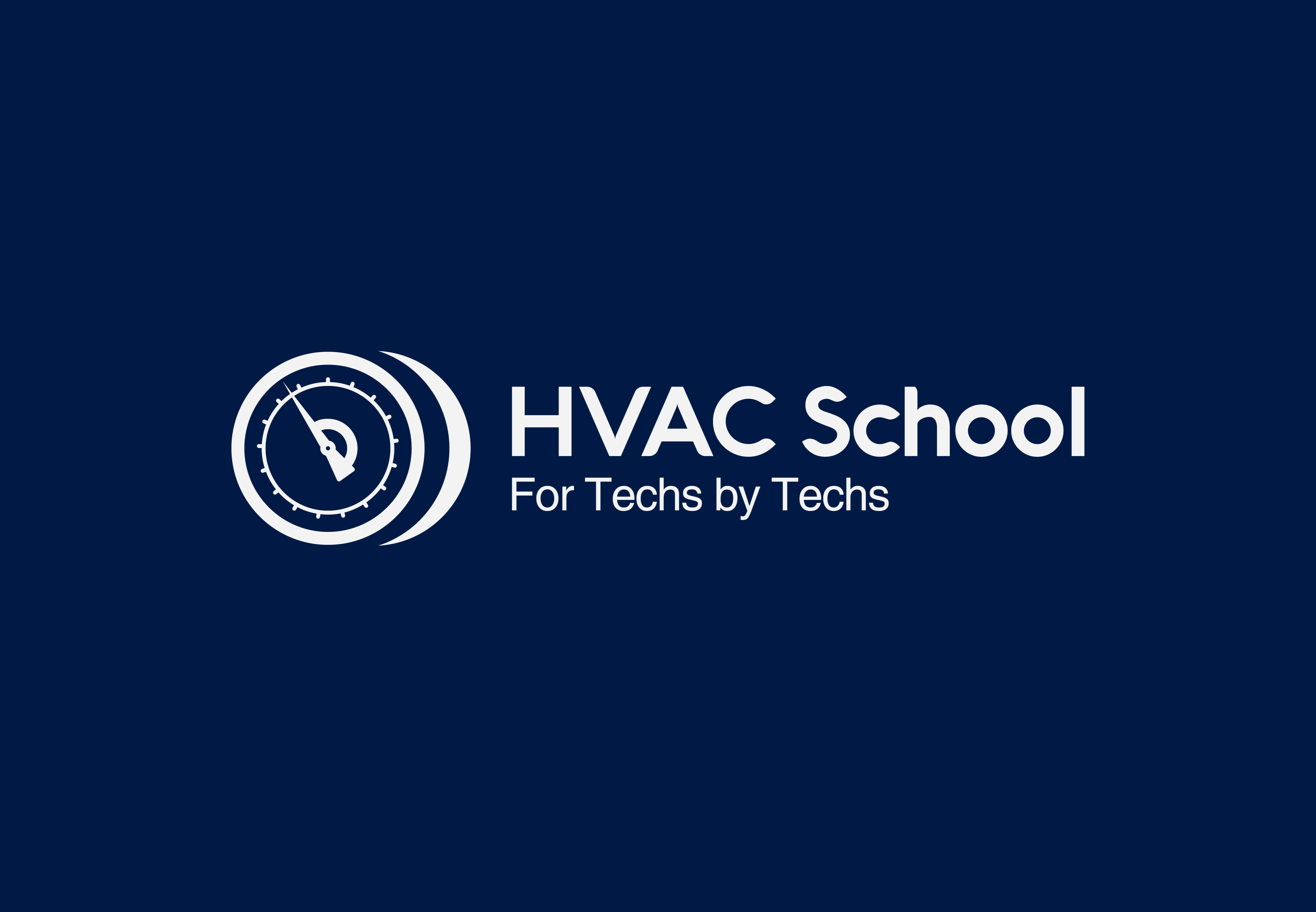
In this episode Bryan and Bill Spohn talk about 10 years of TruTech tools and we read some of the comments from the big 10 year giveaway.
Read more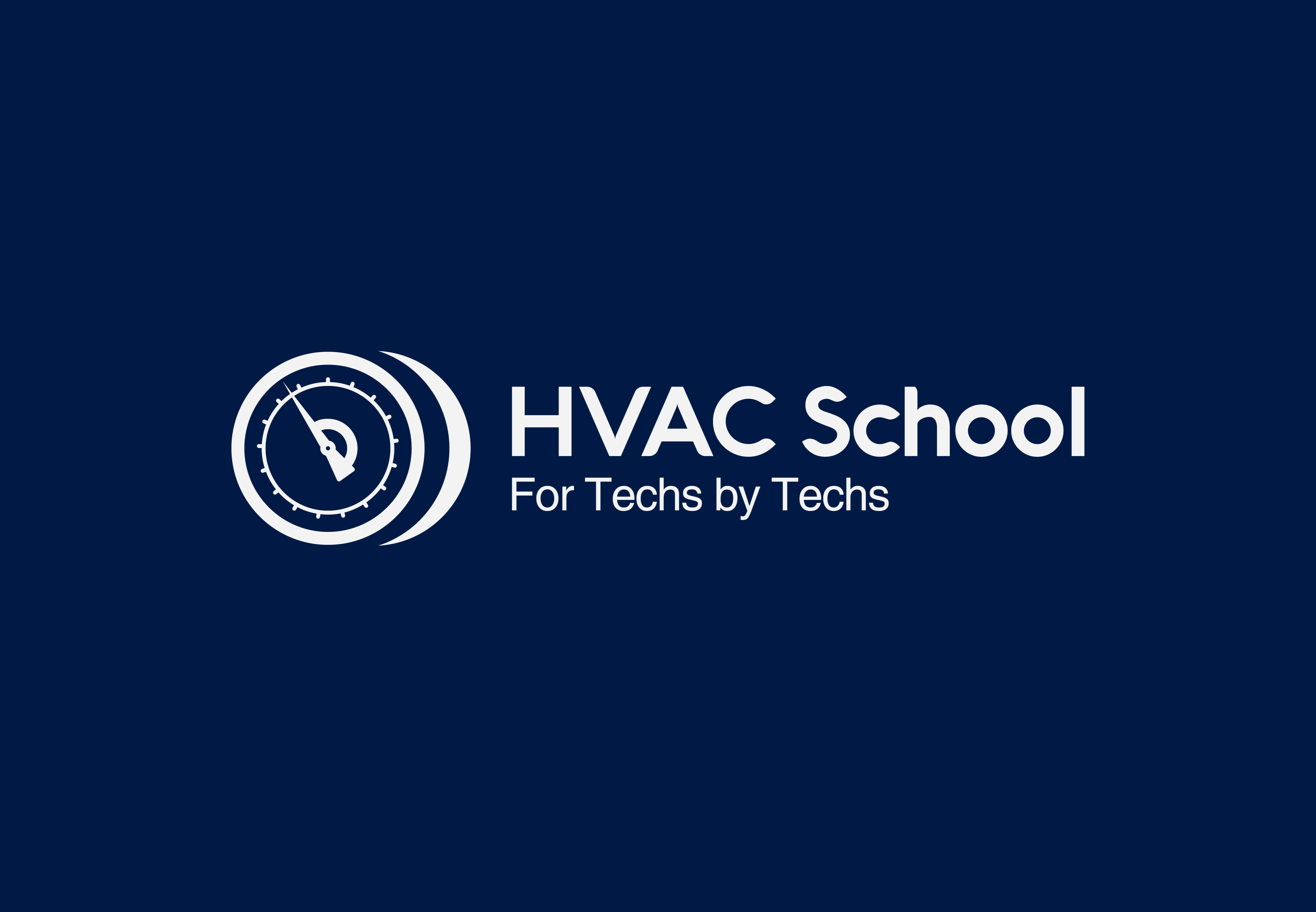
In this episode Bryan talks with Adolfo Wurts about advances in technology and automation and how it has and will continue to impact the trade.
Read more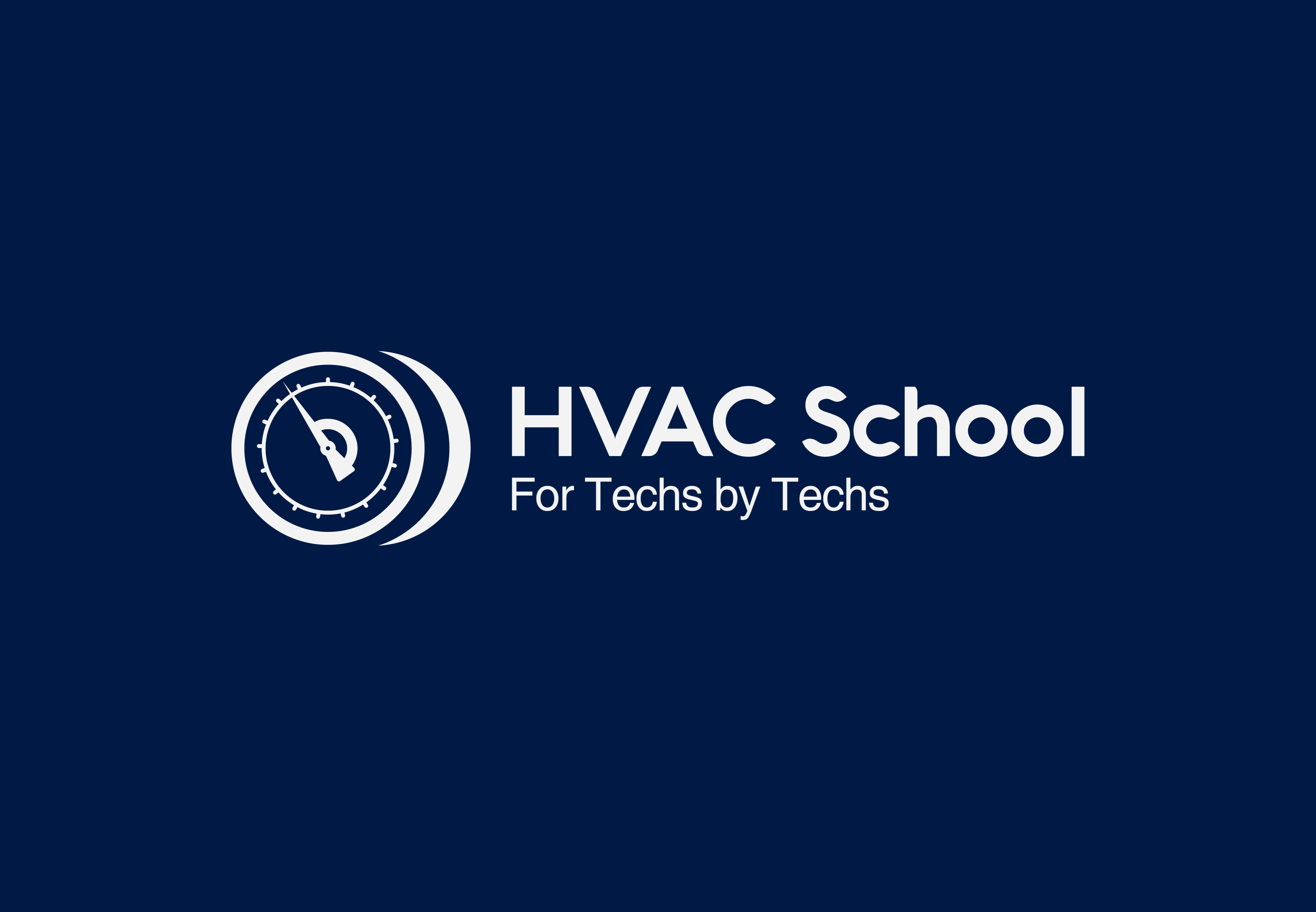
Jeremy Arling from the EPA discusses the new changes to the EPA 608 rules and regulations including recovery, evacuation and much more.
Read more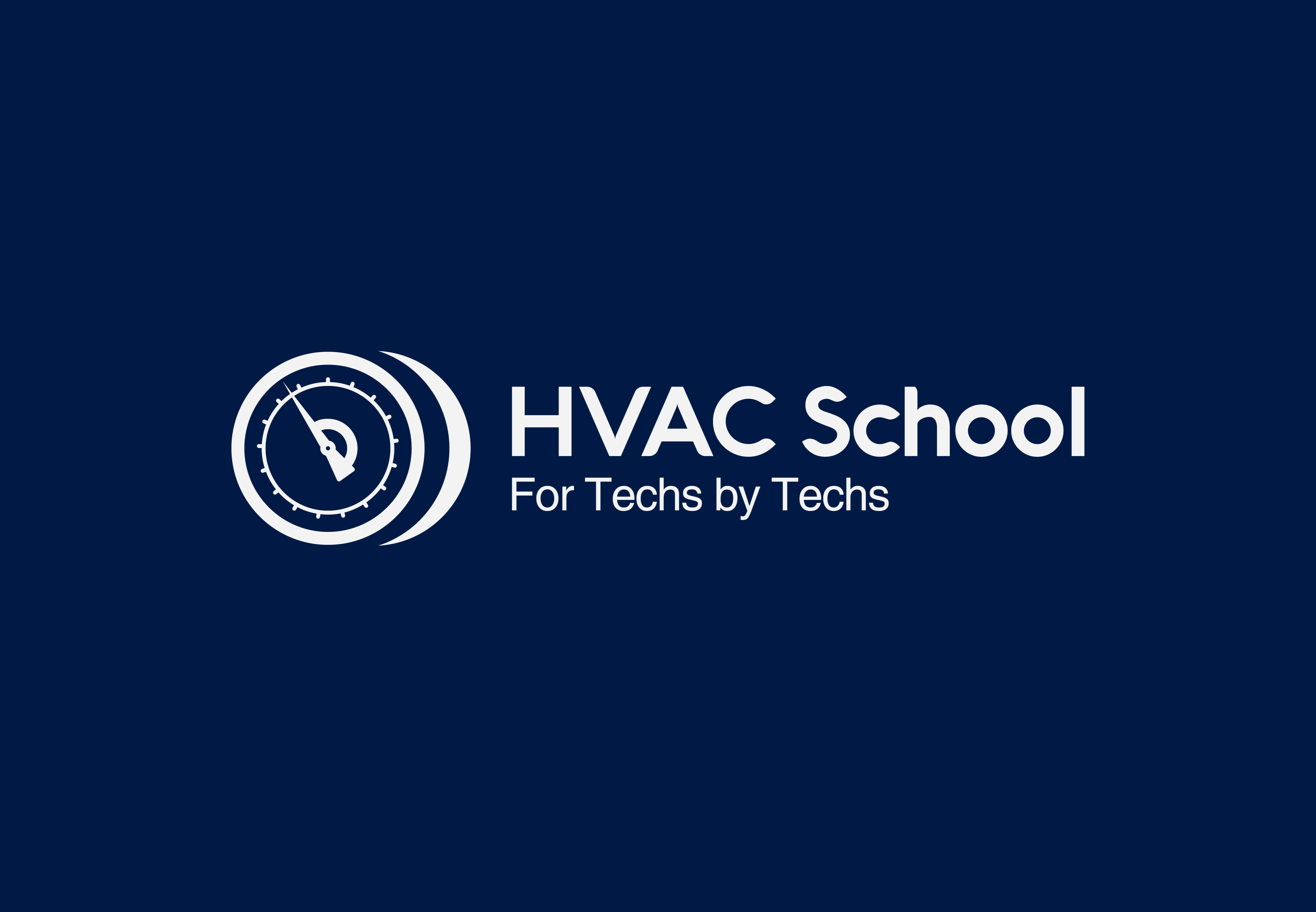
In this episode, Jim Bergmann talks about evacuation, moisture, and vacuum best practices
Read more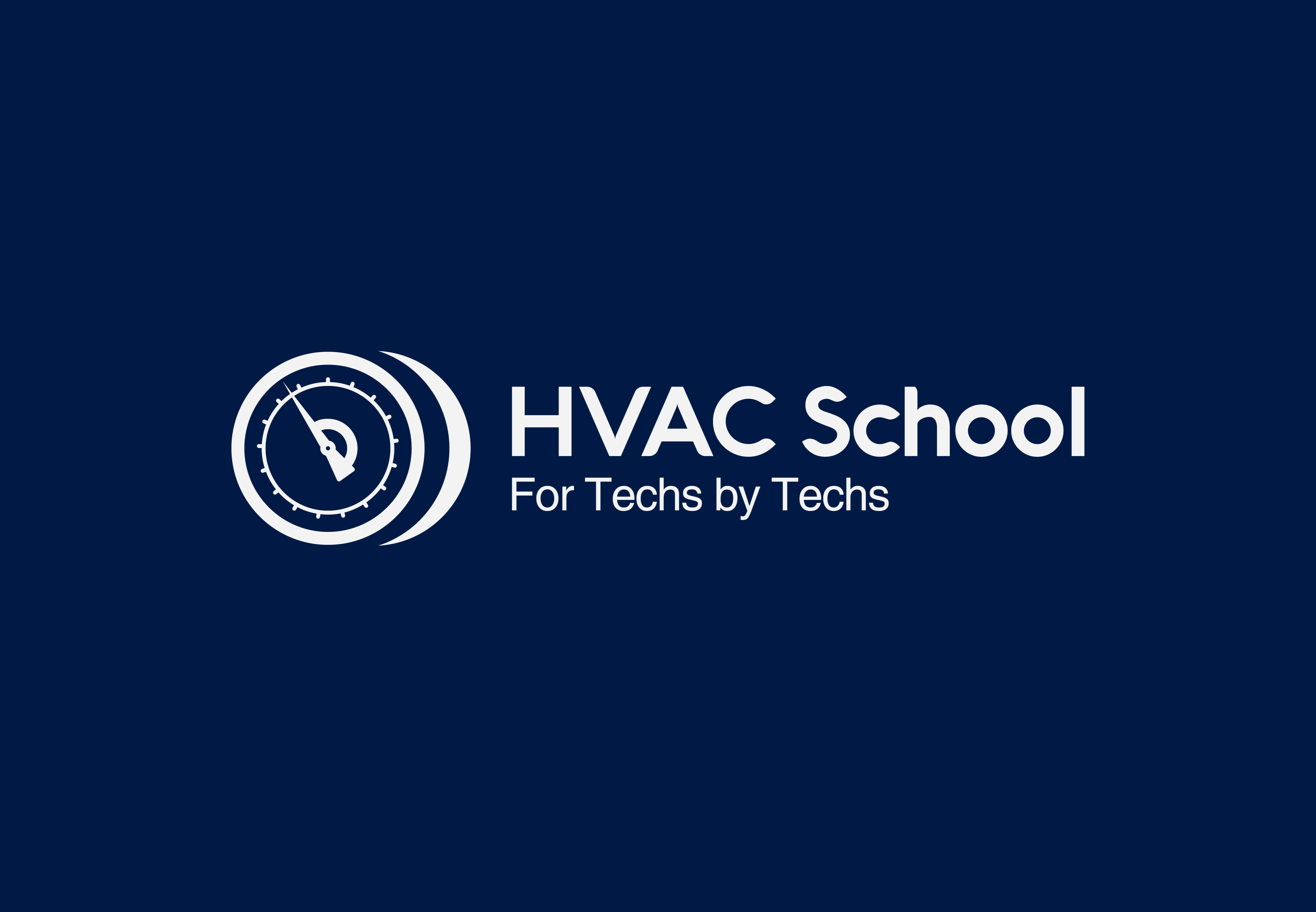
In this episode we talk humidity, dry bulb, wet bulb, grains of moisture, enthalpy, weather and so much more.
Read more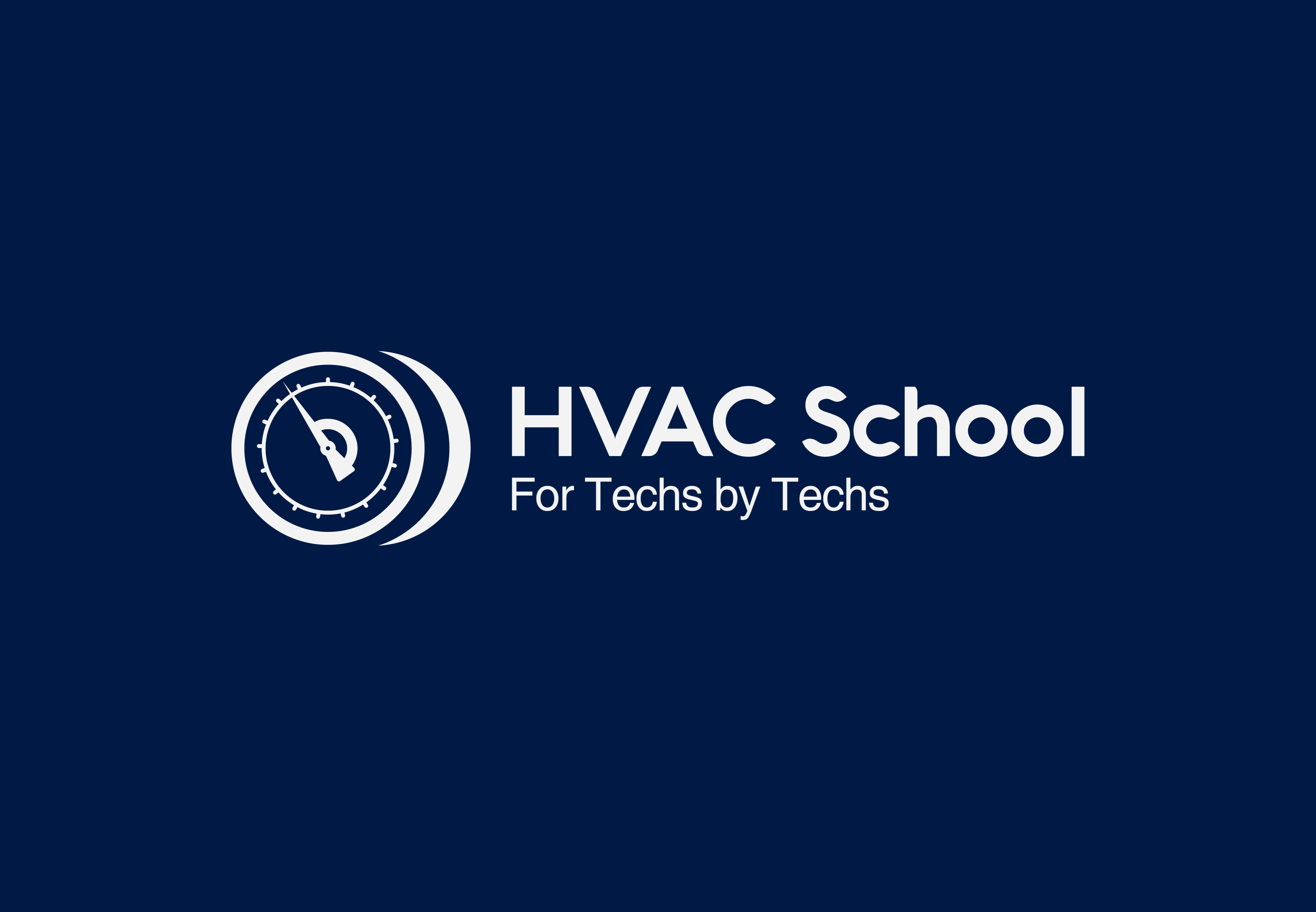
In this episode of The Hvac School Podcast Jim Bergmann and Bryan talk about measuring Voltage drop and how it can prevent “bandaid” repairs.
Read more