April 2017
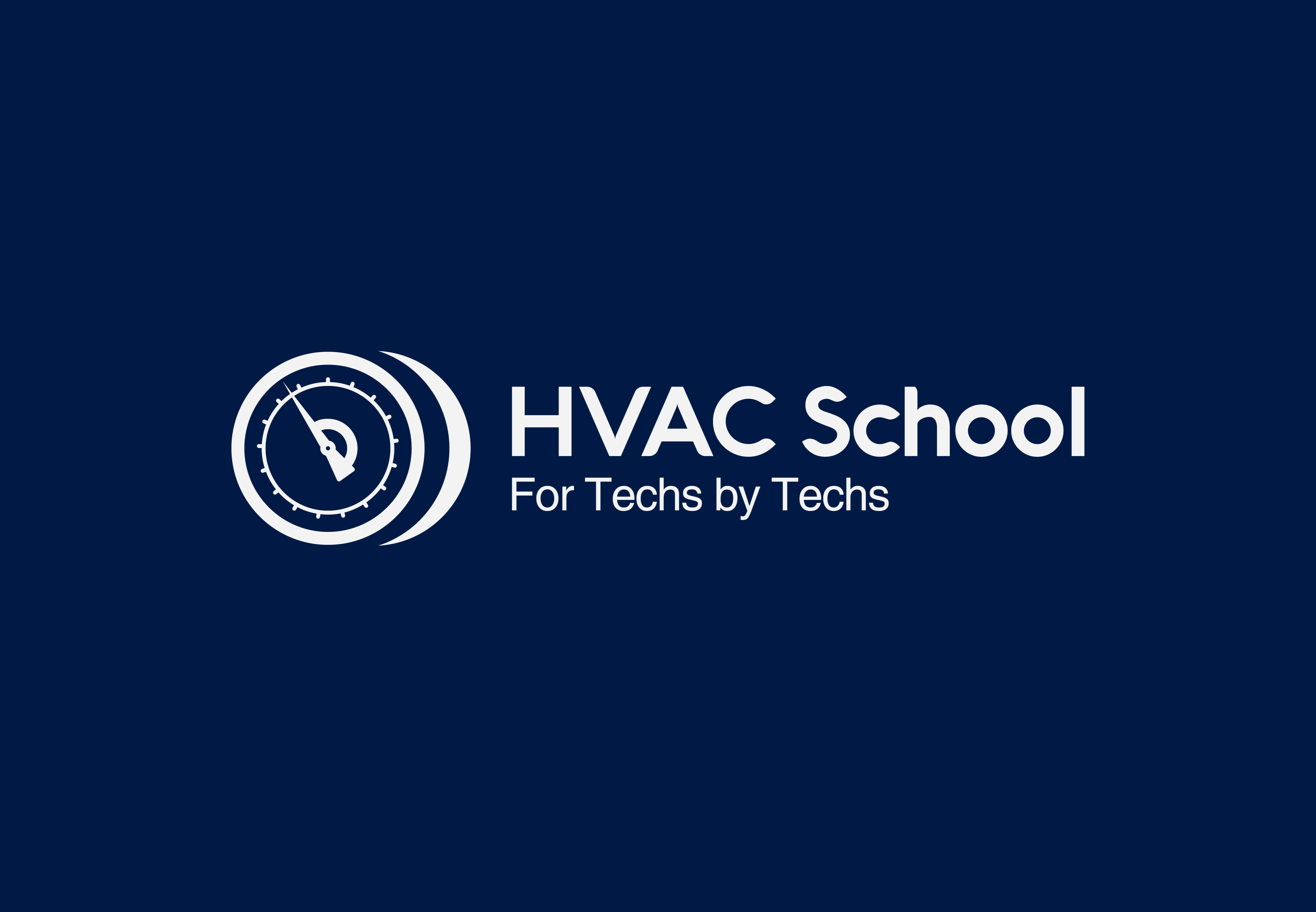
In this episode of the podcast Jeff walks Bryan through a new chiller startup step by step
Read more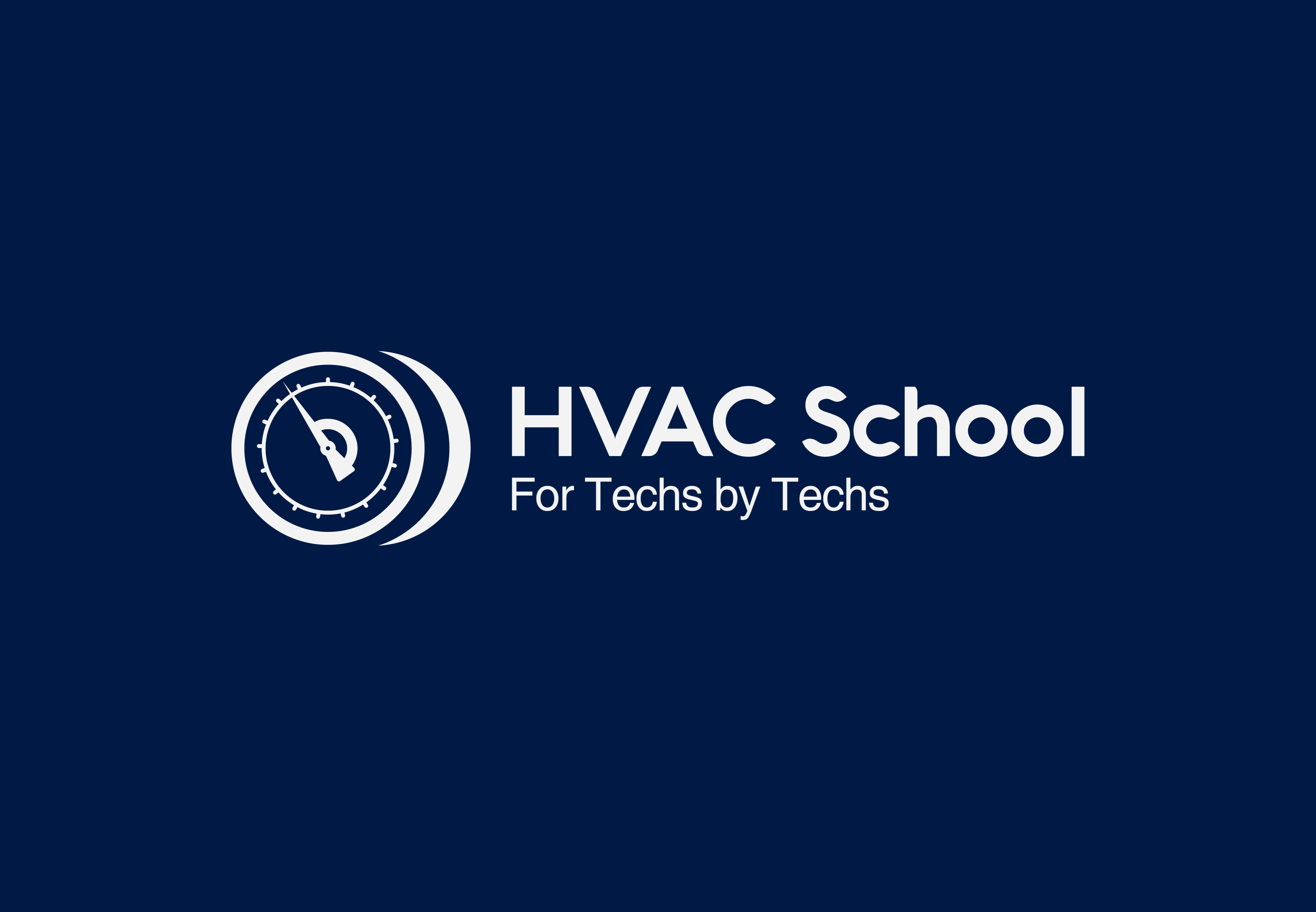
In this episode Bryan talks with James Bowman, technical director at Rectorseal, in person at the HVAC Excellence conference about hard start kits, potential relays and more.
Read more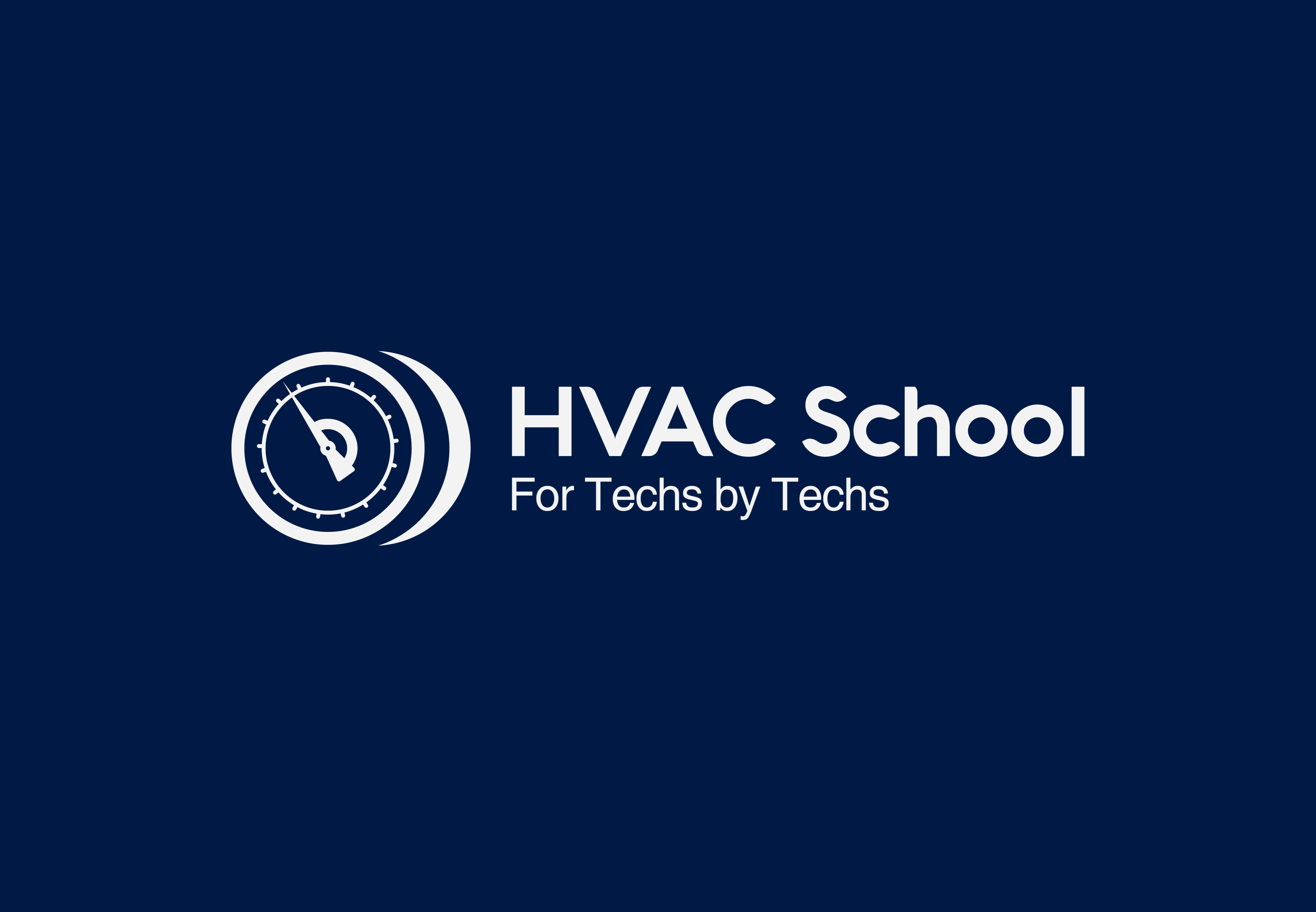
In part 2 of this conversation we go through the condensing unit and wrap up the call with our no fluff customer service best practices.
Read more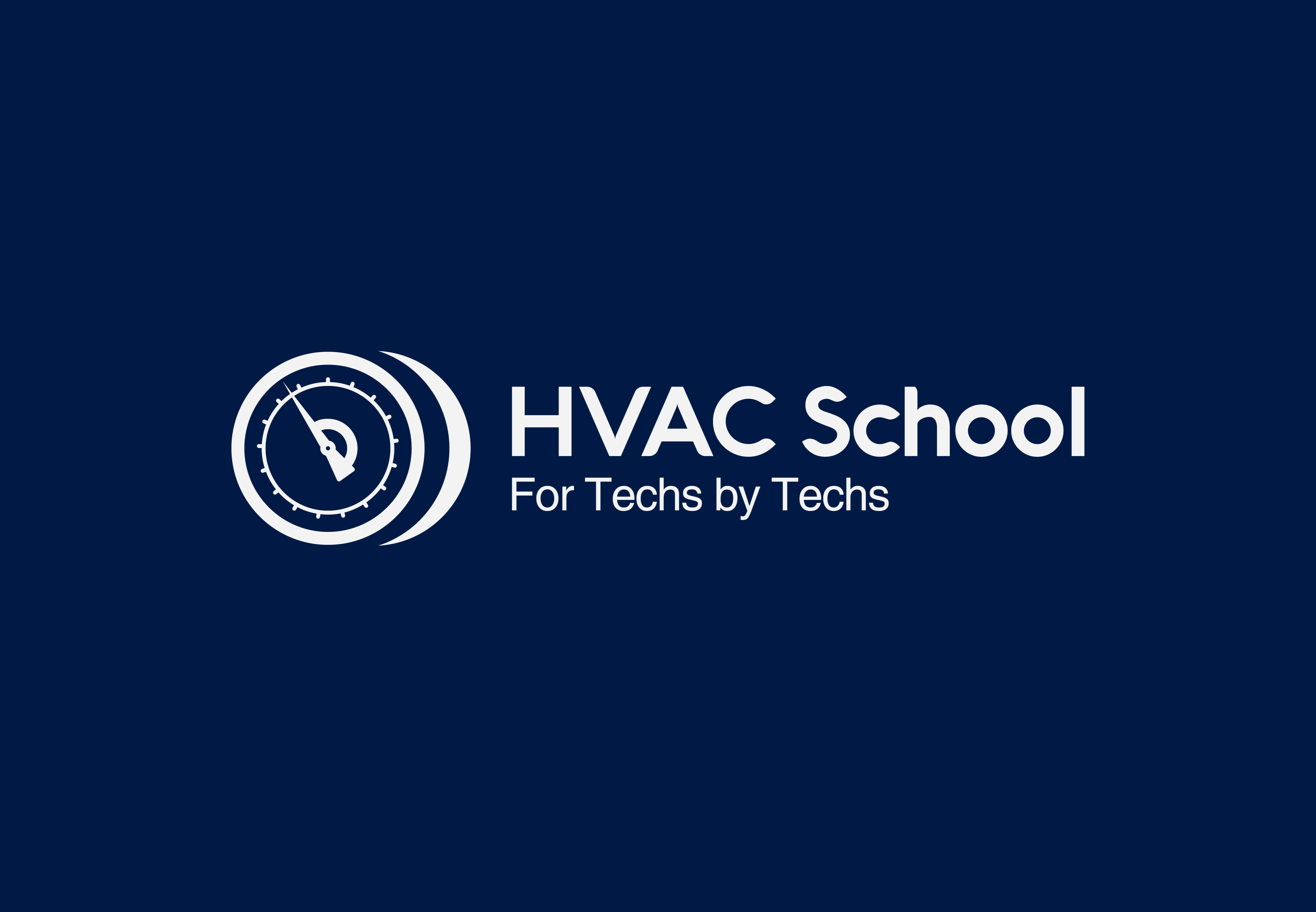
This is part 1 of 2 on the soft skills practices of approaching and completing a residential service call in the best manner possible.
Read more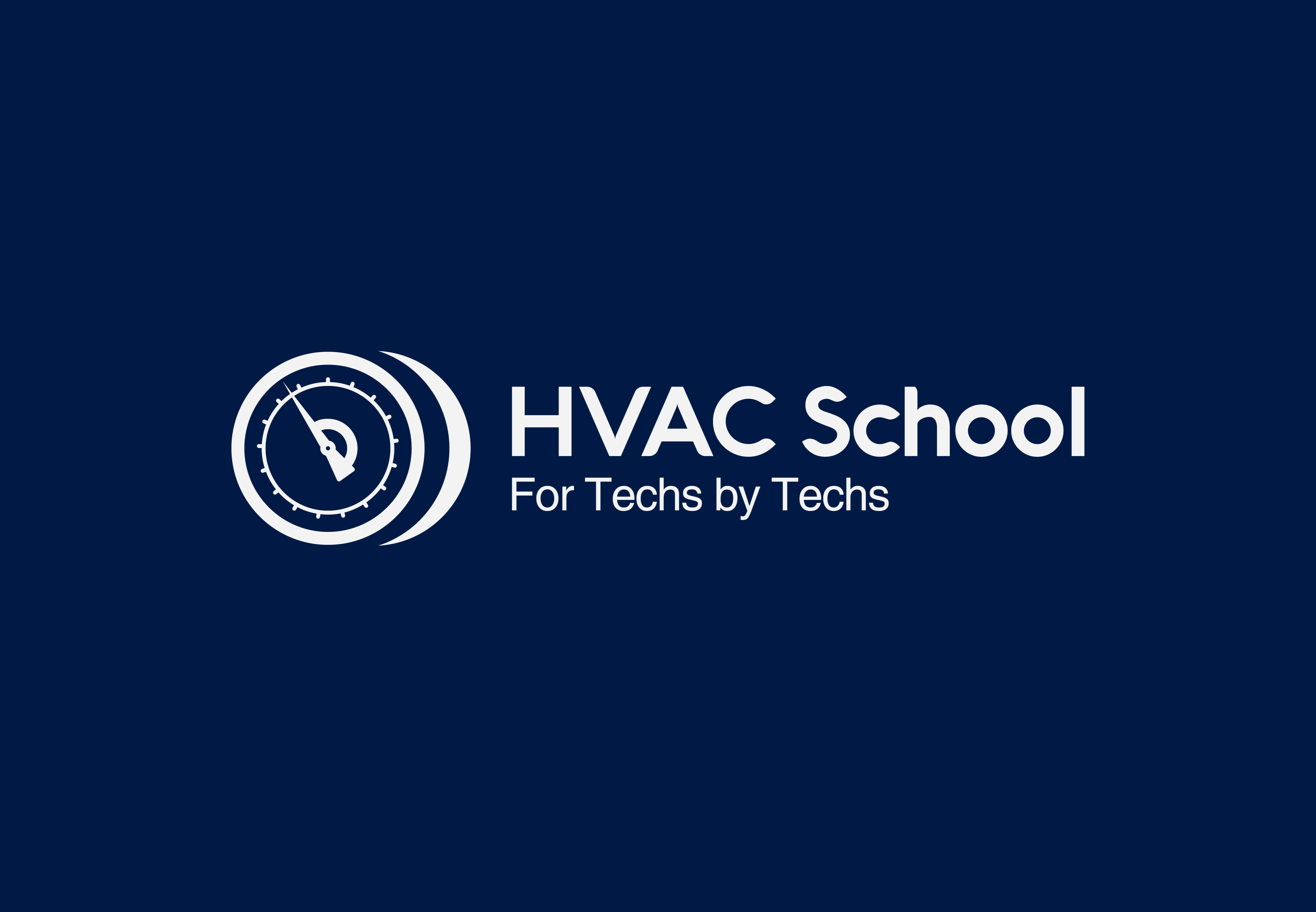
In this episode we talk about some myths related to bonding, grounding, neutral and equipment ground
Read more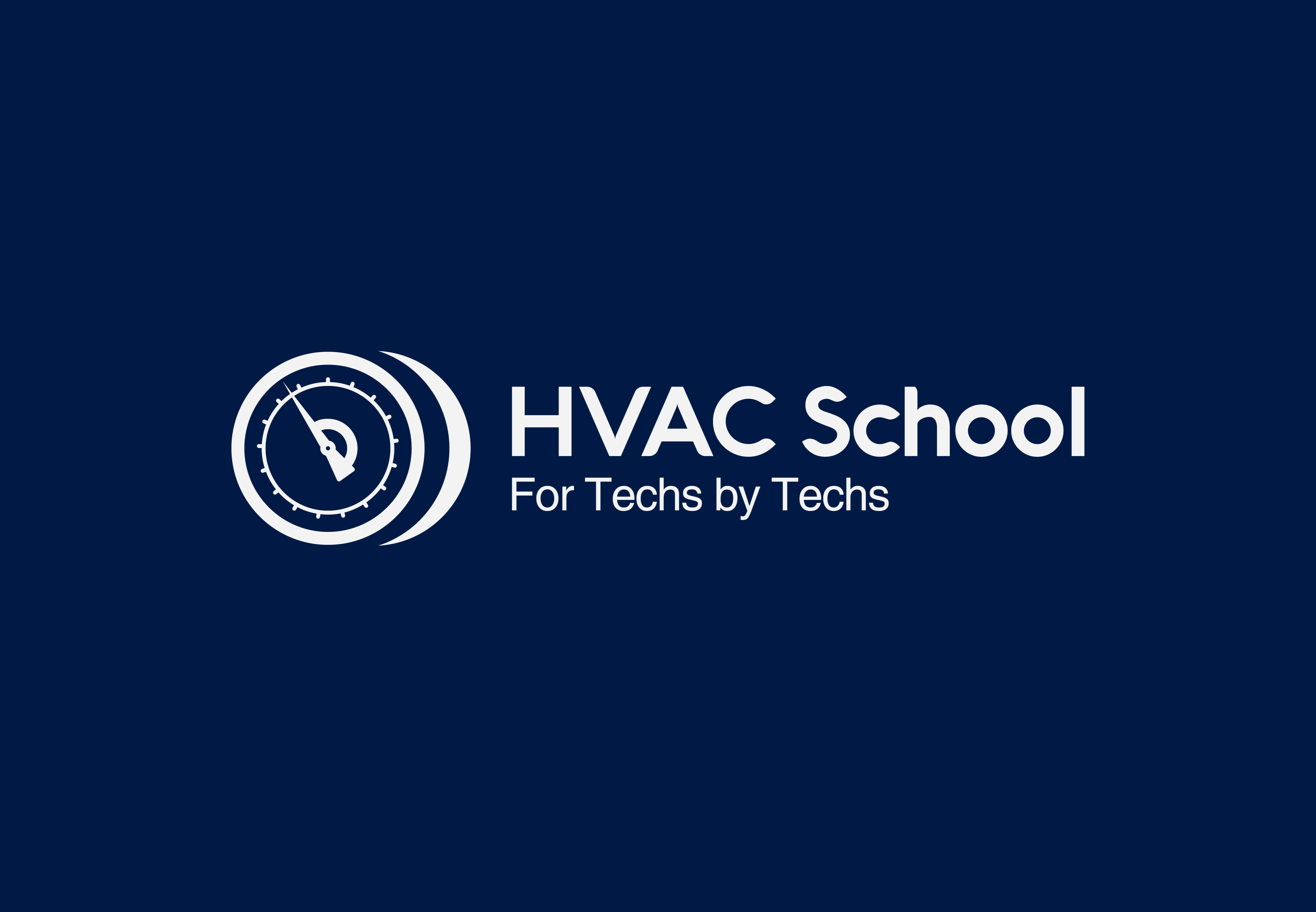
We talk to Nick Messick about some ice machine basics and when and when not to call tech support.
Read more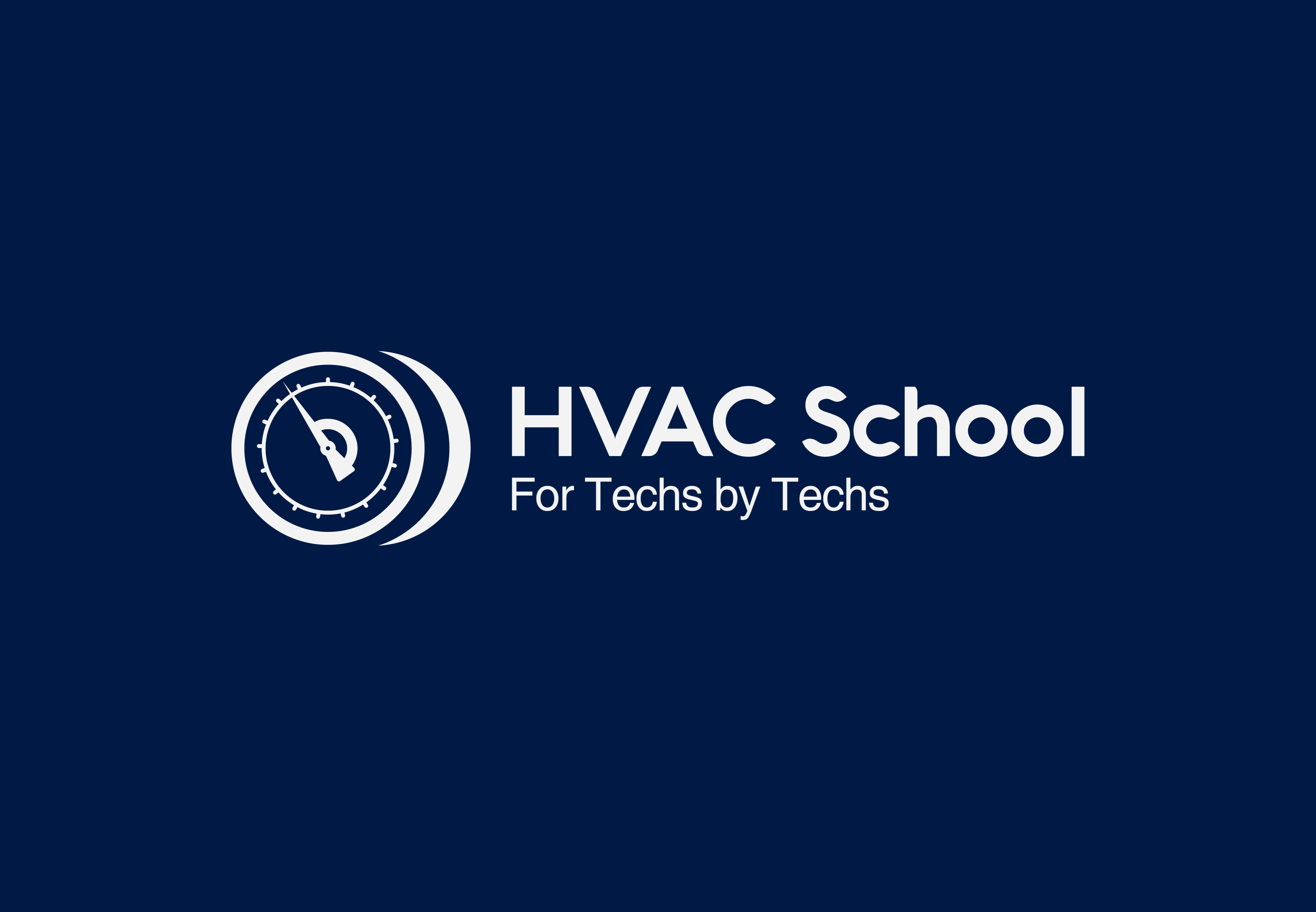
In this episode we talk the National Electrical Code, Wire Sizing, Breaker sizing, wire insulation rating, derating conditions and much more.
Read more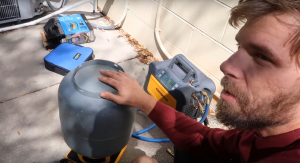
Recovery is the removal of refrigerant from a system to either store and send in for recycling or to reintroduce back into the same system. Here are some top tips – Make sure your tank is empty and evacuated to 300 microns if you plan to return the refrigerant back into the system. Never mix […]
Read more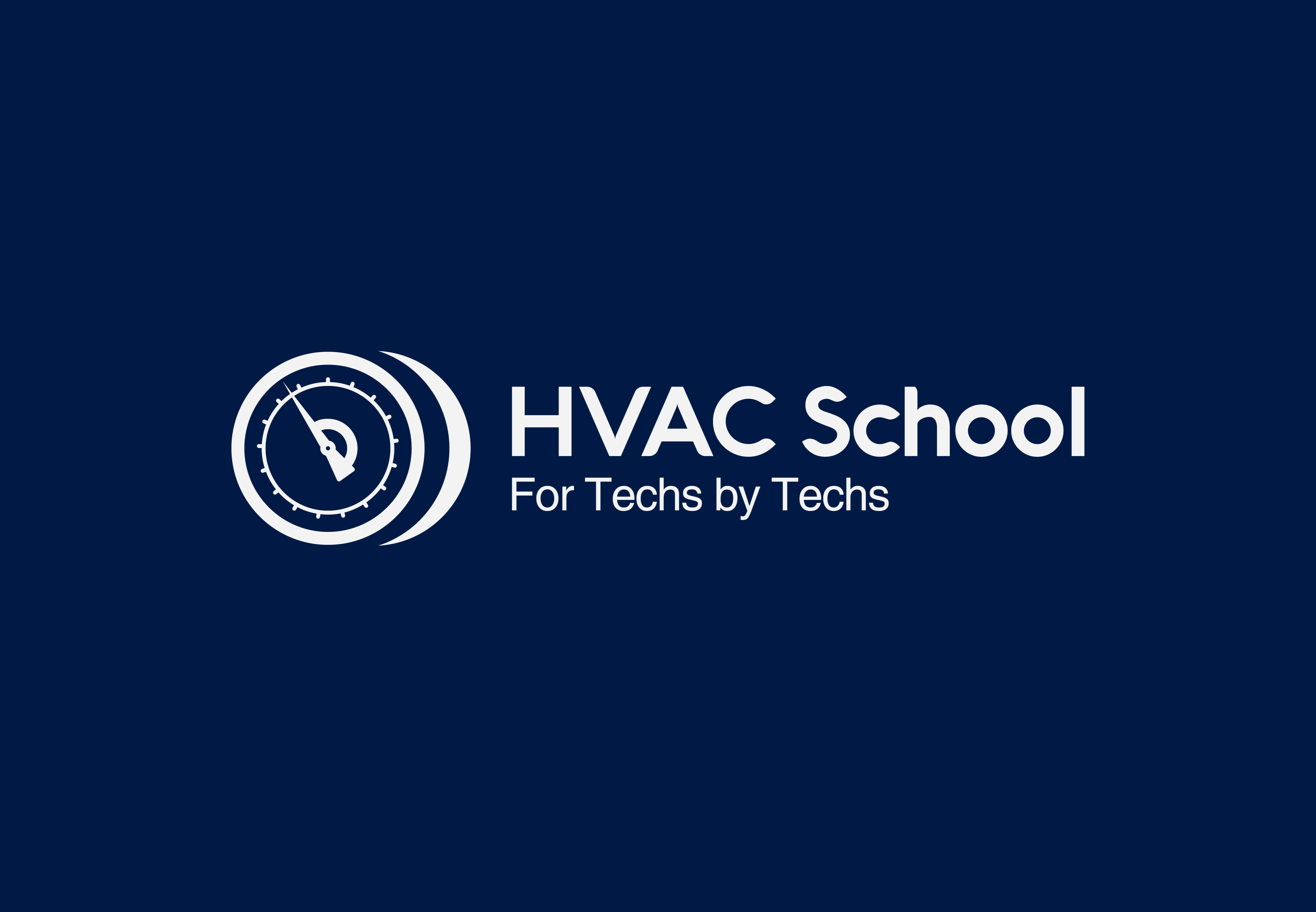
In this episode Bryan talks with Bill Spohn from TruTech about the TruTech story, some practical airflow measurement advice and tech vs. engineer mindset when it comes to training and testing. Participate in the 10 year anniversary giveaway and use the offer code “getschooled” if you have any tool needs for 8% off at checkout.
Read more