February 2017
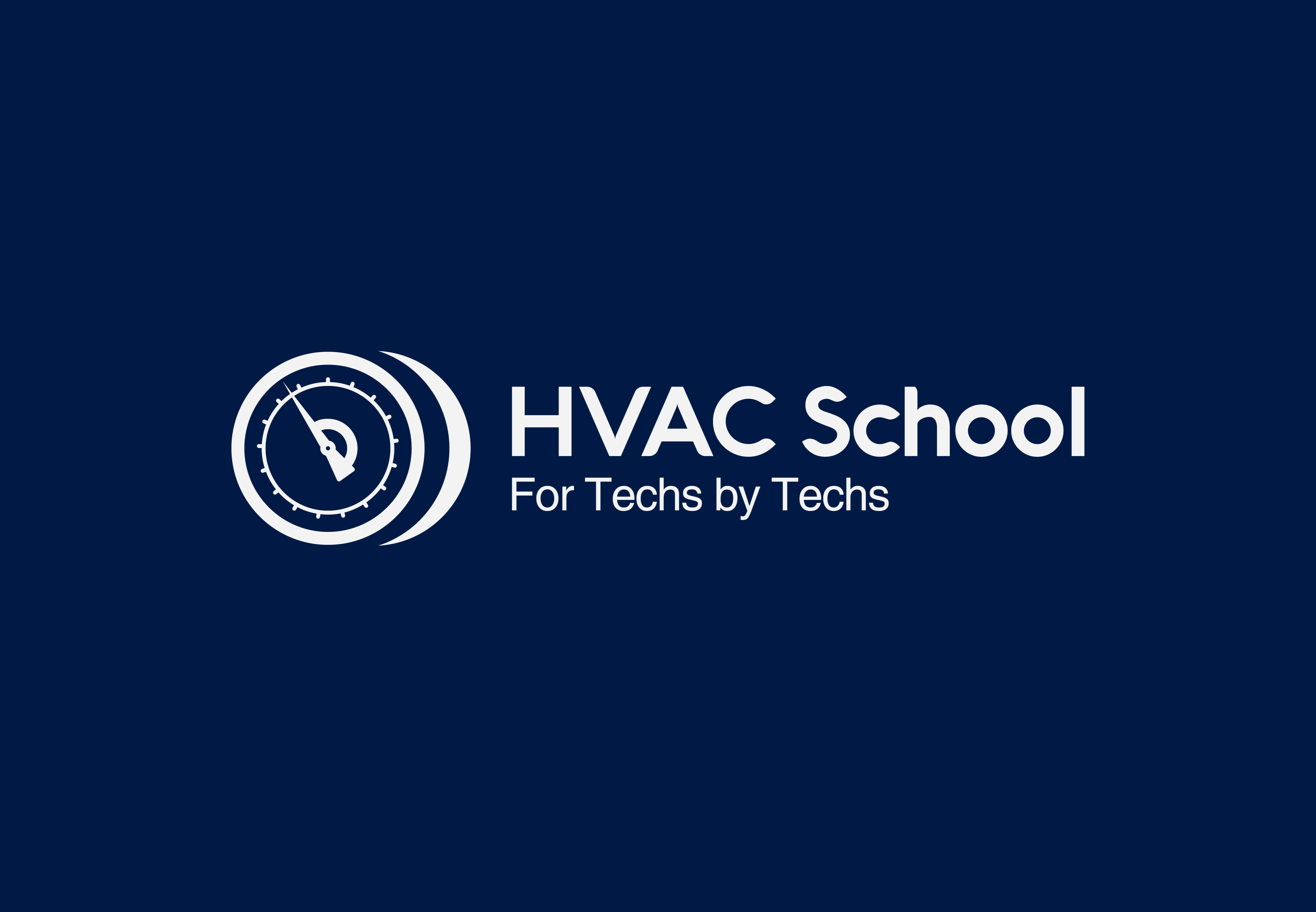
In this podcast we talk about – Condensing Temperture – Heat mode superheat – Heat mode subcooling – Saturation – Condenser Split and much more
Read more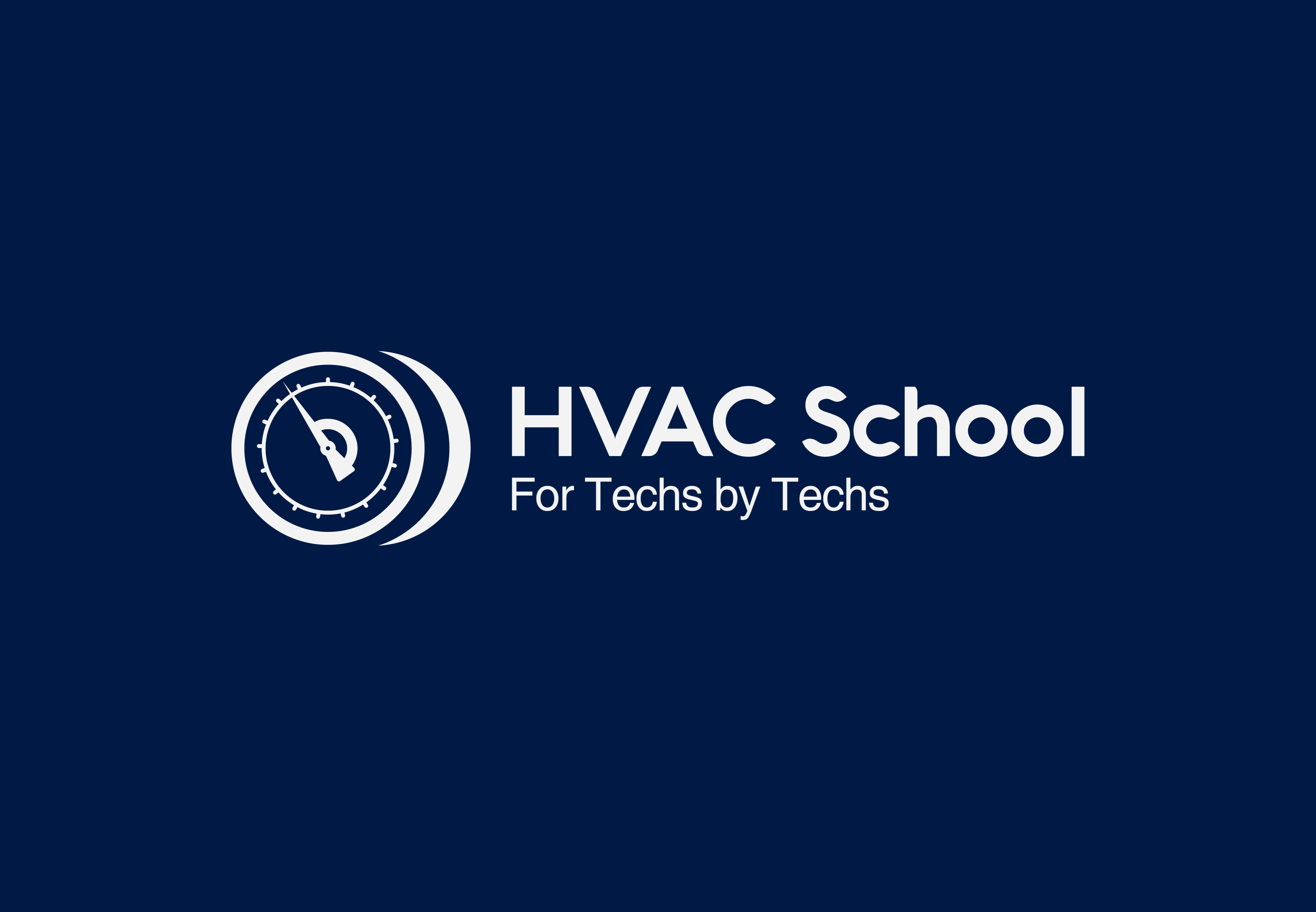
In this video Bryan talks about Heat (Enthalpy) Adiabatic cooling Latent and Sensible heat Evaporative Cooling Humidity Blower Off Delay
Read more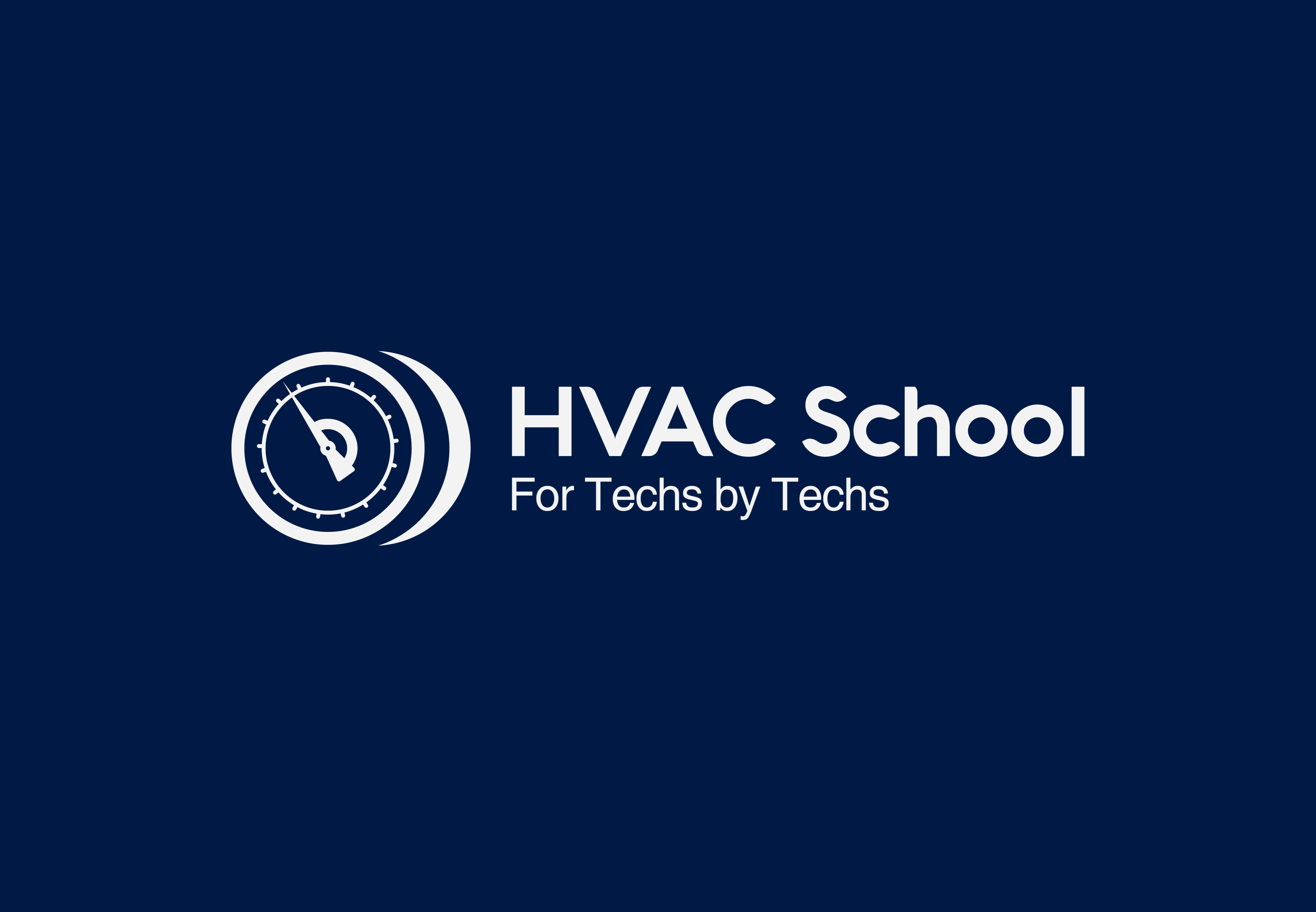
In this episode Bryan talks a bit about the air side of the system including latent and sensible, Relative Humidity, Wet Bulb, Dry Bulb and static pressure
Read more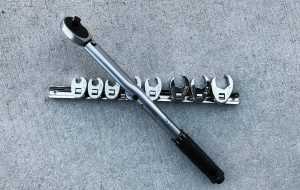
I’ve got a confession to make. I'm “that guy.” Call it OCD, call it being anal-retentive, but I'm always making an effort to be as technically correct as possible. One aspect of that effort has been the use of torque indicating or torque limiting tools when tightening fasteners. It started after I put new valve […]
Read more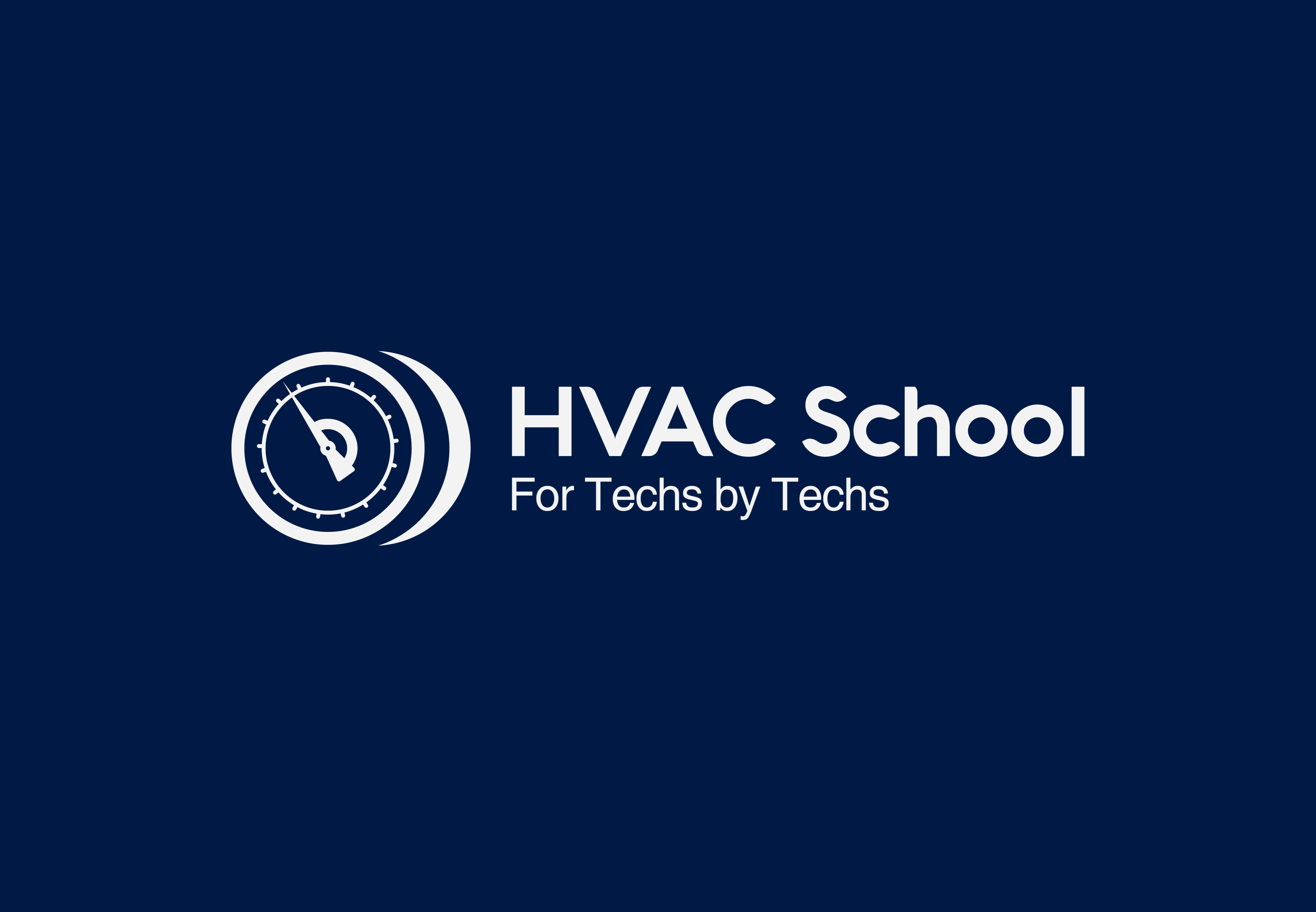
In this first episode of a new series Justin talks about the calls he is doing before and after he does them, giving us a look inside the van of a senior HVAC tech.
Read more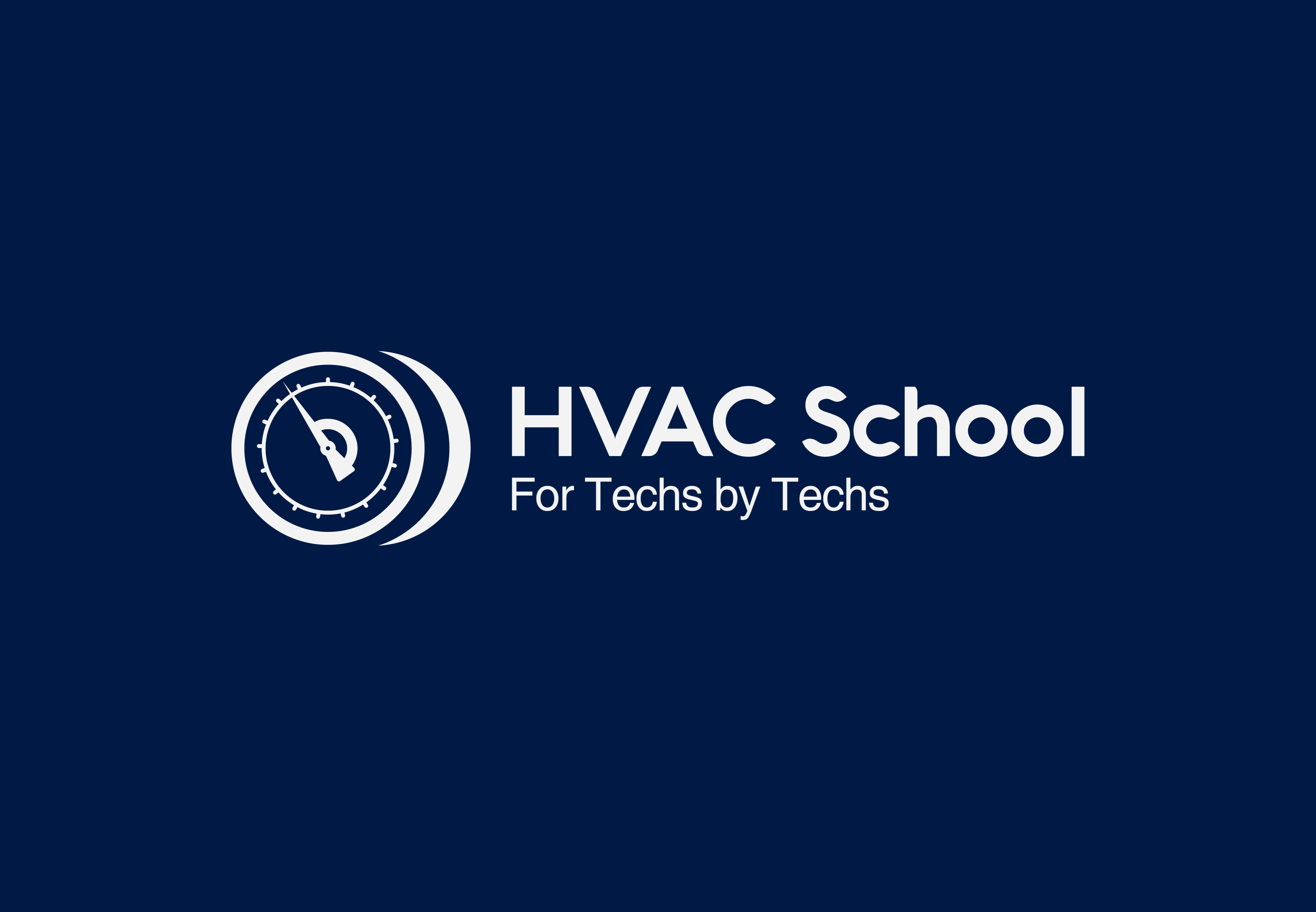
In this live video Bryan talks about Flowing Nitrogen Reasons techs give not to flow nitrogen Reasons that some cases create more carbon than others Demonstration video by Tim Bagnall
Read more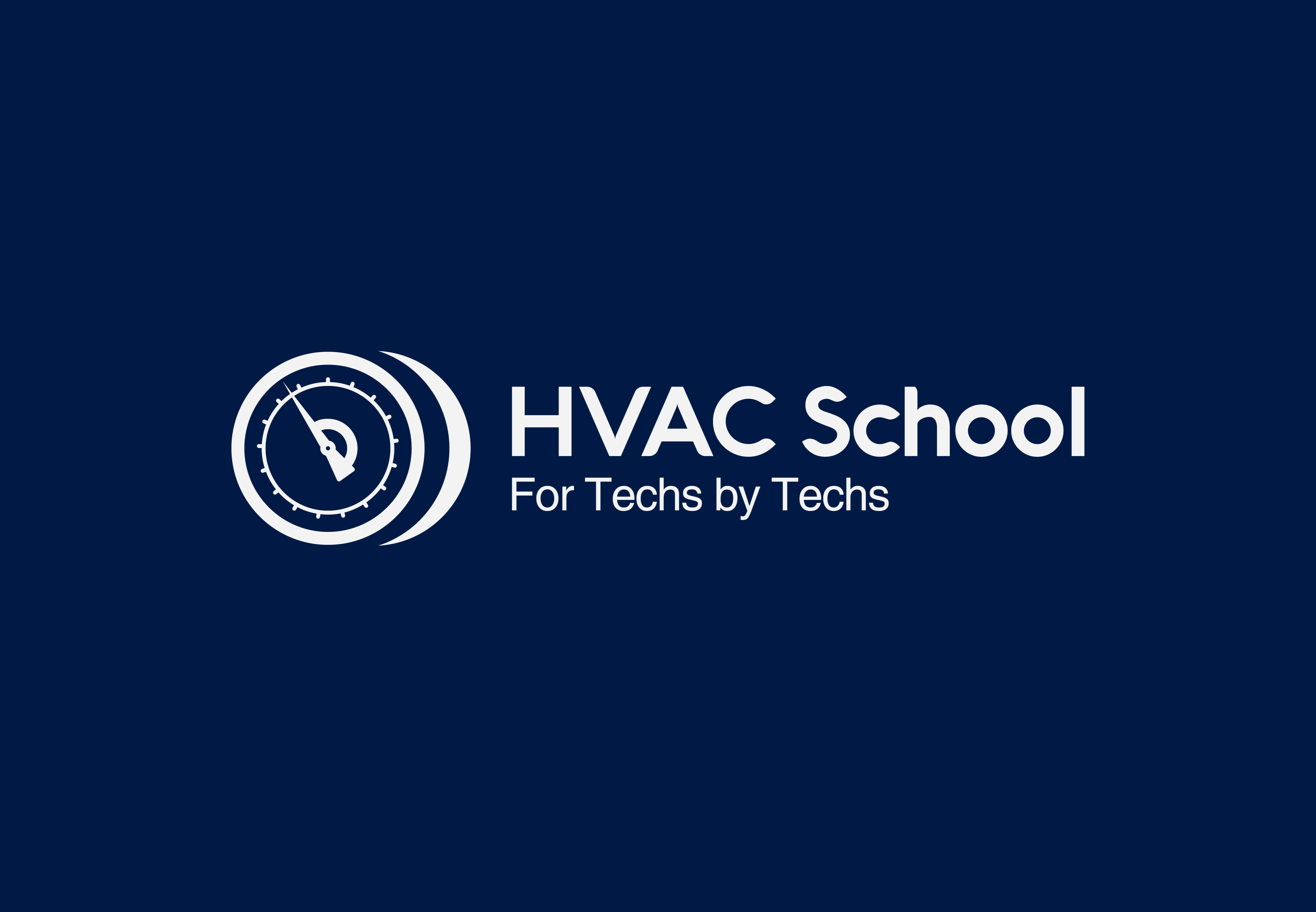
In this video Bryan talks about Refrigerant Blends The reasons for retrofit The drop-in fallacy Oil types Oil Miscibility Temperature Glide Capacity change Refrigerants to consider R427A R438A R422D R407C & A Helpful Links Choosing the right retrofit (EPA) Honeywell Retrofit Guidelines Retrofit with R438a by “The Professor”
Read more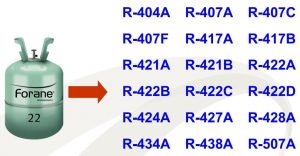
The price of R22 is getting ridiculous, and one of the #1 requests I have been getting is for recommendations on other refrigerants to use in place of R22 and best practices, so here we go. No, you shouldn't mix There are NO refrigerants that you are supposed to use to top off an R22 […]
Read more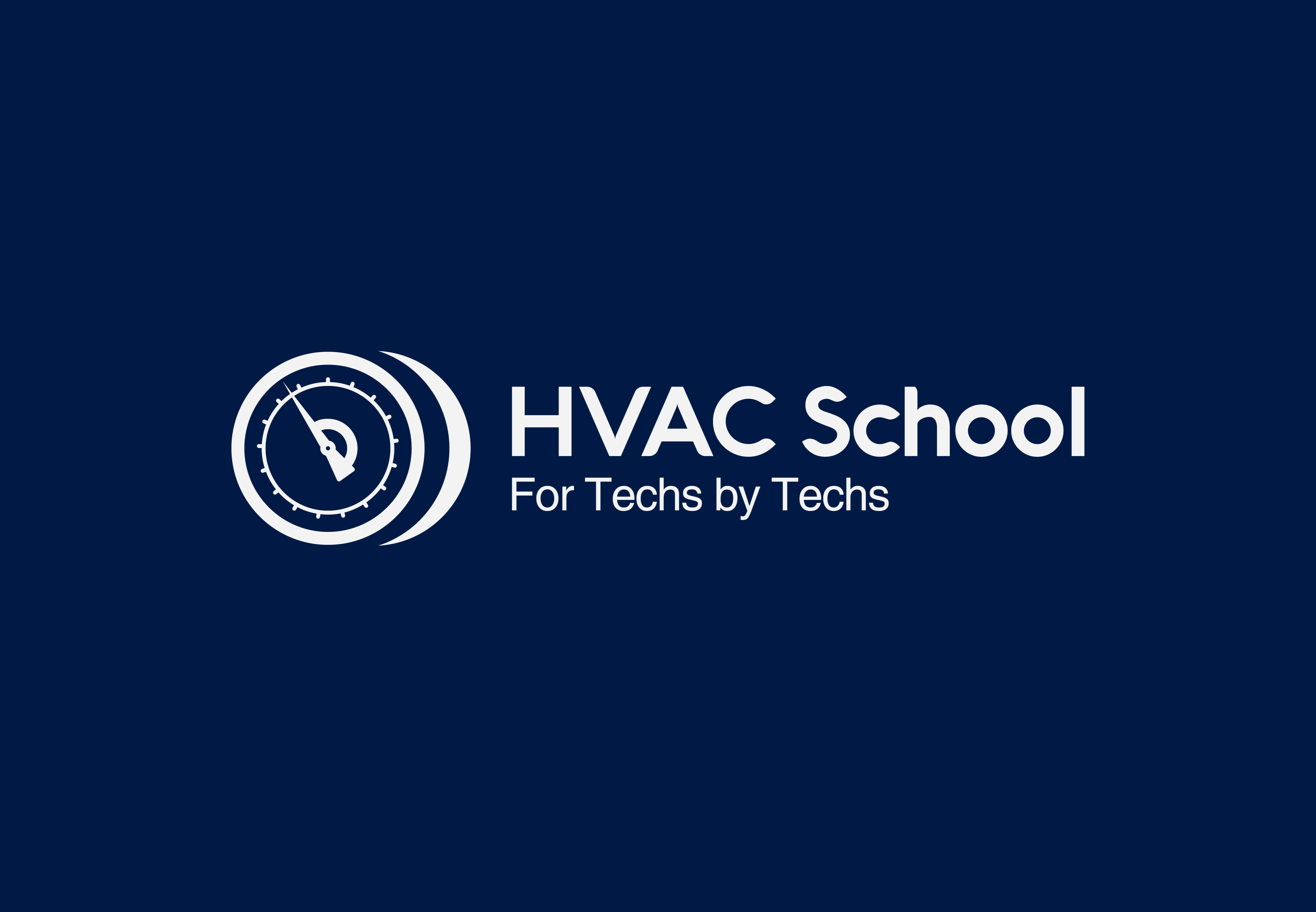
In this episode of the HVAC School Podcast we talk about – – Carrier's bypass economizer – Hard Start Kits – StayBrite #8 – Discharge Line Temperature – Coremax Valve Cores – Notched Belts – Motor Temperature ratings and much more……
Read more