November 2016
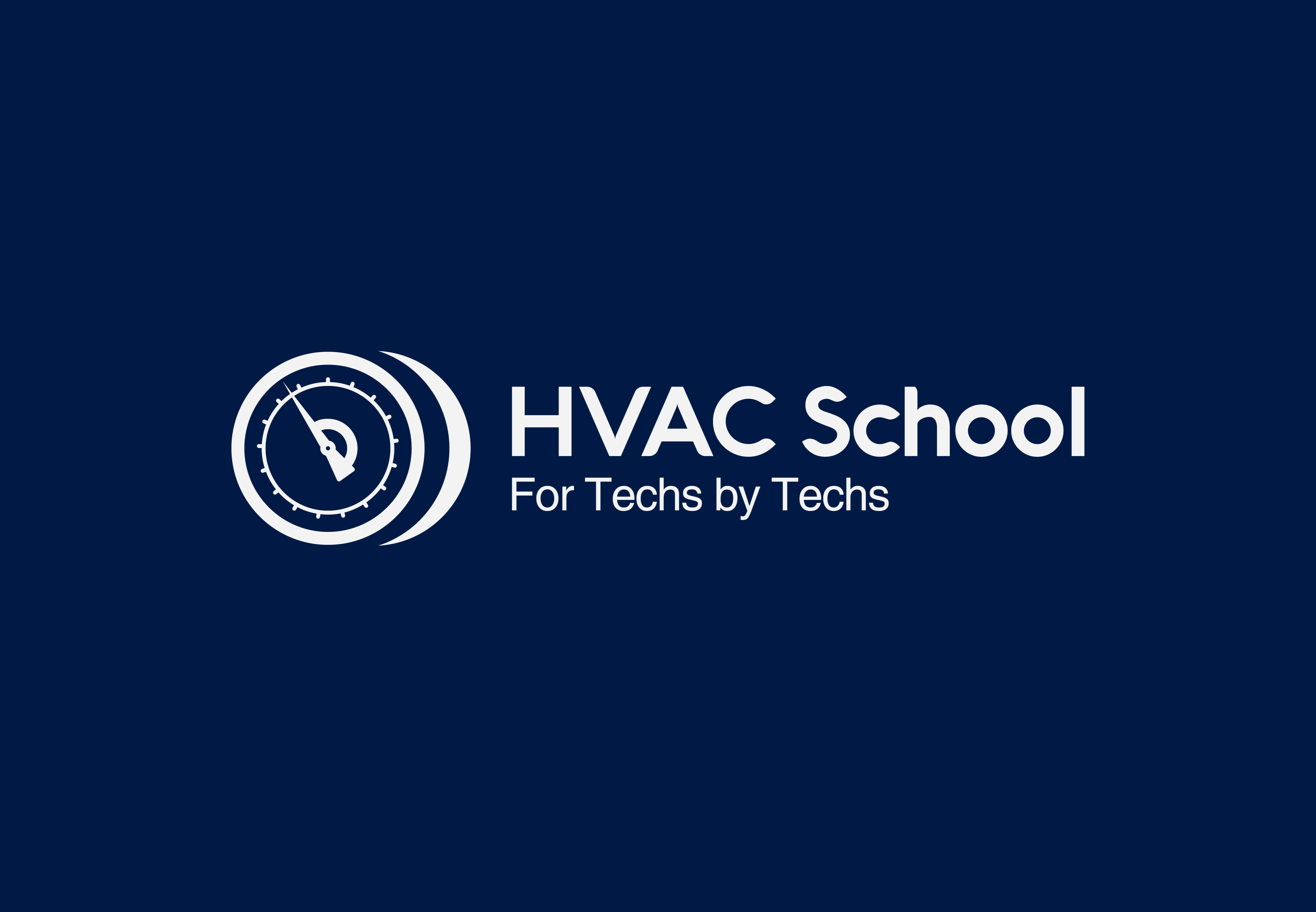
In this episode we talk through some electrical basics. Including potential difference, motor leads, capacitor basics and much more.
Read more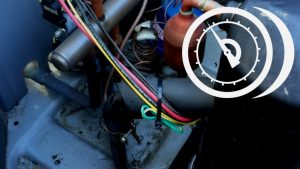
There are a few important things that I suggest checking on every service call to reduce callbacks and increase customer satisfaction. One of them that often gets missed is preventing wire rub-outs. One of my area managers and experienced tech Jesse Claerbout shot a video showing the simple step he takes to prevent major damage. […]
Read more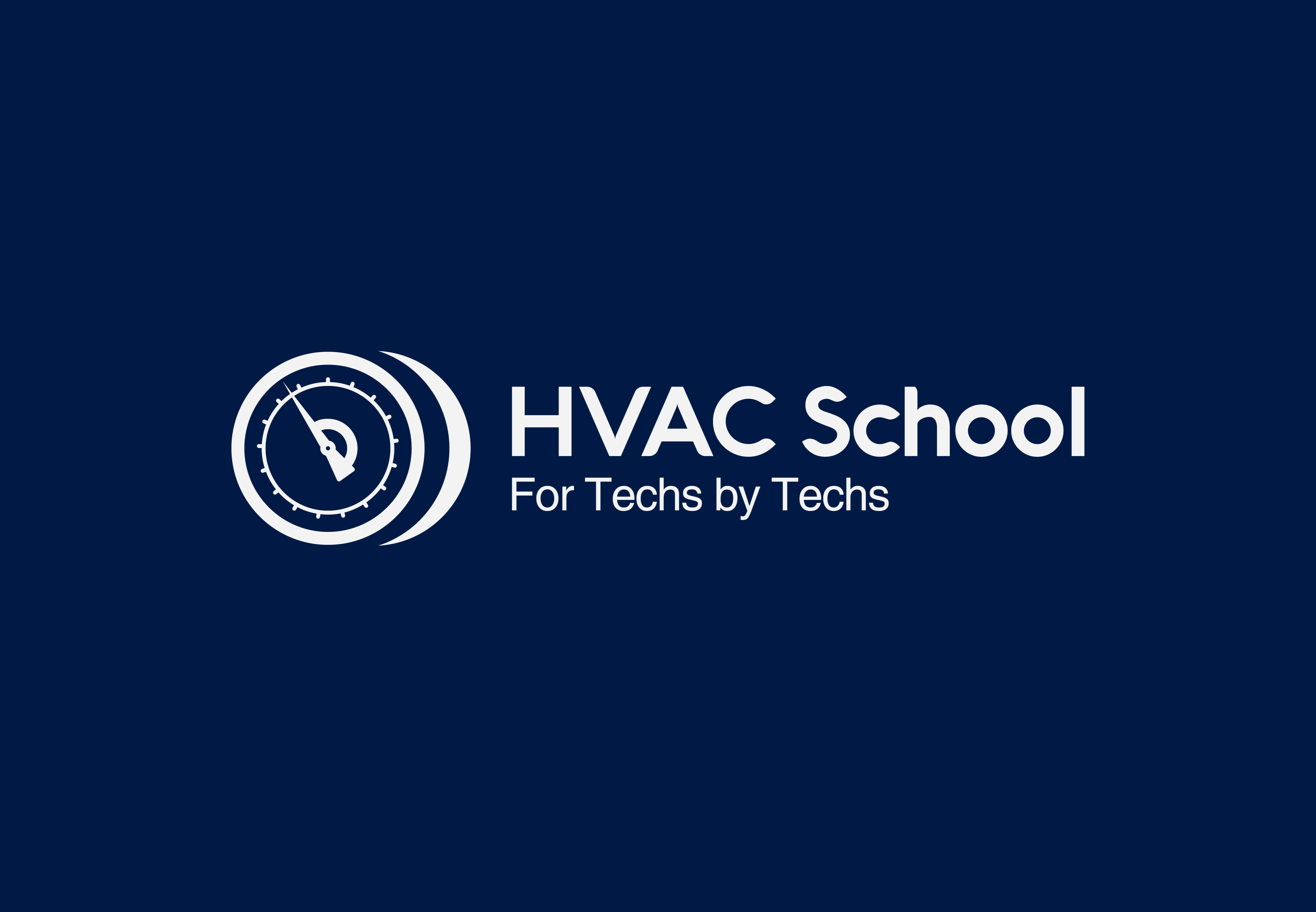
Bryan talks to Justin Skinner from Virginia and they talk about furnace sequence of operation and diagnosis tips.
Read more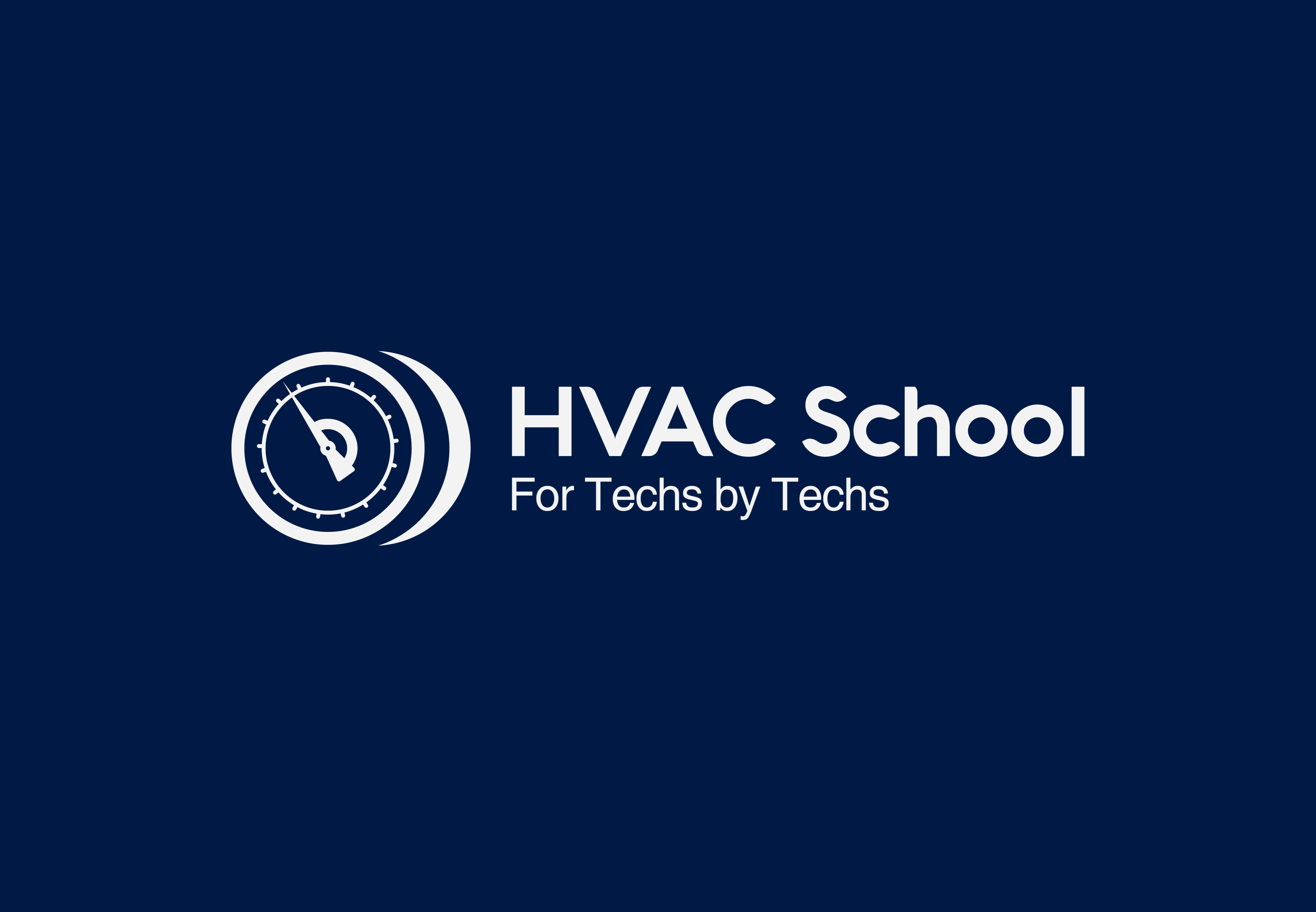
In Florida we have a lot of heat pumps and pool heaters. In this episode I talk to my staff about some things they will want to know before it gets cold.
Read more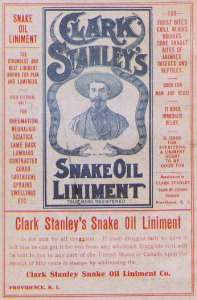
We all see a lot of questions about dyes, leak stoppers, lubricants, inhibitors, and snake oil. All of those were designed to go into the refrigerant circuit and “improve” something. I just go back to what Ray Johnson always said. (Ray is one of my early heroes in the biz, and he taught me a […]
Read more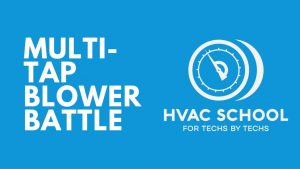
Here's the first question: Does it really matter if the speed taps on a motor are run or common? Well, yes… sort of. In some cases, it helps to identify if you're dealing with an open winding or an open thermal overload. The thermal overload breaks common, but you will still read a path between […]
Read more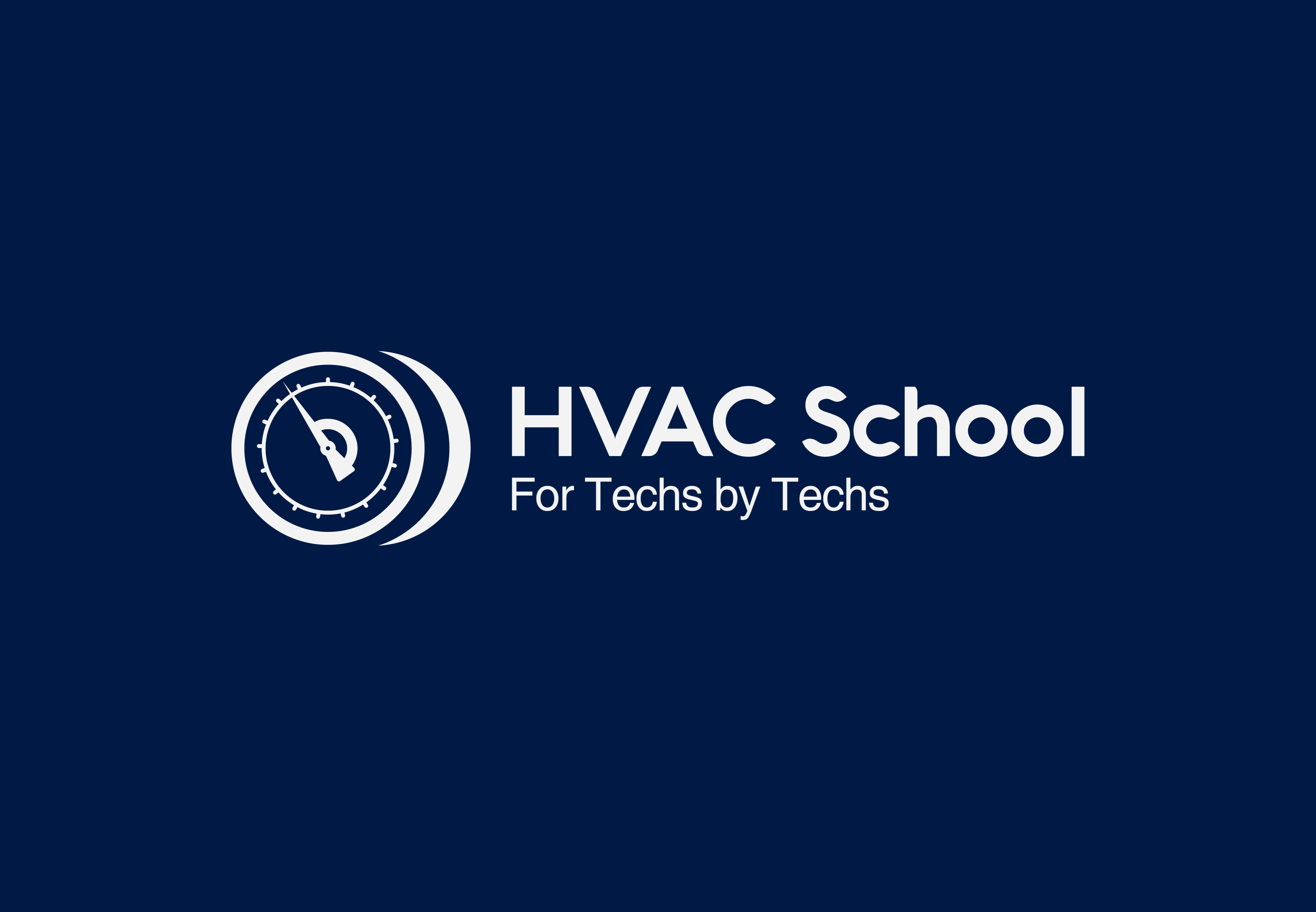
In this episode I talk to Jeremy Smith and he shares some of his refrigeration experience… and his Barry White smooth voice. Also – got to hvacrschool.com/10K to participate in Stephen Rardon's awesome tool giveaway.
Read more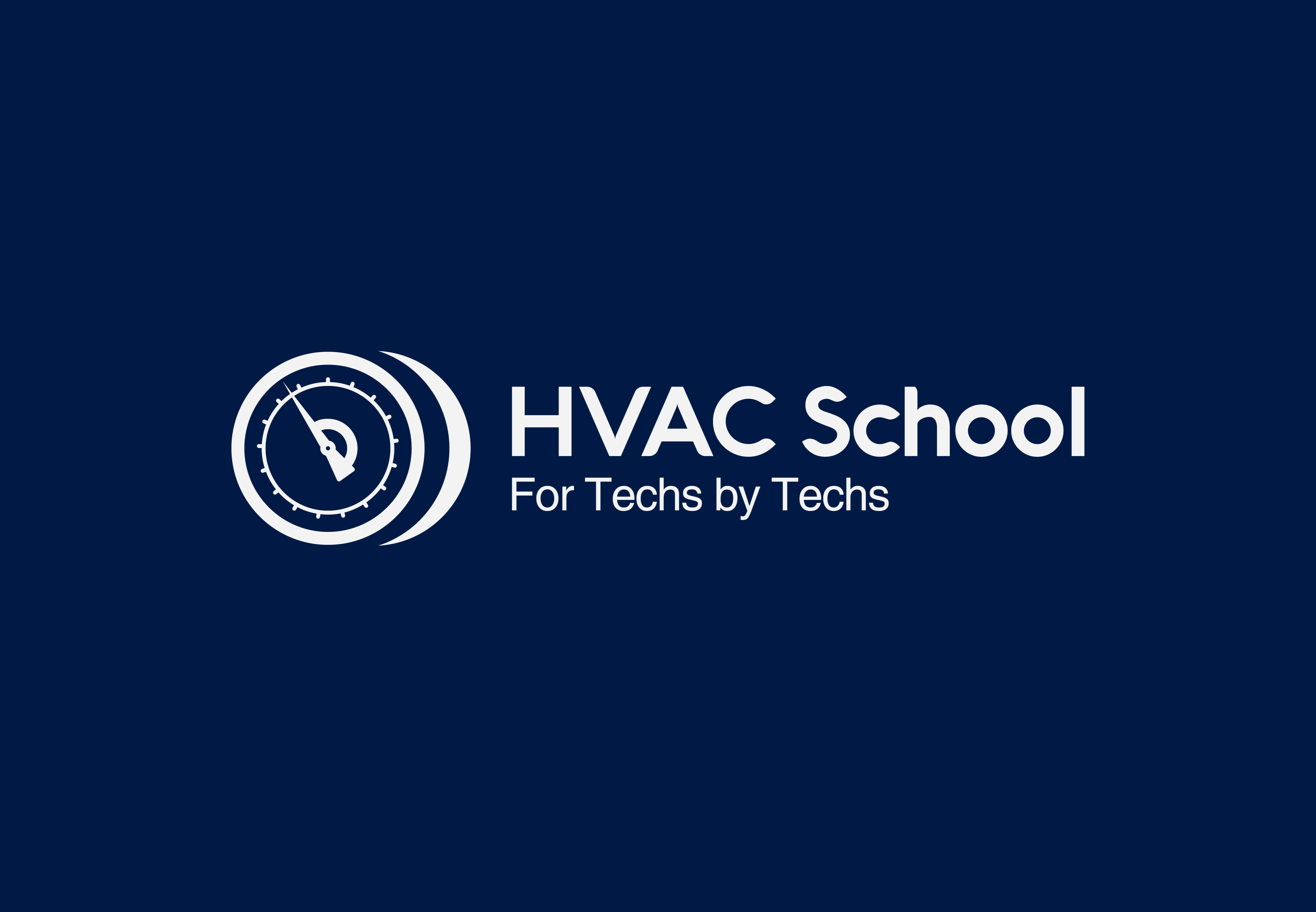
I talk to Tim Bagnall from Arizona in this episode and we discuss flowing nitrogen and the differences between Florida and Arizona.
Read more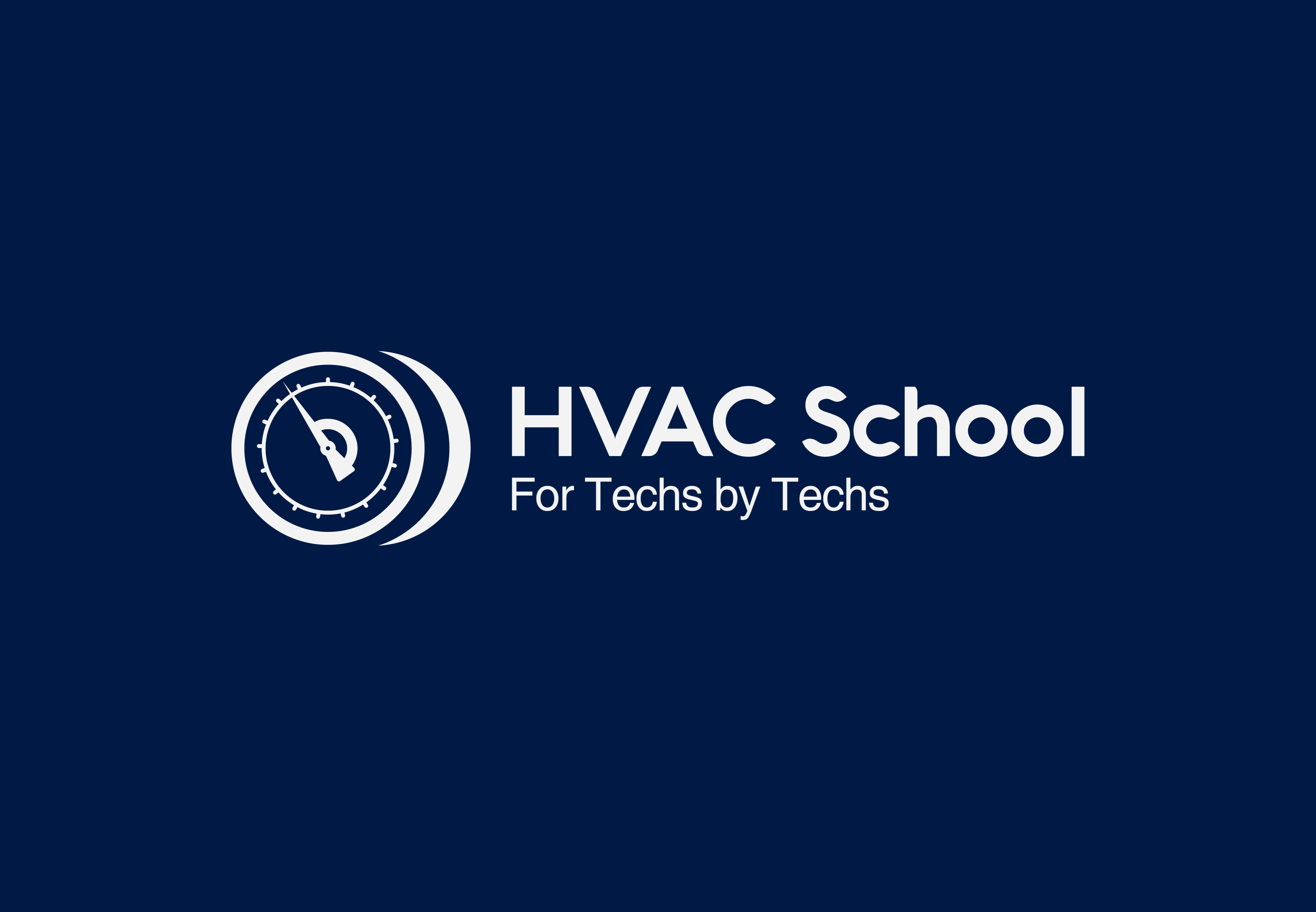
In this episode of HVAC school we cover some things you need to be checking on every service call. Air Filters Coils Corrosion Drains Electrical Connections Rubouts System Setup Operation Modes Find out more at hvacrschool.com
Read more